C3-B3: Standardised test methods as well as safety and design concepts
Table of contents
Project data
Titel | Title TP C3-B3-I-a: Entwicklung von Bemessungs- und Sicherheitskonzepten sowie standardisierter Prüfkonzepte zur Materialcharakterisierung von Carbonbeton im Basisvorhaben C3-B3: Konstruktionsgrundsätze, Sicherheits- und Bemessungskonzepte sowie standardisierte Prüfmethoden für Carbonbeton | TP C3-B3-I-a: Development of safety and design concepts as well as standard test concepts for the material characterisation of carbon reinforced concrete as part of the basic project C3-B3: Construction principles, safety and design concepts as well as standardised test methods for carbon reinforced concrete Förderer | Funding Bundesministerium für Bildung und Forschung (BMBF); Projektträger: PT Jülich / C3 – Carbon Concrete Composite Zeitraum | Period 01.2015 – 06.2016 Verbundvorhabenleiter | Leader of the joint research project Prof. Dr.-Ing. Dr.-Ing. E.h. Manfred Curbach Leiter Teilvorhaben | Subproject manager Prof. Dr.-Ing. Dr.-Ing. E.h. Manfred Curbach Bearbeiter | Contributor Dipl.-Ing. Elisabeth Schütze, Dipl.-Ing. Karoline Holz, Dipl.-Ing. Jörg Weselek Projektpartner | Project Partners Institut für Statik und Dynamik der Tragwerke (ISD), TU Dresden | Technical Center – Baustofftechnik, Implenia Construction GmbH, Leipzig | Betonwerk Oschatz GmbH | Dlubal GmbH, Leipzig | Fraunhofer Zentrum für internationales Management und Wissensökonomie (IMW), Leipzig | Ingenieurbüro Grassl GmbH, Berlin | Hentschke Bau GmbH, Bautzen | Institut für Betonbau (IfB), HTWK Leipzig | MFPA Leipzig GmbH | Institut für Massivbau, RWTH Aachen | SCALE GmbH, Dresden | SKZ-KFE gGmbH, Halle |
Report in the year book 2016
The responsibility for failure
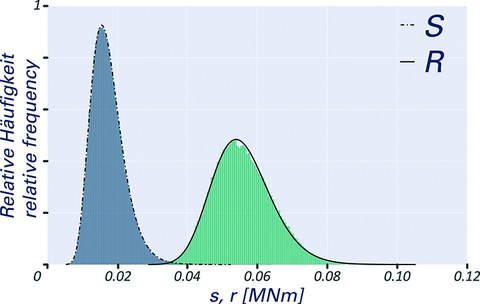
Frequency distributions of Stresses S and Resistance R of a rectangular concrete cross section reinforced with carbon
The reliable failure prevention of load-bearing structures is mandatory and can be considered a dominating subject of civil engineering. To ensure reliability, structures subjected to various forces throughout their entire, pre-defined lifespan shall be designed by making use of an appropriate utilization of resources. The requirements can be summarized as load capacity, serviceability, and durability. For the establishment of new building methods, successfully complying with the reliability requirements may prove to be difficult.
In this context, this paper investigates the calibration of a safety range, which should include the natural data spectrum related to the material property values of those structures constructed with carbon and concrete – also known as carbon reinforced concrete.
A simulation of the ultimate limit state (ULS) for a cross section is implemented in a so-called Monte-Carlo analysis. The ULS marks the border between survival and failure. Within the mentioned analysis, it is possible to sample discrete occurrences of influencing parameters and properties of the materials and geometry respectively. Those could be, for instance, the strength of carbon or the effective depth. Similarly, within such a model, the stresses can also be introduced as randomly distributed. Finally, the corresponding resistances (R) and stresses (S) are ‘counted’ and recorded in a frequency diagram. Subsequently, the number of occurrences within the overlapping area could be determined and, considering the overall number of samples, the probability of failure (Pf) can be calculated for a given case. The complement of Pf can be used to describe the reliability of a structure.
Furthermore, from the manufacturer’s point of view, the quantification of the influences within the model could be interesting. Keeping in mind quality control, it is relevant to know, whether scattering of the material property values – e.g. the strength of carbon – affects the probability of failure of the final structure or not. And if it is so, whether it can be expressed as a value. A specialized sensitivity analysis was found to be a very useful tool. The result can be depicted in bar charts or, even easier to read, in a sketch of the contributing material and geometric relations where the size of the symbols corresponds to the influence of the respective variable.
Carbon concrete swings
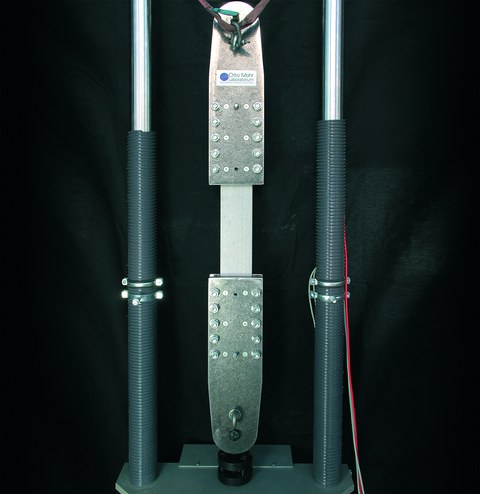
Setup of a cyclic tensile test
One of the most important requirements for a broad application of a new material in the construction industry is the availability of reliable material characteristics, which can be used to determine the load-bearing behaviour of structural elements. As this requirement was seen as an essential first step toward introducing the material into the market, standard test methods for a reproducible characterization of bond and tensile load bearing behaviour were determined within the basic project C3-B3 of the project C3 – Carbon Concrete Composite.
Subsequently, testing facilities for the assessment of tensile load bearing behaviour and bond behaviour under non-predominantly static, cyclic loads were to be developed and tested, since a characterization of the fatigue behaviour of carbon concrete was needed for an even wider range of applications. For this purpose, existing and newly developed test methods were continuously refined and optimised in cooperation with the partners MFPA Leipzig GmbH and RWTH Aachen University. The standardised setup for tensile tests applied here proved to be very suitable for cyclic testing on the composite material carbon concrete and the determination of material characteristics. In the tests, for instance, the impact of load frequency and load level on the material behaviour was evaluated. It turned out that limiting the test frequency to a maximum of 10 Hz is advisable. Higher frequencies – up to 30 Hz were tested – lead to resonant oscillation of the specimen. Moreover, by varying load level and amplitude, an identification of the stress dependence of the fatigue behaviour, was attempted. Current results suggest a dependence on mean stress. However, this has yet to be verified by further research.
To clarify, whether the application of dynamic loads leads to an increase of specimen temperature, temperature development was investigated experimentally in one of the fatigue tests. With an infrared camera, a significant temperature increase of the test specimen of up to 10 K compared to the ambient temperature was observed. Around the cracks the temperature was up to 3 K higher than on the other parts of the specimen surface, indicating that friction between concrete and reinforcement causes increased temperatures especially around the cracks. The fatigue behaviour of the bond between carbon and concrete is still the subject of current research that is being continued within further subprojects of C3.
Report in the year book 2015
Well tested is half approved
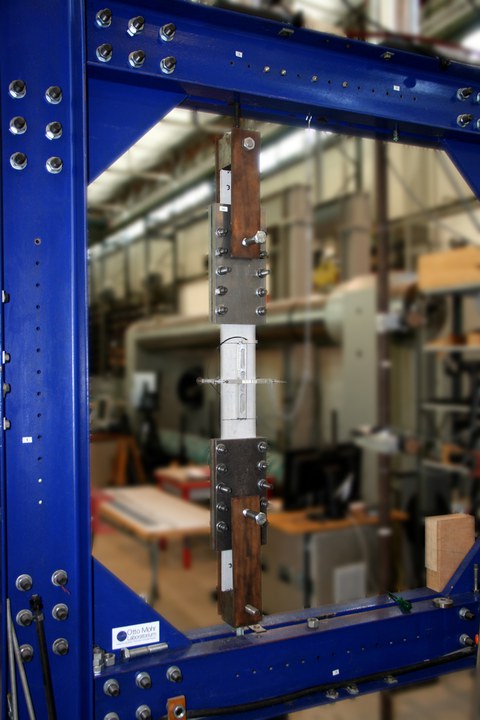
Sieht so der zukünftige Standardzugversuch aus?
The increasing interest in the practical application of carbon concrete over the past years caused a growing demand for approvals, standards and guidelines. However, for standards and approvals – and thus for the successful application and distribution of carbon concrete – not only calculation models and safety concepts are required, but also all the material characteristics of the composite must be known. But, what are the essential characteristics? and how can we determine them? As various research centres throughout Germany, as well as abroad, are currently studying carbon concrete, diverse answers to this question can be found and there are no binding recommendations as of yet. There is a general consent that tensile load bearing behaviour and bond behaviour are the key characteristics. As to the applicable test methods, on the other hand, there are several approaches. The resulting diversity of available test methods makes it hard to identify comparable and reproducible characteristics. Thus, establishing the determined characteristics as a base for obtaining any type of approval is complicated. In order to provide reliable values, and thereby to simplify the necessary processes, uniform – standardized – test methods are required. Hence, defining standard test methods is an important step towards simplification, optimization and quality assurance for carbon concrete construction.
So what are the requirements for such a standard test – shall the requirements be for bond behaviour, for tensile behaviour or for other material characteristics? And how will the appropriate standard test procedure look like? At present, we are taking the first important steps to answer these and other questions in the basic project B3 within the project C3 – Carbon Concrete Composite. Here, test procedures for bond and tensile behaviour are compared in round robin tests between partners of TU Dresden, RWTH Aachen und MFPA Leipzig GmbH. Subsequently, standard test methods for the material characterization of carbon concrete are defined. These activities will then be continued in the C3 project V1.2 by developing verification and test concepts for standards and approvals.
Light. Economic. Safe.
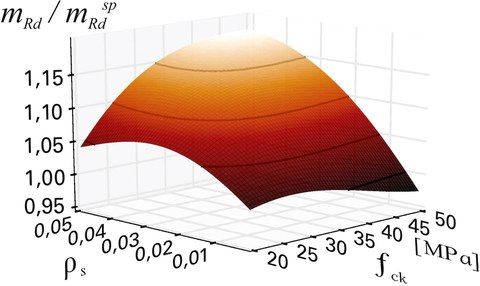
Response surface for the ratio of the probabilistic and semi-probabilistic calculation of a strengthened cross section
Textile reinforced concrete (TRC) attains increasing attention among experts. Few years ago, this topic was just attributed to scientific circles. To become a part of the state-of-the-art in the construction industry, an economic fixation of the safety margin, that ensures a sufficient reliability of its construction elements, is required. For this purpose, the resistance and the load side, in the design equation, are decoupled by the commonly used partial safety concept. On both sides, coefficients are added to consider unavoidable scattering effects.
Subsequently, a method is needed to determine this decisive factor on the resistance side for TRC as a novel material, due to the lack of experience on which basis other partial safety factors had been calibrated in civil engineering. In fact, the aim should be a compromise between an economic design on the one hand, and a sufficient safety level, which marks the minimal boundary, on the other.
Assuming an operational safety level, which is comparable to those of existent constructions, a realistic probabilistic model for an engineering model of strengthened beams is built. It is based on the First Order Reliability Method (FORM), where uncorrelated scattering parameters are adopted to calculate the load capacities of various structure samples. In terms of a pre-set failure probability, the theoretical resistance of this structure, with numerous combinations of input variables, e.g. concrete strength or percentage of reinforcement, can be determined by the response surface method.
It is also possible to carry out the calculations under simplified preconditions, where the input variables are defined as fixed values, e.g. mean values or quantiles for the material strengths. The scattering character of them is considered by the mentioned partial safety factors. Simply put, this procedure is known as the semi-probabilistic safety concept. But one value needs to be set; the desired partial safety factor for TRC under tension, γt*.
By comparing the results from the, more realistic, probabilistic and the simplified semi-probabilistic calculation – for the corresponding combinations of input variables – the determination of the safety margin for each combination is possible. Under equal conditions, if the ratio of these calculations does not fall below the value of 1.0, it can be said, that the safety level is sufficient. On the counterpart side, high ratios indicate an uneconomic usage of TRC within the design model.