Alternative Konstruktionsformen für Carbonbeton
Inhaltsverzeichnis
Leichte Decke aus CRC
Titel | Title Entwicklung leichter Deckenelemente aus Carbonbeton | Development of lightweight ceiling elements made of carbon concrete composite Förderer | Funding Institut für Massivbau, TU Dresden Zeitraum | Period 09.2016 – 04.2018 Leiter | Project manager Dr.-Ing. Harald Michler Bearbeiter | Contributor Dipl.-Ing. Sebastian May |
Bericht aus dem Jahrbuch 2018
BAUEN LEICHT GEMACHT
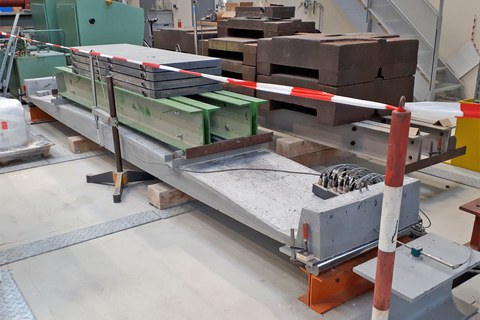
Dauerversuch an einem Deckenelement
Im Rahmen dieses Institutsprojektes entwickelten, erforschten und prüften wir ein materialeffizientes Deckenbauteil aus Carbonbeton für den herkömmlichen Hochbau als Fertigteil. Durch eine Reduzierung der benötigten Betondeckung auf ein Minimum – für Carbonbewehrung nur notwendig zur Sicherstellung der Verbundkraftübertragung – können Bauteile aus Carbonbeton gegenüber dem konventionellen Stahlbetonbau, wo eine viel größere Betondeckung zum Schutz der Bewehrung vor Korrosion gebraucht wird, mit geringeren Bauteildicken hergestellt werden.
Bekannte Stahlbetondeckenhöhen können über den Grenzwert der Biegeschlankheit abgeschätzt werden. Dabei darf das Verhältnis von Spannweite zur statischen Nutzhöhe im Allgemeinen maximal 35 sein, beziehungsweise 25 im Fall von Flachdecken des konventionellen Hochbaus. Bei einer Vollplatte mit einer Spannweite von 4,5 m ergibt sich somit eine Nutzhöhe von 18 cm. Zur Bestimmung der Konstruktionshöhe muss noch eine Betondeckung von rund 3 cm berücksichtigt werden. Die Deckenplatte besitzt letztendlich eine Höhe von 21 cm und erfüllt damit die oben beschriebenen Grenzwerte.
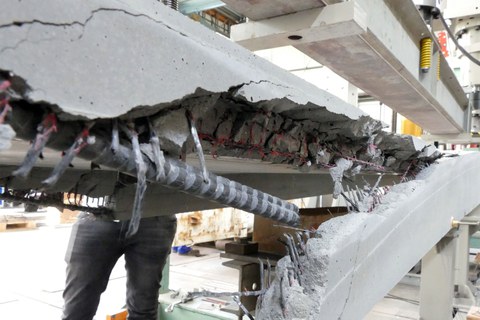
Versagen des Deckenelementes und der Carbonstäbe
Das Carbonbeton-Deckenelement wurde in Summe viermal mit teils geringfügigen Modifikationen am Bewehrungskorb sowie Optimierungen beim Herstellprozess gefertigt und anschließend erfolgreich auf seine Tragfähigkeit getestet. Neben der Traglastprüfung wurde auch das Dauerstandverhalten im Otto-Mohr-Laboratorium der TU Dresden geprüft. Die vertikalen Belastungen werden bei dem Deckenelement über einen Druckbogen mit Zugband abgetragen. Der Bogen entspricht dabei einer einfach gekrümmten Schale mit einer Wandstärke von gerade einmal 4,5 cm. Der Bogenschub wird über in den Stegen angeordnete Carbonstäbe aufgenommen. Bei einer unsymmetrischen Belastung des Druckbogens wird die Beanspruchung über Biegung aufgenommen.
Das Deckenelement wiegt mit 400 kg gerade einmal 30 % eines herkömmlichen Stahlbetonvollquerschnitts mit gleichen Außenabmessungen. Mit dem Konstruktionsprinzip konnte ca. 1 t Beton und damit auch natürliche Rohstoffe wie Kies gespart werden. Das neu entwickelte Deckenelement zeigt sehr gut, dass durch die Verwendung von flexiblen und hochfesten Carbonbewehrungen zukünftig ein nachhaltiges sowie ressourcensparendes Bauen unter Einhaltung der erforderlichen Nachweise möglich ist.
Bericht aus dem Jahrbuch 2017
RESSOURCENSPARENDES DECKENBAUTEIL AUS CARBONBETON
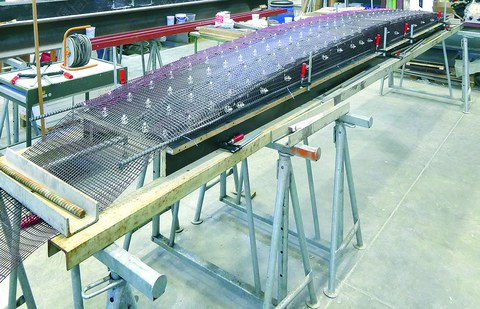
Bogenschalung mit Stab- und Mattenbewehrung aus Carbon
Im Rahmen eines Institutsprojektes entwickeln, erforschen und prüfen wir materialeffiziente Deckenbauteile aus Carbonbeton für den herkömmlichen Hochbau. Durch die Reduzierung der benötigten Betondeckung auf ein Minimum – für Carbonbewehrung notwendig zur Sicherstellung der Verbundkraft-übertragung – können Carbonbetonbauteile
gegenüber dem konventionellen Stahlbetonbau, wo eine viel größere Betondeckung zum Schutz der Bewehrung vor Korrosion gebraucht wird, mit deutlich geringeren Bauteildicken hergestellt werden.
Durch die Kombination von höherfesten Betonen – welche im Rahmen des Verbund-projekts C3-B2 entwickelt wurden – und der hochfesten Carbonbewehrung können formoptimierte Bauteile deutlich effizienter und ressourcensparender gebaut werden. Dies wurde bereits anhand eines Carbonbetonträgers im Vorhaben C3-B2 gezeigt, bei dem eine Reduzierung der benötigten Betonmenge um 50 % gegenüber einem herkömmlichen Stahlbetonträger erzielt werden konnte.
Nun wurden leichte Carbonbeton-Deckenelemente hergestellt und erfolgreich auf ihre Tragfähigkeit getestet. Bei dem Deckenelement werden die vertikalen Belastungen über einen Druckbogen mit Zugband abgetragen. Der Bogen entspricht dabei einer einfach gekrümmten Schale mit einer Wandstärke von gerade einmal 4,5 cm. Der Bogenschub wird über in den Stegen angeordnete Zugstäbe aufgenommen. Bei einer unsym-metrischen Belastung des Druckbogens wird die Beanspruchung über Biegung aufgenommen. Das neu entwickelte Deckenbauteil wiegt mit 400 kg ungefähr 1,0 t weniger als ein Stahlbetonvollquerschnitt mit gleichen Außenabmessungen. Somit konnte mit dem Konstruktionsprinzip 70 % an Beton gespart werden. Die Herstellung des auch optisch ansprechenden Deckenbauteils konnte nur mit der flexiblen und hochfesten Textilbewehrung aus Carbon erfolgen.
Mit der Bauteilprüfung im Otto-Mohr-Laboratorium der TU Dresden konnte, wie bereits rechnerisch vorab ermittelt, bewiesen werden, dass alle Anforderungen an das Bauteil in den Grenzzuständen der Tragfähigkeit und der Gebrauchstauglichkeit eingehalten sind. Aktuell befindet sich noch ein Deckenelement im Dauerstandversuch. Hierbei wird über sechs Monate eine konstante Last auf das Bauteil aufgebracht und so das Langzeitverhalten des Verbundwerkstoffes geprüft. Nach dem Dauerlastversuch wird im Frühjahr 2018 die Resttragfähigkeit des Deckenelements geprüft werden.
Bericht aus dem Jahrbuch 2016
Leichtes Carbonbetondeckenelement
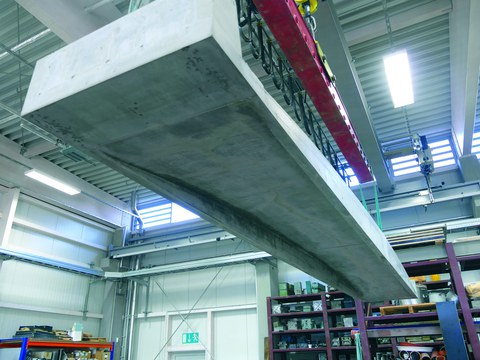
Unteransicht des leichten Deckenelementes aus Carbonbeton
Herkömmliche Stahlbetondeckendicken können über den Grenzwert der Biegeschlankheit abgeschätzt werden. Das Verhältnis von Spannweite zur Nutzhöhe darf dabei im Allgemeinen maximal 35 sein. Bei Flachdecken des üblichen Hochbaus wird lt. Zilch/Zehetmaier in der Regel der Grenzwert 25 angenommen. Bei Vollplatten mit einer Spannweite von 4,5 m ergibt sich somit eine Nutzhöhe von 18 cm. Zur Bestimmung der Deckendicke muss noch die Betondeckung von rund 3 cm berücksichtigt werden. Die Decke weißt somit eine Höhe von 21 cm auf und erfüllt die oben beschriebenen Grenzwerte. Wird hierbei nun ein Meterstreifen einer Platte betrachtet, dann wiegt das Deckenelement mit den genannten Querschnittsmaßen über zwei Tonnen. Zudem wird viel Material verbraucht.
Zur Sicherstellung der Tragfähigkeit und der Gebrauchstauglichkeit einer Konstruktion hinsichtlich einer Biegebeanspruchung wird ein innerer Hebelarm zwischen Druck- und Zugzone benötigt. Der Bereich dazwischen ist i. d. R. nicht voll ausgelastet und bietet Potential zur Materialeinsparung. Dies geschieht unter anderem schon bei Stahlbetonhohldielen. Eine solche alternative Bauweise erlaubt eine Reduzierung des Eigengewichts und des Materialbedarfs bei gleicher Leistungsfähigkeit.
In der genannten Vollpatte bildet sich unter Gleichlast ein Druckbogen zwischen den beiden Auflagern aus. Die Zugkraft wird durch die Biegezugbewehrung aufgenommen. Der Druckbogen entsteht im Beton. Dieser Mechanismus wurde in einem kleinen internen Forschungsprojekt aufgegriffen. Es sollte ein Deckenelement entwickelt und erforscht werden, das durch die Kombination von Bogentragwirkung und Verwendung von Carbonbeton eine leichte und extrem belastbare Konstruktion im Hochbau ergibt. In vorausgehenden Berechnungen wurde festgestellt, dass gegenüber der herkömmlichen Vollplatte über 50 Prozent an Gewicht und somit Material gespart werden können. Das Carbondeckenelement erlaubt daher eine materialgerechte, intelligente und nachhaltige Bauweise im Hochbau.
Anschließend wurde die Schalung und auch die ersten Prototypen hergestellt. Die 450,0 cm × 62,5 cm × 20,0 cm großen und 4,0 cm dicken Elemente werden Anfang 2017 einem Tragfähigkeitstest unterzogen werden, die dann Grundlage für ein darauf aufbauendes Forschungsprojekt mit Praxispartnern sein werden.
CRC-Decke mit alternativer Verankerung
Titel | Title Carbonbetondeckenelement mit alternativer Verankerung | Ceilings made of carbon reinforced concrete with alternative anchoring Förderer | Funding Institut für Massivbau, TU Dresden Zeitraum | Period 01.2016–04.2016 Leiter | Project manager Prof. Dr.-Ing. Dr.-Ing. E.h. Manfred Curbach Bearbeiter | Contributors Dr.-Ing. Harald Michler, Dipl.-Ing. Alexander Schumann |
Bericht aus dem Jahrbuch 2016
Parkhausplatte aus Carbonbeton
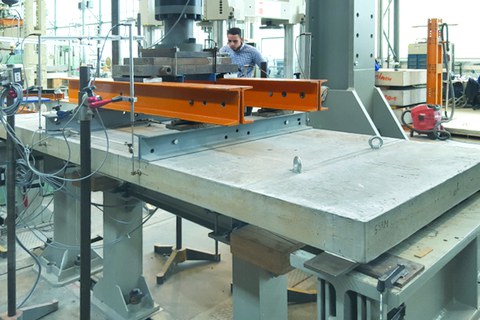
4-Punkt-Biegeversuch am Deckenelement
Heutzutage weisen viele Parkhausdecken aus Stahlbeton erhebliche Schäden auf. Die Stahlbewehrung in den Deckenplatten erfährt aufgrund der hohen Chloridbelastung infolge des im Winter verwendeten Tausalzes oftmals erhebliche Korrosionsschäden. Um dieser Problematik entgegenzuwirken, müssen die Platten mit teuren Beschichtungen und Oberflächenschutzsystemen versehen werden. Eine Alternative zu konventionellen Systemen stellt aufgrund der nicht korrosionsgefährdeten Carbonfasern die Herstellung von Parkhausplatten mit Carbonbeton dar. Aus diesem Grund wurde in einem Tast-
versuch die prinzipielle Eignung einer Deckenplatte aus Carbonbeton untersucht. Es wurde eine Platte mit einer Dicke von 10 cm, einer Spannweite von 2,5 m und einer Breite von 1 m hergestellt. Als Materialien kamen für den Beton der Feinbeton Pagel TF10 und für die Bewehrung das Gelege TUDALIT-BZT1-TUDATEX zur Anwendung.
Eine Herausforderung bei der konstruktiven Durchbildung des Deckenelementes stellte die Endverankerung der Bewehrung dar. Um die vollständige Tragfähigkeit der Gelege ausnutzen zu können und um ein Auszugversagen zu verhindern, wurde das Carbongelege in den Endbereichen des Bauteils in Form von Schlaufen ausgebildet und wieder zurück in die Bauteilmitte geführt. Somit konnte die Bewehrung in Feldmitte problemlos 3-lagig verbaut werden. Die Herstellung der Carbonbetondecke erfolgte im Gießverfahren, wobei das Carbongelege mit Abstandhaltern in ihrer Lage gesichert wurde.
Die Tragfähigkeit des Bauteils wurde im 4-Punkt- Biegeversuch ermittelt. Die maximal aufnehmbare Prüflast der Carbonbetondecke betrug im Versuch 158 kN. Bei dieser Last war die Grenzdehnung des Geleges erreicht und es trat ein Zugversagen ein. Die Bruchspannung des Carbongeleges in der untersten Lage betrug 1950 N/mm². Somit konnte die volle Festigkeit des Carbongeleges erzielt werden. Mit Berücksichtigung des Eigengewichts konnte das Bruchmoment zu 65,6 kNm bestimmt werden, womit für den gewünschten Anwendungsbereich die erforderliche Tragfähigkeit sicher gewährleistet ist.
Mit dem durchgeführten Bauteilversuch konnte nachgewiesen werden, dass für Parkhausplatten aufgrund der nichtkorrodierenden Fasern der Verbundwerkstoff Carbonbeton eine sinnvolle Alternative darstellt. Weiterhin konnte das Problem der Endverankerung für Neubauteile mit flexiblen Gelegen durch die im Bauteilversuch erprobte Bewehrungsführung gelöst werden.