GROSSE STAHLBAU-EXKURSION 2015
Autoren: Dipl.-Ing. Thomas Faßl, Prof. Dr.-Ing. Richard Stroetmann
Vom 29. September bis zum 01. Oktober 2015 fand die fünfte große Stahlbau-Exkursion für Studentinnen und Studenten der Fakultät Bauingenieurwesen der TU Dresden statt. Den insgesamt 46 Studierenden des 4. bis 10. Fachsemesters, begleitet durch Herrn Prof. Richard Stroetmann, Thomas Faßl und Lars Werner vom Lehrstuhl für Stahlbau, wurde während der Reise ein fachlich hochwertiges und abwechslungsreiches Programm geboten.
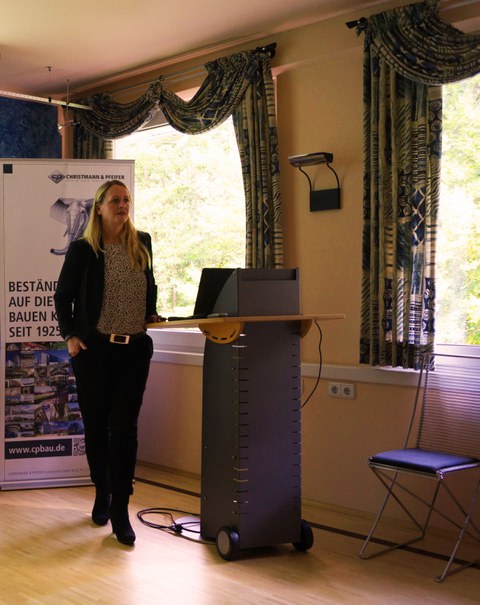
Bild 1. Unternehmenspräsentation Christmann & Pfeifer durch Tina Klingelhöfer
Das Unternehmen Christmann & Pfeifer in Angelburg war nach einer langen Anfahrt das erste Etappenziel. Nach dem freundlichen Empfang von Tina Klingelhöfer und der Stärkung der Gruppe durch das Mittagessen, stellte sie die Tätigkeitsfelder und Besonderheiten von Christmann & Pfeifer in einer Firmenpräsentation vor. Seit 1925 bietet C+P Leistungen für verschiedenste Bereiche des Bauwesens an. Das Unternehmen ist u. a. im Hoch- und Brückenbau, Industrie- und Gewerbebau, Leichtmetall- und Schlüsselfertigbau tätig. Im Portfolio finden sich innovative Ideen, wie z. B. mobile Parkhäuser oder die im Brückenbau eingesetzten Preflex-Träger. Die Christmann & Pfeifer Gruppe besitzt außerdem eine Sparte zur Fertigung von Möbelsystemen und Einrichtungsgegenständen. Neben der Vorstellung laufender und erfolgreich abgeschlossener Projekte wurden den Studierenden Wege für den Einstieg in das Unternehmen aufgezeigt und persönliche Erfahrungen von Mitarbeitern geschildert.
Im Anschluss an die Präsentation ging es in die 20 Minuten entfernten Produktionshallen in Breidenbach, die sowohl Stahlbau- und Einrichtungsfertigung als auch das Ausbildungszentrum beinhalten. Im Zuge der Tour durch die Werkshallen mit Herrn Daniel Pfeifer erhielten die Studierenden Einblicke in die klassische Stahlbaufertigung und die Herstellung von Preflex-Trägern. Im Ausbildungszentrum konnten sie sich zusätzlich an einem Schweißsimulator probieren.
Nach dem aufschlussreichen Unternehmensbesuch verließ die Gruppe C+P und erreichte nach einer kurzen Fahrt die Talbrücke Münchholzhausen an der Autobahn 45 bei Wetzlar. Dort erwartete sie bereits Karl-Heinz Isselmann und Bärbel Bachmann von Donges SteelTec, die das Bauwerk vorstellten und die Exkursionsteilnehmer über die Baustelle führten.
Die bestehende 1966 errichtete Balkenbrücke aus Spannbetonhohlkästen muss aufgrund der deutlich gestiegenen Verkehrslasten, konstruktiver Mängel und Schäden erneuert werden. Der Ersatzneubau ist als 13-feldrige Stahlverbund-Deckbrücke mit einer Gesamtbrückenlänge von 485 m und zwei getrennten Überbauten konzipiert. Diese werden als Trägerrost mit je zwei I-Profil-Längsträgern und in regelmäßigen Abständen angeordneten Querträgern ausgeführt. Im Bereich der größten Spannweiten (ca. 51 m) wird der Querschnitt über den Pfeilern aufgevoutet. Donges SteelTec ist hierbei für die Fertigung, Lieferung und Montage der kompletten Stahlkonstruktion einschließlich des Korrosionsschutzes verantwortlich [1]. Während der Verkehr über eine Hälfte des bestehenden Bauwerks rollt, erfolgt parallel der Neubau auf der anderen Seite. Ist die erste Hälfte des Ersatzneubaus fertiggestellt, wird der Rest der alten Talbrücke rückgebaut und der zweite Teil errichtet. Die Fertigstellung ist für das Jahr 2018 geplant.
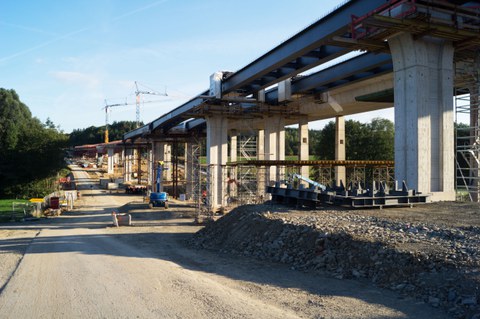
Bild 2. Talbrücke Münchholzhausen an der A45 bei Wetzlar
Nach dem aufschlussreichen aber auch anstrengenden Tag erreichte die Exkursionsgruppe am Abend Limburg an der Lahn. Mit einem gemeinsamen Abendessen im Restaurant Schwarzer Adler und dem Spaziergang durch die wunderschöne Limburger Altstadt vergingen die letzten Stunden des ersten Exkursionstages.
Der zweite Tag begann mit dem Besuch der eindrucksvollen Baustelle der Hochmoselbrücke. Diese wird die Ortschaften Ürzig / Zeltingen in etwa 160 m über dem Moseltal überqueren. Mit ihren Dimensionen sowie dem Entwurfs- und Montagekonzept ist sie eines der größten Stahlbrückenneubauvorhaben nach der Wiedervereinigung Deutschlands im Jahr 1990. Die Brücke schließt eine wichtige Lücke im europäischen Fernverkehrsnetz im Zuge der B50-neu (Hochmoselübergang), die die A1 mit der A61 verbindet.

Bild 3. Fotomontage der fertigen Hochmoselbrücke

Bild 4. Fotomontage der fertigen Hochmoselbrücke
Zum Konsortium, das für die Umsetzung des Bauvorhabens verantwortlich ist, gehören Eiffel Deutschland und deren Mutterkonzern Eiffage aus Frankreich sowie Porr Deutschland. Michael Hagedorn von Eiffel empfing die Exkursionsteilnehmer und legte in einem fachkundigen Vortrag die wichtigsten Fakten, erstaunliche Details und aufschlussreiche Animationen zum Bauwerk dar. Die Hochmoselbrücke wird als Deckbrücke über 11 Felder mit einer Gesamtlänge von knapp 1,7 km ausgeführt. Das Stromfeld über der Mosel weist mit ca. 210 m die größte Spannweite auf. Der Überbau hat eine Höhe von bis zu 7,80 m und eine Breite von 29 m. Er bietet für jede Fahrtrichtung Platz für zwei Fahrspuren und eine Standspur. Die Stahlbrücke besteht aus einem Hohlkasten mit beidseitigen Auskragungen und einer orthotropen Fahrbahnplatte. Zusätzliche Längsträger und in regelmäßigen Abständen angeordnete Diagonalen unterstützen die Auskragungen. Die geplante Stahltonnage für die Deckbrücke beträgt ca. 33.000 t. Dabei kommen Stähle in den Güten S355 und S460 zum Einsatz. Die Brückenpfeiler bestehen aus einzelligen Hohlquerschnitten und sind bis zu 160 m hoch. Ihre Gründung erfolgt auf Großbohrpfählen mit Durchmessern von bis zu 2 m.

Bild 5. Montagezustand Hochmoselbrücke nach dem 4. Verschub

Bild 6. Auskragung mit diagonaler Abstrebung
Im Anschluss an den interessanten Vortrag konnten sich die Studierenden ein Bild von den Arbeitsabläufen und dem Baufortschritt machen. Während der Begehung des Überbaus erläuterte Michael Hagedorn die wesentlichen Abläufe zum Montageverfahren. Die Hochmoselbrücke wird im Taktschiebeverfahren hergestellt. Die Stahlkonstruktion wird auf einem Vormontageplatz hinter dem östlichen Widerlager vormontiert und mit zur Werksbeschichtung ergänzendem Korrosionsschutz versehen. Der Querschnitt besteht aus insgesamt 8 zusammengeschweißten Einzelteilen. Dabei entstehen 82 Schüsse mit Längen von 15 bis 25 m. Das Einschieben des Überbaus mit einer zentralen Verschubeinheit auf dem Vormontageplatz ist für die Hochmoselbrücke ungeeignet, da hierdurch zu große Horizontalkräfte aus Reibung auftreten, die von den Pfeilern statisch nicht aufgenommen werden können. Daher werden die Vorschubkräfte auf den Überbau über Systeme an den jeweiligen Pfeilern aufgebracht, die die Reibungskräfte überwinden und für einen direkten Kräfteausgleich am Pfeilerkopf sorgen. Hierdurch wird erreicht, dass nahezu keine äußeren Horizontalkräfte aus dem Verschubvorgang abzutragen sind. Für diese neue Lösung wurde ein Patent angemeldet.
Beim Einschieben des Überbaus wird der Hohlkastenquerschnitt als Vorbauschnabel genutzt. Die vorderen 90 m werden bis zum Erreichen des Wiederlagers ohne Fahrbahnverbreiterung ausgeführt. Dadurch werden die Schnittgrößen und Verformungen der Auskragung reduziert. Zur Entlastung während des Taktschiebens wird ein 80 m hoher und 640 t schwerer Pylon auf dem Überbau positioniert und mit ca. 160 km Abspannlitzen versehen. Dreieckförmige Ergänzungen des Profils an den Flanken des Stahlhohlkastens sorgen für einen strömungsgünstigen Überbauquerschnitt. Zur Vermeidung von Pfeilerschwingungen im Bauzustand wurden Kuben an einigen Schäften angeordnet. Die Fertigstellung der Hochmoselbrücke ist für das Jahr 2019 geplant. Inwieweit die neueren Erkenntnisse über das Bodenverhalten des Westhangs die Bauarbeiten verzögern und Planungsänderungen erforderlich machen, bleibt abzuwarten.
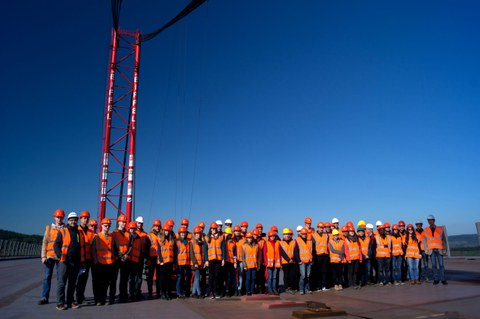
Bild 7. Exkursionsgruppe des Instituts für Stahl- und Holzbau der TU Dresden auf dem Überbau der Hochmoselbrücke
Nach einer kurzen Stärkung verabschiedete sich die Exkursionsgruppe und erreichte an der Saar ihre nächste Station - das Stahlwerk der Dillinger Hütte. Dieses ist mit seiner 325-jährigen Geschichte, über 5000 Mitarbeitern und einer jährlichen Rohstahlproduktion von über zwei Millionen Tonnen führend in der Grobblechherstellung in Europa [2].
Die Teilnehmer wurden von Eric Körtgen empfangen und nach einer kurzen Videopräsentation gemeinsam mit Tobias Graf zur Werksbesichtigung begleitet. Zu Beginn konnten die Studierenden einen der Hochöfen des Stahlwerkes besichtigen, bei dem die Schmelze gerade abgestochen worden war und das flüssige Roheisen zum Weitertransport in einen Torpedowagen geführt wurde. Nach Erläuterungen zur generellen Funktionsweise eines Hochofens und zur Verwendung anfallender Nebenprodukte, wie z. B. Hochofenschlacke, folgte die Besichtigung des Grobblechwalzwerkes, das eines der leistungsstärksten der Welt ist. Hier werden Brammen und Blöcke mit teilweise ungewöhnlichen Abmessungen verarbeitet. Dabei sind Längen bis 36 m, Breiten bis 5 m und Dicken von bis zu 450 mm realisierbar [3]. In Zukunft soll die maximale Dicke noch auf bis zu 600 mm angehoben werden.
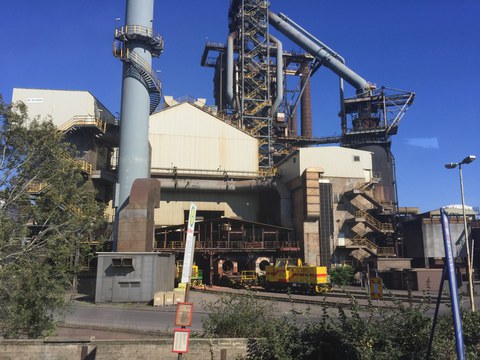
Bild 8. Blick auf das Gelände der Dillinger Hüttenwerke
Vor der Warmumformung werden die Brammen in Stoßöfen auf die notwendige Umformtemperatur von ca. 1.200 °C erwärmt. Nach dem Entfernen der Zunderschicht erfolgt das Walzen zu Grobblechen in Quartowalzgerüsten mit Walzenbreiten von bis zu 5,5 m und Walzkräften von maximal 11.000 t. So können große Blechdicken bei gleichzeitig hohen Umformgraden hergestellt werden [3]. Die Führung im Walzwerk, dicht neben heiß glühenden Brammen und Grobblechen, machte den Werkstoff Stahl für die Studierenden erlebbar und förderte das Verständnis für die Herstellung. Zusätzlich erhielt die Exkursionsgruppe noch einen Einblick in die Steuerzentrale des Walzwerks. Zum Abschluss des Besuchs stellte Herr Körtgen in einer Bustour über das Werksgelände weitere Bestandteile des Unternehmens vor, wie z. B. die Erzhalden, die Kokerei und die Mischbetten zur Vorbereitung der Sinterung. Nach dieser einzigartigen Werksbesichtigung erreichte die Gruppe am Abend des 30.09. die Stadt Wiesbaden und nutzte die verbleibenden Stunden des Tages zu individuellen Erkundungen.
Zum Auftakt des dritten und letzten Tages besuchte die Dresdner Exkursionsgruppe die Baustelle des Ersatzneubaus der Schiersteiner Brücke, die im Zuge der A643 über den Rhein führt und Mainz mit Wiesbaden verbindet. Wolfgang Stremmel von Hessen Mobil und Hans-Jürgen Pätzold von Plauen Stahltechnologie empfingen die Exkursionsteilnehmer auf der Baustelle und stellten das Projekt in einer Präsentation vor. Während der anschließenden Baustellenbegehung konnte sich alle das Brückenbauwerk aus der Nähe anschauen.
Aufgrund des deutlich gestiegenen Verkehrsaufkommens und gravierender Schäden an der 1962 errichteten Brücke wurde der Ersatzneubau notwendig. An der ursprünglichen Rheinquerung, die mit einem Stahlhohlkasten über den Stromfeldern und Stahlverbundbalken über den Flutfeldern ausgeführt wurde, traten Risse insbesondere an Schwachstellen der Schweißnähte auf, die z. T. auf mangelhafte Ausführungsqualität zurückzuführen sind [4]. Die konstruktive Gestaltung der orthotropen Fahrbahnplatte ist wegen der Notwendigkeit zum ermüdungsgerechten Konstruieren heute nicht mehr zulässig. Darüber hinaus verfügt der damals eingesetzte Stahl nicht über eine ausreichende Duktilität senkrecht zur Walzrichtung, sodass Terrassenbrüche aufgetreten sind. Früher lagen noch keine ausreichenden Kenntnisse über dieses Phänomen vor [4].
Im Zuge der Verstärkung der bestehenden Vorlandbrücke auf der Mainzer Seite und dem gesunkenen Rheinpegel stellte sich Anfang 2015 ein Pfeiler schief. Dadurch senkte sich der Überbau schlagartig um ca. 30 cm und riss. Nach zweimonatiger Sperrung, der Anordnung von Hilfsunterstützungen und der Ausführung notdürftiger Reparaturarbeiten wurde die Überfahrt für Fahrzeuge bis 3,5 t wieder zugelassen [5].

Bild 9. Querschnitt der neuen Schiersteiner Brücke im Stromfeld auf der Wiesbadener Seite
Den Wettbewerb für den Ersatzneubau der Schiersteiner Brücke konnte die Grontmij BGS-Ingenieurgesellschaft zusammen mit dem Architekturbüro Ferdinand Heide für sich entscheiden. Der Entwurf der Planungsgemeinschaft ähnelt dem bestehenden Bauwerk. Die Gesamtlänge der Brücke beträgt ca. 1.280 m. Sie ist in 14 Felder aufgeteilt, die von zwei parallel angeordneten Durchlaufträgern überspannt wird. Die maximale Stützweite im Stromfeld beträgt 205 m. Für den sechsspurigen Ausbau weisen die beiden Überbauten eine Breite von jeweils 21,7 m auf. Die Neubauten sind als Balkenbrücken mit stark gevoutetem Querschnitt über den Strompfeilern konzipiert. Die Höhe des Haupttragwerks variiert zwischen 3,3 m im Flutbereich und 8,3 m über den Strompfeilern. In den Hauptstrom- und Nebenöffnungen wird der Brückenquerschnitt als einzelliger Hohlkasten mit orthotroper Fahrbahnplatte in der Stahlgüte S355 ausgeführt. In den Flutbereichen erfolgt ein Wechsel zu Stahlverbundplattenbalken mit Hohlkästen (zweizelliger Verbund-Hohlkastenquerschnitt) und Stahlbetonfahrbahnplatte.

Bild 10. Zweizelliger Verbund-Hohlkastenquerschnitt der Vorlandbrücke

Bild 11. Montagezustand der Schiersteiner Brücke mit Aufvoutung über den Strompfeilern
Der Bauablauf erfolgt mit Rücksicht auf die Nutzung des bestehenden Bauwerks ähnlich wie bei der Talbrücke Münchholzhausen. Im ersten Schritt wurde ein Überbau der bestehenden Brücke abgerissen. Der Verkehr rollt währenddessen über den verbleibenden Überbau. Parallel dazu wird der erste neue Überbau errichtet. Es erfolgen zunächst Montage und Verschub der an das Stromfeld angrenzenden Brückenfelder. Dann wird das vormontierte Stromfeld mit Pontons eingeschwommen und mit Litzenhebern eingehoben. Zum Schließen des vorgehaltenen Montagefreiraums wird eine Vorlandbrücke nochmals um ca. 10 cm verschoben. Die Pfeiler im Flusslauf werden für den Ersatzneubau nach Ertüchtigung wiederverwendet. Nach der Fertigstellung der ersten Richtungsfahrbahn nimmt diese den Verkehr auf, der verbleibende Überbau der alten Brücke wird rückgebaut und an gleicher Stelle durch den zweiten neuen Brückenteil ersetzt.
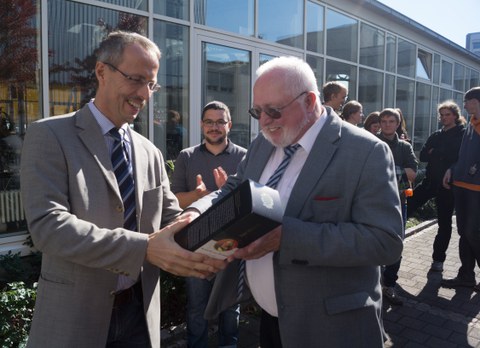
Bild 12. Prof. Dr. Richard Stroetmann (TU Dresden, links) und Karl-Heinz Isselmann (Donges SteelTec, rechts)
Im Anschluss an die Besichtigung der Schiersteiner Brücke besuchte die Exkursionsgruppe das Unternehmen Donges SteelTec in Darmstadt. Karl-Heinz Isselmann stellte das Unternehmen in einer Präsentation vor, erläuterte die Firmengeschichte und gab einen Überblick über das Portfolio bereits realisierter und laufender Projekte. Im Jahr 1872 gegründet, blickt Donges auf eine mittlerweile über 140-jährige Firmengeschichte zurück. 2008 wurde das Unternehmen zu einer Tochter der Mitsubishi Hitachi Power Systems Europe GmbH.
Zu den Kernkompetenzen des Unternehmens zählt der Brücken-, Kraftwerks-, Sportstätten-, Industrie- und Hallenbau. Mit einer produzierten Jahrestonnage von etwa 25.000 t, ca. 350 hochqualifizierten Mitarbeitern und Stückgewichten in der Fertigung von maximal 160 t gehört Donges SteelTec zu den führenden Stahlbauunternehmen Deutschlands. Zu bekannten Projekten des Unternehmens zählen u. a. die Stadionüberdachung der Rhein-Neckar-Arena in Sinsheim, die Elbebrücke Schönebeck, die Flügelwegbrücke in Dresden, das Messeparkhaus in Stuttgart und die Bügelbauten am Berliner Hauptbahnhof.
Im Zuge der von Dr. Peter Schäfer und Karl-Heinz Isselmann geführten Werksbesichtigung konnten die Studierenden die verschiedenen Fertigungsprozesse vom Grobblech und Stahlprofil bis zum fertigen Bauteil verfolgen. Die Palette der Bearbeitungsschritte reichte von der Anlieferung über das Ablängen, Bohren, Stanzen und Schweißen bis hin zum Strahlen und Beschichten der einzelnen Bauteile. Besonders imposant war die aktuell laufende Fertigung von Kesselgerüststützen für den Kraftwerksbau, bei deren Produktion trotz der immensen Abmessungen eine hohe Genauigkeit zur Einhaltung der Fertigungstoleranzen erreicht werden muss.
Nach der freundlichen Einladung zum Mittagessen in der Kantine von Donges SteelTec ging die Fahrt weiter zum Main-Wehr Viereth in der Nähe von Bamberg. Thomas Dietrich vom Wasserstraßen-Neubauamt Aschaffenburg begrüßte die Gruppe und erläuterte das Bauvorhaben in seinen wesentlichen Zügen. Das 1924 errichtete Wehr in Viereth-Trunstadt besteht aus einem zweifeldrigen Walzenwehr, einem Maschinenhaus und einer Schleusenanlage. Durch Heben und Senken der großen Stahlwalzen wird der Wasserdurchfluss reguliert. Für die Feinregulierung werden die Walzen unter das Niveau des Oberwassers abgesenkt und dadurch überströmt. Zur Einstellung großer Durchflussmengen werden sie angehoben, sodass das Wasser darunter abfließen kann. Der Antrieb erfolgt einseitig über Steuerketten und Zahnstangen.

Bild 13. Walzenwehr Viereth-Trunstadt
Da die Walzen des Wehrs nicht mehr dem Stand der Technik entsprechen, Korrosions- und Ermüdungsschäden aufweisen, starke Schwingungen und ausgeprägte Leckagen auftreten, werden sie durch neue, hydraulisch angetriebene Drucksegmente ersetzt. Die Segmentschilde werden oberwasserseitig mit beweglichen Fischbauchklappen ausgestattet, mit denen die Feinregulierung des Abflusses erfolgt. Für große Abflüsse werden die Segmente angehoben und unterströmt. In der Bauphase wird am Oberwasser ein Revisionsverschluss angeordnet, der aufgrund seiner Bauweise auch an anderen Wehren einsetzbar ist. Für die Baugrubenumschließung an der Unterwasserseite kommt eine speziell angefertigte Konstruktion zum Einsatz, deren Tore über Klappscharniere im Hochwasserfall manuell geöffnet werden können. Dies ist notwendig, da das Abflussvolumen über das verbleibende Wehrfeld im Hochwasserfall unter Umständen nicht ausreichend ist. Während der Führung über die Baustelle, die bis 2019 fertiggestellt werden soll, konnten die Steuerkanzel für die angeschlossene Schleusenanlage, das Maschinenhaus und die Baugrube im Unterwasserbereich besichtigt werden.

Bild 14. Tor der Schleuse Viereth-Trunstadt

Bild 15. Trockengelegte Baugrube
Nach dieser letzten Anfahrt im Rahmen der Großen Stahlbau-Exkursion 2015 trat die Gruppe die Rückreise nach Dresden an. Die vom Institut für Stahl- und Holzbau durchgeführte Exkursion wurde finanziell durch die Fakultät Bauingenieurwesen und die Gesellschaft der Freunde und Förderer der Technischen Universität Dresden unterstützt. Hierfür ein herzliches Dankeschön von den Studierenden und den Organisatoren. Ein besonderer Dank geht ebenso an die einladenden Unternehmen, Behörden, deren Vertretern und Mitarbeitern, die nicht nur die gelungenen Besichtigungen ermöglicht und gestaltet haben, sondern auch für eine gute Verpflegung sorgten.
Literatur:
[1] http://www.donges-steeltec.de/fileadmin/user_upload/pdf/480_Muenchholzhausen.pdf
[2] http://www.dillinger.de/dh/unternehmen/daten/index.shtml.de
[3] https://www.dillinger.de/dh/unternehmen/produktion/walzwerk/dillingen/index.shtml.de
[4] Pelke, E., Dieter, A.: Die neue Rheinbrücke Wiesbaden-Schierstein – Wettbewerb und Entwurf. Verlag Ernst & Sohn, Stahlbau 82 (2013), Heft 2, S. 106-121.
[5] http://www.swr.de/landesschau-aktuell/rp/schiersteiner-bruecke-zwischen-mainz-und-wiesbaden-land-will-schadenersatz-fuer-bruecken-gau/-/id=1682/did=16240752/nid=1682/ya0gui/