Festigkeit und stoffgesetzliche Beschreibung von Beton unter biaxialem Impakt
Inhaltsverzeichnis
Projektdaten
Titel | Title |
Kurzbeschreibung
Beton kann in unterschiedlichsten Situationen stoßartiger oder wechselnder Beanspruchung unterliegen. Beispielsweise können Fels- und Gesteinsbrocken auf Betonstraßen herabstürzen, es kann in Unfallsituationen zu Fahrzeuganprall auf Betonkonstruktionen kommen, oder Tragkonstruktionen von Fabrik- und Fertigungshallen können dynamischer Belastung infolge schlag- und stoßartiger Maschinenprozesse ausgesetzt sein. Bei solchen Beanspruchungen unterliegt der Beton hohen Dehnraten, das bedeutet, dass sich die Dehnungswerte im Beton sehr schnell ändern.
Ziel des Projektes ist es, das Verhalten von Beton unter hohen Belastungsgeschwindigkeiten zu erforschen. Von besonderem Interesse ist dabei die Festigkeitssteigerung von Beton, das heißt, welchen Widerstand Beton dynamischer Belastung im Vergleich zu statischer Belastung entgegensetzen kann.Eine Methode für die Untersuchung von hohen Dehnraten ist der Split-Hopkinson-Bar. Hierbei wird der Durchgang einer Druck- oder Zugwelle durch den Betonprobekörper untersucht. Der Betonprobekörper befindet sich in einer geraden Achse direkt zwischen zwei langen Übertragungsstäben. Auf das eine Ende des Übertragungsstabes wird ein Druckimpuls aufgebracht, der sich dann als Druckwelle zunächst durch den Übertragungsstab, durch den Betonprobekörper und schließlich durch den zweiten Übertragungsstab fortsetzt. Durch Messung der durchlaufenden Welle vor und nach dem Probekörper können Rückschlüsse darüber gezogen werden, wie sich die Welle innerhalb des Probekörpers verändert hat. Um hohe Dehnraten messen und analysieren zu können, werden hohe Anforderungen an die messtechnische Signalerfassung gestellt. So muss eine Abtastrate von mindestens 500.000 Messungen pro Sekunde gewährleistet werden.
In einer weiteren Phase des Forschungsvorhabens soll der Split-Hopkinson-Bar auf zwei Dimensionen erweitert werden, um das Betonverhalten unter mehraxialer dynamischer Beanspruchung zu untersuchen. Anders als beim eindimensionalen Fall befindet sich der Betonkörper hier in zwei Achsen zwischen insgesamt vier Übertragungsstäben. Eine außerordentliche Herausforderung dieser Versuchsanordnung besteht darin, dass insbesondere die Impulsauslösung in den Übertragungsstäben beider Achsen synchron erfolgen muss, damit die beiden Druckwellen gleichzeitig und in gleicher Phase auf den Betonkörper auftreffen.
Ein weiteres Ziel des Forschungsprojektes ist es, die aus den experimentellen Untersuchungen am Split-Hopkinson-Bar gewonnenen Erkenntnisse in ein mehraxiales Materialmodell einfließen zu lassen.
Bericht aus dem Jahrbuch 2012
Schnell und laut
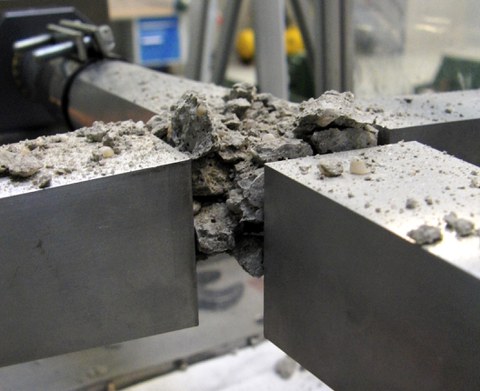
Zerstörte Betonprobe nach einem Versuch im zweiaxialen Split-Hopkinson-Bar
Man sieht nicht viel, man hört es nur – so ungefähr kann man sich einen Versuch am Split-Hopkinson-Bar vorstellen. Ein kurzer, lauter Knall und ein 80 mm langer Betonzylinder zerspringt in tausend Bruchstücke. Das ist beeindruckend, aber es stellt sich die Frage: Wozu das Ganze?
In diesem Versuchsstand sollen Materialeigenschaften unter sehr hohen Belastungsgeschwindigkeiten, wie sie z. B. bei einem Fahrzeuganprall auftreten, erforscht werden. Am Institut für Massivbau steht seit zwei Jahren ein klassischer einaxialer Split-Hopkinson-Bar für dynamische Druck- und Zugversuche an Betonproben zur Verfügung. Außerdem wird der weltweit erste biaxiale Split-Hopkinson-Bar entwickelt. Ziel ist es hierbei, die Betonprobe aus zwei Richtungen gleichzeitig stoßartig zu beanspruchen. Was anfangs recht einfach klingt, entpuppt sich bei genauerer Untersuchung als ein sehr diffiziles Unterfangen, da die beiden Druckimpulse bis auf wenige Mikrosekunden genau synchronisiert werden müssen, um von einer wirklich zweiaxialen Belastung der Probe ausgehen zu können. Herkömmliche Belastungs- und Auslösetechniken wie Federschusskanonen, Pendelhämmer, berstende Membranen oder Explosionen bieten keine ausreichend präzise Auslösung. Deshalb wurden zur Beschleunigung der Impaktoren Gasdruckkanonen gewählt.
Zur Überwachung aller relevanten Systemparameter ist der Versuchsstand mit vier Halbleiter-Dehnmessstreifen, vier Drucksensoren und zwei Lichtschranken ausgestattet. Die Steuerung der Auslösezeitpunkte übernimmt mikrosekundengenau ein computergesteuerter Mikrocontroller. Durch diesen können die konstanten Zeitunterschiede von drei Millisekunden zwischen den beiden Beschleunigungsanlagen ausgeglichen werden. Die Abhängigkeit der Zeitverzögerungen vom Befülldruck muss hierbei berücksichtigt werden. Weitere Schwankungen und Ungenauigkeiten in der Synchronität konnten durch die Verkürzung der Pneumatikwege, die exakte Positionierung der Impaktoren in den Gasdruckbeschleunigern und das Einschießen der Anlage über mehrere hundert Versuche minimiert werden. So ist es mittlerweile mehrfach gelungen, bis auf zehn Mikrosekunden genaue Belastungsimpulse in beiden Achsen zu erzeugen. Die weitere Optimierung wird uns auch in Zukunft noch beschäftigen.
Bericht aus dem Jahrbuch 2011
Kurzzeitdynamisches Verhalten von Beton
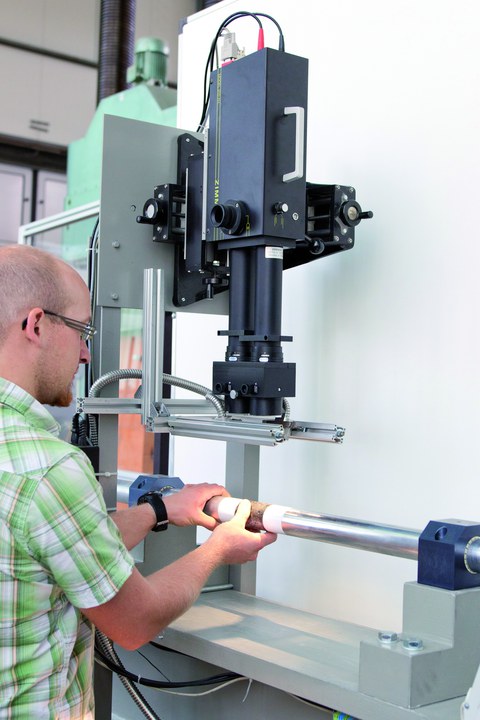
Vorbereiten des Versuchs
Das Prinzip des Split-Hopkinson-Bar (SHB) wurde bereits 1949 zur dynamischen Materialuntersuchung entwickelt. Heute ist dieses Versuchsprinzip eine etablierte Methode, um das Verhalten eines Materials unter hohen Belastungsgeschwindigkeiten (Impakt) zu charakterisieren. Der klassische Versuchsaufbau besteht aus einer Beschleunigungseinrichtung, die einen Impaktor auf die gewünschte Geschwindigkeit beschleunigt sowie zwei langen, in der Regel zylindrischen Stäben, zwischen denen die Probe eingeklemmt wird. Durch den Stoß des Impaktors auf den ersten Stab wird eine Druckwelle induziert, die den ersten Stab, die Probe und den zweiten Stab durchläuft. Damit kann ein Probekörper einaxial mit sehr hohen Dehnraten belastet werden, die z. B. einem Fahrzeuganprall, Flugzeugabsturz oder Steinschlag entsprechen.
Bisherige Forschungen zum geschwindigkeitsabhängigen Verhalten verschiedenster Materialien haben ergeben, dass die Festigkeit der Werkstoffe für Druck- und Zugbelastung mit steigender Verzerrungsrate zunimmt. Für Beton fällt die Steigerung der Zugfestigkeit mit Faktor sechs bis acht deutlich größer aus als für die Druckfestigkeit, die sich nur auf das Zwei- bis Dreifache erhöhen lässt. Weiterhin ist bekannt, dass sich die Betonfestigkeit unter mehraxialer Druckbelastung erhöht.
Nun stellt sich die Frage: Können sich diese beiden Effekte überlagern, so dass Beton unter mehraxialer hochdynamischer Belastung noch höhere Belastungen ertragen kann als unter statischen Bedingungen? Der Beantwortung dieser Frage widmet sich ein aktuelles Forschungsprojekt. Hierfür sollen würfelförmige Probekörper in zwei Richtungen gleichzeitig durch einen Impakt belastet werden. Da Impaktvorgänge innerhalb sehr kurzer Zeiten von meist nur wenigen Millisekunden ablaufen, ist die größte Herausforderung für die geplanten Versuche die exakte Synchronisierung der Belastungen aus zwei Richtungen. Erreicht werden soll diese Präzision durch zwei Gasdruckkanonen, die die Impaktoren mit Hilfe von Druckluft beschleunigen. Die Drucklufteinspeisung und die Auslösung der Gasdruckkanonen werden computergestützt durch Mikrocontroller gesteuert.
Das Spannungs-Dehnungs-Verhalten der Betonprobe wird indirekt über die Dehnungen in den Stäben ermittelt. Dafür werden auf alle Stäbe, jeweils in der Mitte, Halbleiter-DMS appliziert, die mit sehr großen Abtastraten ausgelesen werden können. Zusätzlich können die Verschiebungen der Probekörperränder berührungslos mit einem Hochgeschwindigkeitsextensometer erfasst werden.
Bericht aus dem Jahrbuch 2010
Betonverhalten unter Impakt
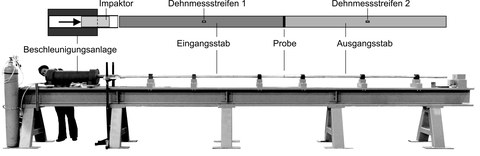
Versuchsaufbau des Split-Hopkinson-Bars
Unter welchen Bedingungen ändern sich die Festigkeitseigenschaften von Werkstoffen?
In dem Forschungsprojekt wird untersucht, welchen Einfluss die Geschwindigkeit einer Belastung auf die Festigkeit von Beton hat. Um diesen Aspekt analysieren zu können, wird ein Split-Hopkinson-Bar genutzt. Der Versuchsaufbau setzt sich aus einer Beschleunigungsanlage für einen Impaktor und zwei langen Aluminiumstäben zusammen, zwischen denen die Probe montiert wird. Der zylinderförmige Impaktor wird in der Beschleunigungsanlage beschleunigt und stößt auf den ersten Aluminiumstab gleichen Durchmessers. Dadurch wird eine Kompressionswelle in dem Aluminiumstab ausgelöst. Diese Welle bewegt sich mit Körperschallgeschwindigkeit durch den Eingangsstab, die Probe und den zweiten Aluminiumstab fort. Wie bei einer Black Box wird über die eingehenden, die reflektierten und die ausgehenden Messergebnisse ein Rückschluss auf die Eigenschaften der Probe während des Versuches gezogen. Die Aluminiumstäbe verhalten sich während des Versuches elastisch, währenddessen die Probe i. d. R. plastisch belastet wird.
Bisher bekannte Untersuchungen beschäftigen sich mit dem Einfluss von Belastungen, die einaxial mit hohen Geschwindigkeiten eingeleitet wurden. Im Rahmen dieses Forschungsvorhabens soll speziell die Auswirkung einer zweiaxialen Belastung einer Probe untersucht werden. Zu diesem Zweck wurde im vergangenen Jahr ein Versuchsanlagenkonzept entwickelt, welches es ermöglichen soll, die Belastung der Probe aus zwei Richtungen überwachen und auch synchronisieren zu können.
Unterschiedliche Belastungs- und Auslösungskonzepte wurden dafür verglichen und auf ihre Umsetzbarkeit hin überprüft. Basierend auf diesen Analysen wurde Druckluft als geeignetes Treibmittel für den Impaktor ausgewählt. Die Versuchssteuerung findet über eine pneumatische Schaltung statt. Halbleiter- und Lasermesstechnik mit Abtastraten im MHz-Bereich ermöglichen es, solche schnellen Impulsvorgänge sicher messen und analysieren zu können.
Dieses Konzept konnte bereits bei einem klassischen einaxialen Split-Hopkinson-Bar getestet werden. Nach den entsprechenden Anpassungen für den zweiaxialen Versuchsaufbau wird nun der zweiaxiale Versuchsstand aufgebaut.
Bericht aus dem Jahrbuch 2009
Beton bei dynamischer Beanspruchung
Beton kann in unterschiedlichsten Situationen stoßartiger oder wechselnder Beanspruchung unterliegen. Beispielsweise können Fels- und Gesteinsbrocken auf Betonstraßen herabstürzen, es kann in Unfallsituationen zu Fahrzeuganprall auf Betonkonstruktionen kommen, oder Tragkonstruktionen von Fabrik- und Fertigungshallen können dynamischer Belastung infolge schlag- und stoßartiger Maschinenprozesse ausgesetzt sein. Bei solchen Beanspruchungen unterliegt der Beton hohen Dehnraten, das bedeutet, dass sich die Dehnungswerte im Beton sehr schnell ändern.
Ziel des Projektes ist es, das Verhalten von Beton unter hohen Belastungsgeschwindigkeiten zu erforschen. Von besonderem Interesse ist dabei die Festigkeitssteigerung von Beton, das heißt, welchen Widerstand Beton dynamischer Belastung im Vergleich zu statischer Belastung entgegensetzen kann.
Eine Methode für die Untersuchung von hohen Dehnraten ist der Split-Hopkinson-Bar. Hierbei wird der Durchgang einer Druck- oder Zugwelle durch den Betonprobekörper untersucht. Der Betonprobekörper befindet sich in einer geraden Achse direkt zwischen zwei langen Übertragungsstäben. Auf das eine Ende des Übertragungsstabes wird ein Druckimpuls aufgebracht, der sich dann als Druckwelle zunächst durch den Übertragungsstab, durch den Betonprobekörper und schließlich durch den zweiten Übertragungsstab fortsetzt. Durch Messung der durchlaufenden Welle vor und nach dem Probekörper können Rückschlüsse darüber gezogen werden, wie sich die Welle innerhalb des Probekörpers verändert hat. Um hohe Dehnraten messen und analysieren zu können, werden hohe Anforderungen an die messtechnische Signalerfassung gestellt. So muss eine Abtastrate von mindestens 500.000 Messungen pro Sekunde gewährleistet werden.
In einer weiteren Phase des Forschungsvorhabens soll der Split-Hopkinson-Bar auf zwei Dimensionen erweitert werden, um das Betonverhalten unter mehraxialer dynamischer Beanspruchung zu untersuchen. Anders als beim eindimensionalen Fall befindet sich der Betonkörper hier in zwei Achsen zwischen insgesamt vier Übertragungsstäben. Eine außerordentliche Herausforderung dieser Versuchsanordnung besteht darin, dass insbesondere die Impulsauslösung in den Übertragungsstäben beider Achsen synchron erfolgen muss, damit die beiden Druckwellen gleichzeitig und in gleicher Phase auf den Betonkörper auftreffen.
Ein weiteres Ziel des Forschungsprojektes ist es, die aus den experimentellen Untersuchungen am Split-Hopkinson-Bar gewonnenen Erkenntnisse in ein mehraxiales Materialmodell einfließen zu lassen.