Textilbeton unter Druck – Einfluss biaxialer Lasteintragung
Inhaltsverzeichnis
Projektdaten
Titel | Title |
Bericht aus dem Jahrbuch 2023
Spannung von allen Seiten
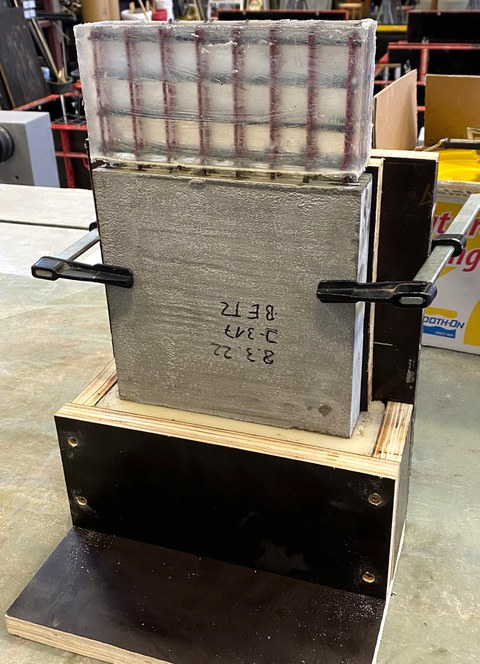
Harzbad zur Einbettung der überstehenden Carbonbewehrung
In der ersten Projektphase wurden Carbonbetonwürfel unter einaxialer Druckbeanspruchung untersucht. Es wurden verschiedene Parameter identifiziert, die die Tragfähigkeit maßgeblich reduzierten, z. B. die Tränkung. Diese Effekte zeigten sich bei unterschiedlichen Betonen gleichermaßen. In Phase 2 des Projekts sollten darauf aufbauend zusätzlich induzierte Querdruck- und -zugbeanspruchungen untersucht werden. Während bei Beton von einer erhöhten Festigkeit bei mehraxialen Druckspannungszuständen ausgegangen wird, sorgt die aus Zugbeanspruchungen resultierende Rissbildung für reduzierte Festigkeiten.
Um zu überprüfen, inwieweit diese Prinzipien auf Carbonbeton übertragbar sind, wurden mit Carbongittern bewehrte Scheiben der Abmessungen 200 × 200 × 40 mm³ aus dem Feinbeton Pagel TF10 hergestellt. Variiert wurden die Herstellungsart (gegossen und laminiert), Lagenanzahl und Orientierung des Bewehrungsgitters sowie verschiedene Gittertypen mit unterschiedlichen Tränkungen, Garnstärken und Maschenweiten.
Die biaxiale Belastung erfolgte bei allen Versuchen in der Bewehrungsebene. Für die Druckbelastungen wurde auf das bewährte Prinzip der Belastungsbürsten zurückgegriffen. Für die Einleitung der Zugkräfte in die Carbongitter musste aufgrund der begrenzten Platzverhältnisse in der Triaxialprüfmaschine eine neue Verankerungskonstruktion entworfen werden. Dies erfolgte schlussendlich über die Klemmung von Harzblöcken, in die die Carbongitter eingebettet wurden.
Bei den Druck-Druck-Versuchen zeigte sich, dass das bloße Vorhandensein einer Gitterbewehrung den größten Einfluss auf die Tragfähigkeit der Probekörper hatte. Das Versagen war stets dominiert durch ein Spalten in der Bewehrungsebene, die weiteren variierten Parameter waren demgegenüber nur von untergeordneter Bedeutung. Die Druck-Zug-Versuche konnten die Annahmen aus dem Stahlbetonbau bestätigen, dass es bei gerissenen Probekörpern zu einer Reduktion der ansetzbaren Druckfestigkeit kommt. Maßgeblich war hier das Rissbild, welches nicht nur von der eingeleiteten Zugkraft, sondern auch von den Parametern Bewehrungsgrad und Tränkung maßgeblich beeinflusst wurde.
Bericht aus dem Jahrbuch 2022
Nächster Zug der Druckbemessung
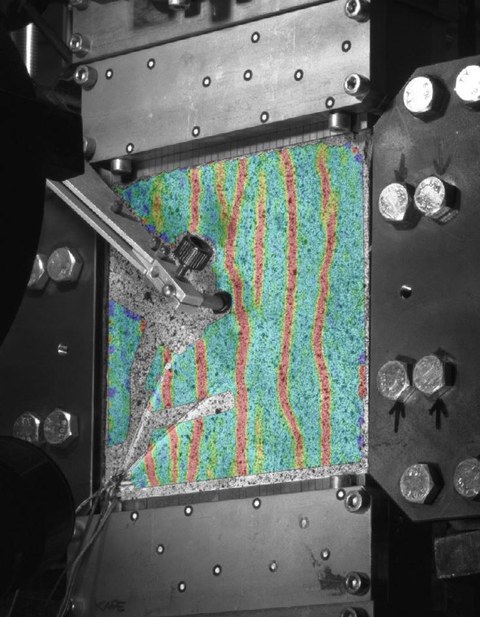
Photogrammetrische Aufnahme des Rissbilds
Mit fortschreitender Forschung werden immer weitere Bemessungsmodelle für den Carbonbetonbau entwickelt, was zu einer Reduzierung der Markteintrittsbarrieren führt und dabei hilft, den Werkstoff zu etablieren. Zum Zugtragverhalten von Carbonbeton liegen inzwischen eine umfangreiche Datenbasis und eine Vielzahl an Bemessungsansätzen vor. Wie genau das Material in druckbeanspruchten Bereichen ausgenutzt werden kann, ist hingegen in einigen Details noch zu klären.
Nachdem in Phase 1 des Forschungsprojekts der Einfluss von Carbonbewehrung in verschiedenen Konfigurationen auf die einaxiale Druckfestigkeit des Werkstoffs untersucht wurde, behandelt die hier beschriebene zweite Phase zweiaxiale Spannungszustände. Neben den Tests mit zweiaxialen Druckbeanspruchungen, welche bereits abgeschlossen werden konnten und die die aus dem Stahlbetonbau bekannte Steigerung der Betondruckfestigkeit genauer untersuchen sollten, steht dabei der Einfluss einer zusätzlich zur Druckbelastung induzierten Querzugbeanspruchung im Fokus. Aus dem Stahlbetonbau ist bekannt, dass die damit einhergehende Rissbildung des Prüfkörpers bzw. des Bauteils zu einer signifikanten Abminderung der aufnehmbaren Druckkräfte führt. Beachtet werden muss dieser Effekt u. a. bei der Bemessung für Querkräfte und Torsionsbeanspruchung.
Bei der Versuchsdurchführung werden sowohl proportionale Lastpfade abgefahren – hierbei werden Druck- und Zugkraft in einem festen Verhältnis zueinander gesteigert – als auch vordefinierte Zugdehnungsniveaus in der Bewehrung angesteuert und anschließend die verbliebene Tragfähigkeit unter Druckbeanspruchung geprüft. Mithilfe von Harzblöcken, die die Carbonbewehrung in den Lasteinleitungsbereichen umschließen, kann auch bei den begrenzten Platzverhältnissen der mehraxialen Prüfmaschine eine ausreichend hohe Zuglast in die Probekörper eingebracht werden, ohne dass es zu einem Verbundversagen der Bewehrung in den Verankerungsbereichen kommt. Es werden unterschiedliche Bewehrungskonfigurationen untersucht, um u. a. den Einfluss des Bewehrungsgrads und des Tränkungsmaterials genauer zu analysieren, und auch die Herstellungsart variiert.
Bericht aus dem Jahrbuch 2021
Carbonbeton gerät unter Druck
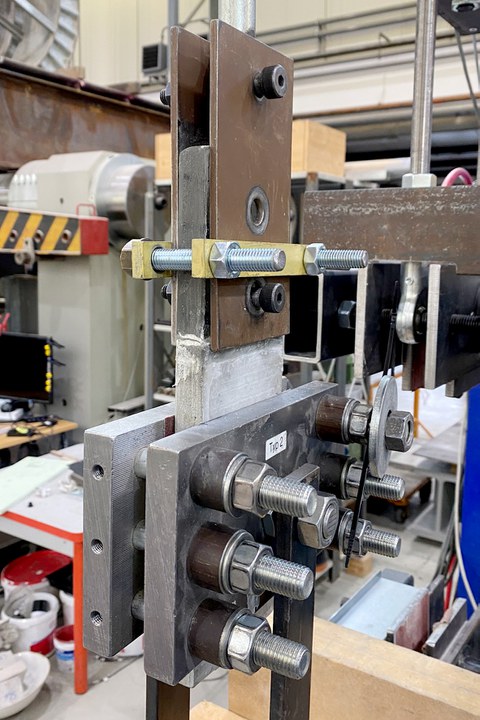
Versuch zur Erprobung der Zugverankerung aus Harz
Während sich die bisherige Forschung im Carbonbeton überwiegend auf das Zugtragverhalten des Verbundwerkstoffs fokussierte, ist das Wissen zum Drucktragverhalten noch rudimentär. In der ersten Projektphase Carbonbeton unter Druck wurden erste Untersuchungen hinsichtlich der einaxialen Druckbelastung durchgeführt und verschiedene Einflussfaktoren identifiziert. Dem Bewehrungsgrad wurde bspw. ein großer Einfluss auf die Drucktragfähigkeit zugesprochen, während die Art der Herstellung eine untergeordnete Rolle spielt. Für die Anwendung am Bauteil eignen sich diese Untersuchungen nur bedingt, da einaxiale Belastungen nur in seltenen Fällen vorkommen. In der Realität liegen meist mehraxiale Spannungszustände vor.
Die zweite Projektphase beschäftigt sich daher mit der Validierung der bisherigen Erkenntnisse für bauteilnähere Spannungszustände anhand zweiaxialer Versuche. Unterschieden wird zwischen zweiaxialen Druckbelastungen und Druckbelastungen mit Querzug in der Bewehrungsebene. Während es bei ersterem um die im Stahlbetonbau gegebene Erhöhung der Druckfestigkeit des Betons in Sonderfällen geht, ist die Abminderung der Druckfestigkeit bei gerissenen Bauteilen, also Druckzonen mit Querzug, für die Querkraft- und Torsionsbemessung essentiell. Für beide Belastungsarten sind Untersuchungen zum Einfluss von Lagenanzahl, Garndurchmesser, Maschenweite, Tränkung, Herstellung und zur Orientierung der Bewehrung vorgesehen. Der Großteil der zweiaxialen Druckversuche konnte dieses Jahr erfolgreich abgeschlossen werden.
Wichtig für eine erfolgreiche Projektdurchführung ist die Wahl geeigneter Lasteinleitungssysteme. Bei den Druckkräften konnte auf bewährte Lasteinleitungsprinzipien zurückgegriffen werden, für die Einleitung der Zugspannungen in die Bewehrung ist jedoch aufgrund der begrenzten Platzverhältnisse in der Triaxialprüfmaschine die Entwicklung einer neuer Verankerungskonstruktion erforderlich. Neben einer gleichmäßigen Einbringung der Zugspannungen ist auf eine möglichst geringfügige Beeinträchtigung der Druckspannungsverteilung zu achten. In Voruntersuchungen wurden dazu verschiedene Verankerungssysteme mit Klemmungen und Bolzen, Verankerungsbereichen aus Harz und Beton sowie zusätzlich besandete Bewehrungen betrachtet.
Bericht aus dem Jahrbuch 2020
Carbonbeton unter Druck – Phase 2
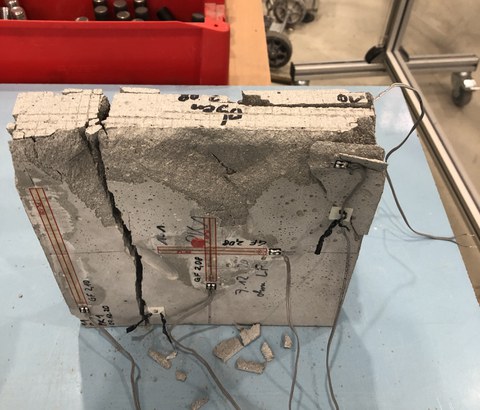
Probekörper nach dem Versuch
Viele Bereiche des Carbonbetons sind bereits seit Jahren Bestandteil der Forschung und weisen erhebliche Fortschritte bei der Reglementierung des Werkstoffes im Bauwesen auf. Während für die Biegung, Querkraft und Torsion beispielsweise Modelle oder Modellierungs-ansätze bestehen, gibt es kaum Kenntnisse über das Verhalten von Carbonbetonbau-teilen unter Druckbelastungen. Erste Erkenntnisse zum Verhalten von Carbon-beton unter einaxialer Druckbelastung konnten in der ersten Projektphase gewonnen werden. Bereits die Umstellung des Herstellungsprozesses von gegossenen Probekörpern auf handlaminierte Einbringung der Textillagen führte zu einer Abminderung der Tragfähigkeit. Untersucht wurde weiterhin der Einfluss verschiedener Parameter auf die Druckfestigkeit von Carbonbeton-würfeln, wie der Lagenabstand, die Garnstärke, die Maschenweite oder eine versetzte Anordnung der Textillagen. Aufbauend auf den Ergebnissen der ersten Projektphase soll untersucht werden, inwieweit sich diese Erkenntnisse auf praxisrelevante Bauteile übertragen lassen. Ein erster Schritt in diese Richtung erfolgt in der aktuell laufenden zweiten Projektphase über mehraxial belastete Carbonbetonscheiben mit den Abmessungen 200 x 200 x 40 mm³. In den meisten Bauteilen liegen (durch beispielsweise Torsions- oder Querkraftbelastungen) induzierte mehraxiale Spannungszustände vor.
Aus diesem Grund sollen basierend auf den Kenntnissen aus dem Stahlbetonbau sowohl mögliche Tragfähigkeitssteigerungen durch Druck-Druck-Belastungen sowie Abminderungen durch Druck-Zug-Belastungen untersucht werden. Neben der textilen Bewehrung selbst, dazu zählen Tränkung, Lagenabstand, Maschen-weite und auch die Textilorientierung, sollen vor allem der Herstellungsprozess und unterschiedliche Spannungsverhältnisse bei den Versuchsdurchführungen variiert werden. Auf Basis der Ergebnisse aus der zweiten Projektphase soll ein numerisches Materialmodell entworfen beziehungsweise das Modell aus der ersten Projektphase erweitert werden. Mit Hilfe dieses Modells können virtuelle Parameterstudien an Großbauteilen durchgeführt werden, um die in einer weiteren Projektphase vorgesehenen Großbauteilversuche zu planen und diese später mit möglichst geringem Aufwand durchführen zu können. Darüber hinaus sollen diese Großbauteilversuche das mit Abschluss dieser Projektphase aufgestellte Materialmodell verifizieren.