BIG STEEL CONSTRUCTION EXCURSION 2013
Authors: Dipl.-Ing. Thomas Faßl, Prof. Dr.-Ing. Richard Stroetmann
In the Whitsun week from 22.05. to 24.05.2013 the fourth big steel construction excursion for students of the faculty of civil engineering of the TU Dresden took place. The 47 students of the 4th to 10th semester, accompanied by Prof. Richard Stroetmann, Jörn Scheller and Thomas Faßl from the chair of steel construction, were offered a high-quality and varied program in the north of Germany.
The Niederfinow ship's hoist near Berlin was the first stop on the way to the Hanseatic City of Hamburg for the Dresden excursion group. The interesting and competent guided tour of this unusual structure was kindly made possible by Peter Huth and Klaus Winter from the Wasserstraßen-Neubauamt Berlin. The existing ship's hoist in Niederfinow has been in service since 1934. The riveted steel construction, which has been entitled "Historic Landmark of Civil Engineering" since December 2007 and will soon reach the end of its service life, is to be replaced by a new facility that has been under construction since 2008. This measure is intended to maintain the functionality of the Havel-Oder waterway and at the same time eliminate a major bottleneck on the only trans-European east-west waterway connection between Szczecin and Duisburg [1]. 285 million will probably be invested in a new building by 2014, which will be able to be passed by large motor cargo ships of waterway class V with a cargo of up to 2,300 tons per ship. Compared to the old ship's hoist, the possible annual cargo throughput will thus increase by 98% to 4,400,000 tons.
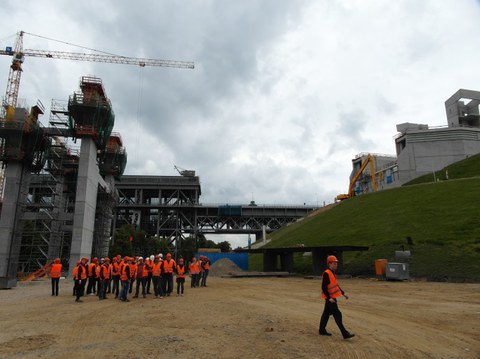
Altes und neues Schiffshebewerk Niederfinow
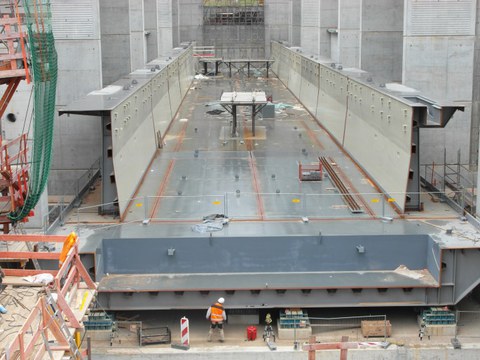
Trog für das neue Schiffshebewerk Niederfinow
Situated between the existing rivet construction and the old lock staircase, the new building rests on a reinforced concrete structure whose design, dimensioning and construction process pose a great challenge due to the low tolerances. The heart of the new lift is the steel trough, which could be viewed in its enormous dimensions during the excursion. With a length of 115 m, a width of 12.5 m and a trough depth of 4 m, its maximum weight in the water-filled state will be 9,800 tons, whereby the applied corrosion protection alone will already take up 3 tons [1]. In order to move these enormous masses and to cope with the height difference of 36 m, the engineers are using technology that has already proved its worth in the old ship's hoist that is still in operation. The lifting operations are realized with the help of ropes attached to the trough and running over pulleys to the counterweights. The mass of the counterweights corresponds to the weight of the water-filled trough, so that the mechanically synchronized drives only have to compensate for frictional and start-up forces and possible water level differences [2]. Finally, the connection between the waterway on land and the ship's hoist is established by the 65.50 m long canal bridge, which can be closed with a rotary segment gate at the connection to the waterway. One of the highlights of the tour of this unique structure was the inspection of the trough, during which the Dresden students were able to witness how individual steel components and up to 120 mm thick sheets are processed and joined together to form a large-format structure. After this interesting prelude and a small lunch snack at the friendly invitation of DSD Brückenbau, the excursion was continued in the direction of Peine.
Arriving in Peine near Hanover, the Dresden excursion group, led by competent employees, visited the steel and rolling mill of Peiner Träger GmbH, which belongs to Salzgitter AG. During the tour of the steel mill, the students were able to directly observe all the steps involved in the production of steel in the two electric arc furnaces through to the production of rolled sections and follow the production sequence. The tour began with the scrap store. With the help of a magnetic crane, the scrap from different categories is loaded into large transport containers and guided on rails towards the furnace by computer control. In the direct current electric arc furnace, the melting process takes place after the scrap and possible additives have been added. When the negative electrodes, which are integrated in the furnace cover, are introduced, an arc is created from the positive bottom electrodes through the charge to the negative electrodes. During this process, which the students were able to experience at close quarters under deafening noise and flying sparks, temperatures of up to 3500 °C are generated. After the material has been melted down, the liquid steel is poured off and fed to the secondary metallurgical ladle treatment to add alloying elements and remove unwanted accompanying elements such as sulfur. The ladle steel is then poured into water-cooled copper moulds, which feed the steel into the continuous casting plant, at the end of which slabs and so-called beam blanks are produced. These intermediate products are temporarily stored and, if necessary, fed into the rolling process. The students now followed the steel on its further production process. Before the rolling process, the steel blanks, which are up to 16 m long, are heated to the desired rolling temperature in modern walking beam furnaces, then rolled to a length of 110 m in the rolling mill and cut to length according to customer requirements. The rolled sections are cooled by air. The resulting pre-curvatures, of which the students were able to see for themselves on site, are compensated by means of a rolling stand with vertical roll arrangement, which is one of the last of its kind. Peiner Träger GmbH uses this production process in its steel and rolling mill to manufacture profiles with a maximum nominal height of up to 1100 mm.
The tour of this plant gave the students an understanding of how steel is made. The knowledge and above all the experience of its manufacture makes it more tangible and promotes understanding of its behavior and properties as opposed to "dry" design on paper.
After the tour of the steel and rolling mill in Peine, which was unique for many excursion participants, the group reached the Hanseatic City of Hamburg in the evening of May 22nd, which all participants could explore individually during the remaining hours of the day.
Well strengthened, the Dresden excursion group then set off the following day to their next destinations. In addition to visiting several bridges in the port of Hamburg, the program also included a visit to the steel and rolling mill of Arcelor Mittal Hamburg GmbH. The visit to this plant was a great addition to the Peine site, as the range of end products and also the manufacturing process of the Hamburg steel mill differed from the rolling mill in Peine that had been visited so far. Arcelor Mittal Hamburg GmbH also produces steel in an electric arc furnace, but in addition to scrap it also uses sponge iron with an iron content of approx. 95% as a starting material, which is obtained in the plant's own MIDREX plant from the direct reduction of iron ore. The molten metal is then produced in the alternating current electric arc furnace and, after ladle treatment, is cast in seven strands into billets measuring 125 x 125 mm. These semi-finished products are then rolled out on the rolling mill on two strands and at a speed of up to 95 m/s into wire rod with diameters of 5.5 to 16 mm and a maximum length of up to 9 km. These finished products can be shipped directly from the plant's own port, which allows unloading of Panama class ships. Finally, Arcelor Mittal Hamburg GmbH's clientele manufactures strands, screws and welding rods, among other products, from the plant's product range [3].
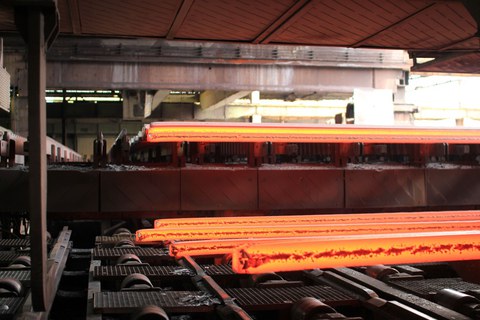
Stahlknüppel als Vorprodukt für Walzdraht
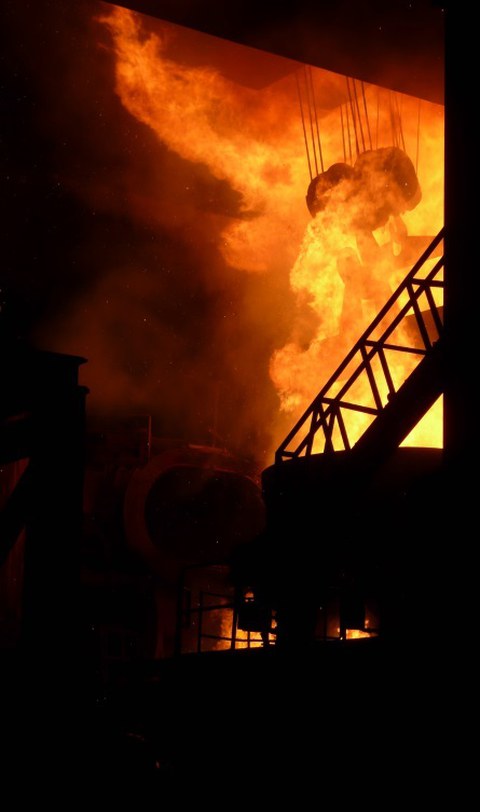
Elektrolichtbogenofen
After this informative visit, which highlighted the diversity of steel production, and a small lunchtime snack at the kind invitation of Arcelor Mittal Hamburg GmbH, the students' program included a tour of the Reiherstieg bascule bridge and the Kattwyk bridge in Hamburg. The group was accompanied and guided by Michael de Hooge from the Hamburg Port Authority, who showed us these special bridge constructions in an inspiring way and made them tangible.
The Reiherstieg bascule bridge was built in 1982 and extensively renovated in 2008 due to the constantly increasing load from road and heavy traffic. The 46 m long and 265 tonne bascule part of the bridge was completely replaced. The hinged section of the bridge is connected to a counterweight via tie rods so that the drives only have to overcome small loads during operation. The special feature of the bridge, however, is that additional longitudinal girders were arranged to the side of the carriageway, which are only connected to the actual superstructure at the level of the end crossbeams. This ensures that the vibration load caused by the large volume of traffic is not transmitted to the tie rods and drive, which is additionally decoupled after each folding process. The highlight of the visit to this structure was the opening of the bridge in the course of a regular operational test, during which the functionality and dimensions of the structure could be admired by the students at close quarters.
Afterwards, the students continued their excursion at the Kattwyk Bridge, which was inaugurated in 1973. This 290-meter-long truss bridge, which is considered the largest lift bridge in Germany due to its 96-meter-long, liftable midspan, transfers both road and rail traffic across the Süderelbe and is considered one of the most important connections in the Port of Hamburg. The railroad track is located in the middle of the carriageway, so that the bridge has to be closed to road traffic during the railroad crossing. Every two hours the lift bridge is raised to a height of 53 m above the water level, thus opening the waterway to shipping traffic. During one of these lifting operations, the students were even allowed to ride up the middle section of the bridge and enjoy the overwhelming view over the port of Hamburg, the panorama of the city and the Köhlbrand Bridge.
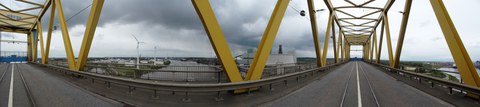
Kattwykbrücke in oberster Hubstellung
The lifting of the middle section is made possible by drives in the two portals, each approx. 70 m high, at the ends of the main field. A total of 32 rope strands are connected with counterweights so that only frictional forces have to be overcome during the lifting process. Despite the large clearance height in the current field when open, the Kattwyk Bridge was severely damaged in an accident. In 1991 the trussed superstructure of the foreshore bridge collapsed due to a ship collision after a ship tried to pass the bridge in the side field instead of in the open current field. In the course of the last few years, however, additional problems have accumulated. The Kattwyk Bridge is not designed for its current load of 50 freight trains and about 9000 vehicles per day. In order to avoid more severe fatigue in the future, planning began in 2008 for a twin lift bridge, which is to be built just 50 m from the current structure. The new bridge will be designed exclusively for railroad traffic. As a result, the existing Kattwyk Bridge can be used for motor traffic for many years to come, so hopefully many more students and engineers will be able to visit this magnificent structure.
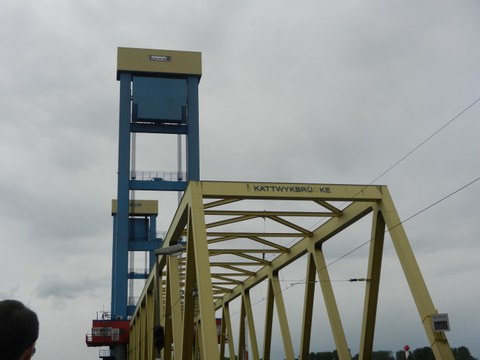
Kattwykbrücke Hamburg
After the Dresden excursion group around Prof. Stroetmann had completed the small round trip in the port of Hamburg, they set off for their second overnight destination in Kiel. On the way to the Hanseatic city, another interesting bridge tour was on the agenda in Itzehoe, to which the Eiffel Deutschland GmbH under the leadership of Ingo Gabinski had invited. There, the Störbrücke bridge spans the river of the same name, which is classified as a maritime shipping route at this point, and with two separate superstructures is intended to transfer the directional lanes of the Federal Highway 23. The new parallel bridge trains replace the previous prestressed concrete construction. Since 2010, one bridge train has already been completed, which will transfer both directional carriageways until the completion of the parallel construction in 2015. The Störbrücke bridge has a total length of 1155 m and spans the river in the current field by means of a beam arch construction with a span of 120 m, whose carriageway slab is designed as a composite structure. The ramp structures, which connect to the ends of the tied arch bridge, are also designed as a composite structure, but with a steel box girder at the bottom. The company Eiffel Germany provided the Dresden students with an extensive guided tour, which included an inspection of the foundation work and the steel box girder segments that were provided, as well as an inspection of the box girder at the abutment. In addition to the practical insights into steel construction details, such as the arrangement of stiffeners in the box girder and at the abutment as well as the roadway transition structure, the assembly of such a large structure was also discussed. The beam arch and the foreland bridges were pre-assembled in sections on the ground and lifted into their final position by means of a large crane. In order to meet the tight schedule, only the most necessary welding seams between the individual cross-section elements were placed on the ground so that the assembly could be carried out quickly by the large cranes. After lifting all the necessary parts, the final assembly was carried out and the welded joints were completed.
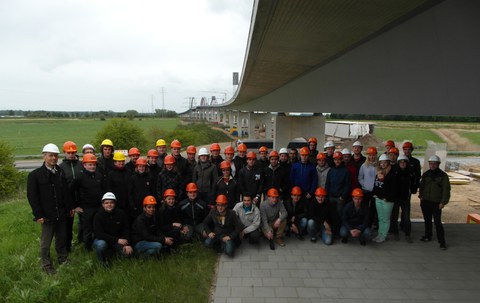
Exkursionsgruppe an der Störbrücke Itzehoe
After the tour of the construction site at Störbrücke had ended with a group photo, the travel group reached Kiel in the early evening after another short bus ride. In the state capital of Schleswig-Holstein, the students reviewed the day over dinner and enjoyed their free time in Kiel's cafés or on a tour of the city.
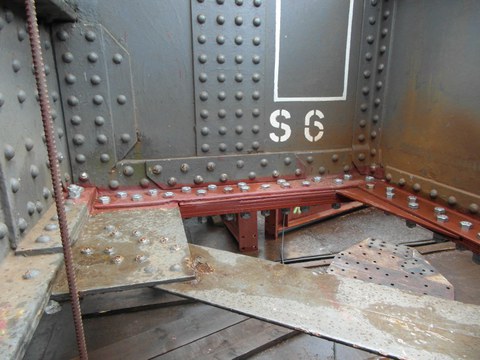
Querträgerverstärkung an der Rendsburger Hochbrücke
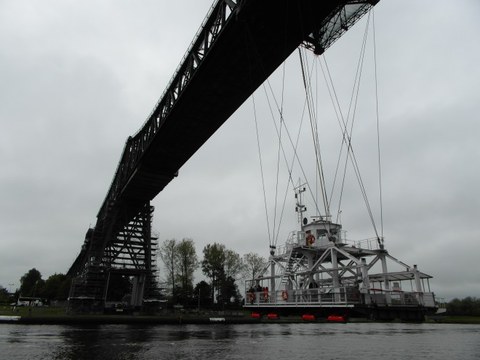
Schwebefähre an der Rendsburger Hochbrücke
The first stop on the last day of the excursion was in Rendsburg. The employees of the Kiel Waterways and Shipping Office (including Rüdiger Schröder and Georg Bey-er) as well as the companies Nobiskrug (assembly manager Michael Cordes) and Stahlbau Schröder offered the students a comprehensive tour of the Rendsburg high bridge, which was built in only two years from 1911 to 1913 and will be managed by the Federal Chamber of Engineers as a "Historic Landmark of Engineering Construction" in Germany from autumn 2013. The 2.5 km long railroad bridge spans the Kiel Canal at a height of 68 m with a clearance of 42 m in the current field and is part of the Neumünster-Flensburg-Fredericia railroad line, which is considered one of the main connections between Germany and Scandinavia. With its appearance and height it is considered a landmark of the region. Since the bridge only carries railroad traffic, a floating ferry was installed in the 140-meter-wide span of the bridge's current field, which transports pedestrians and cars to the other side of the canal. The Dresden students took the opportunity to travel on this floating ferry, of which only eight examples exist worldwide.
Subsequently, individual excursion groups were able to inspect the reinforcement work on the piers, on the canal bridge and corrosion protection work. Already about 20 years ago, the riveted bridge construction was started to be repaired with regard to corrosion protection. In addition, the Deutsche Bahn AG decided to reinforce the Rendsburg high bridge for a higher load. The passage of freight trains with a length of up to 875 m generates high braking forces in particular, for which the superstructure and piers must be reinforced. For this purpose, the pier foundations are enlarged and braced together to be able to transfer the high horizontal forces into the soft ground. At the same time, severely corroded parts of the piers are replaced and damaged riveted joints are replaced with screws. While some students looked at the reinforcement measures on the pier foundations, another group was allowed to explore the work on the canal bridge. Under running, single-track railroad traffic, the superstructure of the canal bridge is reinforced here by lamella packages, the renewal and addition of components and the necessary bolted joints. After completion of all reinforcement and repair measures, which is scheduled for 2015, the "old railroad line" will meet the requirements for a new line.
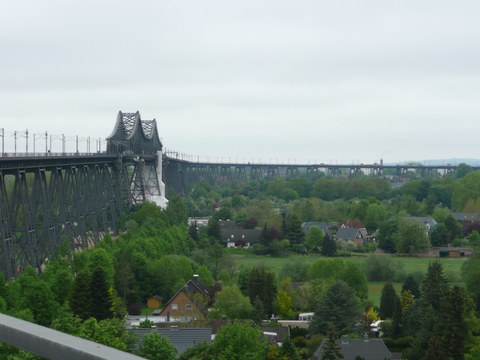
Eisenbahnhochbrücke Rendsburg
While a group of students devoted themselves to the Rendsburg high bridge, the second part, under the guidance of Mr. Diethard Stier, divisional manager for steel construction, was able to get to know the Nobiskrug company and the associated shipyard, which is not far away. In a short company presentation the Dresden students were shown the fields of activity of the company. Besides the construction of luxury yachts, Nobiskrug is also at home in special steel construction, hydraulic steel construction and offshore. Thus the company is not only significantly involved in the renovation of the Rendsburg high bridge, but also delivered the necessary new truss bridge segment to Hamburg after the ship impact at the Kattwyk bridge in 1991. A specially developed pontoon and two tugs, also manufactured in-house, were also used to transport the bridge component manufactured in the Nobiskrug halls.
After this interesting company presentation and the inspection of the production halls on the Nobiskrug factory premises, all excursion participants strengthened themselves together with a bratwurst at the Rendsburg high bridge at the friendly invitation of Stahlbau Schröder. Well satiated, they then set off on their journey to the penultimate station of the excursion.
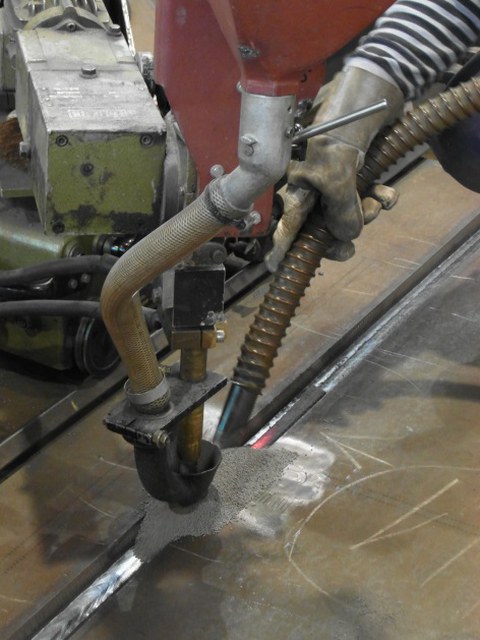
Unterpulverschweißen
With a delay of more than two hours, caused by a long Friday afternoon traffic jam on the freeway, the excursion group was welcomed in the late afternoon by Dipl.-Ing. Jan Mehnert on the premises of Eiffel Stahltechnologie GmbH in Hannover. Here, the students were able to gain many practical impressions on the subject of cutting and welding work and exchange information on the numerous welding instructions. They were also able to marvel at large-format components such as truss elements for the Botlek Bridge in Rotterdam and orthotropic roadway slab elements. Of particular interest was also the submerged arc welding of heavy plates, which most of the students had previously only known from theory. After the tour of the approx. 22,000 m² production area of Eiffel Stahltechnologie GmbH in Hanover, which is known for excellent projects such as the roof construction of the AWD Arena in Hanover or the Tropical Hall in the Leipzig Zoo, a pleasant last item was on the agenda. In Schönebeck on the Elbe, the excursion group enjoyed an excellent common dinner and reviewed the highlights of the excursion before returning to Dresden late in the evening. A little later than planned, but safe and sound, all participants finally arrived back in the Saxon state capital after three days full of impressions and interesting sightseeing.
On behalf of all participants, special thanks go to the Institute of Steel and Wood Construction for the organization and co-financing of the excursion, which was a complete success and of high professional quality, as well as for the financial support by the Society of Friends and Sponsors of the Dresden University of Technology. We would also like to thank the inviting companies, authorities and their representatives and employees, who not only made the successful visits possible, but also often provided us with good meals.
Literatur:
[1] Das neue Schiffshebewerk in Niederfinow. Online verfügbar unter: http://www.schiffshebewerk-niederfinow.info/schiffh5.ht;, letzter Zugriff: 10.06.2013
[2] http://www.wna-berlin.de/bauwerke_anlagen/schleusen_schiffshebewerke/schiffshebewerk_niederfinow/index.html; letzter Zugriff: 10.06.2013
[3] http://www.arcelormittal.com/hamburg/; letzter Zugriff: 11.06.2013