Promotionen 2024
Diese Seite bietet eine Übersicht über die erfolreich abgeschlossenen Dissertationen am ILK. Durch interdisziplinäre Forschung und enge Industriekooperationen entstehen wegweisende Erkenntnisse. Klicken Sie auf einen Dissertationstitel, um mehr zu erfahren.
Promovent: Gordon Just
Betreuender Hochschullehrer: Prof. Dr.-Ing. habil. Maik Gude
Das komplexe Schädigungsverhalten endlosfaserverstärkter Kunststoffe stellt ein wesentliches Hemmnis bei der Erschließung des Leichtbaupotentials dieser Werkstoffgruppe dar. Die Entwicklung werkstoffangepasster Berechnungsmodelle, die eine zuverlässige Prognose der Verbundschädigung ermöglichen, bildet deshalb eine wichtige Grundlage für die Werkstoff- und Bauteilentwicklung hochbeanspruchter Faserverbundstrukturen.
Die derzeit verfügbaren Schädigungsmodelle sind oft nur auf bestimmte Schichtaufbauten der Faserverbundlaminate anwendbar, berücksichtigen die Zwischenfaserbruchbildung nur in transversal beanspruchten Schichten oder vernachlässigen die für Faserverbunde charakteristische Streuung der Werkstoffkennwerte, die von der heterogenen Mikrostruktur und inhärenten Störstellen bestimmt wird.
In der vorliegenden Arbeit wird deshalb eine physikalisch begründete Modellierung des Schädigungsverhaltens von Faser-Kunststoff-Verbunden (FKV) mit beliebig orientierter Endlosfaserverstärkung hinsichtlich Zwischenfaserbruchbildung bei quasi-statischer
und zyklischer Belastung entwickelt. Das Hauptaugenmerk liegt dabei auf der Entwicklung eines Modellansatzes, der sich durch eine möglichst breite Anwendbarkeit bezüglich des Schichtaufbaus und der Belastung der Laminate auszeichnet.
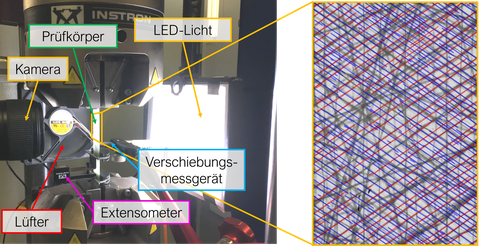
Experimenteller Aufbau zur Messung von Zwischenfaserbrüchen in FKV-Laminaten (links) und erkannte Risse (rechts).
Ausgehend von umfangreichen experimentellen Untersuchungen mit automatisierter Erkennung und Quantifizierung der Zwischenfaserbrüche (vgl. Abb.1) wurde ein vollständig analytisches Schädigungsmodell entwickelt.
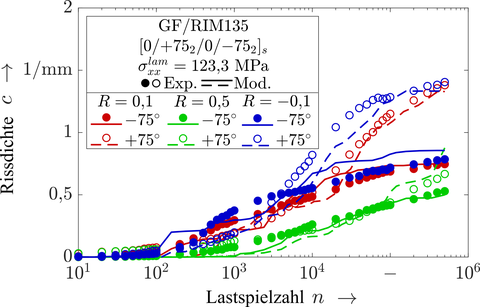
Modellprognose und experimentelle Ergebnisse für ein multiaxial verstärktes FKV-Laminat.
Das Modell nutzt dabei Betrachtungsweisen zur Energiefreisetzungsrate und ermöglicht somit die Berechnung von FKV-Laminaten mit unterschiedlichen Faserorientierung (vgl. Abb. 2) und frei wählbarem Schichtaufbau. Die hohe Prognosegenauigkeit des Modells wurde in der Arbeit anschaulich für quasi-statische als auch zyklische Belastungen dargelegt. Der physikalisch begründete, energiebasierte Ansatz ermöglicht darüber hinaus die Übertragbarkeit des kalibrierten Modells auf bisher nicht experimentell untersuchte Laminatkonfigurationen, ohne erneute Modellkalibrierung oder zusätzliche Experimente. Somit wird eine breite Anwendbarkeit des Modells bei gleichzeitig hoher Flexibilität und kurzen Berechnungszeiten gewährleistet.
Promovent: Dr.-Ing. Moritz Kuhtz
Betreuender Hochschullehrer: Prof. Dr.-Ing. habil. Maik Gude
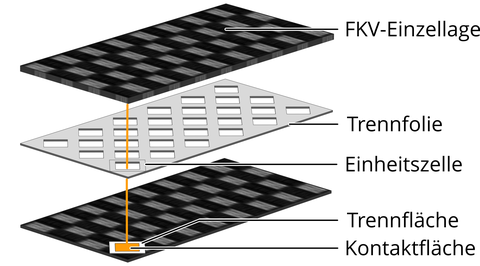
Abb. 1: Konzept der Zwischenschichtmodifikation durch perforierte Trennfolien.
Faser-Kunststoff-Verbunde (FKV) sind aufgrund ihrer hohen spezifischen mechanischen Eigenschaften und ihres guten Energieaufnahmevermögens prädestiniert für den Einsatz in crash- und impactbelasteten Leichtbaustrukturen. Insbesondere kohlenstofffaserverstärkte Kunststoffe zeigen hierbei jedoch ein sprödes Versagensverhalten, das zu katastrophalem Strukturversagen führen kann und ein ungenutztes Potenzial hinsichtlich des Energieaufnahmevermögens darstellt. Das gezielte Zulassen von Delaminationen in impactbelasteten FKV-Strukturen führt zu einer Reduktion der intralaminaren Spannungen, wodurch ein kritisches Faserbruchversagen verhindert werden kann. Als Folge lassen sich sowohl das Energieaufnahmevermögen steigern als auch die Strukturintegrität erhalten.

Abb. 2: Testaufbau für den Impactversuch an generischen Fan-Schaufeln.
Auf Grundlage einer umfangreichen experimentellen Analyse des Einflusses der modifizierten Zwischenschichten (Abb. 1) auf das Werkstoffverhalten werden eine Berechnungsmethodik und eine Methode zur effizienten experimentell-numerischen Parameterbestimmung entwickelt. Mit Hilfe validierter Berechnungsmodelle wird der Einfluss der Zwischenschichtmodifikationen auf das Impactverhalten von FKV-Strukturen aufgezeigt. Als Ergebnis dieser Untersuchungen werden erstmalig Gestaltungshinweise für zwischenschichtmodifizierte FKV-Strukturen abgeleitet. Durch deren Anwendung wird bei experimentellen Impactversuchen an generischen FKV-Triebwerksschaufeln (Abb. 2) eine höhere Energieaufnahme bei gleichzeitigem Erhalt der Strukturintegrität erreicht (Abb. 3).
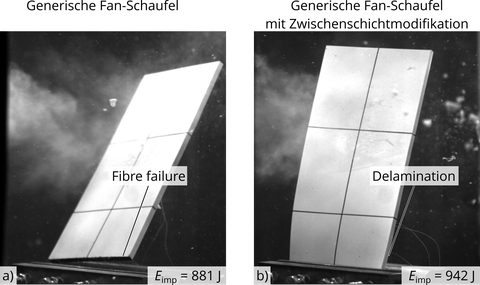
Abb. 3: Versagensverhalten generischer FKV-Fan-Schaufeln ohne Zwischenschichtmodifikation (a) und mit Zwischenschichtmodifikation (b).
Promovent: Dr.-Ing. Michael Müller-Pabel
Betreuender Hochschullehrer: Prof. Dr.-Ing. habil. Maik Gude
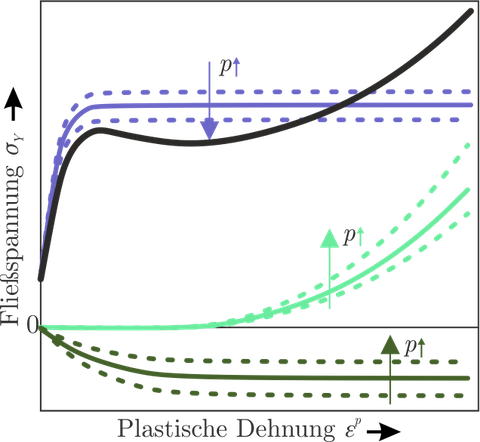
Abb. 1: Schematische Darstellung des Einflusses eines Teilvernetzungsgrades auf das Deformationsverhalten von Epxidharzen.
Duroplastische Polymere bieten ausgezeichnete mechanische Eigenschaften und sind als Matrixmaterial für faserverstärkte Kunststoffe fest etabliert. Aufgrund ihrer netzwerkartigen Molekülstruktur neigen sie jedoch zu sprödem Verhalten und gelten als nicht umformbar. Wird das Netzwerk durch angepasste Prozessführung nur teilweise ausgebildet, zeigen Duroplaste jedoch stark ausgeprägtes plastisches Verhalten, das u.a. für die Entwicklung neuartiger formgebender Fertigungsverfahren interessant ist. Zur Entwicklung derartiger Verfahren fehlten bislang jedoch detaillierte experimentelle Daten sowie darauf aufbauende Materialmodelle, die den Einfluss des Vernetzungsgrades (Abb. 1) auf die mechanischen Eigenschaften korrekt abbilden können.
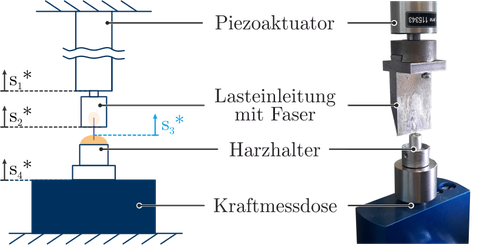
Abb. 2: Hauptkomponenten des entwickelten Prüfstands zur Analyse der Faser-Matrix-Interaktion.
Die Dissertation enthält neben innovativen Prüfmethoden auch geeignete Ansätze zur Beschreibung des Materialverhaltens und zur Faser-Matrix-Interaktion im teilvernetzten Zustand (Abb. 2) und liefert damit erstmals die benötigten Grundlagen zur technologischen Ausnutzung der vernetzungsabhängigen Eigenschaften duroplastischer Matrices.