Multibody-system simulation (MBS)
Full title: |
Multibody-system simulation (MBS) |
Abstract: | The MBS covers the numerical simulation of the dynamic behavior of real systems. |
Objectives: |
The model development process in the multi-body system simulation subdivide the system to be analysed into a finite number of bodies. The movement between the bodies is described by means of joints, force-elements and constraints. Depending on the research objective, the bodies can be modelled both rigidly and by modal-reduced substitute systems. This methodology allows the investigation of the dynamics of arbitrary, complex systems, whereby the fields of application can extend over the investigation of the accuracy of clocks, the driving behavior of vehicles or the dynamics of turbomachines. In multi-body system simulation, the focus of our analyses is, among other things, on determining the time-variant loads that are characteristic of a system. These are often not known in the design of machines and systems, but are absolutely necessary for resource-saving dimensioning, e.g. of drive systems. Another core competence is the optimization of system behavior. This means both the identification of critical operating states and the development and simulative testing of damage prevention measures which can be used to extend the service life of existing machines significantly. In order to maintain the closeness to reality when creating the multi-body simulation model, the calculation models are always analyzed with regard to the selected boundary conditions and the system boundary. Our experience shows that the system boundary has to be extended beyond mechanics in certain applications. This means in particular the realistic provision of the drive and output loads of drive systems. Interdisciplinary expert knowledge is required to describe these loads, since, for example, specialist areas from electronics and control engineering (converter-fed asynchronous machine), fluid mechanics (wind field, flow field) or terra mechanics (digging force model, driving on soft soils) have to be served. For these as well as other problems, mathematical models were developed at the Chair of Machine Elements. The functionality of the models was confirmed by measurements on real systems. |
Contacts: |
Dr.-Ing. Thomas Rosenlöcher |
Current projects: | |
Completed projects: |
|
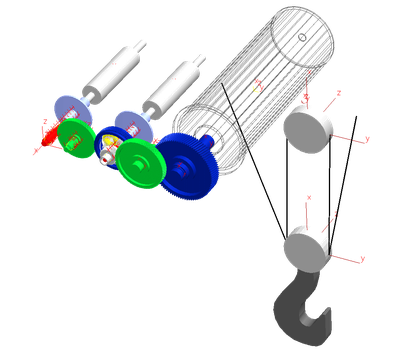
© IMM
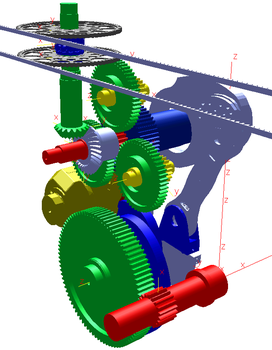
© IMM
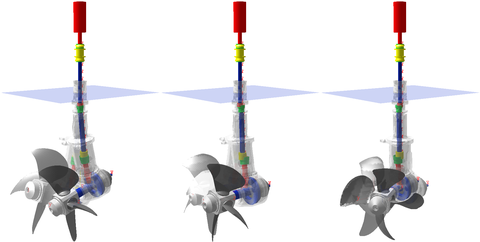
© IMM
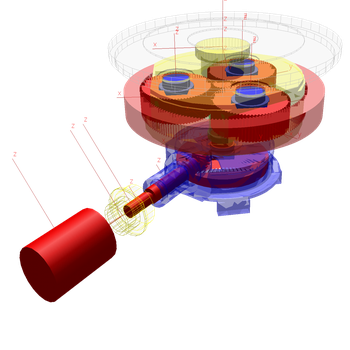
© IMM
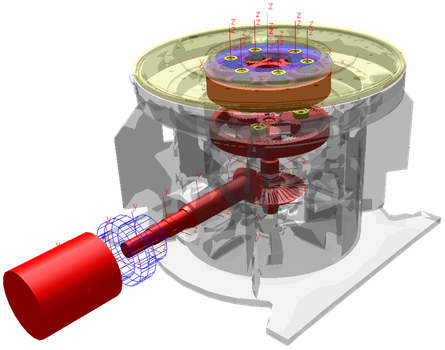
© IMM
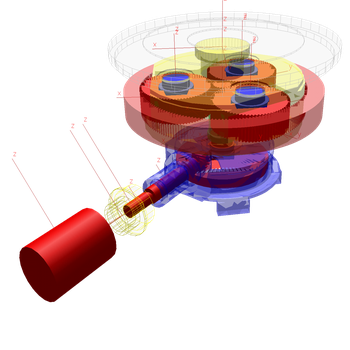
© IMM
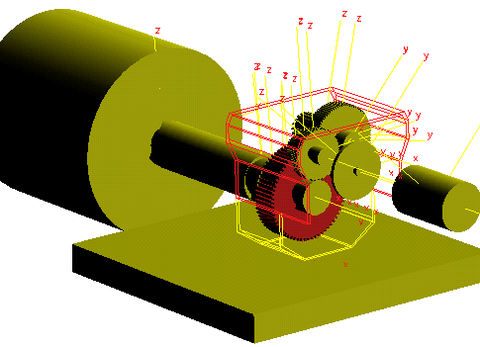
© IMM
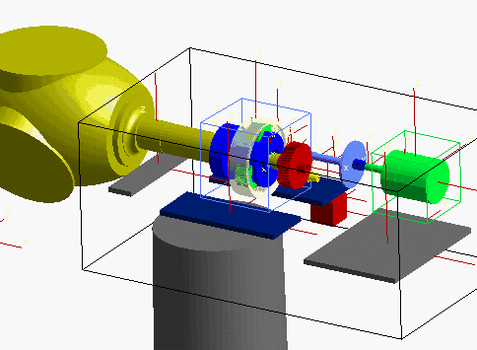
© IMM
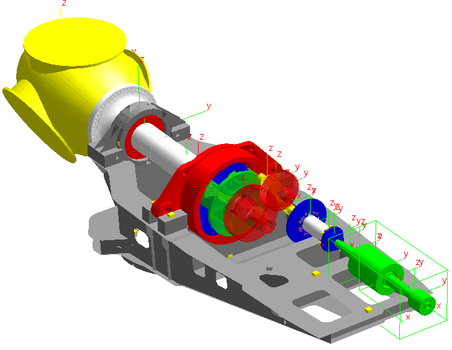
© IMM
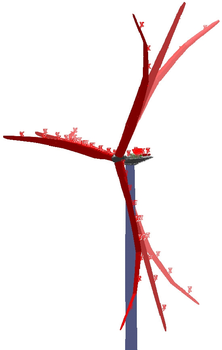
© IMM
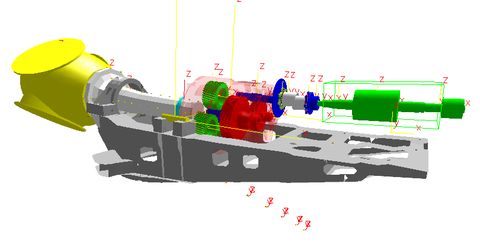
© IMM
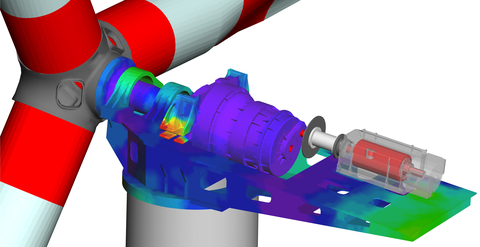
© IMM
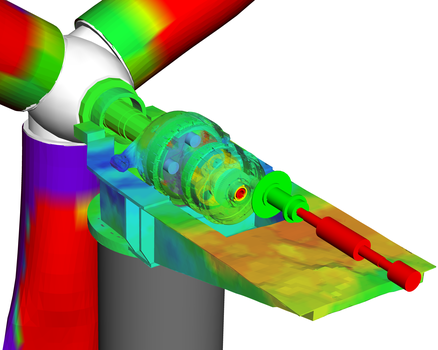
© IMM
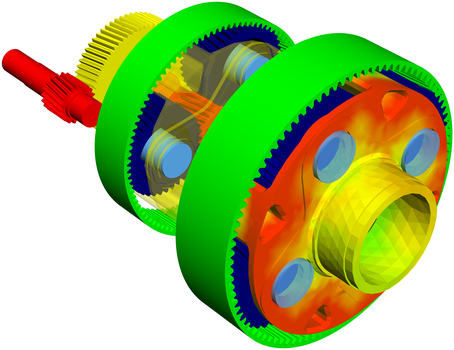
© IMM
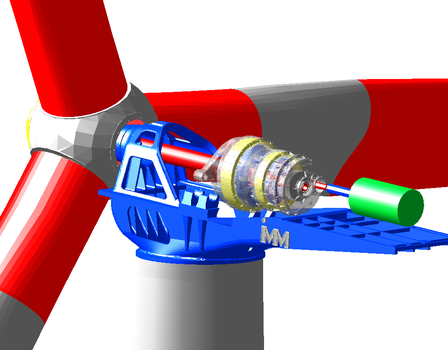
© IMM
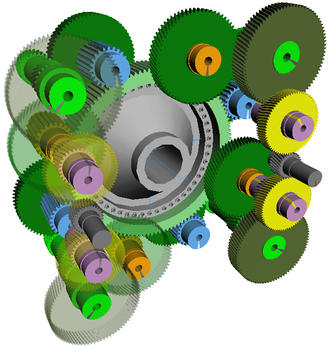
© IMM
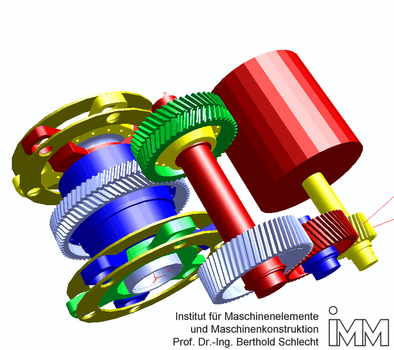
© IMM