Wind energy turbines
Table of contents
- G - 19 Analysis of fatigue induced strains using fiber-optic sensors
- G - 18 Fatigue resistance of shear-loaded dry concrete joints
- G - 17 Influence of dry concrete joints on the fatigue behavior of prestressed concrete beams
- G - 16 Segmented structures under torsional loading
- G - 15 State of the art of segmental construction (literature research)
- G - 14 Concept for experimental test on segmented concrete towers
- G - 12 Design of a resonance-based testing facility
- G - 11 Large-scale tests on segmented concrete towers
- G - 5 Analysis of prestressing wire breaks using acoustic emission measurements
- G - 1 Unevenness of joint surfaces of segmented towers
G - 19 Analysis of fatigue induced strains using fiber-optic sensors
Full title: Investigation of internal strain evolution in concrete under fatigue loading using fiber-optic sensors
Wind turbines play a central role in the expansion of renewable energies. According to the current design status, however, they have so far only been designed for a service life of 25 years. For safe use of the turbines beyond this, the design principles need to be adapted, which in turn requires a more precise understanding of the changes that occur in the material during the lifetime.
The tower structures of wind turbines are subjected to bending stresses due to wind and wave loads. This results in linearly varying strain gradients in the tower cross-section. This non-uniform loading leads to a material degradation of the cross-sectional areas subjected to higher stresses and consequently to a redistribution of stresses. This effect is being investigated in more detail at the Institute of Concrete Structures in tests on fatigue-loaded concrete beams. In order to obtain information about the internal strain development in addition to the surface measurement data of the test specimens, fiber optic sensors were embedded into the concrete beams.
As part of this study, the following tasks are to be carried out:
- Literature review on the fatigue behavior of concrete beams
- Literature review on strain measurement using fiber optic sensors
- Support in the setup and execution of the beam tests
- Evaluation of fiber optic measurement data from fatigue tests on concrete beams
- Investigation of internal strain development in concrete during fatigue loading
Contact person:
Clara Schramm
0351 463 41117
G - 18 Fatigue resistance of shear-loaded dry concrete joints
Segmental concrete construction has been an established method for several decades, primarily used in segmental bridge construction and in the tower structures of hybrid wind turbines. Prefabrication of the segments in precast concrete plants offers numerous advantages over in-situ concrete construction, including shorter construction times, improved component quality, and the feasibility of more complex formwork geometries. The joints that inevitably occur between individual segments are often either bonded or constructed as dry joints. In recent years, dry joints with ground, planar contact surfaces—i.e., without any shear interlocking—have gained increasing importance. This design approach enables simplified disassembly and reuse of the segments, thereby contributing to resource-efficient and sustainable construction practices.
In practice, the use of dry joints between concrete segments is already widespread; however, the load-bearing behavior of such joints under cyclic loading is neither fully understood nor reliably modeled. To address these issues, the Institute of Concrete Structures is conducting both static and cyclic friction tests on concrete shear specimens.
Within the scope of this work, the following subtasks are to be processed for this purpose:
- Literature review on the friction behavior of dry, smooth concrete joints under cyclic loading
- Support in the setup and execution of cyclic friction tests in the laboratory
- Evaluation of measurement data from fatigue tests on concrete shear specimens
- Investigation of friction behavior under cyclic loading (force transmission at the joint, temperature development, joint deformation)
Contact person:
Clara Schramm
0351 463 41117
G - 17 Influence of dry concrete joints on the fatigue behavior of prestressed concrete beams
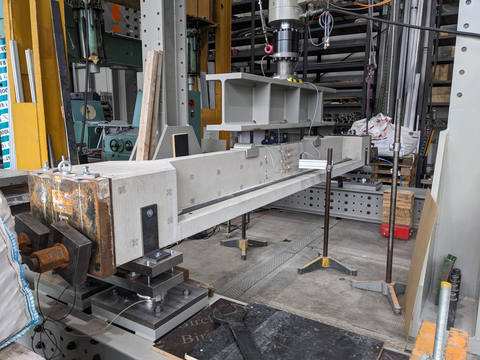
Large-scale fatigue test on a prestressed concrete beam
Wind turbines play a central role in the expansion of renewable energies. According to the current design status, however, they have so far only been designed for a service life of 25 years. For safe use of the turbines beyond this, the design principles need to be adapted, which in turn requires a more precise understanding of the changes that occur in the material during the lifetime.
The tower structures of wind turbines are subjected to bending stresses due to wind and wave loads. This results in linearly varying strain gradients in the tower cross-section.
This non-uniform loading leads to a material degradation of the cross-sectional areas subjected to higher stresses and consequently to a redistribution of stresses. This effect is being investigated in more detail at the Institute of Concrete Structures in tests on fatigue-loaded concrete beams. In this context, particular attention is given to the influence of dry joints, which are located between the precast concrete segments of real wind turbine towers, on the stress distribution within the cross-section
Within the scope of this work, the following subtasks are to be processed for this purpose:
- Literature research on the fatigue behavior of concrete beams
- Literature research on the fatigue behavior of dry concrete joints
- Support in construction and realisation of the beam tests
- Evaluation of measured data of fatigue tests on concrete beams with dry joints
- Investigation of the influence of dry concrete joints on the fatigue behavior of the concrete beams
Contact person:
Clara Schramm
0351 463 41117
G - 16 Segmented structures under torsional loading
Full title: Investigation of force transmission in the joint of segmented structures with dry and ground joints under torsional loading in bridge and civil engineering
Over the next 20 years, more than 50% of the existing bridges on the existing German autobahn network will have to be replaced. Furthermore, in order to achieve the expansion targets in the field of renewable energies, the construction of an increasing number of more powerful wind turbines is essential. In order to achieve these ambitious targets, the use of new, innovative design solutions is required in addition to proven construction methods. Prefabricated segmental structures, in which the supporting structures are divided into individual segments, represent a promising solution. These segments are manufactured in a precast concrete plant, assembled on the construction site and connected to each other in a form-fit and force-fit manner by external prestressing. The minimisation of production steps on the construction site enables extremely economical and fast construction processes, which is why this design method is now being used more and more worldwide. However, in Germany, this solution has not yet been able to gain full acceptance due to concerns about the durability of the structure as a consequence of the resulting joints. The growing ecological awareness of the construction industry and the further development of automation and digitalisation in precast concrete production are creating new possibilities for the further development of modular segmental construction.
The construction method is characterised by the joints which unavoidably occur. A further development in this area is the design of dry, ground segment joints without interlocking components. The load transmission in these joints takes place exclusively via friction. The shear resistance of the joints depends on the level of the external prestressing force in combination with the friction coefficient of the surface. When the cross-section is subjected to torsion, additional normal stresses arise in addition to the typical and well-known shear stresses according to St. Venant. These additional normal stresses interact with the normal stresses due to prestressing, thus directly influencing the load-bearing capacity of the dry joint, as actual research shows.
Especially the following points are to be solved:
- Literature review on segmental designs of reinforced and prestressed concrete structures
- Initial studies on the theory of warping torsion
- Parameter studies on selected typical cross-sections to determine the level of additional normal stresses
- Relating the calculation results to the joint resistance
- Discussion of calculation results
Contact person:
Max Götze, M.Sc.
0351 463 35606
G - 15 State of the art of segmental construction (literature research)
Full title: Literature research on the state of the art of segmental structures of reinforced concrete and prestressed concrete structures
* only Project Work *
Over the next 20 years, more than 50% of the existing bridges on the existing German autobahn network will have to be replaced. Furthermore, in order to achieve the expansion targets in the field of renewable energies, the construction of an increasing number of more powerful wind turbines is essential. In order to achieve these ambitious targets, the use of new, innovative design solutions is required in addition to proven construction methods. Prefabricated segmental structures, in which the supporting structures are divided into individual segments, represent a promising solution. These segments are manufactured in a precast concrete plant, assembled on the construction site and connected to each other in a form-fit and force-fit manner by external prestressing. The minimisation of production steps on the construction site enables extremely economical and fast construction processes, which is why this design method is now being used more and more worldwide. However, in Germany, this solution has not yet been able to gain full acceptance due to concerns about the durability of the structure as a consequence of the resulting joints.
The environmental awareness of the construction industry opens up new possibilities for modular segmental construction. This method makes it possible to achieve ambitious goals such as increasing resource efficiency, minimising greenhouse gases and promoting a circular economy. The circular reuse of whole structures or individual modular segments offers particular potential for the construction sector, which has not yet been fully utilised. In the future, it could therefore be possible to replace or dismantle parts of a structure and reuse them elsewhere. The further development of the construction industry, in particular the automation and digitalisation of precast concrete production and the use of high-strength and high-performance concretes, also favours the use of modular structures.
Especially the following points are to be solved:
- Literature review on segmental designs of reinforced and prestressed concrete structures
- Literature review on topics such as joint design, prestressing and local effects
- Classification of segmental structures according to selected criteria (such as cross-sections, joints, construction sequence, circularity, etc.)
- Presentation of the load-bearing behavior of such designs
- Research on the circularity of segmental structures
- Summary of the state of research in this field
Contact person:
Max Götze, M.Sc.
0351 463 35606
G - 14 Concept for experimental test on segmented concrete towers
Full title: Development of a test and measurement concept for experimental large-scale tower tests on multi-dived concrete segments of wind turbines
Wind turbines play a central role in the expansion of renewable energies. In order to achieve the ambitious expansion targets in the field of renewable energies, ever more powerful wind turbines need to be erected. The result is towers of increasing height with larger rotor diameters. At the same time, reducing the costs of manufacturing and operating the turbines is of crucial importance. These approaches have led to the development of hybrid towers as a powerful and economical option.
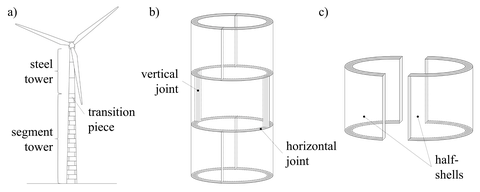
a) hybrid tower of a wind turbine, b) divided concrete segments, c) half shell segments
These towers consist of steel sections at the top and precast concrete segments at the bottom. The circular concrete segments are dry stacked and clamped together with external tendons. The shear stress in the joint is transferred exclusively by friction. Additional vertical joints divide the circular ring segments into smaller components. The resulting half, third or quarter shells significantly reduce transport costs and assembly time compared to other designs. At the same time, this leads to a more complex load-bearing behavior. In addition to the typical normal and shear stresses, the splitting of the cross-section results in additional secondary stress components. The interaction of these stresses directly affects the load-bearing capacity of horizontal dry joints, the behavior of which has not been fully understood or reliably modelled. For this reason, the Institute of Concrete Structures is carrying out extensive numerical analyses and tests on large-scale model towers.
Especially the following points are to be solved:
- Literature research on tower constructions of wind turbines and external prestressing
- Literature research on existing calculation models for the load-bearing capacity of dry concrete joints
- Initial investigation of the theory of warping torsion
- Numerical preliminary investigations (no previous knowledge of numerical simulations required)
- Development of a suitable test and measurement concept
Contact person:
Max Götze, M.Sc.
Phone: 0351 463 35606
E-Mail:
G - 12 Design of a resonance-based testing facility
Full title: Design of a resonance-based testing facility as a frame system
In order to further advance future research on tower constructions of wind turbines, knowledge about the fatigue behavior is of great importance. The cyclic loads from wind and wave loading lead to high numbers of load cycles throughout their life time. In order to reproduce the fatigue stress of wind turbines well experimentally, large-scale cyclic tests on structural elements are necessary.
For this, high numbers of load cycles and high input forces must be realised. The resonance-based testing method is an efficient way to apply the required cyclic load. Two contrarotating imbalanced motors are used to generate the input force. The excitation frequency of the motors is set close to the natural frequency of the system. This leads to resonance and consequently to a dynamic magnification of the forces. In order to preserve the existing energy in the system as much as possible without adding more and more energy, damping and friction mechanisms must be reduced. To minimise the energy dissipation, a closed frame as a mechanical system could be a solution for a resonance-based testing facility.
Within the scope of the work, a design for a oscillating frame system as a resonance-based testing facility is to be developed. First of all, the resonance-based testing method and oscillating frame systems are studied. Then two or three pre-designs are worked out. Then, one design should be selected, which is designed in more detail under specified boundary conditions. For this purpose, a simple numerical model is created to analyse the vibration behavior and to design the components.
Depending on interest and level of knowledge, the task is formulated jointly.
Contact person:
Dipl.-Ing. Clara Schramm
0351 463 41117
G - 11 Large-scale tests on segmented concrete towers
Full title: Large-scale tower tests on the load-bearing behavior of segmented concrete towers of wind turbines
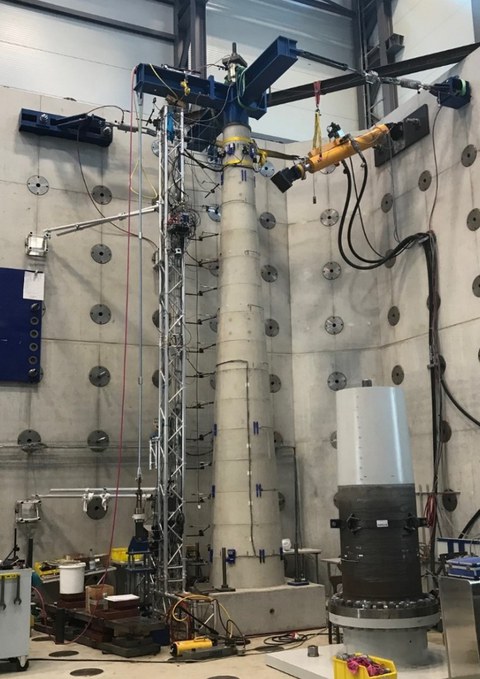
Large-scale test on the load-bearing behavior of a segmented concrete tower of wind turbines
Wind turbines already account for the largest share of electricity generation from renewable energies in Germany. To further increase the performance of wind turbines, the trend is towards ever taller towers and larger rotor diameters. Especially for large hub heights, so-called hybrid towers have become successfully established. The upper part of such towers is composed of several steel sections, whereas the lower part consists of prestressed precast concrete rings. The individual concrete segments are usually not glued or mortared together, but stacked dry on top of each other and connected by external tendons.
Far more than half of all newly installed wind turbines are manufactured using this construction method. In this way, it is possible to erect turbines with total heights of 240 m and more. Despite the great practical relevance, the complex load-bearing behavior of such concrete towers with dry joints is neither fully understood nor can it be reliably modelled. Therefore, large-scale experiments with model towers on a scale of approximately 1:10 are being carried out at the Institute of Concrete Structures. The aim of the tests is to record the real load-bearing behavior of such towers and to develop calculation models based on this. Within the scope of the thesis, a detailed examination of such tower structures and of the tower tests is to be carried out. In particular, the following points are to be dealt with:
- Literature research on tower structures of wind turbines and their load-bearing behavior
- Documentation and support in the execution of the tower tests
- Evaluation of selected test results
- Comparison of the test results with existing calculation models
Contact person:
Dipl.-Ing. Florian Fürll
0351 463 32317
G - 5 Analysis of prestressing wire breaks using acoustic emission measurements
Acoustic emission analysis (SEA) is a non-destructive testing method that can draw conclusions about a change in the condition of the structure based on the analysis of the acoustic waves emitted by the structure. An application of SEA can be found in structural monitoring, detection and localization of prestressing wire breaks, and materials research, among others. At the IMB of the TUD, research is being conducted to detect and localize possible wire breaks of tendons in wind turbines using SEA.
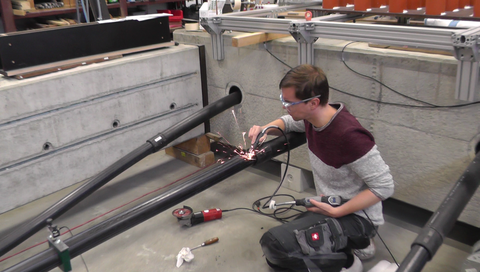
Cutting of a tendon
In order to form real boundary conditions of wind turbines even in laboratory tests, a prestressing frame with dimensions of 12 m × 4 m was set up, where a total of four tendons were prestressed, each with a length of about 10 m. The tendons were separated by Dremel. The installed tendons were artificially cut with the help of Dremel. The acoustic signals generated as a result were measured by the acoustic emission sensors, which were placed in a distributed manner in the tensioning frame. The attached picture shows, for example, the cutting process of a tendon in the tensioning frame and the measurement technique used.
The measured signals show different characteristics of the propagation path from the fracture location of the tendon to the measurement sensor and are to be analyzed with respect to the propagation conditions. In the analysis of the signals, a distinction is made between qualitative and quantitative evaluation. In the former, some acoustic emission features such as peak amplitude, signal energy are extracted and statistically evaluated. In the latter, the whole transient waveforms of the signals are considered and evaluated in both time and frequency domains.
Depending on the student's interests and the type of student work, the scope of work can be customized. For a diploma thesis, knowledge of programming in Python or Matlab is required. A detailed assignment will be worked out accordingly.
Contact person:
Dipl.-Ing. Ronghua Xu
0351 463 33776
G - 1 Unevenness of joint surfaces of segmented towers
Full title: Effects of unevenness on joint surfaces of segmented tower structures for wind turbines
In order to achieve the expansion targets in the field of renewable energies, the further cost reduction of wind power generation in manufacturing and operation is inevitable. More powerful turbine classes and the development of new locations in low-wind regions or forest areas require the construction of higher tower constructions. In recent years, so-called hybrid towers have become established, especially for large hub heights. The upper part of such towers is composed of several steel sections, whereas the lower part consists of prestressed precast concrete rings. The individual precast concrete rings are connected by external tendons that run inside the tower and are anchored in the foundation and in the intermediate adapter. Transmission of shear forces between the individual segments is provided by frictional resistance in the horizontal joints. Current design models assume ideally flat flange surfaces at the top and bottom of the segments and thus assume a constant normal stress distribution at the compression connection.
Experimental investigations show, however, that a highly non-uniform normal stress distribution occurs in the joints as a result of a pure prestressing load. The reason for this lies in imperfections occurring on the joint surfaces. Investigations into the accuracy of the joint surfaces on real segments for wind turbines make it clear that the surfaces are not ideally flat despite grinding processes, but exhibit unevenness. Numerical simulations show that especially the occurring waviness on the joint surfaces can significantly influence the joint bearing behavior and the joint bearing capacity.
Within the scope of the work, the effects of the waviness occurring on the joint surfaces on the joint bearing behavior are to be investigated by means of analytical and numerical calculations. For this purpose, parameter studies are to be carried out, among other things, in order to find out the most unfavorable manifestations of the waviness with respect to the joint bearing capacity.
Contact person:
Dipl.-Ing. Florian Fürll
0351 463 32317