DEM-Simulation von Impaktvorgängen (GRS)
Inhaltsverzeichnis
Projektdaten
Titel | Title DEM-Simulation von Impaktvorgängen | DEM-Simulation of Impact Processes Förderer | Funding Bundesministerium für Wirtschaft und Technologie (BMWi) Zeitraum | Period 10/2010 – 09/2013 Leiter | Project Manager Prof. Dr.-Ing. Dr.-Ing. E.h. Manfred Curbach Bearbeiter | Contributor Dipl.-Ing. Birgit Beckmann |
Kurzbeschreibung
Ziel des Forschungsvorhabens ist es, das Verständnis von Bruchvorgängen, Schädigungsprozessen und Wellenausbreitung im Beton infolge Impaktbelastung zu vertiefen. Dazu soll das Betonverhalten unter Impaktbelastung, das heißt unter hochdynamischer Belastung und den damit verbundenen hohen Dehnraten, in einer numerischen Simulation nach der Diskrete Elemente Methode untersucht werden. In der Simulation sollen die Ausbreitung von Druckwellen studiert und dabei die Entstehung von Mikrorissen und Gefügeänderungen sowie die Auswirkungen von Defekten in der Struktur der Materialien auf deren Belastbarkeit untersucht werden. Dabei ist eine enge Verknüpfung aus numerischer Simulation und experimentellen Untersuchungen erforderlich. So sollen die kürzlich am Institut für Massivbau durchgeführten Impaktversuche an Betonplatten ebenso in die Simulation einfließen wie die geplanten Versuche am Split-Hopkinson-Bar.
Bericht aus dem Jahrbuch 2013
DEM-Simulation von Betonbruch
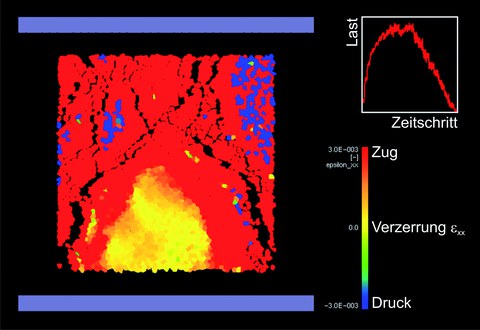
Verzerrung bei vollstandigem Versagen
Ziel dieses Forschungsvorhabens ist es, das Versagens- und Bruchverhalten von Beton zu untersuchen. Dabei geht es weniger um die Untersuchung des Materialverhaltens im elastischen oder sicher tragfähigen Bereich, sondern es geht gezielt um die Untersuchung des Bruchverhaltens und die dem globalen Bruch vorausgehende und fortschreitende Rissentwicklung. In einer am Institut entwickelten numerischen Simulation wird ein 10 cm großer Betonprobekörper unter vertikaler Druckbeanspruchung bis zum vollständigen Versagen belastet.
In der Simulation werden auf Grundlage der Diskrete-Elemente-Methode (DEM) die Kräfte und Verschiebungen im Betonkörper infolge äußerer Belastung berechnet. Um den Vergleich mit Ingenieurgrößen zu ermöglichen, können aus den bekannten Systemvariablen makroskopische Größen wie Spannungen und Verzerrungen ermittelt werden. Hierzu werden Verfahren der Durchschnitts- beziehungsweise Mittelwertbildung eingesetzt.
Die Spannungen und Verzerrungen sind Nachverarbeitungsgrößen und haben entsprechend keinen Einfluss auf den weiteren Simulationsverlauf. Spannungen und Verzerrungen sind konzeptionell kontinuumsmechanische Größen. Das bedeutet, dass die Spannungen und Verzerrungen verschmiert und in einem bestimmten, wählbaren Einflussbereich als konstant angenommen werden. Und es bedeutet weiterhin, dass die Ermittlung von Spannungen und Verzerrungen stetige Felder – das heißt also einen kontinuierlichen Körper − voraussetzt. Die beiden Bilder zeigen exemplarische Ergebnisse des Projektes. Im linken Bild ist die Dehnung eines Probewürfels in horizontaler Richtung zu Belastungsbeginn und noch vor Erreichen der Maximallast zu sehen. Man erkennt, dass in den rot dargestellten Bereichen höhere Zugdehnungen auftreten als in den gelb (neutral) dargestellten. Auf diese Weise können solche Gebiete, in denen später ein Riss entstehen wird, erkannt werden, bevor die makroskopisch sichtbare Rissbildung einsetzt. Das rechte Bild zeigt die horizontale Dehnung beim vollständigen Versagen. An diesem Bild ist vor allem erkennbar, dass die Ermittlung der Verzerrungen (und Spannungen) zwar formal durchführbar, aber nur eingeschränkt aussagekräftig sind, da der Betonkörper durch die fortschreitende Rissbildung und die starke Schädigung nicht mehr als kontinuierlicher Körper betrachtet werden kann und daher die erforderlichen Voraussetzungen stetiger Felder nicht gegeben sind. Aussagen zu Verzerrungen sind also lediglich im Anfangsstadium der Belastung am ungeschädigten Probekörper sinnvoll.
Bericht aus dem Jahrbuch 2012
DEM-Simulation von Phänomenen beim Betonbruch
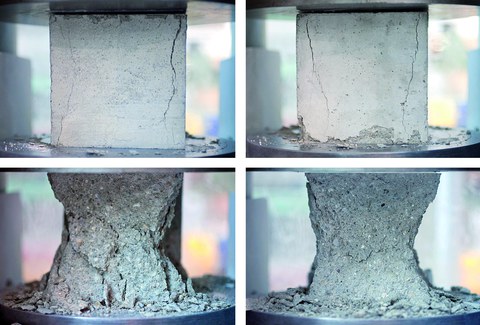
Druckversuche im Laborexperiment
Im Fokus dieses Forschungsvorhabens stehen Bruchvorgänge im Beton. Dabei geht es nicht darum, eine bestimmte Maximallast zu erzielen oder das Verhalten im sicher tragfähigen Lastbereich zu untersuchen, sondern es sollen gezielt Bruchvorgänge und Versagensmechanismen untersucht werden. Warum entsteht ein Riss genau an dieser oder jener Position? Wie stark weichen die Risspositionen von Versuch zu Versuch ab? Kann man schon im Vorfeld z. B. an Mikrorissen erkennen, wo später ein globaler Riss entstehen wird? Solchen Fragen soll in diesem Forschungsprojekt nachgegangen werden.
In realen einaxialen Druckversuchen werden geringfügig variierende Maximallasten erzielt. Diese liegen im Bereich derselben Größenordnung, sind aber von Versuch zu Versuch nie exakt gleich. Die Bruchbilder zweier Versuche zeigen ein einander ähnelndes, typisches Bruchbild; aber auch sie sind nie exakt dieselben, sondern unterscheiden sich in Art und Lage der tatsächlichen Risse.
Solche realen Laborversuche werden in diesem Forschungsprojekt in einer zweidimensionalen numerischen Simulation auf Basis der Diskrete-Elemente-Methode (DEM) abgebildet. Dabei wird der Betonkörper als Ensemble einzelner Partikel diskretisiert. Anders als bei kontinuumsbasierten Methoden sind hier die einzelnen Partikel kinematisch unabhängig, können sich aufeinander zu- und voneinander wegbewegen. Aus der gedachten Überlappung zweier Partikel wird eine Rückstoßkraft berechnet, so dass, wenn dies für alle Partikel über den gesamten Betonkörper hinweg getan wird, der Kraftfluss von der Lasteinleitungsplatte durch den Betonkörper hindurch auf die Auflagerplatte sichtbar wird. Bewegen sich zwei Partikel voneinander weg, so entsteht – quasi automatisch – ein Riss. Risse werden also nicht durch spezielle Risselemente oder zusätzliche Rissweitenparameter der Simulation hinzugefügt, sondern sie entstehen allein dadurch, dass sich Partikel voneinander lösen.
Durch eine bei der Partikelgenerierung integrierte Zufallsfunktion entstehen jedes Mal ähnliche, aber geringfügig abweichende Partikelensemble. Dies ist mit der Herstellung im Labor vergleichbar, z. B. bei mehreren Betonproben aus derselben Charge, denn weder im Labor noch in der Simulation ist beispielsweise die Lage von Zuschlagskörnern und Zementstein zweimal exakt gleich. Wird der Druckversuch mit virtuellen Probekörpern simuliert, so ergeben sich – genau wie im realen Laborexperiment – ähnliche, doch nie exakt gleiche Bruchbilder.
Bericht aus dem Jahrbuch 2011
2D-DEM-Simulation des Betonbruchs
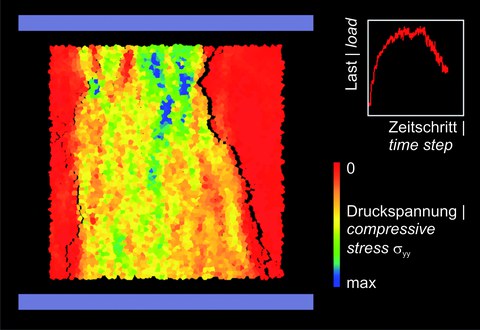
Druckspannungsverteilung im Betonprobekörper im Nachbruchbereich
Ziel des Forschungsvorhabens ist es, Bruchphänomene von Beton insbesondere unter hohen Belastungsgeschwindigkeiten zu erforschen und Rissmuster, die während beziehungsweise im Vorfeld des Betonversagens entstehen, numerisch zu simulieren. Dabei werden Betonprobekörper abgebildet, wie sie auch im realen Laborexperiment vorkommen. Ein Schwerpunkt der Betrachtung liegt dabei auf Impaktbelastungen, wie sie etwa bei Steinschlag oder Fahrzeuganprall auftreten.
Mit einem am Institut für Massivbau entwickelten Programmcode wird das Betonverhalten mit der Diskrete-Elemente-Methode (DEM) simuliert. Dabei wird der Betonkörper in einzelne – diskrete – Elemente unterteilt. Aus kinematischer Sicht kann jedes der Elemente seine eigene Starrkörperbewegung durchführen. Über virtuelle Belastungsplatten wird die äußere Belastung auf den Betonkörper aufgebracht. Zwischen den Betonelementen werden Kontaktkräfte übertragen, die im nächsten Berechnungsschritt die Position und Bewegung eines Elements beeinflussen. Auf diese Weise kann mit einem Ensemble zahlreicher einzelner Partikel das Verhalten eines Betonprobekörpers simuliert werden. Ein großer Vorteil dieser Methode ist es, dass Risse prinzipiell überall entstehen können. Im Vergleich zu kontinuumsbasierten Simulationsmethoden werden Risse hier nicht durch spezielle, an potentiell gefährdeten Stellen dem Modell hinzugefügte Risselemente repräsentiert, sondern die Risse gehen während der Simulation quasi automatisch aus dem Berechnungsmodell und der jeweiligen Belastungssituation hervor. Die entstehenden Rissmuster von äußerlich gleichen, aber durch verschiedene Ensembles simulierten Betonkörpern enthalten – genau wie im realen Laborexperiment – jeweils geringfügige Unterschiede und spiegeln somit den statistischen Charakter der Bruchvorgänge von Betonkörpern wider.
In einem der eigentlichen Simulationsrechnung nachgelagerten Postprocessing-Algorithmus können aus den an jedem Element wirkenden Kräften Spannungen ermittelt werden, um somit einen Vergleich mit Ingenieurgrößen zu ermöglichen.
Die Graphiken zeigen die Spannungsverteilung kurz nach Erreichen der Maximallast beziehungsweise im Nachbruchverhalten, wobei nach dem Bruch größere Rissöffnungen zu verzeichnen sind. In rot dargestellten Elementen wird kaum bzw. keine Druckspannung mehr übertragen, so dass die späteren Abplatzungen des Betonkörpers schon zu erkennen sind, wenn die Risse noch haarfein sind.
Bericht aus dem Jahrbuch 2010
DEM-Simulation von Impaktvorgängen
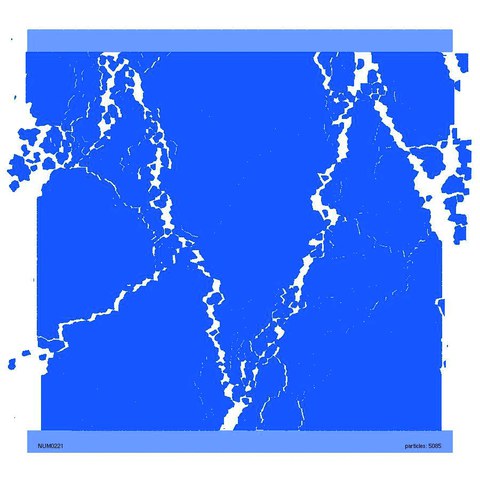
Rissmuster nach dem simulierten Versagen eines Betonwürfels
Ziel des Forschungsvorhabens ist es, das Verständnis von Bruchvorgängen, Schädigungsprozessen und Wellenausbreitung im Beton infolge Impaktbelastung zu vertiefen. Dazu soll Beton unter hochdynamischer Belastung und den damit verbundenen hohen Dehnraten mit der Diskrete Elemente Methode (DEM) numerisch simuliert werden. In der Simulation sollen die Ausbreitung von Druckwellen und die Entstehung von Mikrorissen und Gefügeänderungen untersucht werden. Dabei ist eine enge Verknüpfung aus numerischer Simulation und experimentellen Untersuchungen erforderlich.
Warum Untersuchung von Impaktvorgängen? Die Untersuchung von Impaktvorgängen ist von grundsätzlichem Interesse. Zum einen sind Unfallsituationen wie Steinschlag, Fahrzeuganprall oder Flugzeugabsturz und die damit verbundenen hohen dynamischen Beanspruchungen nicht vermeidbar. Daher dient die Erforschung von Impaktbelastungen dem Schutz von Bauwerken, besonders von solchen, die wie Krankenhäuser oder Kernkraftwerke einer erhöhten Tragsicherheit bedürfen. Dies gilt umso mehr, da ein durch Impaktbeanspruchung verursachtes Versagen zumeist ohne Vorankündigung geschieht. Zum anderen besteht aber auch ein Interesse, die theoretischen Grundlagen der sehr komplexen Vorgänge von Bruch-, Rissbildungs- und Schädigungsprozessen im Beton bei Impakt zu verstehen. Die dabei im Betongefüge entstehenden Risse müssen nicht zwangsläufig zum Versagen führen, jedoch bedingen sie erheblich geänderte Materialeigenschaften.
Warum numerische Simulation? Auch wenn Simulationen einen virtuellen Raum darstellen und daher reale Experimente nicht ersetzen können, so erlauben sie die Untersuchung von Vorgängen, die beispielsweise infolge hoher Temperaturen, hoher Drücke oder Explosionsgefahr schwer experimentell umzusetzen sind. Darüber hinaus sind räumliche und zeitliche Größen in einer Simulation quasi beliebig skalierbar, unabhängig davon, ob der reale Vorgang wenige Sekunden oder mehrere Monate dauert. Zudem können Einflussgrößen einzeln und unabhängig von einander variiert werden. Eine Computersimulation stellt eine Verbindung zwischen Laborexperiment und der mathematisch-physikalischen Theorie dar. Die Interaktion von zwei Partikeln – z. B. von zwei Festkörpern oder zwei Molekülen – ist analytisch beschreibbar. Aber schon ein Drei-Partikel-System bereitet große analytische Schwierigkeiten. Daher sind Computersimulationen ein geeignetes Hilfsmittel, solche Problemstellungen zu behandeln.