Resolving compact components
Table of contents
Project data
Titel | Title |
Summary of funding period 2
The aim of the project is to develop a fundamental methodology for the design of material-efficient carbon-reinforced concrete components on the basis of normal stress-active, shell-shaped structures with different curvatures, with which the usually solid component cross-section is resolved. In funding period 1, this design idea was investigated in its basic features for globally bending load-bearing elements of conventional building construction. In funding period 2, the design space will be fundamentally expanded in order to generalize the approach on this basis. Furthermore, intersections and details, restrictions of different manufacturing methods and the environmental impact will be analyzed in depth.
Report from the annual report 2023
Resolved TRC structures in real-scale tests
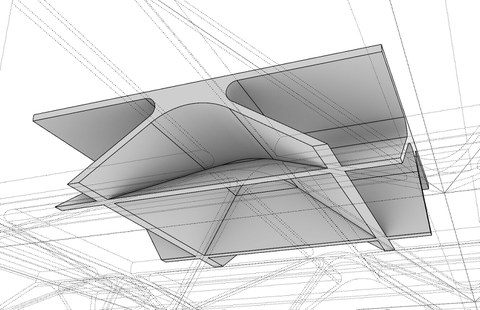
Detail eines innerlich aufgelösten Deckenelements
After a sequence of technology tests, the concreting methodology was verified in 2023. Thus, the concreting chamber was modified to incorporate the required size of the planned resolved slab elements for the methodology of die casting under reduced air pressure conditions. Also, the preparation and validation of the numerical simulation workflow were conducted including the selection of the most appropriate material models.
In the working packages in 2023, the goal was to develop and investigate full scale textile-reinforced concrete (TRC) elements with resolving internal shell-type substructures in two geometrical variants. The first solution assumed a single orientation of the main load-bearing profiles and, in contrast, the second solution possessed double orientation of folds or shell segments. According to the performed parametric study within the admissible parametric space, the inner membranes of TRC elements were selected to be 10 mm thick with a non-curved geometry, resulting from the principal design of the plate’s cross section. It was decided to perform tests with two total heights of the structures, 100 mm and 200 mm.
For manufacturing, the proposed TRC structures incorporated large amount of components to be assembled in proper order. Accordingly, each plate possessed a set of formwork blocks made of extruded polystyrene (XPS), that formed the outer shape as well as inner voids of the resolved elements. The XPS blocks were assembled with special spacers developed in the project in between to ensure a proper gap and to exactly position the textile reinforcement (solidian GRID Q85-CCE-21) in the middle of the thin TRC membranes.
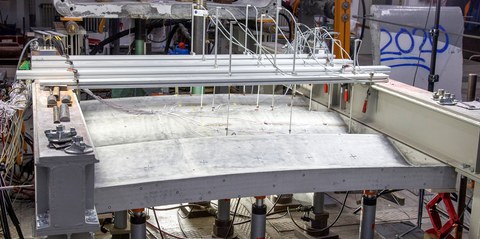
Internally resolved ceiling slab in the 9-point bending test
After the production, the large-scale elements were demolded on the 3rd day and consequently tested after storage under laboratory conditions at an age of 28 days. The plate structures were loaded with nine point loads introduced by synchronized hydraulic cylinders. Due to practical reasons, the elements were tested in upside down position. The structures failed due to reaching the limit force in the shear area close to the line supports. The numerical simulation showed good agreement with the experimental results, especially in regard of bending deformation and position of cracking zones. The estimation of the ultimate limit load in numerical analysis showed a deviation of 25 % from the experimental data. This topic will be addressed with high priority in 2024.
Report from the annual report 2022
Validation of the numerical model
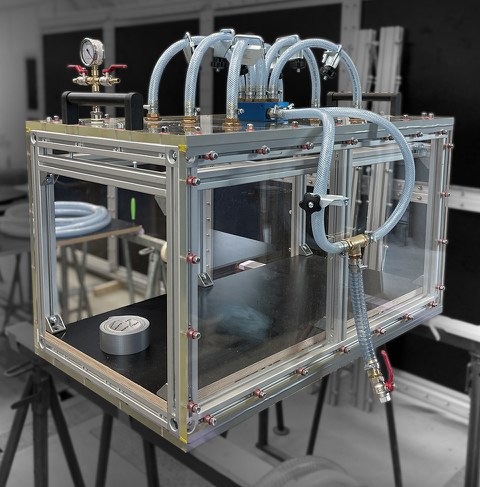
Small vacuum chamber for concreting of standard test samples
For the successful and coordinated implementation of the upcoming work packages of the C01 project of CRC/Transregio 280, it was important to complete the preparatory work in both key areas of the project in order to make clear design routines and test processes available. Basic experimental questions were solved and trial calculation of the simply supported arch-liked shell performed. Both the results from the numerical analysis and experimental results are getting to be matched in the upcoming working steps of the project.
In 2022, a special multipurpose concrete box was assembled for the concreting of carbon reinforced concrete samples with various shapes and geometries. To precisely control the shape, the samples assumed to be casted within the envelope made of extruded polystyrene (XPS). Each XPS block was cut using a hot wire CNC machine and covered afterwards with a layer of epoxy resin to ensure good separation of the hardened concrete sample during demoulding. With the help of automatically generated and 3D printed space holders, the carbon textile reinforcement can be hold very precisely in the required position.
Furthermore, a big part of the project activity was devoted to the preparation of the procedure of concrete casting under vacuum conditions that is mentioned as Vacuum-Infused Textile-Reinforced Concrete Moulding (VI-TRC-M) casting method. For this purpose, two vacuum chambers were assembled. The first smaller chamber aimed to perform a casting of sequence of standard samples at once. The samples will be later used either for tensile, compression or split tensile tests. Basic tests on the composite carbon reinforced concrete are also planned. The second, larger chamber was constructed for the purpose of casting of large scale TRC samples with maximum dimensions of up to 3.5 m in length, 1.1 m in width, and 0.4 m in height. The concrete casting formwork was designed with two important features for the project. On the one hand it can be used under normal non-vacuum and under vacuum conditions. On the other hand, connecting elements offer the possibility of extending the geometry in all three spatial directions if this is required for larger samples to be tested in later project phases.
Report from the annual report 2021
Preparation of the technology tests
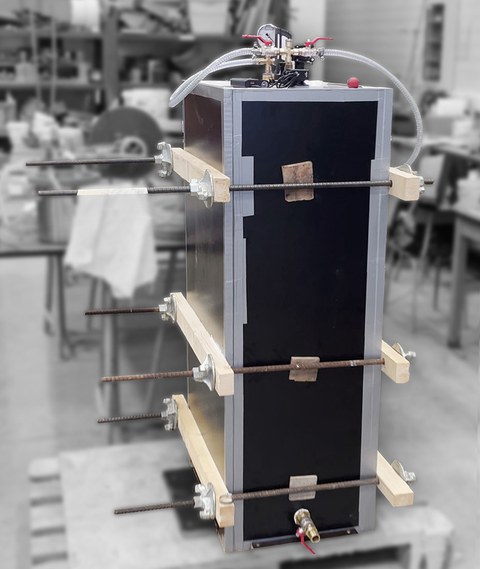
Vacuum chamber prepared for concreting
In the first year of funding, the main task was to create the software background for future optimisation routines for novel, lightweight carbon concrete load-bearing structures with a shell-like intersection inside. A new set of questions raised such as limitations according to the available production methods and demands resulting from the requested range of degree of freedom for the optimisation procedures.
The light inner structure will predominantly consist of multiple intersecting shells and – optimally – have a varying bio-inspired shape. The thickness of the shell components may also vary to be as well adapted as possible to the force flow. To provide such flexibility it is required to develop a method of realisation of the hollow parts that can be customisable with minimum efforts. Additionally, it is required to integrate textile reinforcement in structural parts under tension.
To keep the shells realizable for production for first experiments it was required to determine the boundaries such as application of only ruled surfaces. Thus, a curved formwork can be manufactured using wide range of techniques and machinery. Soft extruded polystyrene (XPS) was chosen for the preparation of non-bearing parts. Furthermore, a selection of an appropriate release agent to be used in between concrete and XPS surface. In order to pour concrete with precise control of all surfaces of the load bearing shell structure and because of the envisioned dense packing of the components it was decided to adapt the well know technology of vacuum injection, widely used for automotive industry, to the needs of concrete construction. The idea behind is not to use vacuum to pump the concrete but to help the concrete flow in the most complicated areas by removing trapped air and by this let concrete fill all up to the smallest void. For verification of the method, a set of special vacuum chambers was designed and assembled.
At the beginning of 2022, initial trials are planned for the production of small shell structures and test specimens to determine the bond behaviour between textile and matrix. After the successful sample tests, it is planned to manufacture and test a large simply supported arch like shell. The results will serve as basis for more complex shell designs and their numerical and experimental analysis.
Report from the annual report 2020
Preparation of the technology tests
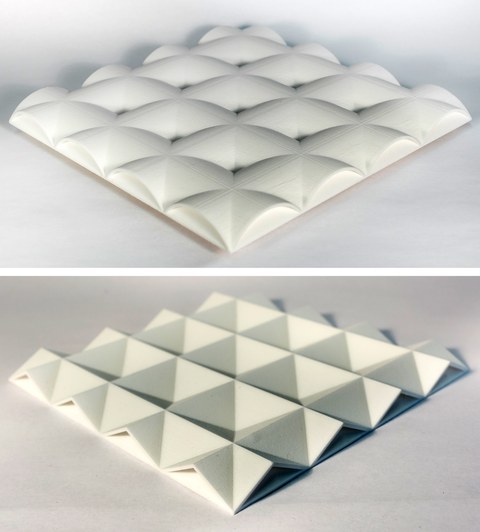
Initial shape ideas for new CRC structures
The overall objective of subproject C01 in the CRC/Transregio 280 is to use the full potential of the material carbon reinforced concrete in the construction of structural elements. A range of ideas has been developed since the beginning of the project in July 2020.
The original idea is self-intersected structures based on inner shells or foldings. To enable exploration as much as possible, within the range of visible solutions of the geometrical shapes, it was decided to use a parametric environment of Rhino 3D + Grasshopper (GH) software. Thus, the shapes designed as a parametric model with a wide range of parameters that control all the geometrical features of the structure and following the biomimetic principle serve as DNA of the selected concrete structure.
The important question is which criteria can be used to assess the performance of the new structures. For example, to reach a minimum weight, a special set of software solutions envisioned within the project. The core element is the parametric environment. To start the calculation procedure, the selected geometry range of solutions is inserted into the GH software, as the DNA data structure. Afterwards, multiple connected FEM solutions may be used to perform high-quality structural analysis. In the next step, the structural analysis results will be verified to exclude potential failure according to a range of selected failure criterion using the ɛ-constraint method from the theory of multiobjective optimization techniques. Only geometrical solutions that match the requirement finally can be used for further processing within the iterational evolutionary-based optimization process. Additionally, it is important to say that within the project it is assumed to explore multiple objective functions used for the optimization task. Such objective functions can be the minimum weight, occurring deformations and stresses or the most efficient financial equivalent of the concrete structures.
The theoretical research will be verified by experiments. Tests are planned on small-scale samples, e.g. for production and detail points, but also large scale ceiling tiles. Tomography will also be used to observe the internal deformation process under load.