Thermal forming
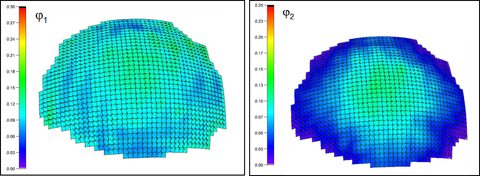
Deformation distributions (principal deformations φ1 , φ2) of shaped spacer structures shaped with a hemispherical punch
Using thermal shaping, two-dimensional, plane materials are smoothed out, folded once or multiple times in a defined fashion, or seamlessly shaped into three-dimensional structures by means of mechanical and thermal effects using the fiber-specific glass transitioning temperature. To produce innovative textile products or textile semi-finished products, these shaping processes are often used in conjunction with sewing and welding technologies. In thermal shaping, a lasting distension/molding in the third dimension is achieved.
Apart from that, the areal shaping of textile structures (e.g. multiple folding of textile structures) is used to increase the active filtering area in the cross-section of textile filters.
The interdisciplinary research activities include the material-adapted, thermo-mechanical design of shaping processes and tools. Adjustments to the machine and process parameters for the various techniques (fixing, ironing and finishing) are made largely empirically in an extensive trial-and-error process. The structure of the materials to be processes varies greatly due to the diversity of fiber materials, threads, fabric structures, finishing effects, and their possible combinations. Most information is not available when setting the process parameters of pressure, temperature and retention time. One challenge is posed by understanding the unstable states of heat transmission and the mass transfer from the porous textile goods to the turbulently streaming water vapor (medium).
The research activities are centered on the converse relations between technological influences in shaping, the microprocesses within the textile material, and the effects of the latter on the shaping results and the quality of the final surface effect. Understanding of the processes within the material is applicable to other areas of the textile production chain.