Material development and testing of prefabricated TRC parts for large containers
Table of contents
Project data
Titel | Title |
Report in the annual report 2020
CRACKING THE CODE OF FINE CRACKS
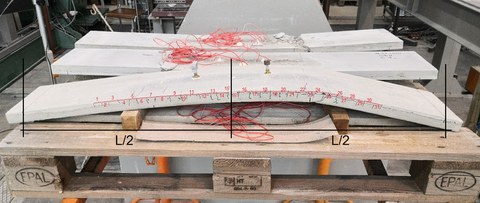
Test specimen after failure
Cracking under pressure is a common condition, but keeping it together when all has cracked is a challenge. In concrete, we expect to see crack formation under loads. The use of textile reinforced concrete (TRC) considerable reduces the crack spacing and width. This particular property makes TRC an ideal material for the construction of silos, not only for structural reasons but also for hygienic ones. Large cracks can lead to the growth of bacteria on the surface of large reservoirs that hold food or liquids. The planning and testing of prefabricated modular elements for silos are the focus of the TextonSilo project. The chosen material is Nonwoven-Textile Reinforced Concrete (N-TRC) – a combination of Carbon Reinforced Concrete (CRC) and Concrete Soaked Nonwoven (CSN) arranged as layers, which form sandwich elements. Special concrete mixes have been developed and further optimized for this purpose.
Therefore, during the first phase of the project, the material behaviour was characterized using small scale tests at the Otto Mohr Laboratory. The tests conducted provided a first glance at the characteristic values of the individual components and also at their composite behaviour. When positioned at the bottom of the sandwich element that is subjected to flexural loads, the relatively ductile CSN layer provides an improved crack distribute on the tension surface. Accordingly, the test results show that the CSN layer considerable reduces the crack spacing and width, even beyond the typical crack distributions observed in TRC elements. This behaviour allows for large deformations at failure and increases the ductility of the material.
From a constructability point of view, the nonwoven geotextile layer is impregnated with
concrete (CSN) and formed into the desired shape. Once the concrete has hardened, the CSN element has the advantage that it can act as a stay-in-place formwork. A further benefit is the rough surface of this material, which prevents the formation of cold joints between the layers of the sandwich element. Also, the irregularities in the material surface, due to the random distribution of nonwoven fibres, provide a natural distance holder for the textile reinforcement. This in turns ensures a good bond between the reinforcement and the fresh concrete.
Report in the annual report 2019
TEXTONSILO – FROM THE IDEA TO THE IMPLEMENTATION
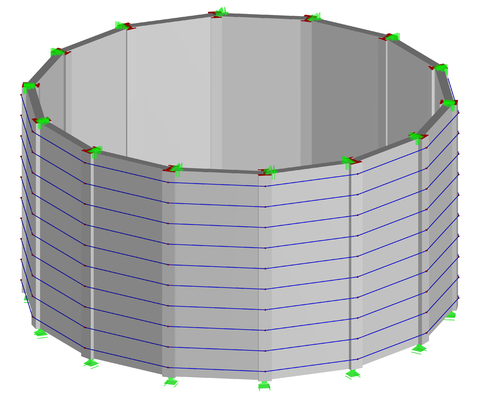
3D visualization of the container
The development of a container that can be manufactured in carbon concrete is led from the initial idea and design to the testing of first prototypes. In comparison to the previous technologies in container construction, the planned element construction method made of textile concrete with external prestressing and support frame structure represents a more flexible and globally applicable way of container construction, which does not require any specialist companies at the construction site. The new construction method also enables temporary installation of the large containers so that they can be used later at another location.
The individual elements, which will be assembled into a 10-metre-high container with a diameter of 20 metres, have a length of 4.25 metres. The need for concrete can be significantly reduced by integrating hollow bodies into the individual component without having to reduce the static height and thus the bending capacity of the component.
Together with the project partners, the component geometry will be optimized with respect to the expected loads of a container with a height of 10 meters and a diameter of 20 meters for the storage of wheat. The reinforcement will be adapted to the tensile stresses occurring in the cross-section.
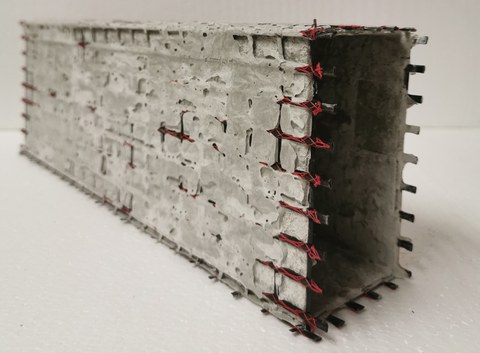
Concrete impregnated fleece with reinforcement as integrated formwork
An integrated formwork consisting of a concrete-impregnated fleece is used for the production of the hollow bodies lying in the component. To stabilize the shape of those hollow bodies, a textile reinforcement is also integrated into this fleece, which is also involved in load transfer. The components will be produced in a vertical formwork having a height of 4.25 metres. For this purpose, a mixing and filling station, which is adapted to the properties of the concrete designed for the components, will be developed.
The material development and testing of precast parts made of textile concrete for the construction of these containers take place at the Institute of Concrete Structures.