Bond between concrete and steel under high loading rates
Table of contents
Project data
Titel | Title Verbund zwischen Beton und Bewehrungsstahl bei hohen Belastungsgeschwindigkeiten | Bond between concrete and steel under high loading rates Förderer | Funding Bundesministerium für Umwelt, Naturschutz, nukleare Sicherheit und Verbraucherschutz (BMUV) Zeitraum | Period 10/2014 – 12/2017 (Phase 1), 05/2018 – 04/2022 (Phase 2) Leiter | Project manager Prof. Dr.-Ing. Dr.-Ing. E.h. Manfred Curbach Team | Team M.Eng. Petr Máca Ph.D, Dipl.-Ing. Lena Leicht Dr.-Ing. Evmorfia Panteki (Phase 1) |
Supported by: Federal Ministry for the Environment, Nature Conservation, Nuclear Safety and Consumer Protection based on a decision by the German Bundestag under project No. 1501566.
Report in the year book 2022
Tension at the end

A spallation specimen after the test
Spallation experiments are carried out to determine the dynamic tensile strength of different materials. The experiments involve generating a compressive stress wave using a split Hopkinson pressure bar (SHPB) that travels through the specimen. However, by contrast to regular SHPB experiments, no output bar is located at the end of the specimen. Instead, the reflection of the compressive wave returns as a tensile wave from the free end of the specimen. On the one hand, preventing premature damage to the specimen due to the compressive wave is essential. On the other hand, the amplitude of the reflected tensile wave must be high enough to lead to the tensile failure of the sample.
Using spallation experiments for testing, the bond between concrete and a reinforcement bar under dynamic loading conditions is also possible. After the casting, the specimens were notched. The notch separated the specimen into two segments connected only by the reinforcement bar that was embedded entirely in the first segment. The bond length was only twice the rebar’s diameter in the second segment. This resulted in a bond failure that occurred in the second segment. To be able to transfer the compressive wave, steel washers filled the notch. The returning tensile wave then loaded the bond zone. Two high-speed cameras and an optical extensometer recorded the displacements and the bond failure.
To investigate possible experimental configurations, we used a numerical model with a pre-defined bond law and validated the evaluation procedure of the experimental data based on the displacements obtained at the same positions as in the experiment. We showed that the acceleration of the second segment could be used to calculate the pull-back force that corresponds to the bond force. The opening of the notch corresponds to the slip of the bar. Finally, we used a detailed numerical model to visualize the crack patterns and provide insights into the development of local stresses. Overall, this project contributes to understanding dynamic material properties and the bond between concrete and reinforcement bars under dynamic loading conditions.
Report in the year book 2021
A good match
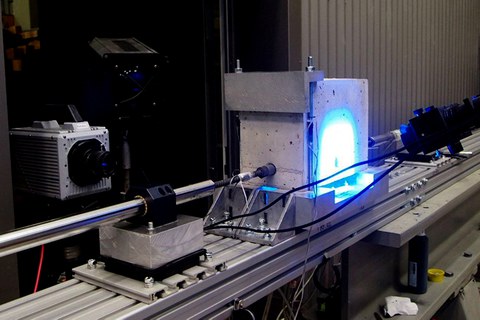
Beam-end specimen in the split-Hopkinson bar
A wide variety of specimen types exists for testing the bond between reinforcement bars and concrete. The aim of the final phase of this project is to investigate a large number of specimens under high loading rate conditions and to identify the dynamic characteristics of the bond between reinforcing steel and concrete.
For this purpose, on the one hand, pull-out, double-pull-out, beam-end and spallation specimens were produced and tested. One goal of the tests is aimed at obtaining a bond stress-slip relationship. This is a characteristic curve relating the pull-out force of the rebar to simultaneously occurring displacement (slip). The tests were performed with a loading velocity between 1 m/s and 7 m/s and with different impactor lenghts in the split Hopkinson bar testing facility. Since different failure mechanisms occur in different types of specimens, they are not directly comparable. On the pull-out and double-pull-out test specimens, splitting crack formation was observed. It was shown that the bond-free length, which was present in the beam-end specimens, can effectively prevent the splitting-crack-induced failure. On the other hand, specimens with transversely embedded reinforcing steel as well as tension bars were manufactured and analysed. Tensile tests with transverse steel were used to investigate the adhesive bond in the transverse direction. The tensile bars were used to investigate the crack pattern and the amount of energy that can be absorbed in the individual cracks over the existing bond length.
In the numerical part of the project, models of the above-mentioned specimens were created in LS-Dyna to describe phenomena that cannot be measured experimentally. In particular, the beam-end test was recalculated in detail and showed good agreement with experimental results. The ribs were explicitly modelled with hexahedral elements. The force transfer was realized by interlocking the concrete keys and ribs by defining a frictional contact between the rebar and the concrete. The resulting bond stress-slip relationship is thus only dependent on the concrete material model.
Report in the year book 2020
Tightly bonded
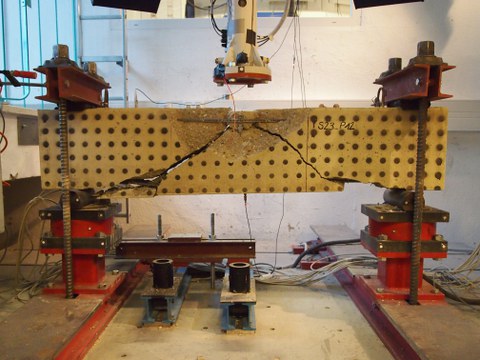
Beam without stirrups, tested with a pressure of 0.8 bar
The second series of impact tests on beams has helped to analyze in-depth the effect on the strain distribution along beams. The tests are carried out in the drop tower of the Otto-Mohr-laboratory with steel impactors with a diameter of 100 mm. The impactors are accelerated to variable velocities by compressed air. Twelve beams were tested in the drop tower, but only with three subseries tested at four different impactor velocities. In one subseries, the beams were stirrup-reinforced in another subseries bond breakers were used. The goal was to place the bond breakers at the position where high plastic strains are expected. The strains measured in the centre of the beam where the bending cracks occurs were in some cases a lot higher within the bond free zone than the strains measured in the bonded area. The measurements in the bonded and unbonded third points where the inclined punching cone cracks are located hardly differed. The impactor velocity was varied within the different subseries. The maximum loading velocity of the stirrup-reinforced beams was higher than in the other two series as these beams can withstand impact better. The bond stresses between the measurements were calculated with the help of discrete strain values divided by the bond length between the measurement points.The results from the drop tower beam experiments helped to find new specimen types for small-scale tests in the split Hopkinson bar and especially allow for the definition of realistic bond stresses and maximum strains that need to be tested on small scale.
Bericht aus dem Jahrbuch 2019
Big impact
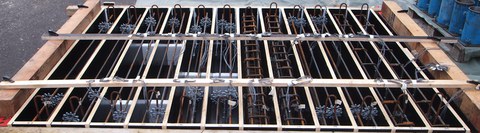
Reinforcement of the beams in the formwork
A hissing noise accompanied the impactor sliding through a steel pipe with a velocity of over 60 km/h. Different beams made of reinforced concrete were placed at the end of the pipe. None of them survived. But that is fine because the task was to destroy the concrete. After all, we want to understand the damage mechanisms of such beams to ensure higher safety of structures. In the project, we focuse on the bond between concrete and steel. During the experimental programme the effects of stirrups spacing, as well as the effects of the reduction of the bond zone length, on the maximum steel strains were investigated. Some specimens were notched in the middle, as well as at the positions where the punching cone typically penetrates the beam’s underside. In addition to reaction forces, beam deflection and acceleration, and the strains on the longitudinal ribs of the reinforcement were measured to calculate the bond stress. Preliminary pull-out tests proved that the embedded strain gauges do not significantly affect the bond behaviour. To get a deeper insight into the experimental set-up, different tests were modelled numerically. This allowed to exactly analyse the strains and damage within the beams, and it served as a good foundation to evaluate bond in structural members.
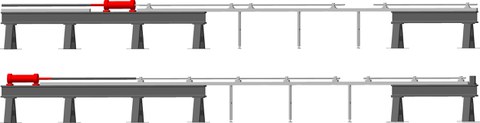
Split Hopkinson bar configurations: tensile (top) and compressive (bottom) configuration
To be able to investigate the bond on the local level, the existing split Hopkinson pressure bar was extended. In the new configurations, it will be possible to measure compressive as well as tensile waves with a length of up to 5 m. The longer stress wave causes larger deformation of the specimen, and in this particular case, it increases the slip between concrete and reinforcement steel. Two tensile configurations will be possible, one with bars made of aluminium for testing concrete under dynamic tension, and another which enables the load introduction directly into the reinforcement bars. Thanks to these new configurations, it will be possible to develop new specimens that are designed to separately study various stress states which are found in structural beams. Finite element modelling was used to optimise these new specimens and to design the measuring concept.
Bericht aus dem Jahrbuch 2018
Bond under impact – the story continues
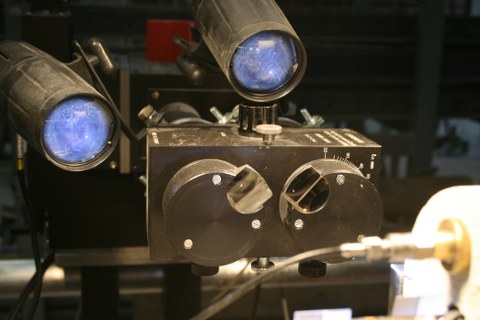
Optisches Extensometer für Schlupf- oder Rissöffnungsmessungen
In the first phase of the project, the localised bond stress-slip relationship between concrete and steel under impact loading was studied. Experimental as well as numerical investigations were carried out on cylindrical and cubical specimens with short bond lengths. In the current, second phase of the project, a more general view on the bond is being pursued. The main aim of the project is to develop a new type of bond test that will be tailored to investigate bond properties under impact loading.
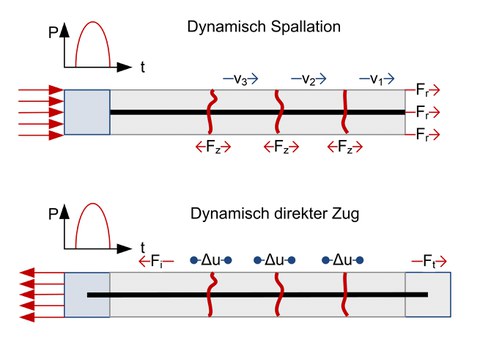
Mögliche Konfiguration von dynamischen Verbundspallations- versuchen
The idea is to use the spallation effect which occurs when a compressive wave travels throughout a brittle specimen, and it is reflected from the free end as a tensile wave that travels in the opposite direction. This stress reversal produces tension in the specimen which causes its failure. To achieve dynamic equilibrium in the sample and to create a long loading pulse, a new split Hopkinson bar will be developed. The length of the incident and transmission bars will be up to 20 m and the length of the impactor will be 10 m. Impactor of such length induces a loading pulse with a length of 20 m that causes much larger movement of the incident bar, allowing for testing of ductile materials or composites where deformation values of more than 5 mm are needed to capture the post-peak failure behaviour.
Another possible type of test considered in this project is based on a beam specimen with fully bonded reinforcement and a predefined cut or window in the middle of the span. Inside of the cut, strain gauges will be attached directly on the steel reinforcement. The idea is to measure realistic bond strain rates that are induced in a beam loaded by the impact.
In addition, numerical investigations in which reinforcement is modelled as beam elements are carried out. These simulations help in designing the experiments and to decide a proper placement of the sensors. They also allow better insight into the stress state of the specimen, especially in the vicinity of the bond zone.
The presented project was funded by the German Federal Ministry of Economic Affairs and Energy (BMWi, project no. 1501566) on the basis of a decision by the German Bundestag.
Report in the year book 2017
Bond under impact
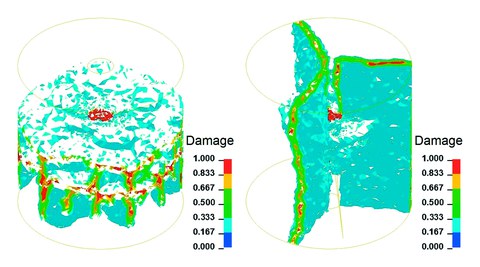
Modelling of damage for loading velocities of 50 mm/s (left) resp. 50,000 mm/s (right)
The overall performance of a composite material such as reinforced concrete is highly dependent on the bond properties between the concrete matrix and the steel reinforcement. When studying the bond behaviour, it is important to consider that it is not the result of a generic material property, but a combination of several factors such as the material properties of concrete and steel, the specific surface area of the steel reinforcement and the size and geometry of the specimen under investigation. Even though the bond characteristics have been studied for over more than 100 years, questions still arise. One of these questions regards the influence of loading rate on the bond properties.
Throughout the project, we studied the bond behaviour under loading rates varying between quasi-static and high dynamic. To achieve the required loading rates, conventional universal testing machines, as well as a drop tower and a split-Hopkinson bar, were used. For the analysis of the measured data, we used wave propagation theory in elastic solids. Steel bars with a diameter of 10 mm was predominantly used, but we were also able to show that the newly proposed testing method is suitable for larger reinforcement bar diameters of 16 mm.
The inertia effect was eliminated from the experimental results by considering the dynamic equilibrium. We concluded that higher loading rates increase the measured bond strength by up to 25%. The failure mode was characterized by shearing-off of the concrete lugs between the ribs. Throughout the experimental work, we did not observe any change in the failure mode.
We also compared pull-out and push-in loading modes and concluded that the push-in type of loading always produced higher bond strengths in comparison to the pull-out one. We used numerical modeling to predict bond behaviour under even higher loading rates. The numerical model didn’t contain any phenomenological dependence of material properties on the loading rate, and it was in good agreement with the experimental results.
Report in the year book 2016
Teamwork at its best – concrete and steel
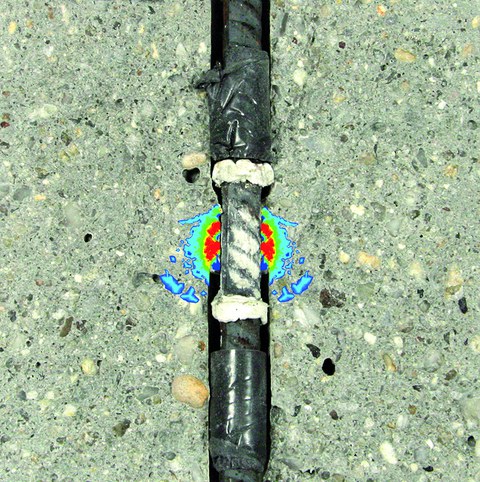
Numerical simulation of microcrack development
Imagine a two-member team: One member is very strong when it comes to tension but it’s rather expensive. The other one is very weak in tension but strong in compression and available in abundance. Yes, we are talking about steel and concrete. Together they form a perfect team: reinforced concrete! Due to the utilization of their respective strengths, the composite material is well known to be a very resource- and cost-efficient material. However, what is not well documented is the behaviour of reinforced concrete under high-stress levels such as those occurring during impact events.
In civil engineering, a structural member is ordinarily considered as a rigid body, and the fundamental equations of state can be solved before and after an impact event. In the current project, we are trying to describe what exactly happens during the impact event and how the force is transferred between the two components of reinforced concrete. Conventionally, bond stress-slip relationships are measured to describe such behaviour. The first challenge when it comes to impact loading is the sampling rate. It needs to be high enough to capture all the significant details. This applies to both the experimental and the numerical part of the project. Therefore, a sampling rate of 1 MHz was used during the tests. To measure the slip of the bar, we used an optical extensometer and a high-speed camera. To determine the correct bond stress, we compared the stress history before and after the bond zone. In addition, we used load cells located under the specimen and accelerometers attached to the upper surface of the concrete specimen. Throughout the project, conventional servo-hydraulic machines were used for testing low-velocity loading, an instrumented drop tower for intermediate loading rates and finally a split-Hopkinson bar for high loading rates. Each experimental set-up was also used as a pattern for simulation.
When it comes to the analysis of the data, special attention has to be paid to the wave propagation throughout the specimen and its various reflections since the improper design of the experiments may lead to misleading results. In addition, the dynamic force equilibrium needs to be checked at each time step. It is shown, that the inertia of the sample needs to be carefully considered when interpreting the results.
Report in the year book 2015
Bond design for impact
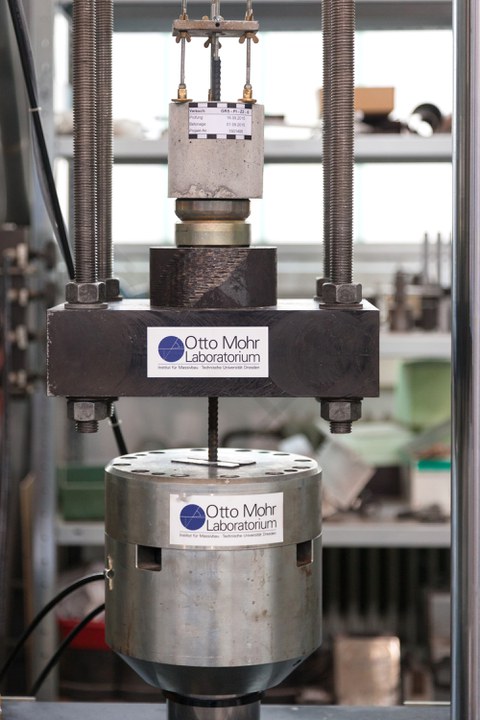
Experiment configuration for quasi-static pull-out test of small cylinders
The world is rapidly changing and new challenges are faced not only in structural design but also in addressing safety design issues. Since reinforced concrete is the most widely used structural material, it is often subjected to different kinds of impact loadings. In the modern world, a high security threat of terrorist attacks like plane crushes, contact explosions, projectile impacts and other types of hard impacts exists. These incidents have short durations, and thus the increase of material properties due to the so called strain rate effect can be utilized in the design for impact. Therefore, the goal of the current project is to show how this effect influences the bond behaviour of steel reinforcement in concrete under impact loading. In the quasi-static case, the bond is predominantly dependent on the compressive strength of concrete as well as the splitting tensile strength. This dependency may be shifted in the case of impact loading, as the tensile strength strain effect is higher than the compressive one.
In the on-going experiments, we compare the bond strength of a reinforcement bar and concrete under impact loading with that of the quasi static one. Two modes of loading are considered: pull-out and push-in tests. So far, the loading mode appeared to have a negligible influence during quasi static loading, whereas the difference under impact loading proved to be more significant. Here, the pull-out mode of testing revealed greater sensitivity to the loading rate compared with the push-in tests. It also showed that the strength of the bond between steel rebar and concrete increases up to 150 % already at intermediate loading rates corresponding to the impact speed of 1–2 m/s. To help determine the bond behaviour under high impact rates, tests in a split-Hopkinson bar are planned in the following year.
In addition, numerical simulations are carried out to calibrate the geometry of the specimen and the exact experimental setup. Furthermore, a detailed numerical model is being created for the simulation of the local bond behaviour. Calibrated using the global bond stress-slip relationships, it should allow a local insight into the structure which is impossible to record experimentally without disturbing the material.
Report in the year book 2014
Bond between concrete and reinforcing steel-bars under high loading rates
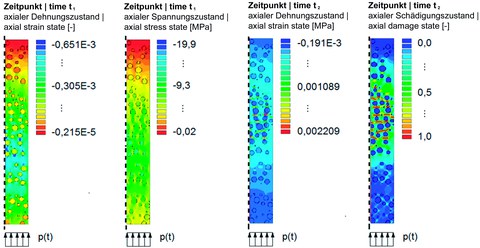
Simulation of a concrete specimen in a compression test in the split-Hopkinson bar
As numerous experiments under dynamic loading have shown, both concrete and steel exhibit strengths that surpass by far the static values. Taking advantage of this could make the future design concept for impact endangered structures even more economic. Before this happens, it must be ensured that the bond between concrete and steel can also withstand the corresponding loads.
The aim of this research project is to investigate this and explore the bond mechanisms in more depth. The project includes both a comprehensive experimental test program and a numerical part. With a time- and space-dependent modeling of the processes, the numeric part shall lead to a deeper understanding of the effects observed in the experiment.
The project builds upon previous work relating e.g. the bond behaviour or the behaviour of plain concrete in tests in the uniaxial split-Hopkinson bar. The focus of previous dynamic studies was on the so-called strain rate effect and specifically on the determination of the contribution of the material and the structural properties of concrete samples to the increase in strength. For this purpose, the simulations were based on purely static assumptions. The implemented constitutive law consistently had no dependencies on the strain rate and disregarded possible physical causes. Experimental models of the simulations were split-Hopkinson bar experiments at various loading rates and concrete mixtures. The evaluation of the numerical data according to the conventional method also resulted in strength values, which were partly somewhat higher than the assumed static values. It turned out, that the strong nonlinearity of the concrete constitutive law plays an important role, as it has a great influence over the longitudinal wave propagation. Visualizations depict clearly the influence of the nonlinearity since at the same time strains localize much stronger than stresses.
The current results offer reasons to hope for many still outstanding answers regarding the bond mechanisms. We also hope for new insights resulting from the soon to begin experimental investigations.