Subproject 11: Methodical development of active multi-matrix composite (MMC) components
Motivation
Especially in logistics and automation technology, kinematic systems that allow for direct interaction with humans are of great interest. Systems, which are characterized by zero backlash and low wear and which are based on materials with low weight, high flexibility, and high strength, such as fiber-reinforced composites, offer considerable advantages. In this context, novel active multi-matrix composite (MMV) components represent a promising solution approach. The integration of active elements into these MMVs eliminates the need for subsequent actuator application and increases the robustness of the system. However, there is currently no suitable integral design and simulation environment available for the development of active MMV-based systems. For example, the material, composite, and structural properties of MMV - e.g. stiffness, compliance, and damping - cannot yet be included within the development process of the overall system.
State of the art and preliminary research
Cross-scale approaches based on FEM have been established for the calculation of effective material properties of fiber-reinforced composites (FRC). Multi-matrix and hybrid composites for setting locally different property profiles have already been investigated to some extent, although the comparison between experimental and numerical results is still pending. The comprehensive investigation of active composites has already been carried out within the framework of the SFB/TR 39, where the focus was on the technical production implementation for series applications. Kinematic systems in the form of compliant mechanisms with fiber-based stiffness modifications for thermoplastic FRC were investigated by the applicant within the framework of the SFB 639.
Scientific questions and project objectives
DThe overall goal of this project is the methodical development and realization of multi-matrix components with customized deformation patterns and kinematic algorithms for the realization of temporally and locally staggered topologies without rigid body mechanisms. To generate such structures by taking into account the local structure-property relationships, software tools and interfaces must be developed for an integrated development environment in which structural analysis can also be carried out on the basis of multi-scale simulation. This enables individual active MMV components to be considered as an integral overall system right from the design and layout stage. Based on this, novel, morphologically complex and hierarchically structured MMV-based systems and construction methods are to be developed.
Contact
Institute of Lightweight Engineering and Polymer Technology (ILK), Chair of Function-Integrative Lightweight Engineering, Faculty of Mechanical Science and Engineering at TU Dresden
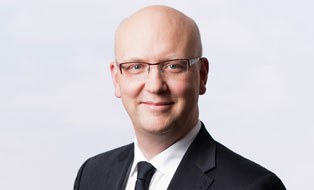
Chair of Function-integrative Lightweight Engineering
NameProf. Dr.-Ing. Niels Modler
Send encrypted email via the SecureMail portal (for TUD external users only).
Institute of Lightweight Engineering and Polymer Technology
Visitors Address:
DÜR, Floor 0, Room 69 Holbeinstr. 3
01307 Dresden
Deutschland