Auflösung kompakter Bauteile
Inhaltsverzeichnis
Projektdaten
Titel | Title |
Kurzfassung Förderphase 2
Projektziel ist die Entwicklung einer grundlegenden Methodik für den Entwurf materialeffizienter Carbonbetonbauteile auf der Grundlage normalspannungsaktiver, schalenförmiger Strukturen mit unterschiedlichen Krümmungen, mit denen der in der Regel massive Bauteilquerschnitt aufgelöst wird. In Förderperiode 1 wurde diese Konstruktionsidee in ihren Grundzügen für global biegebeanspruchte Tragelemente des üblichen Hochbaus untersucht. In Förderperiode 2 wird der Designraum grundlegend erweitert, um darauf basierend den Ansatz zu verallgemeinern. Des Weiteren werden Durchdringungspunkte und Details, Restriktionen verschiedener Herstellmethoden und die Umweltwirkung vertieft betrachtet.
Bericht aus dem Jahrbuch 2023
Aufgelöste TRC-Strukturen im 1 : 1-Test
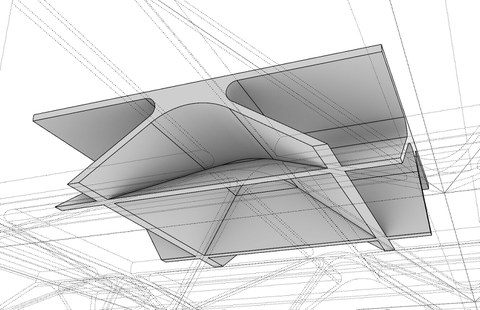
Detail eines innerlich aufgelösten Deckenelements
2023 wurde die Betonierkammer so modifiziert, dass die Herstellung von großformatigen, innerlich aufgelösten Deckenelementen mit der Methodik des Betongießens unter reduziertem Luftdruck möglich wurde. Außerdem wurde die Validierung des numerischen Simulationsworkflows klar vorangebracht.
Ein Hauptziel 2023 war es, in zwei geometrischen Varianten realmaßstäbliche Plattenelemente aus Textilbeton (TRC) mit schalenartigen Substrukturen, die das üblicherweise massive Bauteilinnere auflösen, zu entwickeln und zu untersuchen. Die erste Variante wies eine einfache parallele Orientierung der auflösenden Tragprofile auf. Bei Variante zwei wurde eine kreuzweise Orientierung der tragenden Substrukturen realisiert. Gemäß der durchgeführten Parameterstudie innerhalb des zuvor definierten zulässigen Parameterraums wurden die inneren Membranen der TRC-Elemente mit einer Dicke von 10 mm und einer ebenen Geometrie gewählt, die sich aus dem Grunddesign des Plattenquerschnitts ergab. Für die Laborversuche wurden Elemente mit 100 mm und mit 200 mm Höhe geplant.
Für die Herstellung der Deckenelemente musste eine große Anzahl einzelner Komponenten vorbereitet und korrekt zusammengesetzt werden. Beispielsweise verfügt jede Struktur über zahlreiche Schalungsblöcke aus extrudiertem Polystyrol (XPS), die sowohl die äußere Form als auch die inneren Hohlräume der aufgelösten Elemente bildeten. Die XPS-Blöcke wurden mit speziellen Abstandhaltern platziert, um die geplante Substrukturdicke möglichst exakt verwirklichen und die Textilbewehrung vom Typ solidian GRID Q85-CCE-21 genau mittig in den dünnen TRC-Membranen positionieren zu können.
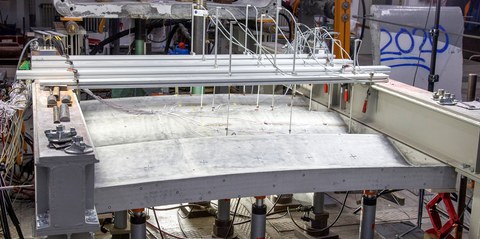
Im Inneren aufgelöstes Plattenelement im 9-Punkt-Biegeversuch
Am 3. Tag nach der Herstellung wurden die Elemente ausgeschalt, die Biegetests fanden jeweils im Betonalter von 28 Tagen statt. Dabei wurden die Platten quasi verkehrt herum getestet, da es aus versuchstechnischen Gründen einfacher war, die Belastung von unten auf die Elemente aufzubringen. Die neun gleichmäßig verteilten Punktlasten wurden von synchronisierten Hydraulikzylindern erzeugt. Das Versagen trat jeweils in der Nähe der Linienlagerung auf. Die numerische Simulation zeigte eine gute Übereinstimmung mit den experimentellen Ergebnissen, insbesondere in Bezug auf die Biegeverformung und die Lage der gerissenen Bereiche. Bei der Abschätzung der Grenztragfähigkeit ergab sich eine Differenz von 25 % zwischen Versuch und Numerik. Die Problematik der Brucherkennung wird deshalb im Jahr 2024 hohe Priorität haben.
Bericht aus dem Jahrbuch 2022
Validierung des numerischen Modells
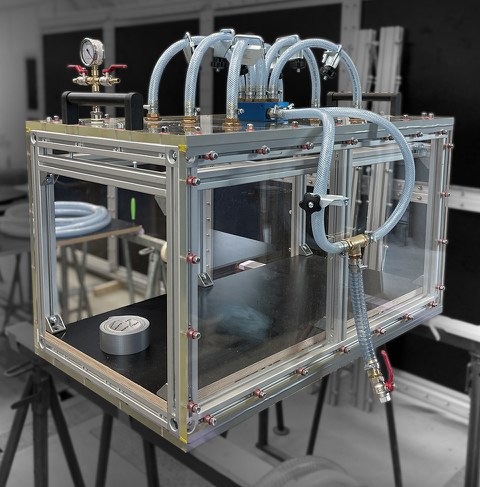
Kleine Vakuumkammer für das Betonieren von Standardproben
Für die erfolgreiche und koordinierte Umsetzung der anstehenden Arbeitspakete des C01-Projekts im SFB/Transregio 280 war es wichtig, die Vorarbeit in beiden Schwerpunktbereichen des Projekts soweit abzuschließen, dass klare Entwurfs- und Prüfabläufe vorliegen. Es wurden grundlegende experimentelle Fragen gelöst und eine Versuchsberechnung der einfach gestützten Bogenschale durchgeführt. Sowohl das Ergebnis der numerischen Analyse als auch die experimentellen Ergebnisse müssen in den nächsten Schritten der Projektbearbeitung abgeglichen werden.
2022 wurde eine spezielle Mehrzweckschalung entwickelt, die das Betonieren von Carbonbetonproben unterschiedlicher Form ermöglicht. Für eine kontrollierte Formgebung werden die Proben in einer Hülle aus extrudiertem Polystyrol (XPS) gegossen. Jeder XPS-Block wurde mit einer Heißdraht-CNC-Maschine zugeschnitten und anschließend mit einer Schicht aus Epoxidharz versehen, um eine gute Trennung von der ausgehärteten Betonprobe zu gewährleisten. Mit automatisch generierten und 3D-gedruckten Abstandhaltern kann die Textilbewehrung sehr genau in der gewünschten Position gehalten werden.
Darüber hinaus widmete sich ein großer Teil der Projekttätigkeit der Vorbereitung des Betonierens unter Vakuumbedingungen. Das geplante Gießverfahren wird als Vacuum-Infused Textile Reinforced Concrete Moulding (kurz: VI-TRC-M) bezeichnet. Dazu wurden zwei Vakuumkammern konstruiert und hergestellt. Die kleinere Kammer zielte darauf ab, alle erforderlichen Standardproben zeitgleich betonieren zu können. Die Proben werden für Zug-, Druck- und Spaltversuche verwendet. Auch sind Standardversuche am Komposit Carbonbeton vorgesehen. Die zweite, größere Kammer ist zum Gießen von großformatigen TRC-Elementen mit maximalen Abmessungen von bis zu 3,5 m Länge, 1,1 m Breite und 0,4 m Höhe geeignet. Diese Kammer ist mit zwei für das Projekt wichtigen Funktionen ausgestattet. Zum einen kann sowohl unter Vakuum als auch unter normalen, also Nicht-Vakuumbedingungen betoniert werden. Zum anderen bieten Verbindungselemente die Möglichkeit einer Erweiterung der Geometrie in alle drei Raumrichtungen, falls dies für größere zu testende Proben in späteren Projektphasen erforderlich ist.
Bericht aus dem Jahrbuch 2021
Vorbereitung der Technologietests
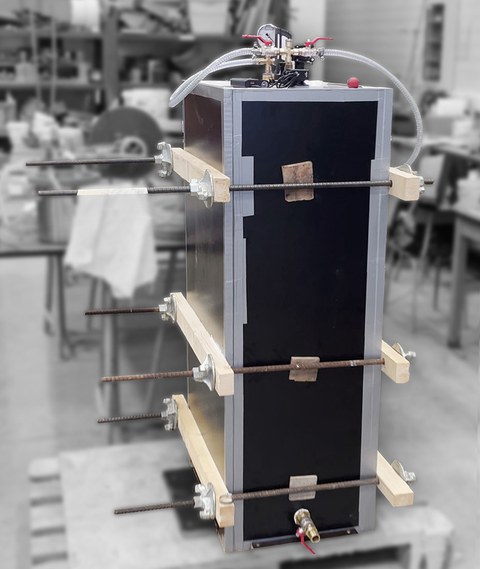
Zum Betonieren vorbereitete Vakuumkammer
Im ersten Förderjahr war die Hauptaufgabe, den Softwarehintergrund für künftige Optimierungsroutinen für neuartige, leichte Carbonbetontragwerke mit schalenförmiger innerer Auflösung zu schaffen. Dabei ergaben sich neue Fragestellungen wie z. B. Einschränkungen gemäß der verfügbaren Produktionsmethoden und Anforderungen infolge des geforderten Freiheitsgradbereichs der Optimierungsverfahren.
Die resultierende innere Struktur wird überwiegend aus mehreren, sich kreuzenden Schalen und – im Optimalfall – variierenden, bio-inspirierten Formen bestehen. Die Schalendicken sind variabel, um möglichst gut dem Kraftfluss zu entsprechen. Um eine solche Flexibilität zu ermöglichen, muss eine Methode zur Realisierung der Hohlkörper entwickelt werden, die mit minimalem Aufwand anpassbar ist. Zudem ist es erforderlich, faserbasierte Bewehrungen in zugbeanspruchten Bereichen zu integrieren.
Zu Beginn wurden Randbedingungen für die Herstellung derartiger Schalen für erste Versuche festgelegt. Zum Beispiel sollen gekrümmte Oberflächen durch Regelflächen beschreibbar sein, um die breite Palette bekannter Techniken für die Schalungsherstellung nutzen zu können. Als Schalungsmaterial wurde extrudiertes Polystyrol (XPS) gewählt. Außerdem wurde ein geeignetes Trennmittel zwischen Beton und XPS-Oberfläche ausgesucht. Um den Beton der tragenden Schalenkonstruktion kontrolliert und mit hoher Oberflächenqualität gießen zu können und wegen der geplanten komplizierten, inneren Geometrie, wurde beschlossen, die bekannte Technologie der Vakuuminjektion – weit verbreitet in der Automobilindustrie – an die Bedürfnisse des Betonbaus anzupassen. Die Idee dahinter ist, das Vakuum nicht zum Pumpen des Betons zu verwenden, sondern den Beton in den kompliziertesten Bereichen durch Entfernen der eingeschlossenen Luft zum Fließen zu bringen und ihn so bis in kleinste Hohlräume zu füllen. Zur Überprüfung der Methode wurde eine spezielle Vakuumkammer entworfen und gebaut.
Anfang 2022 sind erste Tests zur Herstellung von kleinen Schalenelementen und von Verbundprobekörpern geplant. Nach deren erfolgreicher Prüfung sind Herstellung und Test einer großformatigen, bogenförmigen Schale geplant. Die Ergebnisse dienen als Grundlage für komplexere Schalenkonstruktionen und deren numerische und experimentelle Analyse.
Bericht aus dem Jahrbuch 2020
Neuartig konstruieren mit Carbonbeton
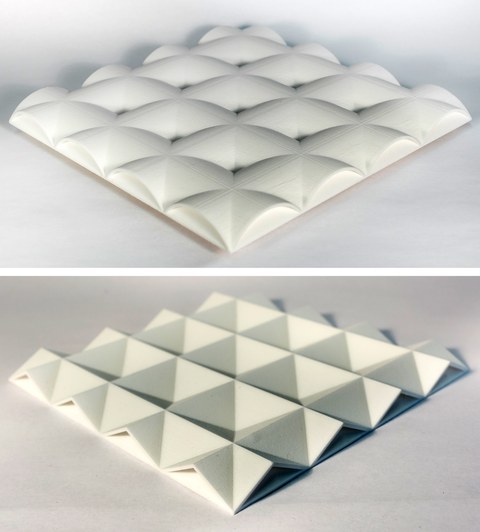
Erste Strukturideen für neuartige Carbonbetonkonstruktionen
Übergeordnetes Ziel des Teilprojektes C01 im SFB/TRR 280 ist es, Bauteile im Inneren durch lastabtragende Strukturen so aufzulösen, dass das volle Potenzial des Baustoffs Carbonbeton ausgenutzt werden kann.
Ein erster Ansatz sind sich selbst durchdringende Schalen- oder Faltwerkstrukturen. Um möglichst viele Lösungen dieser geometrischen Grundformen zu untersuchen, wurde entschieden, eine parametrische Umgebung der Software Rhino 3D + Grasshopper (GH) zu verwenden. Auf diese Weise dienen die als parametrisches Modell mit einer Vielzahl von Parametern entworfenen Formen, die alle geometrischen Merkmale der Struktur steuern und nach dem biomimetischen Prinzip – als DNA der ausgewählten Betonstruktur – funktionieren.
Eine wichtige Frage ist, nach welchen Kriterien die Leistungsfähigkeit der neuen Strukturen bewertet werden soll? Eine Möglichkeit ist das Mindestgewicht. Kernelement des iterativen Optimierungsverfahrens ist die parametrische Umgebung Die Berechnung startet mit ausgewählten Geometrielösungen, die über die DNA-Datenstruktur in die GH-Software eingefügt wurden. Anschließend können mehrere verbundene FEM-Lösungen verwendet werden, um eine qualitativ hochwertige Strukturanalyse durchzuführen. Im nächsten Schritt werden die Ergebnisse der Strukturanalyse überprüft, um potenzielle Fehler nach ausgewählten Fehlerkriterien unter Verwendung der ɛ-Constraint-Methode aus der Theorie der multiobjektiven Optimierungstechniken auszuschließen. Nur geometrische Lösungen, die der Anforderung genügen, werden weiter innerhalb des iterativen evolutionären Optimierungsprozesses verwendet. Wichtig ist, dass innerhalb des Projekts mehrere Zielfunktionen für die Optimierungsaufgabe untersucht werden – z. B. Zielfunktionen wie Mindestgewicht, auftretende Verformungen und Spannungen oder das effizienteste finanzielle Äquivalent der Betonstrukturen.
Bestandteil des Arbeitsplanes ist es außerdem, die theoretische Forschung durch Experimente zu verifizieren. Es sind Tests an kleinmaßstäblichen Proben, bspw. zur Herstellung und an Detailpunkten, aber auch an Deckenplatten im Metermaßstab geplant. Mit Hilfe der Tomographie soll zudem der innere Verformungsprozess unter Last beobachtet werden.