Space-enclosing components of textile reinforced concrete under high temperature stress
Table of contents
Project data
Titel | Title
Raumabschließende Bauelemente aus Textilbeton unter Temperaturbeanspruchung | Space-enclosing components of textile reinforced concrete under high temperature stress |
Report in the yearbook 2015
TRC under high temperature exposure
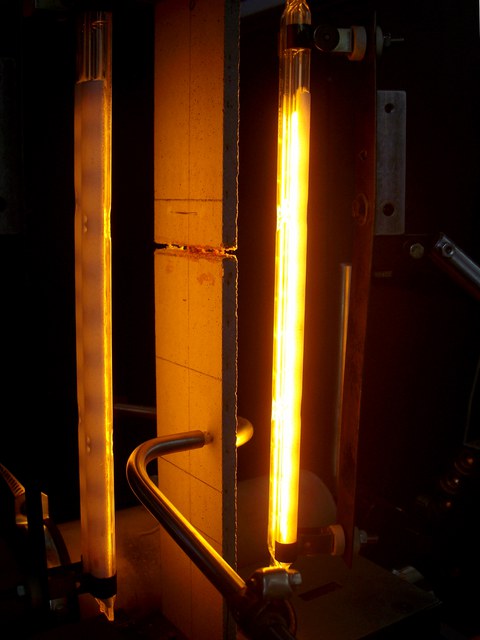
Pull-out test on a TRC specimen under temperature loading
The field of application of textile reinforced concrete (TRC) is constantly expanding by several research and development projects. Textile reinforced concrete façades are already established. Practical applications underline this fact, for example the Soccer City in Johannesburg. Weight reduction is one main benefit of thin TRC plates. Convenient features, for example simple transportation, easy installation and light dimensioning of the primary bearing structure, are only some of the advantages. The limited knowledge about the material behaviour of TRC, when subjected to high temperatures, such as fires, restricts the practical use of TRC façades. As a result of this project, new insights about the behaviour of TRC under high temperatures could be found.
First, an optimization of the basic materials was done. Our partners at the Institute of Textile Machinery and High Performance Material Technology (ITM) developed a high temperature resistant coating for textile reinforcement. Thereby, the new coating guarantees the force transmission between reinforcement and concrete under high temperatures. To improve the fire resistance of the concrete, polypropylene (PP) fibres were added to the mixture. The PP fibres melt at temperatures about 120 °C. The result is additional pore volume within the matrix. Now, the water vapour that results from the evaporation of water trapped within the matrix can expand without causing a high internal pressure, which could lead to concrete spalling.
Further investigations of the fine-tuned materials followed in the form of uniaxial tensile and bonding tests under different temperatures. The results show a substantially improvement of the load bearing behaviour of the modified TRC. For example, in pull-out tests at 200 °C, a five time higher characteristic bond value was detected with the optimized materials, as with normal materials.
Furthermore, an analysis of the temperature fields from the façade panel followed, which was developed within the project. The modelled construction correspond to a three layer sandwich construction, consisting of a 3 cm thick TRC plate, a 6 cm thick vacuum insulation panel and a second 1,5 cm thick TRC plate. Finally, large scale fire tests, with temperature measurements, were done under realistic conditions. A good correlation between simulation and large scale fire test was reached.
Report in the yearbook 2014
Textile reinforced concrete slabs under high temperature
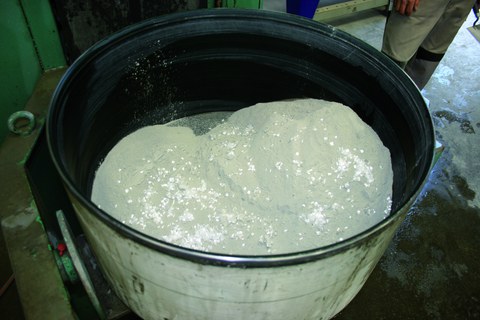
Dry concrete mixture with polypropylene short fibers
The design of facades by using textile reinforced concrete (TRC) slabs is on the rise. Using only 2–4 cm thin structural elements, it is possible to make huge savings due to a lower self-weight compared with that of relative thick reinforced concrete slabs. This has an effect not only on material consumption and transport, but also in the supporting structure of a building. The basic material behaviour of TRC has already been well investigated, but some research is needed in regard to the behaviour of TRC at (very) high temperatures, as those typical in the case of fire. The aim of the project is to make the usage of textile reinforced concrete façade panels feasible in areas with high fire protection requirements.
It is known, that the bond between the textile reinforcement and the concrete deteriorates at higher temperatures. The main reason is the poor fire resistance of the coating applied on the yarns during textile production. This is mostly a styrene-butadiene coating. The disadvantage is that such a coating melts under the influence of heat. Therefore, our project partner from the Institute of Textile Machinery and High Performance Material Technology at the TU Dresden developed a heat resistant coating. Simultaneously, we optimised the concrete mixture at our research institute. With the help of milled polypropylene fibres, which are already used in tunnel constructions in a similar way, it was possible to create a heat resistant concrete. It works like this: The milled fibres melt at high temperatures. Thus, inside the concrete matrix there is more space for the water vapour, which develops because of the evaporation of the pore water. So, the increase in volume takes place without reaching critical stress concentrations in the concrete, which could lead to large-scale spallings.
For TRC elements, typical trials were done to characterise the new materials. In addition, we did e. g. uniaxial tensile tests with steady-state and non-steady temperature stress up to 600 °C to determine stress-strain relations for TRC under different temperatures. The bond between yarn and concrete was investigated using pull-out tests under temperature stress. The results will help to design a TRC façade. At the end of the project, large-scale slabs will be fire tested to validate the results.