Ceramic composites
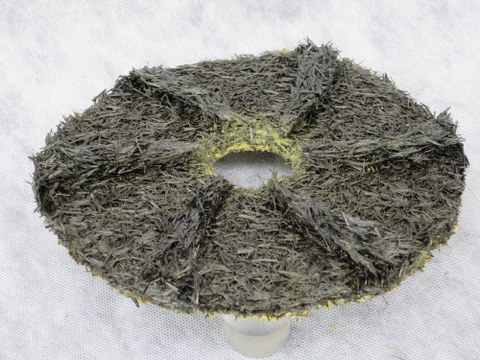
Oriented short-fiber-preform for requirement-adapted C/SiC ceramic
In comparison to metal materials, ceramics offer lower densities, greater hardness, and superior wear and temperature resistances. Correspondingly, ceramic materials are being used in a variety of applications in almost all industries, and are constantly being developed further. The main limitations of monolithic ceramics are in their high brittleness and low ultimate strain, which can lead to internal tension and ultimately material failure, when combined with heat expansion at uneven component heating. These disadvantages can be overcome by a sufficient fiber reinforcement, achieving significantly improved crack resistance, increased ultimate strain, fracture toughness, and thermal shock resistance. These are the reasons for an increasing use of fiber-reinforced ceramic materials. The linings of rocket engines and their burners are made from fiber-reinforced ceramics. Furthermore, ceramic composites are used in thermal power plants, turbines, compressors and brake discs for cars.
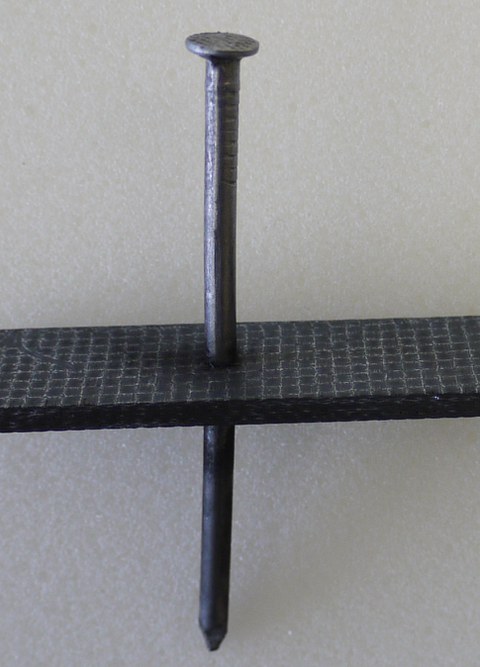
Fiber-reinforced composites ceramic
Ceramic and carbon fibers are perfectly suited reinforcement materials due to their high temperature resistance. For a number of newer, thermomechanically loaded components from energy engineering, vehicular engineering, and aeronautics, the use of fiber-reinforced ceramic materials is sensible, as they can help provide long durability and improved mechanical properties. Most the required components have complex shapes. Therefore, near-net shape 3D fiber scaffolds (preforms) based on innovative, resource-conserving production methods are developed, realized, and tested at the ITM.
To ensure high tear resistance, the fiber/matrix interface design has to be adjusted specifically. A defined fiber/matrix bond is needed and usually realized by fiber coatings and other thermal or chemical pre-treatments to ensure a defined force insertion into the reinforcement fiber. This allows a force transfer, and the tear energy can be dissipated efficiently.
In the context of interdisciplinary research projects, the ITM supports research and development with strong industry involvement, aiming for:
- new processes for a cost-efficient and wasteless production of component-adapted 3D preforms for fiber-reinforced ceramics based on generative-additive production methods,
- load-adapted 3D net shape preforms from fibers or fiber bundles with adjustable fiber volume count, porosity and an additional reinforcement based on continuous filaments for heavy mechanical duty components with complex, near-net shape geometry and varying wall thicknesses, and
- suitable fiber coating for fiber/matrix interfaces allowing a maximized, application-related damage tolerance of the fiber-reinforced composite ceramics.
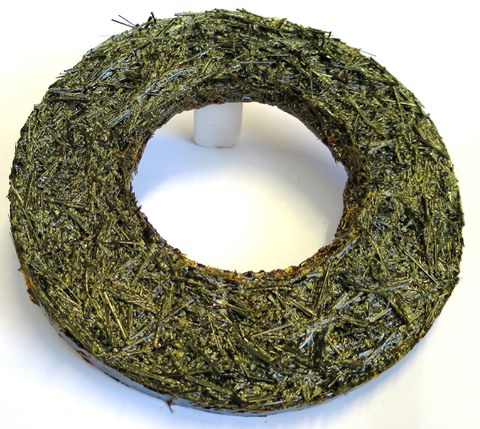
Oriented short-fiber-preform for requirement-adapted
Contact person:
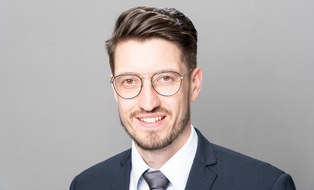
Mr Dr.-Ing. Dominik Nuss
Research Group Leader Surface Formation Technology
Send encrypted email via the SecureMail portal (for TUD external users only).
Visitor Address:
George-Bähr-Straße 3c, Zeuner-Bau, Room 115
01069 Dresden
Deutschland