Entwicklung und Integration von skalierten Simulationsmodellen
Laufzeit: | 02/2019 – 05/2021 |
Finanzierung: | Euronorm |
Bearbeiter: | Dipl.-Ing. Tom Albrecht, Dr.-Ing. Lars Penter |
Kooperation: |
AUSGANGSSITUATION
Durch moderne Simulationssoftware ist es heute möglich, nahezu alle technischen Systeme im virtuellen Raum abzubilden und deren Betriebsverhalten zu untersuchen, noch bevor der erste Prototyp realisiert wurde. Die wesentlichen Ziele umfassender Simulationen im Bereich Umformmaschinen sind konstruktive Optimierungen, Optimierungen des Fertigungsprozesses und die Entwicklung und Auslegung von Antriebs- und Regelungssystemen.
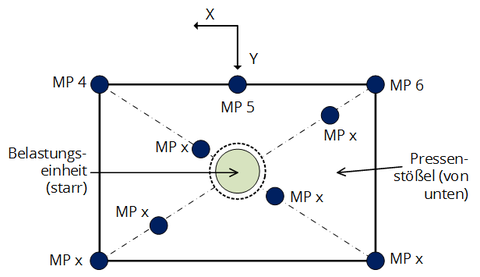
Messpunkte am Stößel
Für einen wirtschaftlichen Betrieb der Umformmaschine müssen hydraulische Antriebssysteme unterschiedlichen Anforderungen genügen. Dazu zählen kurze Verfahrzeiten für hohe Hubzahlen, eine hohe Prozessstabilität sowie eine hohe Energieeffizienz. Weitere wichtige Anforderungen hinsichtlich der mechanischen Pressenstruktur – Pressenrahmen, Stößel und Führungssystem – sind eine ausreichende Steifigkeit zur Aufnahme der Presskräfte, ein ausreichend großer Werkzeugraum, die Zugänglichkeit des Arbeitsraumes mit Auswirkungen auf die Gestellform sowie die Führungsgenauigkeit des Stößels.
Diesen Anforderungen stehen zahlreiche Einflussfaktoren und Zielkonflikte gegenüber, die die Auslegung der mechanischen Pressenstruktur und der elektrohydraulischen Antriebs- und Regelungssysteme erschweren. Die vielfältigen, innerhalb der Umformmaschine auftretenden Effekte und Wechselwirkungen sind bei der Auslegung der Maschine und der Entwicklung der Antriebs- und Regelungssysteme zwangsläufig zu berücksichtigen. Dabei können moderne Simulationswerkzeuge ein wichtiges Hilfsmittel für den Maschinenentwickler sein.
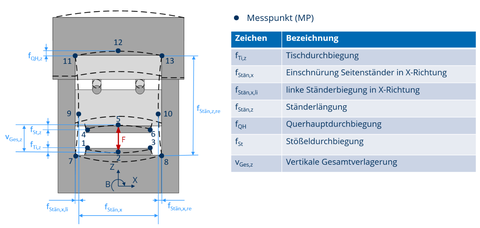
Messpunkte an Pressen zum experimentellen Abgleich mit den Simulationsergebnissen
Ungeachtet der großen Zahl zur Verfügung stehender Simulationssoftware stützen sich heutige Entwicklungsarbeiten hydraulischer Pressen neben experimentellen Erprobungen jedoch überwiegend noch immer auf Erfahrungswerte. Diese Entwicklungsmethodik erschwert die Auslegung der Maschinen, da die Zusammenhänge zwischen den speziellen Anforderungen eines Fertigungsprozesses, den konstruktiven Randbedingungen der Maschine und den auftretenden spezifischen Störgrößen auf das Antriebs- und Regelungssystem nicht in ihrer Gesamtheit vom Entwickler erfasst werden können. Neben nicht optimal ausgelegten Maschinen kann diese Herangehensweise zu deutlich langwierigeren Produktentwicklungsprozessen führen, da die Maschinenkonzepte durch ungenaue oder falsche Annahmen in einer frühen Entwicklungsphase durch mehrere Iterationsschleifen korrigiert werden müssen.
Der Einsatz moderner Simulationssoftware bietet die Möglichkeit der tiefergehenden Analyse auftretender physikalischer Effekte an Maschinen und somit ein beträchtliches Potential zur Optimierung von Maschine, Fertigungsprozess, von Antriebs- und Regelungssystemen sowie zur Effektivitätssteigerung des Produktentwicklungsprozesses. Für eine realitätsnahe Abbildung von Umformmaschinen werden heute verschiedenste Simulationsmethoden eingesetzt. Dazu zählen die 3D-CAD-Modellierung, die FEM-Simulation, die Mehrkörpersimulation (MKS) sowie die Block-Simulation. Die Anwendung derartiger Programme erfolgt bei den Maschinenherstellern bis heute allerdings nur teilweise und in geringem Umfang. Gründe dafür sind der hohe Einarbeitungsaufwand für die effektive Bedienung der unterschiedlichen Simulationsprogramme, der hohe Zeitaufwand für die Erstellung realitätsnaher Modelle sowie die generell fehlende Erfahrung mit Simulationssoftware.
Als Folge der heute üblichen Entwicklungspraxis werden sowohl das Potential von Umformmaschinen hinsichtlich der oben definierten Anforderungen, als auch das Potential für einen effektiven Produktentwicklungsprozess in vielen Fällen ungenügend bzw. nicht ausgeschöpft.
Zielstellung
Übergeordnetes Ziel des Vorhabens ist es zu untersuchen, ob die Auslegung und Optimierung der grundlegenden mechanischen Eigenschaften der Umformmaschine, des reduziert abgebildeten Fertigungsprozesses sowie der hydraulischen Antriebs- und Regelungssysteme anhand einer vereinfachten Modellierung des Gesamtsystems möglich ist.
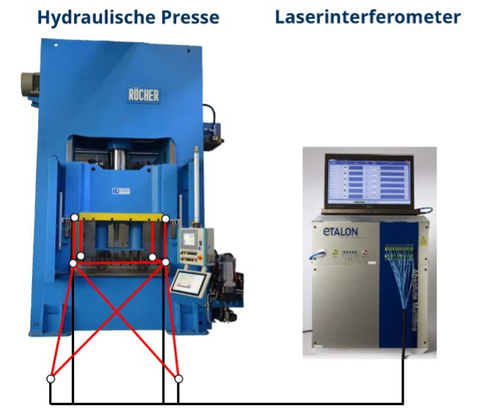
Skizze Versuchsaufbau mit Laserinterferrometer
Ausgehend davon ist zu prüfen, ob die Auslegung einer Umformmaschine in der Entwurfsphase vordergründig auf Basis eines einzigen, reduzierten Maschinenmodells möglich ist und ob eine virtuelle Bewertung der Systemeigenschaften sowie erste Optimierungen auf dieser Grundlage durchführbar sind. In der Vorentwicklungsphase neuer Maschinen, also noch vor deren detaillierter 3D-CAD-Modellierung, könnten mit wesentlich geringerem Aufwand als bisher alternative mit etablierten Antriebssystemen, verschiedene Regelungsstrukturen sowie mechanische Maschineneigenschaften und Parameter des Fertigungsprozesses miteinander verglichen und optimale Konfigurationen entwickelt werden.
Des Weiteren soll die Möglichkeit untersucht werden, derartig reduzierte Simulationsmodelle so zu skalieren, dass sie zur realitätsnahen Abbildung unterschiedlicher Maschinen angewendet werden können. Eine solche Skalierungsmethodik würde die Auslegung von Mechanik, Fertigungsprozess sowie von Antriebs- und Regelungssystemen unterschiedlicher Maschinen mit nur einem einzigen skalierbaren Modell ermöglichen. Darüber hinaus bietet eine derartige Skalierungsmethodik die Chance, vorhandene Umformmaschinen auch ohne genaue Kenntnisse über deren Systemeigenschaften und die komplexen Wechselwirkungen simulativ hinreichend genau abzubilden. Maschinenbetreiber könnten so durch wesentlich geringeren Aufwand als bisher Simulationsmodelle der vorhandenen Maschinen entwickeln, um ihre Fertigungsprozesse weiter zu optimieren.
Ein mit diesem Vorhaben verbundenes zukünftiges Entwicklungsziel ist ein modellbasiertes Entwicklungstool, welches auf dem im Vorhaben erworbenen Wissen und den entwickelten Modellen sowie Methoden basiert. Eine derartige Entwicklungssoftware bietet die Möglichkeit, sowohl Maschinenherstellern als auch Maschinenbetreibern die Vorzüge und Potentiale moderner Simulationswerkzeuge bei der Entwicklung und Auslegung neuer Maschinen und der Optimierung von Fertigungsprozessen bereitzustellen, ohne dass diese in eine zeit- und kostenaufwendige Einarbeitung für den Umgang mit unterschiedlichen Simulationssoftwares investieren müssen.
Kontakt
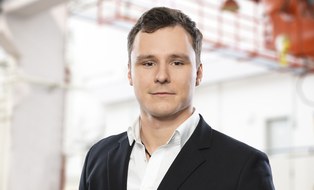
Research associate
NameMr Dipl.-Ing. Tom Morris Albrecht
Machine Technology
Send encrypted email via the SecureMail portal (for TUD external users only).
Chair of Machine Tools Development and Adaptive Controls
Visiting address:
Kutzbach-Bau, Room 106 Helmholtzstraße 7a
01069 Dresden