Great steel construction excursion 2019
Authors: Christoph Schäfer, M.Sc. , Prof. Dr.-Ing. Richard Stroetmann
Shortly before the start of the winter semester 2019/2020, the seventh major steel construction excursion of the Institute of Steel and Timber Construction of the TU Dresden took place from September 30 to October 02, 2019. The total of 19 students from the 4th to 10th semester, accompanied by Prof. Dr.-Ing. Richard Stroetmann and research assistant Christoph Schäfer, were offered a challenging and varied program on the trip through Saxony, Thuringia and Bavaria: the production of steel, the rolling of bar-shaped components, the workshop production of steel components and the assembly of these elements in the construction field. Construction sites for structural steel engineering, steel bridge construction and hydraulic steel engineering were visited to give the students as broad a view as possible of the areas of application of steel construction.
After an early start, Plauen Stahl Technologie in Voigtland was the first destination of the day. After a short introduction into the history, the presentation of the range of services as well as the fields of activity for civil engineers in the steel construction company, a tour through the production facilities followed. Here, the various processing steps, from heavy plate to coated assemblies, could be viewed. The company has existed at the Plauen site since 1885 and has changed its name several times in the course of its history. This is due, among other things, to the division of Germany after World War 2 and reunification. Following the discontinuation of the construction of conventional coal-fired power plants, the company's portfolio of services focuses primarily on steel and composite bridge construction as well as structural steel engineering and hydraulic engineering. Among the approx. 200 employees are numerous civil engineers trained at the Technical University of Dresden.

Abbildung 1: Exkursionsgruppe und Vertreter von Plauen Stahl Technologie
After a joint lunch, the participants continued to the second excursion destination, Unterwellenborn near Saalfeld in Thuringia. There, the Thuringia steel mill with its electric arc furnace and adjoining rolling mill awaited the excursion participants. The guided tour of the Thuringia steel mill began for the group with a brief overview of the company's history and an introduction to steel production. Then it was off to a tour of the plant starting with the scrap yard. Steel scrap in various sizes is used as the starting material, which is melted in the electric arc furnace. During the tour, the excursion participants were able to get an impression of the melting process. It was hardly possible to stay in the furnace hall without hearing protection. Once the steel scrap has been completely melted, the liquid steel moves on to the ladle furnace. Here the excursion participants were able to observe at close range how alloying elements (e.g. aluminum) are added to the melt. Then it was off to the continuous caster. The participants got an impression of the extreme heat as the tour took them along a catwalk that runs over the preliminary sections (beam blanks). A flame-cutting device is used to separate the continuous strands into segments with lengths of 4.50 to 11.00 meters. These then roll on to the next station, the rolling mill, or are stored temporarily to pass through the rolling process later after reheating in the pusher furnace. Before the beam blanks enter the various rolling stands, they are cleaned of oxidized deposits by high-pressure cleaning in the scale washer. Now the participants were able to get an idea of how long a beam blank that was previously just under ten meters long becomes when it is rolled out into a rolled section. In this case it was a cross-section IPE240 which became a total of around 75 meters long. Rolling lengths of up to 100 meters are possible at the Thuringia steel mill, and the process itself is multi-stage. After rolling, the sections, which are still hot up to 950 °C, are measured and the material is material tested by sampling. The rolled section is then pushed onto a 100-meter cooling bed for cooling, which connects the rolling mill with the finishing line. Here, the cooled profiles are straightened and then shortened to the transport length in a sawing line. After the very interesting two-hour tour, the group drove to Suhl in the Thuringian Forest. After checking into the hotel, the participants ended the day with a joint dinner in a nearby restaurant. The next morning, the group left by bus for Würzburg. After a ninety-minute drive, they reached the first destination of the day, the Talbrücke Heidingsfeld. This is a large bridge in steel composite construction, which is being completely rebuilt as part of the expansion of the A3 federal highway near Würzburg. The excursion participants were received at the construction site by Ms. Lewandowska, the construction advisor of the Autobahndirektion Nordbayern responsible for the viaduct, and Mr. Gumbel and Mr. Schulz of the "Talbrücke Heidingsfeld" consortium. The consortium consists of the companies Ed. Züblin AG Direktion Brückenbau Süd-Ost from Dresden and the company Donges Steeltec GmbH from Darmstadt. First, the participants were shown two short films that included the general planning and the planned construction sequence of the bridge as well as the demolition of the existing structure. There were numerous difficulties during the demolition, as the viaduct crosses a railroad line as well as a country road. In addition, there are residential buildings in the immediate vicinity that also had to be protected. At the time of the excursion, preparations were underway to advance the last field. First of all, the participants went to the cycle cellar, where they were introduced to the idea of incremental launching and were able to experience its implementation in the construction field. Then they went to a bridge re-storage facility of the first superstructure, which is currently in operation, where the bridge bearings and the roadway transition could be inspected at close range. Particularly impressive for the participants here was the noise generated by the passing of the roadway crossings, especially by trucks. Finally, they went to the still unfinished superstructure, on which numerous head bolt dowels were protruding. These dowels serve to ensure a sufficient bond between the reinforced concrete carriageway slab and the box girder made of structural steel.
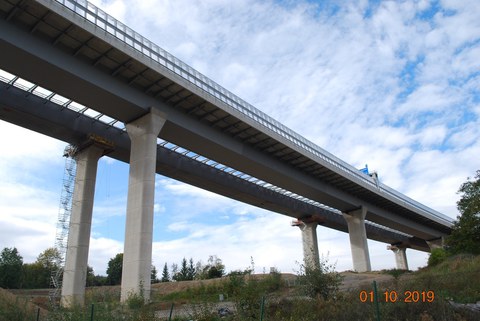
Abbildung 2: Fertiger und befahrener (vorn) und fertigzustellender Überbau (hinten) der Talbrücke Heidingsfeld
In the late morning, the excursion group drove on to the second stop of the day, the production halls of the Max Bögl Group in Sengenthal. After a two-hour drive and a very friendly welcome by Mr. Wulf, lunch first awaited the participants in the company's internal development center. Afterwards, the company group and the steel construction production were presented. A capacity of up to 35,000 tons of steel is an absolute top value in Germany, which can be achieved at Max Bögl mainly by manufacturing the tower tubes of the hybrid tower for wind turbines (WTG) developed by Max Bögl Wind AG. In addition, bridges, halls, storey buildings and other steel structures are also manufactured in Sengenthal. After the presentation, the excursion group took the bus to the other side of the plant site. They passed the precast concrete production facility where, in addition to the usual (semi-)precast elements for solid construction, segments for tunnel tubes and the aforementioned concrete segments for hybrid wind turbine towers are also produced. Arriving at the production halls for steel components, the excursion participants were first guided through the production of tower segments for wind turbines. The particularly high degree of automation in the production of these components was impressive. This was followed by a guided tour through the halls containing the "classic" steel construction production. Here, the participants were able to marvel at the assembly of the structure of the Danube bridge in Linz (Austria). The new bridge construction is characterized by a spatial arch structure that leads to very challenging junctions. After the assembly stations, the tour continued to the coating plant where, among other things, large bridge parts as well as machine girders for large offshore wind turbines with a dead weight of up to 65 tons are coated. From the coating plant, the tour then continued to the coach. The last destination of the second day was Landshut in Lower Bavaria with its very beautiful, historic city center. After the two-hour bus ride and check-in at the hotel, the second joint dinner with wheat beer and typical Bavarian specialties took place. The third and last day of the excursion began with a 20-kilometer bus ride to Vilsbiburg. Here, the students marveled at a hall construction of the company Christmann & Pfeiffer, which is to serve as a new operating site of the mechanical engineering company Flottweg. Later, centrifuges for separating solids and liquids will be produced at this site. These machines can reach centrifugal forces up to 3,000 times the earth's gravity. During the project presentation, particular emphasis was placed on the phases of tendering and awarding contracts, which are of great importance for the economic efficiency of a construction project. Different ideas about the construction costs often clash during the award negotiations. This was also the case with this project. By partially modifying the design and approval planning, it was possible to reconcile the different objectives. This was followed by a tour of the construction site, during which the technical execution and sequence of assembly measures were the focus of the explanations. Part of the roof structure are larger trusses that could not be transported to the construction site in one piece. They were first pre-assembled on the ground and then lifted to the installation site by mobile cranes. The roof purlins were then installed, stabilizing the trusses perpendicular to their plane. In the usual steel hall construction, one starts with a bracing span to which the trusses that are later assembled are connected via purlins. This was not the case in this construction project, as the hall roof trusses are stabilized by reinforced concrete walls (in this case fire walls as defined by the Industrial Construction Guideline). Another focus of the explanations was the assembly and alignment of the crane runway girders. These girders, designed with welded-on flat steel rails, form the track of the bridge cranes to be operated later: Therefore, higher requirements were placed on their dimensional accuracy than for other components. The tour of the construction site was followed by a guided tour of the main plant of Flottweg SE. The name originates from the founding period, when the company still manufactured motorcycles. It was easy to get away with a motorcycle, so the company name "Flottweg" seemed obvious to the founders. During the tour of the main plant of the mechanical engineering company, the differences to the previously visited steel construction companies became clear. Whereas at the steel construction companies, larger components were assembled from heavy plates, at the mechanical engineering company, components are mostly produced by "machining" production techniques such as turning, milling and grinding. Centrifuges have a fast rotating shaft that is supported in a hub. This results in very high demands on manufacturing accuracy and operational stability. The short and very interesting insight into the production of the mechanical engineering company ended with a joint lunch organized by the companies Flottweg and Christmann & Pfeiffer.
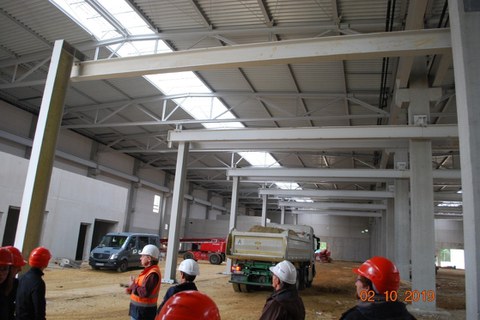
Abbildung 3: Exkursionsgruppe in der neu errichteten Fertigungshalle von Flottweg SE
After lunch, the group went to Viereth-Trunstadt near Bamberg for the last site visit. There, the excursion participants were already awaited by Mr. Dietrich from the Wasserstraßen-Neubauamt Aschaffenburg, the construction manager for the renovation of the Viereth weir. This is a barrage of the Main with a drop of six meters. The roller weir was built in 1925 and has been in continuous use ever since, so that modernization work now needs to be carried out on the facility. One of the two old roller weirs had already been removed, the excavation pit was dry and preparations were being made for the installation of the new pressure segment closure. First, the old removed roller weir was inspected, which was still in good visual condition despite its age. The weir itself was also not the component that caused problems on this plant. Rather, it was the roller locks and the associated toothed rails that were repeatedly damaged. For this reason, after the weir system was rehabilitated, pressure segment closures were used instead of roller weirs. The new gate was pre-assembled and ready for lifting. Mr. Dietrich explained the operation of this closure in more detail. Afterwards, the tour continued over the old footbridges into the drained weir field. This was drained on the upstream side by a floating inspection gate. In the event of a flood, regulation can be achieved by opening segment gates. Furthermore, the excavation pit must be cleared and the lifting gates on the downstream side opened. After the ninety-minute tour, the participants returned to Dresden.

Abbildung 4: Übersicht der im Bau befindlichen Wehranlage: Altes Walzenwehr (vorn) und trockenge-legtes Wehrfeld (hinten)
The Steel Construction Excursion 2019 was financially supported by the Faculty of Civil Engineering, the Society of Friends and Sponsors of the Dresden University of Technology and the Institute of Steel and Timber Construction. Special thanks also go to the inviting companies and authorities , who made the construction site and plant visits possible, provided company representatives and employees for the technical arrangement and, last but not least, ensured good catering for the excursion group.