BIG STEEL CONSTRUCTION EXCURSION 2007
Author: Dr.-Ing. Holger Flederer
This year's big steel construction excursion took place from 30.05. to 01.06.2007. The group of 44 students from the 4th to 10th semesters and the staff of the Chair of Steel Construction started punctually at 8 a.m. on May 30 for their bus trip through eastern and northern Germany. The first excursion destination was Plauen Stahl Technologie GmbH, which we reached after a 2-hour drive.
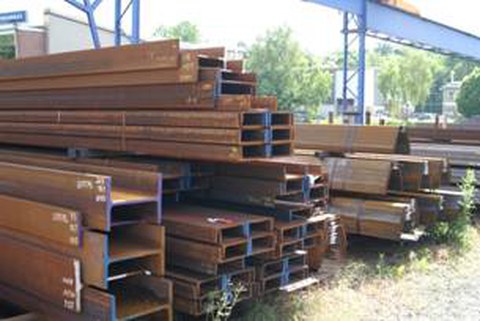
Lagerung
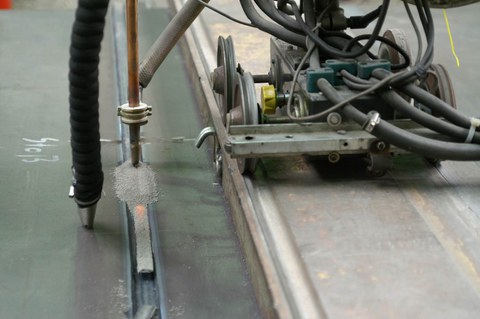
Unterpulverschweißen
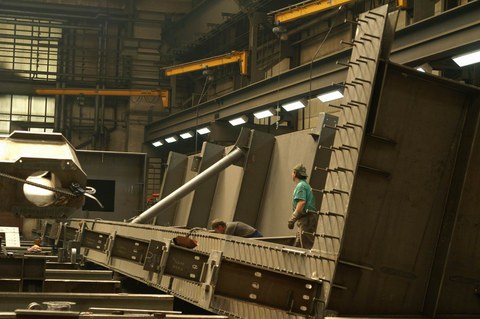
Teil des Überbaus der Schrägseilbrücke Niederwartha
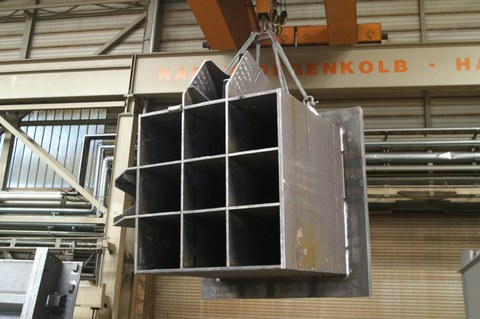
Stützenfuß für das Kraftwerk Boxberg
Mr. Rau, the head of the structural engineering department, gave us an introductory company presentation explaining the philosophy and structure of Stahlbau Plauen. Also the development of the company as well as current and already executed projects were presented.
Plauen Stahl Technologie GmbH is a high-performance steel construction company with over 130 employees and an annual capacity of approximately 20,000 tons of steel construction. The company offers a comprehensive range of services, starting with project management, project planning or design support, engineering services and fabrication up to erection. The company specializes in the product groups of architectural steel construction, multi-storey and composite construction, halls, power plant construction and bridge construction.
Steel construction in Plauen originated in 1885 with the founding of the company F. Sachs, Plauen. In 1947, VEB Stahlbau Plauen was founded in association with VVB Eisenkontor Land Sachsen, Dresden. After several name changes, the company was transformed into a limited liability company (GmbH) in 1990, whose shares changed hands frequently. Plauen Stahl Technologie GmbH has existed as an independent medium-sized company since July 2003.
Afterwards, we were invited to a plant tour, where we got a good impression of the working methods and the field of activity of a medium-sized steel construction company. From storage and goods labeling to cutting and welding technology to corrosion protection, we were able to see every work step that is necessary to process sectional steel and steel sheets into steel components weighing up to 150 tons.
In particular, we were able to observe the production of components for the Niederwartha cable-stayed bridge, the Boxberg power plant and final work on a Danube sluice gate.
After lunch in the plant canteen, to which the company invited us, we continued our journey in the direction of Magdeburg.
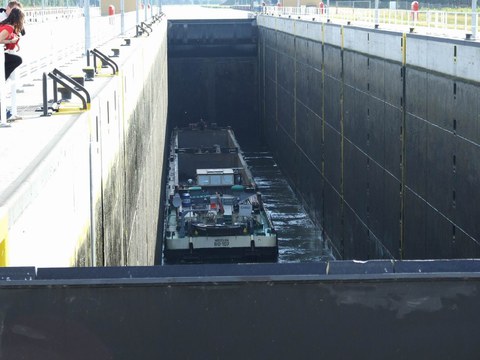
Schleuse in Betrieb
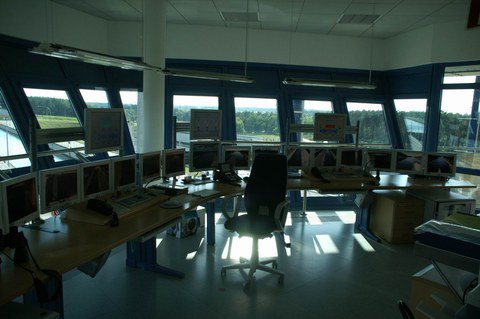
Kontrollraum der Schleusenanlage
After a bus ride of about 3 hours, we reached our next destination at 5:00 p.m.: the Magdeburg waterway junction. Here, Mr. Fiedler from the new waterway construction office in Magdeburg was already waiting for us and immediately began his expert guided tour. Construction of the canal bridge and the ship lift at Hohenwarthe began as early as 1934. Only eight years later, however, construction work had to be stopped due to the war. Since the Elbe often has insufficient water levels for shipping, new plans emerged to cross the Elbe with a canal bridge and to compensate for the existing difference in elevation between the Elbe-Havel Canal and the Mittelland Canal with a lock at Hohenwarthe. Before the completion of the waterway junction (October 10, 2003), shipping had to take a 12 km detour across the Elbe. This additional effort, which at first glance seems harmless, increased even more when one considers, in addition to the fluctuating Elbe water levels, that the trough of the Rothensee ship lift is limited to 82 m long ships.
On the site of the Hohenwarthe float lift, which had been started before the Second World War, the Hohenwarthe double spar lock was built from November 1998 to October 2003. For this purpose, the shafts of the dismantled lifting gear first had to be backfilled and depth-compacted to reduce subsidence.
At the eastern end of the Mittelland Canal maintenance, ships have to overcome a height difference of approx. 18.5 m to the Elbe-Havel Canal. In order to save water (canal dewatering) and pumping energy, three staggered economizing basins, one above the other, were arranged at each side of the lock for the upstream and downstream locks. This saves 60 % of the lock water requirement. In "regular" operation, the remaining 40% of the chamber contents must be returned to the upper sluice. Due to the recultivation of opencast mining areas, there is an increased demand for water in the Elbe-Havel Canal, which is why water recirculation will be dispensed with until about the year 2010 and a minimum number of daily lock operations will additionally be ensured by empty locks.
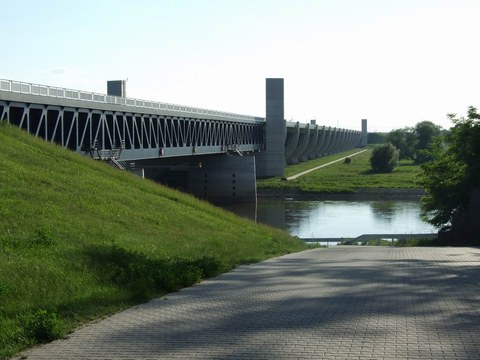
Kanalbrücke über die Elbe

Detail: Lager
Europe's longest canal bridge forms the heart of the Magdeburg waterway interchange. The 918 meters of the trough bridge are divided two-thirds into the foreshore bridge (690 m, 16 spans) and one-third into the river bridge (228 m, 3 spans).
The design of the Strombrücke borrows heavily from the canal bridge begun in 1934. Considering the extreme loads on the bridge, it appears almost filigree due to the main girders dissolved as trusses. The loads are transferred from the cross girders, which are about 1.90 m high, to the longitudinal girders. The individual bearings of the current bridge have to bear a vertical load of approx. 135 MN (equivalent to 13,500 t) - with a dead weight of 35 t.
After the detailed and interesting tour, our journey continued towards Braunschweig, where we spent the night in a cozy hotel (family-run).
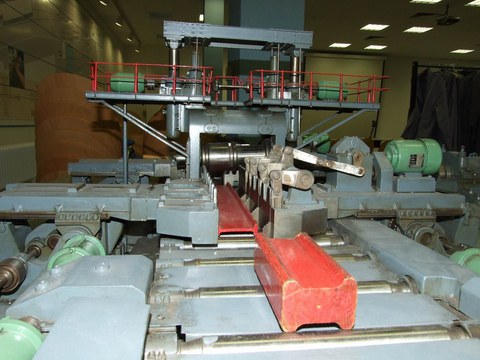
Modell zur Veranschaulichung des Herstellungsprozesses - horizontales Walzenpaar mit Träger
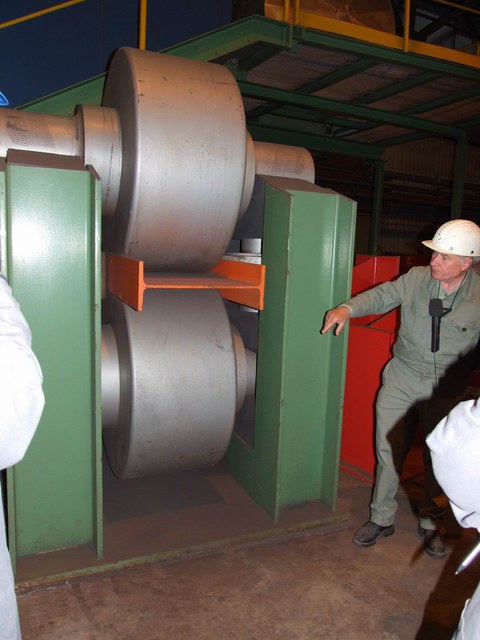
Modell zur Veranschaulichung des Herstellungsprozesses - Walzstraße
The first item on the agenda of the second day of our excursion was the Salzgitter AG rolling mill in Peine, which we reached at 9:00 am. There, we were welcomed by company employees in the visitor center.
After a brief welcome, we were given a very clear presentation of the steel mill. We learned that "Peiner Träger GmbH" is a company of the Salzgitter Group which currently employs about 1240 people.
The history of the rolling mill goes back to the end of the 19th century. A milestone in the company's history was the year 1914, when the patent for the wide-flange beam was acquired, which has since been marketed internationally as "Peiner Träger".
In the course of an eventful history, the various locations of Salzgitter AG grew into an innovative and efficient steel group. Today, the Salzgitter Group is one of Europe's leading steel technology groups.
An electric arc furnace (700 V/130 kA), a ladle furnace, a purging stand and a continuous casting plant are available in Peine for steel production, with only scrap being used as starting material. The blooms or beam blanks produced in this way, which help to rationalize beam production, can be processed into beams or sheet piles either on the "universal medium beam line" or the "heavy beam line".
A film about the company's history and steelmaking technologies rounded off the first part of the tour.
After the majority of the excursion participants had decided to visit the "heavy rolling mill", the group was divided in two and each individual was equipped with protective clothing, including helmet and goggles, as well as headphones.
At the beginning of the tour, we were shown on the model the production of the parallel-flanged wide-flanged beams, whereby the production of the desired beam shapes takes place in a reversing process. Profiles between 14 and 24 m in length are usually produced in this way. We were able to observe how a bloom insert with dimensions of 280 x 420 mm coming from the walking beam furnace was first rolled out to the preliminary profile and then formed into the finished profile.
Passing the cutting unit and the outdoor area for cooling the beams, the tour of the roller leveler concluded the plant tour. The special feature of this machine, which helps to ensure the straightness and low angular deviations of the "Peiner Träger" beams, was the upright arrangement of the rolls. This orientation of the rolls is rarely used but offers many advantages, for example the beams do not have to be rotated for subsequent testing.
The visit to the rolling mill was rounded off by a joint lunch in the plant canteen, where there was an opportunity to clarify any questions that remained unanswered.
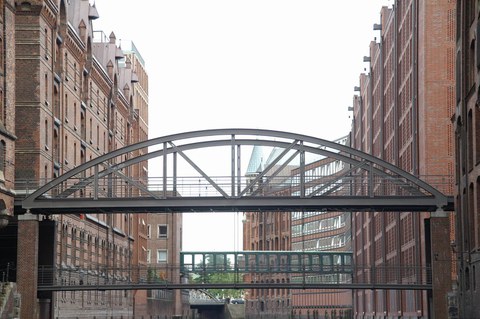
Speicherstadt Hamburg
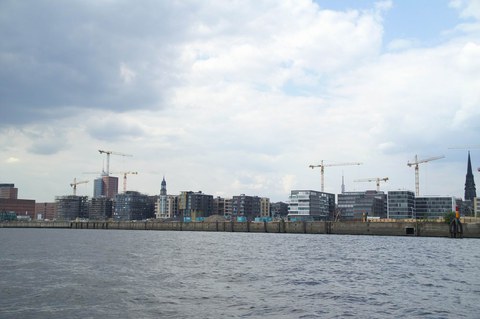
HafenCity Hamburg
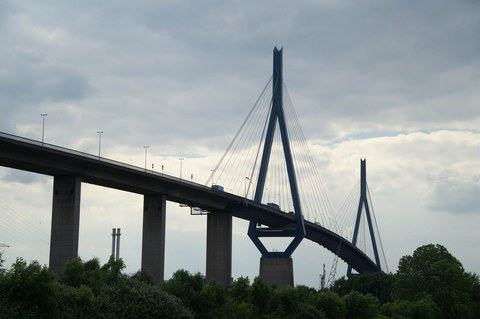
Köhlbrandbrücke
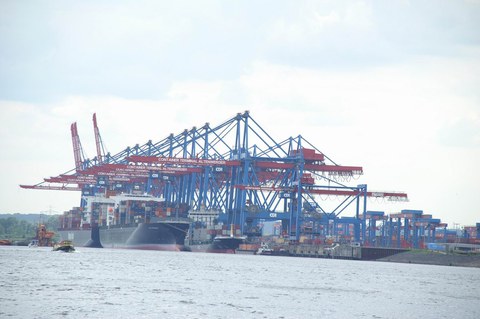
Container Terminal Altenwerder
When hunger was satisfied and all questions answered, we continued our journey towards Hamburg, where we arrived in the early afternoon. There we were first welcomed by Dr. Schmitt, an employee of the HPA. HPA stands for Hamburg Port Authority, the so-called port administration, which is mainly responsible for the creation and maintenance of the infrastructure in the port of Hamburg. From our meeting point, we boarded one of the many launches for the harbor tour that now followed. First, we passed through Speicherstadt, the largest warehouse complex in the world founded on oak piles. In the past, Speicherstadt was used to store and load general cargo such as tea, coffee and spices. Today, mainly carpet dealers, agencies, museums and exhibitions are located in the old brick buildings. We continued on the water in the direction of the large HafenCity construction site, where a separate district with office space and apartments will be built by 2008.
At the end of the tour, our attention turned to the port city and the Landungsbrücken, the Old Elbe Tunnel and the Hamburg Fish Market with the Fish Auction Hall.
Back at the pier, there was no time to lose, because our trip was still to go to Stralsund that day.
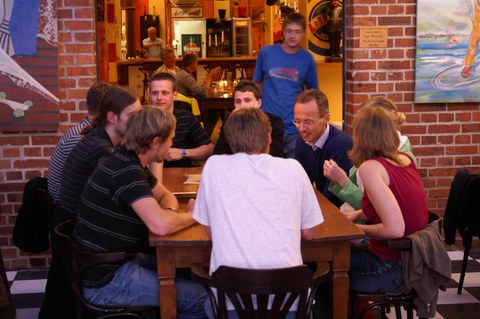
Im Restaurant Fisherman’s in Stralsund
Arriving in Stralsund at about 9:00 p.m., we quickly moved into our quarters at the InterCity Hotel, because we had planned to have dinner together. This we took in the restaurant Fisherman's, a rustic restaurant with a view of the harbor.
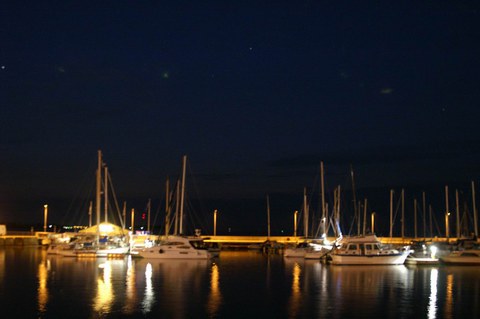
Blick auf den Hafen in Stralsund
Day three of our excursion began with a visit to the 2nd Strelasund crossing in Stralsund.
At the PYLONeum information center, we first heard a detailed presentation about the Rügen feeder road and the 2nd Strelasund crossing.
The line determination with far-reaching preliminary investigations for this project already took place in June 2000, the ground-breaking ceremony was in August 2004. The Strelasund crossing belongs to the traffic project German Unity "feeder road from the BAB 20 to Bergen/Rügen". The 53.2 km long route is expected to be completed by the end of 2008.
The core of the 4,100 m long crossing between the Stralsund bypass and the Altefähr junction is a 2,830 m long bridge. Running parallel to the existing Rügen embankment, the overall structure is made up of six individual structures due to the varying superstructure: the Stralsund foreshore bridge, the Ziegelgraben bridge, the Dänholm and Strelasund foreshore bridges and the Strelasund bridge.
In order to keep a 42 m high and 126 m wide aisle free for shipping, a cable-stayed variant was chosen for the Ziegelgraben Bridge. Statically, it acts as a spanned beam because the 127.75 m high pylons rest on spherical bearings. The steel superstructure with an orthotropic deck is supported by a total of 32 tensioned steel cables arranged in a harp shape above the two main openings (126 m / 198 m). In a comparison of variants, a two-part pylon in the shape of a teardrop proved to be the most convincing solution both visually and statically.
After the informative lecture, the group went to the bridge construction site. At the PYLONeum, we were introduced to the various innovative new features, such as the H4b system, which is designed to hold back a 38-ton truck traveling at 60 km/h, and the quieter roadway crossings.
Afterwards we drove by bus along the old Rügen embankment, from which one can overlook the entire project, and received expert explanations of all construction phases.
After this overall impression, we were allowed to visit the construction site on foot until the main opening. Here we were introduced to another innovation - in the production of the stay cables. Due to an expert opinion on bird protection, a minimum diameter of the cables of 18 cm was necessary, which would have led to a considerable sag in conventional constructions. Thus, the stay cables were designed - uniquely in Germany - with single strands, which has the advantage that individual links can be replaced.
The interesting information about the structure was rounded off by a wonderful view of Stralsund and the Baltic Sea.
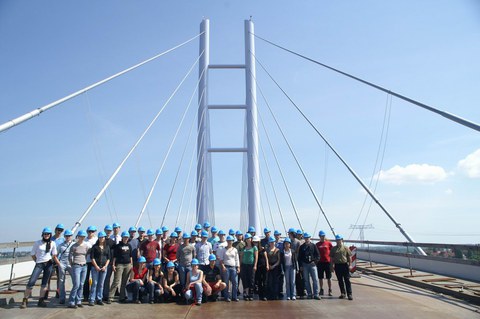
Gruppenfoto auf der Strelasundbrücke
After a lunch snack at the port of Stralsund, we drove on towards Warnemünde, to the last program point of our excursion: the Aker Warnow shipyard.
At 3:00 p.m. sharp, Mr. Kuchorzak and Mr. Höffner welcomed us with a short introduction to the shipbuilding group Aker Yards ASA and then, with the help of two colleagues, led us around the shipyard in four groups.
Aker Yards ASA, headquartered in Oslo, is an international shipbuilding group focused on building sophisticated ships. Aker Yards includes 17 shipyards in 7 countries with a total of 20000 employees. In addition to cruise ships and ferries, the product range includes merchant ships, offshore installations and special ships.
The shipyard in Warnemünde and the shipyard in Wismar are the only German sites of Aker Yards ASA. They are currently focused on the construction of merchant vessels. With a total of around 2,300 employees at both sites, deliveries this year are expected to be between 15 and 16 container ships. However, in order to secure future orders, special shipbuilding and the construction of icebreaking container ships are increasingly being considered. The close cooperation between the shipyards in Wismar and Warnemünde is remarkable. For example, the fully equipped forecastle is built in Warnemünde, while the stern, equipped with the propulsion unit and propeller, is built in Wismar. Final assembly will take place in Wismar after the forecastle has been towed.
Both shipyards underwent extensive modernization measures in the mid to late 1990s. In Warnemünde, for example, the slipway with its cable crane system, visible from afar, had to make way in part for new production halls and a 600-ton gantry crane that was many times more powerful. Today, both shipyards are among the most modern in the world.
The construction of the foreship in Warnemünde is carried out in sections and begins with the cutting of the plates. These are cut to size using autogenous or plasma cutting systems with a waste of 15 - 20%. This is followed by the partial joining of individual sheets using submerged-arc single-side welding systems and welding robot gantries, as well as automatic stiffening. The joining of 200 to 600 t sections is mainly carried out manually using the MAG flux cored wire (136) and manual arc welding (111) welding processes. A weight check of the sections is carried out during the complete production process. Welds are also inspected in accordance with a weld inspection plan. Critical weld seams in shipbuilding which therefore have to be inspected include, for example, cross joints in the ship's hull. The skin is shaped by clamping it onto a pin-jet gauge, whereby residual stresses are accepted. The fabricated sections are supported on bracing, which is primarily arranged under transverse bulkheads and longitudinal stiffeners to prevent buckling of the outer skin. After blasting and coating the individual sections in huge coating halls, they are fully equipped and welded together to form the complete foreship. For transport to Wismar for final assembly, the last transverse bulkhead is welded watertight, if necessary, and the complete forecastle is trimmed by section flooding to prevent it from capsizing or even sinking during the crossing.
This impressive presentation of the use of steel formed the crowning conclusion of our excursion.
We rounded off our trip with an excursion to the center of Warnemünde. We took advantage of this for a half-hour short break at the beach, which even motivated some brave people to swim in the ice-cold Baltic Sea.
After a last dinner together in the restaurant Atlantic we started our long way back to Dresden. Around 2:00 a.m. we reached our destination tired and enriched by many impressions.