Light bearing ceiling elements made of TRC for the building in the stock
Table of contents
Project data
Titel | Title Produkt- und Verfahrensentwicklung von leichten tragenden Deckenelementen aus textilbewehrtem Beton für das Bauen im Bestand | Product and process development of light bearing ceiling elements of textile reinforced concrete for the building in existing Förderer | Funding BMWi; Projektträger: AiF Projekt GmbH Zeitraum | Period 07.2014 – 06.2016 Leiter | Project Manager Prof. Dr.-Ing. habil. Ulrich Häußler-Combe Bearbeiter | Contributor Dipl.-Ing. Tilo Senckpiel Projektpartner | Project partners ASSMANN BERATEN + PLANEN GmbH, NL Dresden | BCS Baustoff Control Service GmbH & Co. KG, Dresden | Dipl.-Ing. H. Bendl Hoch- und Tiefbau GmbH & Co. KG Sebnitz | Sächsisches Textilforschungsinstitut e.V., Chemnitz |
Report in the year book 2016
The future of the Prussian cap
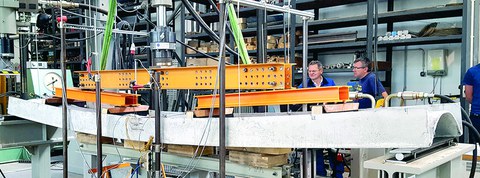
6-point bending test on a 4.5 m ceiling element
The development of light, load-bearing ceiling elements made of textile reinforced concrete for use in existing buildings is the goal of this R & D project, which is pursued jointly by business and research partners. The business sector partners are developing the technology to produce the ceiling elements. At our institute, we carry out the small and large-scale component tests which form the basis for a design model.
The project’s aim is to make the ceiling elements portable and mountable by hand, so that the use of hoists is no longer required. This constructability feature demands the elements have minimal weight. To be able to install a component with the required dimensions (60 cm wide, 20 cm high), the shape of the ceiling elements must be optimally formed, and a very efficient material needs to be chosen. The search to fulfil these requirements led to the shape of a barrel shell with two lateral, vertical upstands. The 1 cm slender shell cross section resulted from a chain line. To optimize the material, the project partners have adopted a dual strategy: on the one hand, ceiling elements are constructed in the classic carbon concrete construction technique; on the other hand, the elements are made with the help of a newly developed technology. The carbon reinforcement is supplemented by a nonwoven, concrete soaked fabric, which simplifies the production of the ceiling elements but also affects the material’s behaviour.
For the investigation of this new composite material, pressure and tensile tests were carried out in the Otto Mohr Laboratory. In addition to the manufacturing and technological advantages provided by the two kinds of reinforcing fabrics, using this method has an influence relative to the load-bearing capacity (e.g. first crack level), the durability (e.g. crack distances) and the ductility (area under the stress-strain curve).
The production of 4.5 m long ceiling elements is possible with classic carbon reinforced concrete as well as with the alternative variant. The elements, which consist of the concrete soaked nonwoven and carbon reinforced fabric, were examined in large-scale, six-point bending tests. On the basis of the results, it was verified that the ultimate and the serviceability limit state checks were fulfilled.
Report in the year book 2015
NTRC ceiling elements
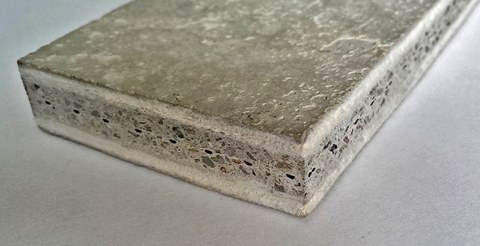
NTRC composite
The aim of the research project “Product and process development of lightweight ceiling elements made of textile reinforced concrete for existing structures” is to develop components which can be transported and installed manually – i.e. without hoists – in an existing building. A basic requirement is to produce elements with the lowest possible weight. This can be accomplished by finding an optimal shape and geometry in combination with a suitable kind of material.
The 3 m long and 60 cm wide components are composed of a barrel shell and two adjacent vertical webs. The development of these ceiling elements goes hand on hand with the development of a new composite material. This step is necessary because the production of curved textile concrete elements is relatively complicated when using the current manufacturing methods (laminating, spraying or casting). Through a further development of textile reinforced concrete (TRC), the project partner BCS has been achieving improvements in terms of the outer shaping of the ceiling elements and the stability of the inner layer of the textile. For this, layers of concrete saturated nonwovens – called fleece concrete composite (FCC) by the manufacturer – had been added to the known TRC, resulting in a new composite material that is referred as NTRC (nonwoven / textile reinforced concrete). The FCC layers are also suitable as a substitute for the otherwise necessary space holders, which must usually be added to the textile scrim by hand.
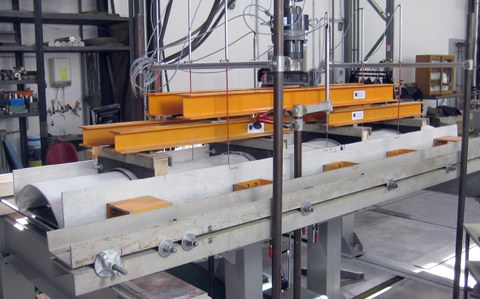
6-point bending test on a NTRC ceiling element
The structural behaviour of the produced ceiling elements have already been investigated in six-point bending tests. Both, the force-deflection curves of the load tests and the stress-strain curves of tensile tests on NTRC tensile specimens, are characterized by a low dispersion, i.e. a high uniformity in production and a high local stability of the textile scrim.
Computational analyses are carried out with the help of finite element models along with the experimental studies. First, the simulation models are calibrated using the determined material parameters of the tensile tests, and they are then validated using the results of the bending tests.