Aug 08, 2022
On the way to the new generation of 3D-printed, structural supercaps
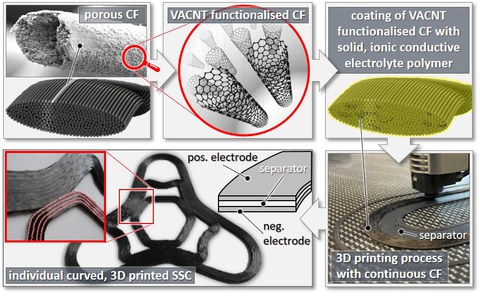
Technology concept for the 3D continuous fiber-printed, free-form, structure-supporting PRINTCAP supercaps
KICK-OFF OF THE EU RESEARCH PROJECT PRINTCAP
On July 11th, 2022, the four cooperation partners - including the Research Center Carbon Fibers Saxony (RCCF) of TU Dresden - met in Paris under the chairmanship of Thales Research and Technology for the kick-off of the research project "Next Generation of 3D Printed Structural Supercapacitors" (PRINTCAP). The project addresses the development of a new generation of supercapacitors (SC) for fast-charging, structural energy storages for the automotive and aerospace industries. The partners jointly discussed possible manufacturing routes and initial concept ideas. They also successfully defined the first process steps.
Against the backdrop of current global challenges such as climate change or the scarcity of natural resources on the one hand, and in view of high individual mobility needs on the other, innovative key technologies needs to be pushed for a sustainable future. Electrically powered vehicles, free of local CO2 emissions, form the backbone of the EU's 2030 climate framework. However, the energy storage systems used, especially batteries, increase vehicle weight to a considerable extent. They also limit the freedom in the vehicle design. Existing energy storage solutions made of layers and stacking methods need shielding housings. Therefore their integration often takes up valuable installation space. Innovative structural supercapacitors (SSC) combine the energy storage function of SC with the high mechanical properties of lightweight composites. Thus, they can achieve a drastic reduction in the weight and space requirements of energy storage systems. The SSC concept opens up a wide field of concrete applications such as fast-charging electric cars or parcel drones that store energy in their own chassis. Particularly in the case of electric-based transport drones, the small dimensions need close attention for an optimal weight distribution in order to maintain flight characteristics. To achieve this, it is necessary to be able to process the SSC as freely as possible during chassis production. In addition, SSC integrated into the chassis must be able to withstand considerable loads and vibrations. Commercially available SC are not sufficient for this task. Hence, the development of a new generation of materials and systems for such applications is of fundamental importance.
This is where the PRINTCAP project comes in and pursues the production of SSC by additive manufacturing processes. 3D printing methods enable their near-net-shape arrangement in the component in the future. The PRINTCAP concept of near-net-shape SSC combines weight- and space-optimized lightweight structures with the energy storage function. For direct transfer to industry, PRINTCAP aims to develop effective design and manufacturing concepts for structure-bearing, free-formed SSC, ranging from the concept phase to demonstration proof. Finally, the concepts to be developed should also include initial solutions for recycling the materials used as well as life cycle analysis studies, in accordance with the cradle-to-cradle principle. For this purpose, PRINTCAP draws on the expertise of the Research Center Carbon Fibers Saxony (RCCF) at the TU Dresden, among others. In addition, the Leipzig University of Applied Sciences (HTWK Leipzig) is contributing its specialist knowledge in the composite design of multifunctional materials. Thales Research and Technology and NAWATechnologies complement the team competencies with their unique technological positions in the field of structural load-bearing electrolytes and the production of carbon nanotube based supercaps. With the synergetic combination of energy storage and lightweight construction, the PRINTCAP project lays the foundation for the free-form production of fast-charging, structure-supporting, resource-efficient energy storage devices.
Project PRINTCAP: „Next generation of 3D printed structural supercapacitors“
Funding
Period
01.06.2022 – 31.05.2025
Project partners
Consortium leadership: Thales Research and Technology (TRT)
Chair Lightweight engineering with composites at the Leipzig University of Applied Sciences (HTWK Leipzig)
NAWATechnologies
Research Center Carbon Fibers Saxony (RCCF) at the TU Dresden, a joint research initiative of the Institute of Lightweight Engineering and Polymer Technology (ILK) and the Institute of Textile Machinery and High Performance Material Technology (ITM)
Subproject of the TU Dresden: Development of energy-storing carbon fibers and continuous-fiber tapes for 3D print of PRINTCAP structural supercapacitors
Project management at the TU Dresden
Prof. Dr.-Ing. Niels Modler (Chair of Function-integrative Lightweight Engineering)
Contact at RCCF
Dipl.-Ing. Daniel Sebastian Wolz, Expert Group "Novel Materials and Special Processes" at the ILK, Head of Unit carbon fibers at RCCF, +49 (0)351 463-44046,
Dr.-Ing. Thomas Behnisch, Head of Expert Group "Novel Materials and Special Processes" at the ILK, Scientific direction at RCCF, +49 (0)351 463-42503,
Boilerplate
The Research Center Carbon Fibers Saxony (RCCF) at TU Dresden is a joint research initiative of the Institute of Lightweight Engineering and Polymer Technology (ILK) and the Institute of Textile Machinery and High Performance Material Technology (ITM) in the field of tailored carbon fibres for pioneering multi-functional structural materials. The centre is staffed by scientists research continuous development chains from fiber raw material to finished component. The RCCF partners investigate fossil and renewable raw materials as basic products and develop tailored carbon fibres for novel multi-functional materials. The findings will be transferred directly into teaching at the TU Dresden. Beyond that, the knowledge transfer to industrial applications is focused.
www.tu-dresden.de/mw/rccf