CAE-Methoden in der Einarbeitungsphase der Blechumformung
Laufzeit: | 10/2008 – 12/2010 |
Finanzierung: | BMWi über die Arbeitsgemeinschaft industrieeller Forschungsgemeinschaften "Otto von Guericke" (AiF), Europäische Forschungsgesellschaft für Blechverarbeitung e.V. (EFB) |
Bearbeiter: | Dr.-Ing. André Hardtmann Dr.-Ing. Lars Penter |
Kooperation: |
|
Zielstellung
An die Maßhaltigkeit von umgeformten Blechteilen und damit an die Werkzeugqualität werden ständig höhere Anforderungen gestellt. Ursachen für Maßabweichungen, die letztlich meist zur Nacharbeit an den Umformwerkzeugen führen, resultieren maßgeblich aus den elastischen Maschinen- und Werkzeugeinflüssen. Diese Einflüsse werden in der derzeit üblichen Werkzeugauslegung nicht berücksichtigt, was mit großer Wahrscheinlichkeit die zur Nacharbeit führenden Differenzen zwischen CAD- und eingearbeiteter Geometrie des Werkzeuges verursacht.
Im Bereich des Werkzeugbaus werden zudem Potenziale zum schnelleren Serienanlauf und zur Kostensenkung in der Verkürzung des Einarbeitungsprozesses gesehen. Deshalb stehen Forderungen nach entsprechender Absicherung der Werkzeugkonstruktion mittels einer prognosesicheren und damit notwendig qualitativ erweiterten numerischen Simulation. Dieses Ziel soll im Vorhaben durch den Ansatz erreicht werden, wesentliche bisher notwendige "Nacharbeiten" vorab in der Werkzeugplanungsphase im Virtuellen zu berechnen und damit bereits bei der Herstellung des "Rohwerkzeuges" zu berücksichtigen. Die Geometrie des Rohwerkzeuges soll damit wesentlich näher an der des Fertigwerkzeuges liegen. Damit soll der notwendige Nacharbeitsaufwand verringert werden.
Lösungsweg
Lösungsansatz ist die Verknüpfung der Umformprozesssimulation unter Berücksichtigung der Maschineneinflüsse mit innovativer Mess- und Auswertetechnik, um die der Simulation zugrunde liegenden Modelle weiterzuentwickeln und damit die Einarbeitung von Umformwerkzeugen wissenschaftlich durchdringen und effektivieren zu können. Das bedeutet:
- Mittels Reverse Engineering soll die "erweiterte Methodenplanung" am realen Einarbeitungsprozess nachgewiesen werden, was bisher nicht erfolgte.
- Mit dem Vergleich der Simulations- und Messergebnisse wird die Realitätsnähe der untersuchten Modelle bewertet.
- Mit der Weiterentwicklung von zur Rückfederungskompensation verwendeten Optimierungsalgorithmen auf die Problematik der Werkzeugeinarbeitung soll die Anpassung der Werkzeugtopologie durch neue Softwarefunktionalität automatisiert ablaufen.
Schwerpunkt der Arbeiten am IWM ist die Weiterentwicklung der FEM-basierten Prozesssimulation zum Umformprozess.
Ergebnisse
Das Vorhaben leistet für die Weiterentwicklung der Simulation von Umformprozessen einen wichtigen Beitrag zur Ermittlung von Randbedingungen und technologischen Parametern bei der Werkzeugentwicklung. Damit kann eine hohe Prozesssicherheit und ein hohe Qualität in Bezug auf die Maßhaltigkeit des umgeformten Bleches gewährleistet werden. Mit einer verbesserten Prognosefähigkeit bei Simulation von Blech¬umformprozessen kann die Zeit bis zum Serienanlauf verkürzt werden, da der manuelle Aufwand bei der Werkzeugeinarbeitung vermindert wird.
Es wurde eine Methode zur Berücksichtigung von elastischen Werkzeugen bei der Umformsimulation vorgestellt, mit der Rechenzeit eingespart werden kann ohne die Ergebnis¬genauigkeit signifikant einzuschränken. Die Methode hat den Vorteil, dass Wirkflächen der Werkzeuge bei der Modellerstellung unkompliziert ausgetauscht oder verändert werden können, ohne dass eine aufwändige Neuvernetzung des gesamten Werkzeuges notwendig ist.
Für die Berücksichtigung der genauigkeitsbestimmenden Einflussgrößen wurde das FEM-Prozessmodell um die elasto-statischen Werkzeug- und Maschineneigenschaften erweitert. Dazu wurden reduzierte Modellansätze verwendet, die das reale Verhalten ausreichend genau beschreiben. Die vollständige Modellerweiterung umfasst auch die Abbildung realer Werkzeug¬wirkflächen durch optische Flächenmessdaten im FEM-Prozessmodell. Dadurch können Effekte der manuellen Werkzeugeinarbeitung und Verschleißerscheinungen im Produk¬tionsprozess bei der Simulation berücksichtigt werden. Das erweiterte Prozessmodell mit der Parametrierung der genauigkeitsbestimmenden Kenngrößen der Pressmaschine nach DIN 55189 ist in Bild 2 dargestellt.
Die entwickelten Prozessmodelle wurden an einem Praxisbauteil verifiziert. Dabei konnte mit jeder Modellerweiterung die Abweichung zum realen Umformergebnis vermindert werden. Der flächenhafte 3D-Vergleich (Bild 3) zwischen dem Ergebnis des vollständig erweiterten Prozessmodells und dem gemessenen Realbauteil zeigt eine gute Übereinstimmung.
Im FEM-Prozessmodell wurden elasto-statische Werkzeug- und Maschineneigenschaften berücksichtigt sowie die Werkzeugoberfläche durch optische Messdaten abgebildet. Durch die relativ geringe Abweichung beim 3D-Vergleich wird die Notwendigkeit und Effektivität der erweiterten FEM-Prozessmodelle nachgewiesen. In weiteren Forschungsarbeiten sind jedoch die Methoden zur Modellerstellung effizienter zu gestalten.
Kontakt
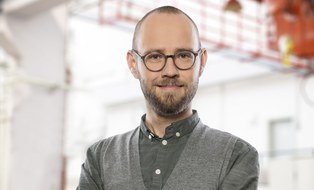
Wissenschaftlicher Mitarbeiter
NameHerr Dr.-Ing. Lars Penter
Oberingenieur Forschung und Lehre
Eine verschlüsselte E-Mail über das SecureMail-Portal versenden (nur für TUD-externe Personen).
Professur für Werkzeugmaschinenentwicklung und adaptive Steuerungen
Professur für Werkzeugmaschinenentwicklung und adaptive Steuerungen
Besuchsadresse:
Kutzbach-Bau, Raum 106 Helmholtzstraße 7a
01069 Dresden