Subproject 2: Continuous in-situ measuring of deformation and stress distribution in I-FRC using structurally integrated 3D sensor networks
Motivation
A sensor system integrated into the textile structure is required for precise, real-time, and in-situ measurements on the deformation and stress distribution of interactive components. Hence, 3D sensor networks consisting of structurally compatible, filamentous, strain-sensitive, and electrical conductors need to be created for degradation and stress condition measurements and fundamentally investigated in terms of their interactions with other I-FRC components.
State of the art and preliminary research
Previous research approaches focused on the development and implementation of textile sensors, e.g. metallic yarns or carbon fibers, using textile-technological fabric formation techniques, such as weaving, knitting, and multiaxial warp knitting for the textile-based, continuous measurement of deformation and stress distribution. Moreover, these sensors were integrated into reinforcement structures and consolidated to interactive FRP components containing thermosetting material. The quality of the force- or form-fit connection between textile-based sensors and load-bearing reinforcing semi-finished product of the FRP is essential for their metrological characteristics (sensitivity, drift, hysteresis); this was proven by investigations conducted within fundamental research projects.
In order to gain local information, unidimensional and longitudinally graded sensors were designed to run along main load axes and successfully implemented in large-scale FRP components, e.g. rotor blades of small wind turbines. Previous research activities were mainly concerned with simple, mostly unidimensional sensor networks for thermoset fiber rubber composites.
Scientific questions and project objectives
The mesoscopic model developed within TP1 (in combination with TP6) will be used to calculate anticipated local/global deformations and stress levels. These calculations are performed to dimension 2D and 3D sensor networks for the directionally selective, spatially resolved, and quantitative determination of deformations generated by actuators through the algorithmic evaluation of superimposed information in terms of elongation, compression, shearing, and bending as well as damage to the I-FRC. In order to create several sensor networks that are integrated into the reinforcement structure and comprise individual, load-adapted sensor paths or loops, textile-technological methods (e.g. varying of incorporation position in multi-layered textile reinforcing structure) are used to generate contact points and isolated areas as well as the interface design. There is a particular need for research regarding the binding-technological modeling of the integration of composite-compatible sensor yarns into the textile reinforcing semi-finished product (type of interlacement or interlooping of yarns and their spatial arrangement within the textile reinforcing structure). These sensor yarns enable the development of load-adapted conductor loops by contacting between several yarn layers and local isolation to avoid shunts. Hence, multi-dimensional sensor networks for the spatially resolved in-situ measurement of complex distortions can be achieved.
Contact
Institute of Textile Machinery and High Performance Material Technology (ITM), Faculty of Mechanical Science and Engineering at TU Dresden
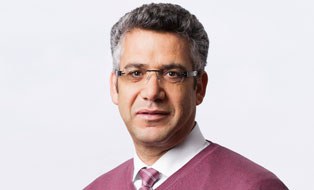
Mr Univ.-Prof. Dr.-Ing. habil. Dipl.-Wirt. Ing. Chokri Cherif
Head of the Institute and the Chair of Textile Technology
Send encrypted email via the SecureMail portal (for TUD external users only).