Design and optimization of cooling structures in compact axles based on simulated 3D temperature fields
Table of contents
Project duration: |
07/2022 – 06/2025 |
Funding: | Funded by the German Research Foundation DFG |
Project manager: | Dr.-Ing. Holger Rudolph |
Partner: | Prof. Dr.-Ing. Jürgen Weber
Technische Universität Dresden |
Motivation
The decentralization and modularization of drives is of great importance in various branches of industry such as machine tool construction, vehicle construction, plastics processing and additive manufacturing technologies in order to increase flexibility, adaptability, reliability and energy efficiency and to achieve better performance optimization. Compact axes are increasingly being used for this purpose. Due to high internal heat losses and large temperature gradients, compact axes have a low heat dissipation capacity, which leads to a shortened service life and increased maintenance requirements. There are currently no tools for efficient design and no methods that take into account the heat balance of compact axles both in the design phase and under operating conditions.
Objective of the project
The aim of the project is the successful development of a methodology for the efficient modeling and calculation of the heat balance of compact linear axes and their cooling structure. It should be possible to take into account thermal interactions between fluid circuits and structure, relatively moving structures and the environment. The method is intended to support the modeling of the temporal and spatial temperature field of compact axes as a function of the thermal loads that occur (heat sources and cooling). It should enable the user to easily create thermal models of electrohydraulic axes (EHA) and electromechanical axes (EMA) both in the design phase and for the subsequent operating phase.
Approach
Methods and tools of the SFB/TR 96 for the efficient simulation of fluid technology components and overall systems, for the thermo-energetically intelligent temperature control of machine tool frames and for the fast and high-resolution simulation of relatively moving assemblies of machines with the aid of model order reduction form the basis for the above-mentioned objectives. In this project, these approaches are combined for the first time and transferred to the thermal behavior of compact axes. The focus is on the coupling of flow simulation with heat transport and temperature field calculation in reduced structural models for high-resolution mapping of the heat exchange between structural components and the fluid system. The implementation is exemplified by one electrohydraulic axis (EHA) and one electromechanical axis (EMA) with and without active cooling at Bosch Rexroth AG.
Challenges
A central challenge is the merging of the different simulation domains. In principle, all axle components influence the thermal-energetic behavior, which leads to very extensive models. However, each user group places different demands on the model properties. Component developers require precise knowledge of the heat balance under process conditions and fast calculation of different load states. On the one hand, this involves a high temporal and spatial resolution of the temperature field and, on the other, the analysis of a large number of design variants for long-lasting load conditions. The machine manufacturer, on the other hand, requires the ability to integrate the component model into an overall machine model. This requires software-independent interfaces, fast computability and low memory requirements.
Path to solution
Near-series EHA and EMA with and without cooling are used as integration objects for the models. As a basis for the parameterization and verification of the axis models, the thermal behavior of the axes is first measured (WP1). In WP2, detailed, domain-specific submodels of the integration objects are developed from the experimental data and the axis design data provided by Bosch Rexroth. As a basis for analysis and operating models, the partial models are combined by coupling to form a detailed overall network model in the digital block simulation (WP3). A detailed axis model for analyses accompanying the design is derived from the overall model (WP4). The modeling and simulation methodology is then evaluated on the basis of thermoenergetic analyses. Finally, the compact axis models are evaluated with regard to their suitability for monitoring during operation.
Results
The desired result is an efficient and flexible methodology for the virtual analysis and design of the thermal budget of compact axles, including their cooling structure. This enables
- rapid calculation of models for various issues in the design and operating phase with high temporal and local resolution of the temperature field,
- acceptable temperature deviations of 5-10 % from the absolute value (sufficient for analysis tasks),
- characterization of both axle types (EHA, EMA) in the entire load range,
- an acceleration of the calculations at model and software level by approx. 50%,
- a reduction of the modeling effort by up to 40 %.
Current status
The EMA and EHA are currently being modeled. At the same time, the developed test stands are being manufactured and assembled.
Contact
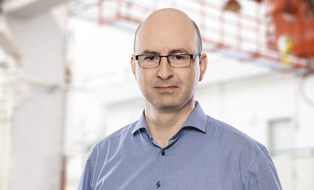
Research associate
NameMr Dr.-Ing. Holger Rudolph
Experimental and numerical machine analysis
Send encrypted email via the SecureMail portal (for TUD external users only).
Chair of Machine Tools Development and Adaptive Controls
Visiting address:
Kutzbach-Bau, Room 207 Helmholtzstraße 7a
01069 Dresden