OPTIFLOW
Model-based flow optimization for fouling reduction in shell-and-tube heat exchangers
Supervisor: Dipl.-Ing. Valentin Scheffel
Duration: 01.08.2024 - 31.01.2027
Funding institution: ERDF/JTF funding guideline Energy and Climate - FRL EuK/2023
Brief description:
Shell and tube heat exchangers play a central role in process engineering processes. Their optimization holds great potential for reducing costs and greenhouse gas emissions. Fouling of shell and tube heat exchangers leads to performance losses, which have to be compensated by increased fuel quantities. The resulting emissions of all refineries worldwide are estimated at approx. 88 million tons of CO2-eq p.a. for 2009. Earlier studies using CFD simulations have shown that the uneven flow through the pipes leads to strongly fluctuating velocity distributions, which causes increased fouling in pipes with a slow flow. Influencing variables such as the tube bundle cross-sectional area (summed area of the tubes), the cross-sectional area of the inlet nozzle, the mass flow and the positioning of the inlet nozzle on the distribution chamber were classified as important factors for further investigations.
Project objective:
The aim of this project is to improve existing guidelines for shell and tube heat exchangers through experiments on a pilot plant heat exchanger and the use of CFD (Computational Fluid Dynamics) model calculations and to develop tailor-made solutions for fouling minimization and performance optimization. The results are to be validated by tests on a shell-and-tube heat exchanger on a pilot plant scale. As a result, costs can be lowered and greenhouse gas emissions, which are additionally caused by inefficient shell-and-tube heat exchangers, can be reduced.
Test systems used/special acquisitions:
A combination of CFD simulations (Computational Fluid Dynamics) and a glass shell-and-tube heat exchanger will be used to investigate the non-uniform flow in a shell-and-tube heat exchanger. The tests on the pilot plant heat exchanger serve to validate the simulation data obtained.
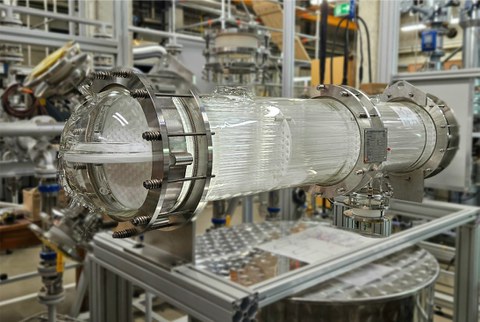
Gläserner Rohrbündelwärmeübertrager
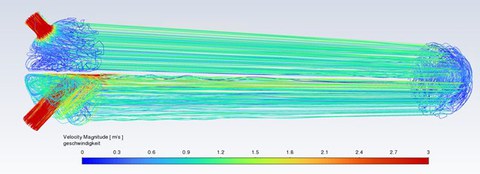
Strömungslinien im Rohrbündelwärmeübertrager
Reports, publications, patents or other copyright laws:
R. Schab, A. Kutschabsky, S. Unz, and M. Beckmann, "Numerical investigation of tubeside maldistribution in shell-and-tube heat exchangers," Heat and Mass Transfer, 2023, doi: 10.1007/s00231-023-03385-5.
R. Schab, T. Dorau, S. Unz, and M. Beckmann, "Parameter Study of Geometrically Induced Flow Maldistribution in Shell and Tube Heat Exchangers," Journal of Thermal Science and Engineering Applications, vol. 14, no. 10, 2022, doi: 10.1115/1.4053633.
R. Schab, T. Dorau, M. R. Malayeri, S. Unz, and M. Beckmann, FlowEnhancer - A Shell-and-tube heat exchanger enhancement that increases Energy Efficiency in the Oil, Gas, Power & Chemical Process Sectors | FlowEnhancer Project | Fact Sheet | H2020 | CORDIS | European Commission. [Online]. Available: https://cordis.europa.eu/project/id/831040 (accessed: Jul. 8 2022).
T. Dorau, R. Schab, S. Unz, R. M. Malayeri, and M. Beckmann, "Impact of flow maldistribution in shell-and-tube heat exchangers," Proceedings of the 12th European Conference on Industrial Furnaces and Boilers, 2020 [Online]. Available: https://infub.pt/Geral/paginas.aspx?cod=138
D. Sumsion et al, "Flow maldistribution in shell and tube heat exchangers," Q4, pp. 85-89, 2019. [Online]. Available: www.eptq.com
Further information:
Association of German Engineers (VDI), Ed., VDI Heat Atlas: Technical Sponsor VDI Society for Process and Chemical Engineering, 12th ed. Berlin, Heidelberg: Springer Vieweg, 2019.
Tubular Exchanger Manufacturers Association, TEMA 9th ED. Standards of the Tubular Exchanger Manufacturers Association, 2007. accessed: Jul. 30 2020 [Online]. Available: https://tema.org/