C3-I: Servo-hydraulic testing machine
Table of contents
Project data
Titel | Title C3-I: Servohydraulische Prüfmaschine | C3-I: Servo-hydraulic testing machine Förderer | Funding Bundesministerium für Bildung und Forschung (BMBF); Projektträger: PT Jülich / C³ – Carbon Concrete Composite Zeitraum | Period 08.2016 – 12.2018 Projektleiter | Project manager Prof. Dr.-Ing. Dr.-Ing. E.h. Manfred Curbach Bearbeiter | Contributor Dipl.-Ing. Karoline Holz Projektpartner | Project partners - |
Report in the year book 2017
UNIVERSAL TESTING MACHINE 2500 KN STATIC / 500 KN DYNAMIC
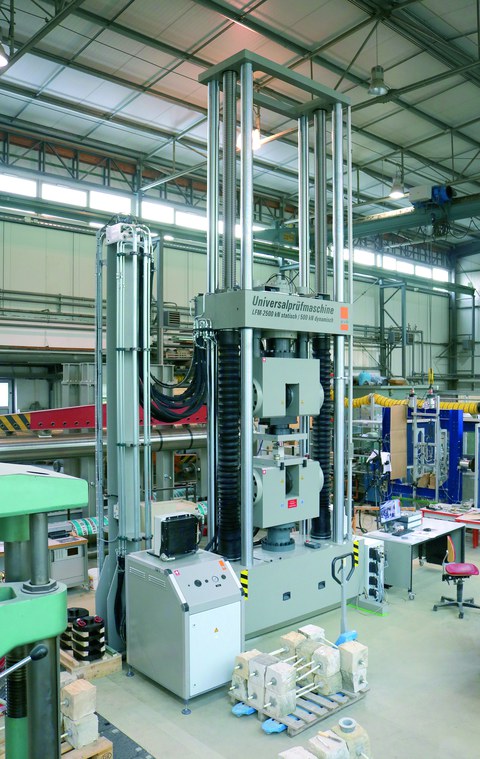
New servo-hydraulic testing machine in the OML
Since October 2017, a four-column universal testing machine with a tensile and pressure range with a maximum static load of 2500 kN and a maximum dynamic of 500 kN is now part of the equipment of the Otto-Mohr-Laboratory.
The machine is a custom product. It is suitable for dynamic long-term / endurance tests up to 25 Hz. The maximum free test length is 3100 mm. Thus, the machine reaches a total height of over 6 m. Flat and round samples can be easily fixed by hydraulic clamping. The samples can be installed with a possible free sample length of 500 mm above or below the clamping in the machine.
To apply the static loads, the crosshead is raised or lowered electromechanically with two ballscrews. The dynamic forces are applied via synchronised cylinders located on the crosshead, and supplied with oil from the existing central hydraulic unit. The maximum amplitude in the dynamic test range depends on the test frequency; for example, samples can be tested with a frequency of 10 Hz and an amplitude of 7.5 mm.
The machine will be used to handle the numerous tests in the research project C3 – Carbon Concrete Composite, e.g. to determine the tensile strength of rods or tendons made of carbon fibres under static and dynamic loads. Due to the universal construction of the machine also tests on other materials are feasible.
The machine control enables a force, distance or strain control and is freely programmable. It contains pre-programmed test programs for tendon tension tests according to ETAG 013, steel tensile tests according to EN ISO 6892-1 and pressure tests of building materials according to EN 12390-3. The data collection of all measurement signals is done synchronous with a maximum sampling rate of 14.4 kHz.
In the case of prestressing elements made of carbon, a greater variety of anchorages and construction types for the tensile members was found. In addition to carbon lamellas and strands, there are bars, couplings and strand loops available on the market. However, due to their differing material properties, the solutions of steel anchorages cannot be transferred directly to carbon. Therefore, a new type of clamping member and its associated anchoring is necessary, one which can meet the requirements of the construction industry. The development of compact anchoring elements is part of the composite project C3-V4.2 – pre-stressed carbon concrete for road bridges, plates and shell structures – which examine the entire range of pre-stressed carbon concrete.