STEEL CONSTRUCTION-EXCURSION 2012
Authors: Dipl.-Ing. Lars Sieber, Prof. Dr.-Ing. Richard Stroetmann
The steel construction excursion on May 30, 2012 led about 40 students accompanied by Prof. Stroetmann and Mr. Sieber from the chair of steel construction to the company Plauen Stahl Technologie (PST) and then to Stahlwerk Thüringen GmbH in Unterwellenborn.
Arrived at the PST company in Plauen, the students were divided into two groups after a short instruction. While the first group started directly to visit the production halls, the other participants were explained the philosophy and the structure of Plauen Stahl Technologie. In a short company presentation, Mr. Völkner, commercial manager at PST, reported on the company's development and introduced current and already completed projects. Mr. Sachse, head of the bridge construction department, explained the tasks and perspectives of a civil engineer in the steel construction company PST.
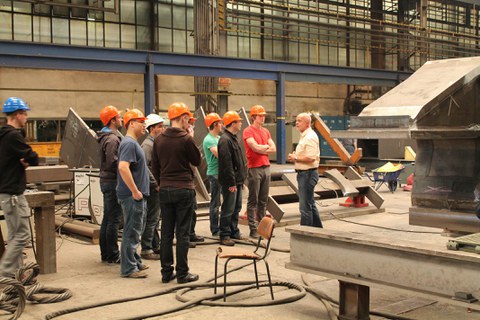
Herr Zuckschwerdt mit Studenten
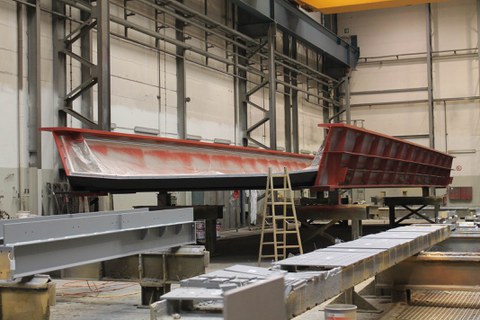
Überbau einer Berliner S-Bahn-Brücke
Afterwards the groups changed and Mr. Neudel and Mr. Zuckschwerdt gave us an insight into the working methods and the field of activity of the medium-sized steel construction company during a factory tour. The work steps involved in the manufacture of a steel construction - from storage and material identification to cutting to size, pre-assembly, welding and preservation - could be followed using interesting project examples.

Werkshalle mit Baggerfertigung
After lunch in the factory canteen, to which the company PST invited us, we continued our journey in the direction of Unterwellenborn.
The second station of the excursion was the steel and rolling mill Thuringia. On arrival at the plant gate in Unterwellenborn, the participants were welcomed by four former employees of the plant and initially provided with protective clothing, including helmet and goggles, as well as ear protection. All four groups then set off on a tour of the plant. After a short walk on the plant premises we reached the production halls of the steel and rolling mill. Our tour started with the scrap yard, which is supplied with scrap metal by trucks and trains with a capacity of approx. 45000 t. After pre-sorting according to size and quality, the tanks for the melt are filled in the electric arc furnace. Afterwards, the participants followed the production of the steel and marvelled under deafening noise at the electric arc furnace, the ladle furnace, in which the correct temperature and alloy of the molten bath are set, and the continuous casting plant. Beam blanks" (semi-finished products close to final dimensions) are produced simultaneously in several strands in this plant. Depending on the double-T-section to be produced, the cross-section and length of the beam blanks are adjusted so that they can be rolled to a length of up to 100 m in the rolling mill. The beams are then cooled in air. Profile deformations from the manufacturing process are eliminated on the straightening machine. The beams are then sawn to the length ordered by the customer and then prepared directly for shipping. During the factory tour, numerous questions arose, which were answered competently and clearly by the former employees of the company.
At this point we would like to thank the companies Plauen Stahl Technologie GmbH and Stahlwerk Thüringen GmbH for the friendly reception, the excellent organization and support.