OBSERVATOR – Development of a digital twin for low-sensor, high-load aircraft components
Project information
- Employer: Federal Ministry for Economic Affairs and Energy (BMWi)
- Program: National aeronautics research program LuFo VI‑1
- Program line: (D) Industry 4.0 / Artificial intelligence
- Subject area: (2) High-performance, safe and economical systems
- Funding objective: (3) High-performance and efficient aviation
- Partners: Lufthansa Technik AG (coordinator), Deutsches Zentrum für Luft- und Raumfahrt e. V., Technische Universität Hamburg, Liebherr‑Aerospace Lindenberg GmbH
- Period: 39 months, starting from December 2020
Objectives
The overall objective of the project is the modeling and evaluation of loads as well as the health status of low-sensor components of aircraft. For this purpose, the application of new technologies, in this project the digital twin, is used. The virtual sensor to be developed is fed on the one hand by aircraft data (e.g. ADS-B, FDR) and on the other hand by acquired data from environmental influences of the aircraft (e.g. weather information, condition of movement areas, etc.). Based on this combined data and the information generated from it, the aim of predictive maintenance is to optimize maintenance processes and save resources in the long term.
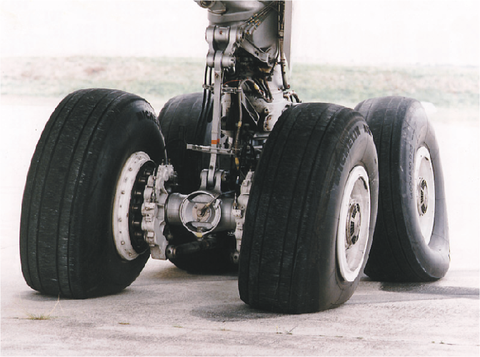
Tire deformation due to loads during a turning maneuver
The main objective of the chair is to provide a database consisting of real data and generically generated data related to ground processes (e.g. landing, taxiing, ground handling) and to model the loads acting on aircraft components as a function of specific operating/load scenarios. The generated virtual measurement data (so-called observers) are used for the subsequent evaluation of the current and predicted conditions of aircraft components (so-called diagnostic and prognostic agents) and are mapped within a digital twin.
Research focus and methodology
The focus is on modeling and evaluation of the loads associated with aircraft ground operations using a data-driven approach. For this purpose, the analysis of historical vehicle utilization profiles, of fleet schedules as well as analytical correlations between operational process and load/stress is performed for integration into a database. Data accumulation is dual, incorporating real data on the one hand and generically generated data on the other. This is to achieve a low-delay exploration of all following methods. By means of a comprehensive inventory, the available real data are collected, deficits are identified and described and interfaces to the database are implemented. The data for load measurement include both environmental parameters (esp. weather data according to METAR, TAF etc.) and the roll trajectory of the aircraft depending on specific operating conditions (e.g. based on ADS-B). Unavailable real data are simulatively generated as generic data, e.g. by means of a roll trajectory predictor, generating technically possible ground operations based on the airport's infrastructure and operating procedures as well as aircraft states/properties. Artificial intelligence (AI) and machine learning techniques are also used (e.g. decision trees such as Random Forest, C4.5 algorithm and pattern recognition such as regression, Bayesian Networks, Hidden Markov Model).
Furthermore, the load cases are modeled using the database, kinematic approaches and maneuverability of the aircraft. The operating scenarios to be modeled and the associated load cases take into account typical normal (landing, taxiing, turning, braking, pushback, etc.), abnormal (engine failure, taxiing with insufficient tire pressure, faulty nose gear steering, etc.) aircraft procedures and certification requirements (e.g. one-gear and rebound landing conditions according to EASA CS-25).
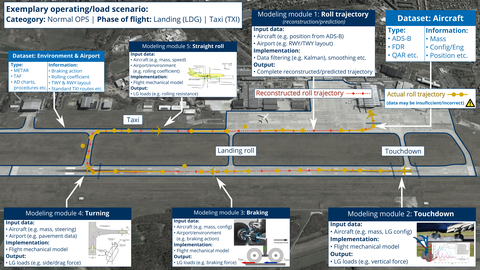
Exemplary operation/load scenario: modeling of landing gear loads for specific aircraft maneuvers during landing (e.g. touchdown, braking) and taxiing (e.g. turning) as well as generic roll trajectories in the context of normal operations
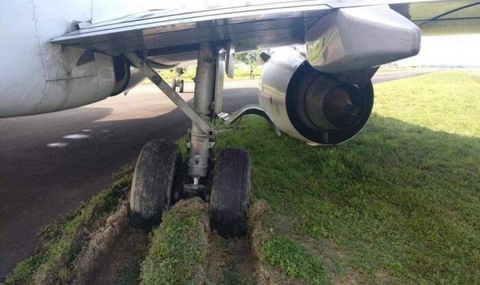
Increased loads due to rolling on soft soil in the course of a RWY excursion
Also, incidents/accidents resulting from unforeseen events on board and/or on the ground or in the immediate vicinity of the aircraft and which do not occur in accordance with the SOPs according to FCOM/FCTM are the subject of the investigations. An example of this is the rolling through unpaved ground when leaving the runway (so-called RWY Excursion): The sinkage, rolling resistance forces and dynamic effects resulting from the so-called tire-ground interaction, especially in the case of low bearing strength, can cause extreme load peaks and thus considerable stresses on aircraft components. Such conditions can also be described in terms of probability theory (accident rate and accident location).
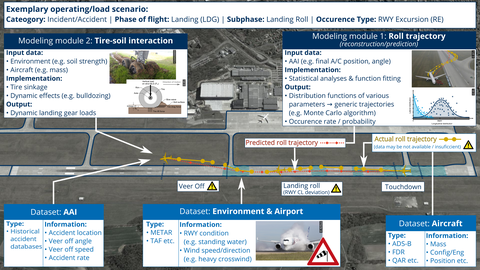
Exemplary operating/load scenario: modeling of landing gear loads (tire-soil interaction) as well as generic rolling trajectories in the context of RWY excursions
With this information, the chair supports the diagnostic capability of the digital twin and contributes the stress histories of a specific aircraft component for evaluation and prognosis of the state of health including resulting maintenance requirements. The applied methods are then validated by comparing prediction and occurred ground/maintenance events. Finally, the certification requirements for aircraft components (esp. according to EASA CS-25) are reviewed and proposals for a load-specific procedure based on real loads are developed in coordination with European Union Aviation Safety Agency (EASA, see agency's web content on the project).
In summary, the focus is on the following main work packages:
- Network-wide provision of aircraft movement data (e.g. taxiing, pushback, towing) and environmental data (e.g. weather, surface condition of movement areas) from a variety of data sources;
- Accurate modeling of historical roll trajectories against a background of sometimes erroneous and incomplete data (e.g., ADS-B);
- Calculation of loads acting on the aircraft and the specific aircraft components during ground operations;
- Derivation of effective load cases for standardized ground processes with regard to Normal and Abnormal/Emergency Procedures (SOPs according to FCOM/FCTM) as well as exceptional conditions in the form of incidents/accidents (e.g. RWY excursions);
- Evaluation of these loads in terms of component wear;
- Development of a reliable predictor for roll trajectories and aircraft component loads along the aircraft’s scheduled cycle to evaluate the health of this component in the agreed forecast time frame and
- Discussion of certification specifications with the joint partner Liebherr‑Aerospace Lindenberg GmbH and the EASA (see web content on the project) based on actual loads and safety assessments.
Publications
- Fricke, H., Schlosser M., Garcia, M. A. and Kaliske, M. (2019): Embedding aircraft system modeling to ATM safety assessment techniques: The runway excursion safety case for runway strips with reduced strength. Transportation Research Interdisciplinary Perspectives, Vol. 3, TRIP-100026. DOI: 10.1016/j.trip.2019.100026