Metal composites
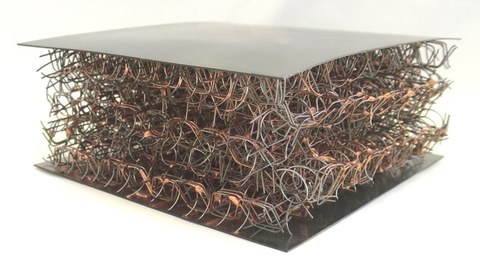
Metal sandwich composite
Metal composites for lightweight design applications are components in multi-material setups from metal sheets and continuous-fiber-reinforced plastic composites (FRPC), sandwich structures consisting of textile-based metallic reinforcement structures and metal sheets, and textile-based structures, either hybrid-designed or infiltrated with metallic matrix. These innovative metal composites in multi-material design promise extraordinary performance potential by reducing weight and adding functional integration.
Sheet metal-FRPC composites
The innovative approach to the production of metal sheet composites consists in the use of textile semi-finished products on a hybrid yarn basis, which is shaped in a joint forming/joining process with the metal sheet, while the joining is performed simultaneously by or during the composite formation. Initially, plane fabrics are created from the hybrid yarns. Here, biaxially and multiaxially reinforced textile structures with adjustable, good draping behavior at stretched reinforcement thread arrangement are at the center of attention. This allows a creaseless, process-integrated forming of plane structures into complex 3D geometries and achieves excellent mechanical properties in the composite. To ensure optimum adhesion between FRPC and metal sheet in the composite, relevant measures for surface treatments are being developed and applied for the textile and the metal sheet.
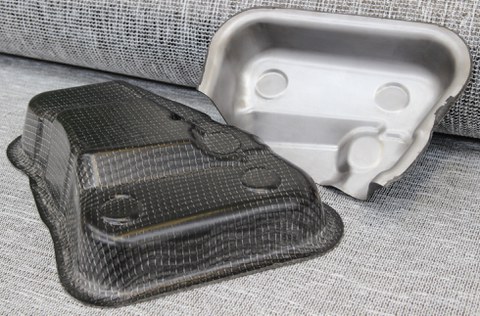
Metal sheet composite technology demonstrator unit B column base
Metal-metal composites
Metal-metal composites can be categorized into metal sandwich composites and metal matrix composites. At the ITM, innovative, textile-based, metallic, cellular 3D structures and the required production technologies and machines are in development. For this, metal wires or rovings are woven or knitted into three-dimensional, cellular structures. Additionally, textile thread materials can be processed to created hybrid structures. The developed structures can be used as cores in metal sandwich components or as reinforcement in a metallic matrix.
Thanks to extensive research regarding the development and realization of metal composites, the ITM can use its know-how for specific, requirement-adapted processing of various materials, the development of suitable production and machine technologies, and the targeted adjustments of material and component properties.
Contact person:
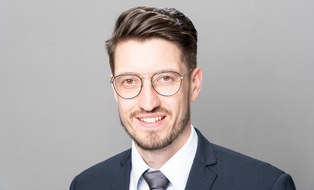
Mr Dr.-Ing. Dominik Nuss
Research Group Leader Surface Formation Technology
Send encrypted email via the SecureMail portal (for TUD external users only).
Visitor Address:
George-Bähr-Straße 3c, Zeuner-Bau, Room 115
01069 Dresden
Deutschland