Preforming Ready-made Technology
The simulation of complex production processes is an important part of modern manufacturing and aims to assist in lowering costs and securely designing any new processes. To produce textile reinforcement structures for complex FRPC components effectively, load-adapted and suitable to further processing, it is necessary to create a digital link between the form-finding process (3D geometry), the load-adapted design, and the textile-technical realization via a 2D contour. The research projects of the ITM for sequential preforming are therefore focused on the following:
- 3D cutting pattern development, simulation and visualization,
- quality control, and
- process parallelization, development of production technologies and tools.
3D cutting pattern development, simulation and visualization
A 3D geometry model (3D CAD or optical scans of physical models) are the foundation for virtual product development. Considering the deformation behavior (especially the shear behavior) of the materials to be processed, the structure-mechanical requirements and the requirements of the draping process (crease-free), the minimum possible number of reinforcement cuttings within the layer setup is determined in simulation and virtually depicted. The aim is to achieve a near-net shape portrayal of the component surface via the preform, to minimize waste and additional labor.
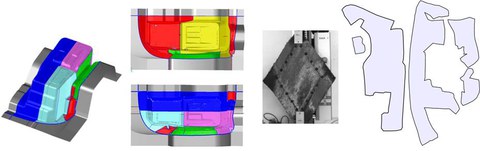
Cutting pattern generation “near-net shape” based on virtual data
Quality control
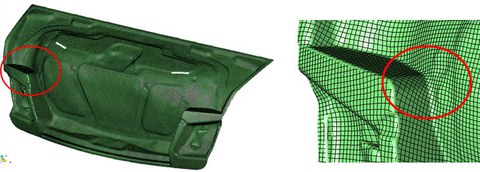
Virtual representation of the reinforcement threads for an early detection of flaws
Furthermore, simulation and visualization of the reinforcement textile on the 3D component allow an early detection of problems and flaws. Cutting pattern and draping strategy can be adjusted accordingly.
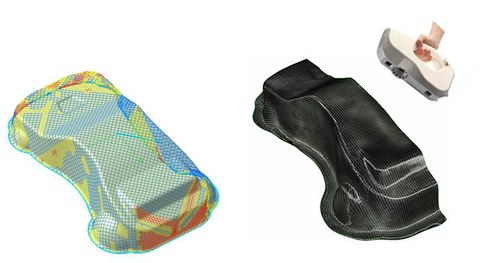
Validation of simulation results for improved material modeling
The results of experimental examinations can be transferred into digital data and used for quality control and comparisons to simulation results. Simulation results can also be useful to develop production technologies (draping strategies) for improvements to the shaping process, and to generate the required draping tools.
Process parallelization, development of production technologies and tools
For a reproducible handling of the cuttings within the preform, they fixed all-over with a binding agent. This limits drapeability. A local application of binding agent to the parts of the cutting that will experience little distortions during the shaping of the component geometry, this can be avoided. The local application of binding agent is determined individually for components and based on simulations, before being realized by suitable application methods and activation possibilities. An important focus of the R&D efforts consists of a technical and technological extension of CNC cutting technology for high-performance textiles by a CNC-positionable operative unit for an optimized application of thermoset and thermoplastic binding agents.
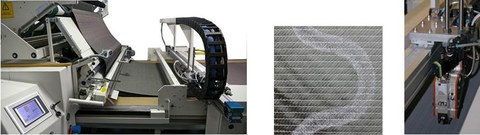
Technology development for a component-adapted structural fixation of textile reinforcement semi-finished products within the process chain for sequential preforming