Structural behaviour by impacting containers (aircraft tanks)
Table of contents
- Project data
- Report in the annual report 2020
- Report in the annual report 2019, part I (experiment)
- Report in the annual report 2019, part II (Numerics)
- Report in the annual report 2018, part I
- Report in the annual report 2018, part II
- Report in the year book 2017, Part I
- Report in the year book 2017, Part II (numerical part)
- Report in the year book 2016
- Report in the year book 2015
- Report in the year book 2014
Project data
Titel | Title
Bauteilverhalten unter stoßartiger Beanspruchung durch aufprallende Behälter (Flugzeugtanks) | Structural behaviour under impact loading by the impacting container (aircraft tanks) |
The presented project was funded by the German Federal Ministry of Economic Affairs and Energy (BMWi, project no. 1501541) on basis of a decision by the German Bundestag.
Report in the annual report 2020
New scales at the Impact research
For many years impact loading is an important research topic at the Institute of Concrete Structures. In the frame of this research, among others, the behaviour of reinforced concrete plates subjected to dynamic loads is investigated and a steadily growing database of impact tests is generated. A large number of experiments with varying material- and testing parameters was carried out. To transfer the knowledge gained from the experimental test to the behaviour expected in real buildings, additional knowledge concerning the scalability and the influencing factors are necessary, which were investigated finally.
For this purpose, in total 15 reinforced concrete plates with three different scales were manufactured. All internal parameters, for example, the slab dimensions, the reinforcement diameters and spaces as well as the concrete cover were either reduced or enlarged, according to the selected scale used in the specimen dimensions. For the conduction of the experiments, the accelerated configuration of the drop tower facility of the Otto-Mohr-Laboratory was used. The usage of an adapted impactor, with an equivalent geometry, was particularly challenging. In particular, the changing of the diameter leads to an insufficient acceleration of the impactor when using the compressed air-driven test facility. To ensure the usual functionality, a sabot construction around the impactor was used to seal the gap between the impactor and the inside of the acceleration pipe. This enabled a linear and uniformly impactor’s movement. The robustness of this system as well as the compression-velocity-relationships of each impactor were investigated by conducting several protests.
Afterwards, the main experiments on precast and size scaled reinforced concrete plates took place. In total five velocity levels with three different scales for each level were tested. Deviations of the impactor’s velocity could be minimized due to the already known charging pressure relationships. Qualitatively, the specimens within one velocity level exhibited similar damages across all scales. Furthermore, the evaluation regarding the quantifiable damage parameter, as well as the local and global component respectively material behaviour, took place.
Report in the annual report 2019, part I (experiment)
Reaching a maximum speed of up to 270 km/h
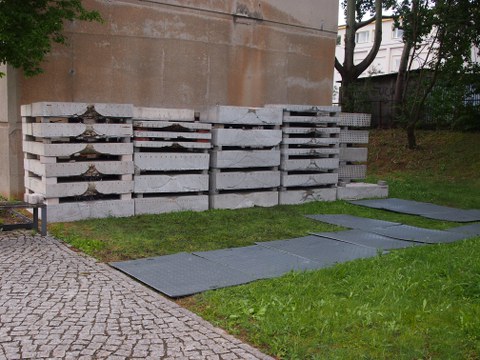
Tested slabs next to the drop tower facility of the Otto Mohr Laboratory
The behaviour of reinforced concrete under static loading has been extensively researched. But there are still knowledge gaps regarding such behaviour under dynamic loading, which need to be closed to protect critical infrastructures from terrorist attacks and natural or technical risks. The knowledge gained within the project “Tankaufprall” has increased the understanding of the material behaviour of reinforced concrete under high loading rates. During the third part of the first period, the experiments of the former project phases will be supplemented and systematically enlarged.
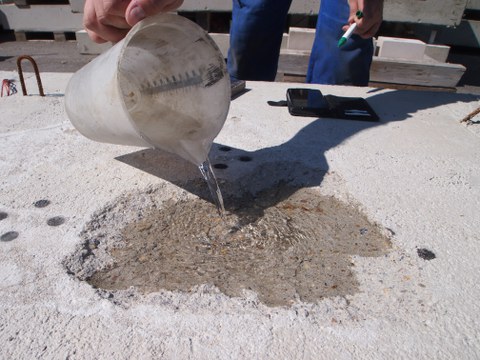
Permeability test under atmospheric pressure
The drop-tower facility located at the Otto-Mohr-Laboratory is available to the Institute of Concrete Structures to conduct the impact tests. The experiments that study the effect of the slab thickness, and of a variable bending and shear reinforcement ratio have already been completed. The main focus was the experimental observation of failure with various damage levels which varied from several bending cracks to a punching failure of the reinforced concrete caused by a complete perforation of the impactor. For the evaluation of the material behaviour and subsequent damage analysis, the deflection and the resonant frequency was measured at some points of the specimen while the experiments were carried out. The permeability of the damaged plates under atmospheric pressure was subsequently tested. In addition, the evaluation of the punching angles on saw-cut slabs was carried out.
To transfer the experimental behaviour results to that of a real building, experiments to account for the size-scale effects are planned. In preparation for this, specimens with uniformly scaled slab geometries and reinforcement arrangements were prepared. These will then be tested and evaluated under equally adapted test parameters.
Report in the annual report 2019, part II (Numerics)
Impact tests of purely virtual structures
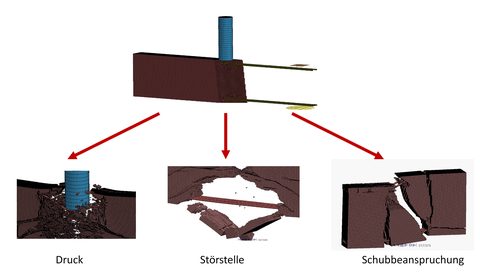
Problems with modelling the reinforcement at dynamic loading conditions
Based on the previous experimental results, a numerical model was created which help to reproduce the real experiments as exactly as possible. The simulations support the experimental methods and provide useful experimental arrangements to extrapolate the knowledge gained to more general structures.
The method was created in LSDyna, based on the FEM with a discrete reinforcement layout with beam models. It could be shown that the Schwer Murray Cap Model best represents the experimentally obtained results at low speeds. However, this law fails at speeds higher than those previously considered, so that a complete re-examination of the behaviour on the material side is necessary over the entire speed range.
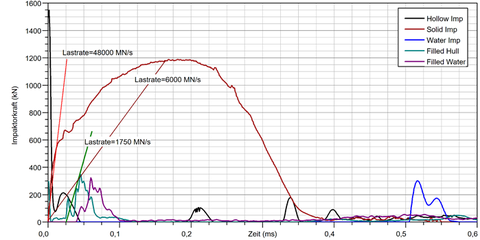
Force-time curve of diff erent impactors and load rates
In a similar way, this also applies to the integration of the discrete reinforcement. A satisfactory solution is currently being worked on for this. Submissions from currently parallel projects for correct reinforcement mapping could provide a breakthrough. Some working points of the numerical project part and the recalculation of the experimentally obtained results were therefore postponed in favour of the investigations on the impactors.
In this subject area, the scenario of a coupled impact event, which is composed of an impact of a rigid impactor and the subsequent impact of a deformable impactor, was analysed with different numerical models. Alternative impactor variants were developed within the models. The experimental boundary conditions were determined on the basis of these models. Relationships between masses, energies and velocities, for the individual types of loads and impact variants, were analyzed. From this comparison, parameters can be derived with a constant degree of damage.
Report in the annual report 2018, part I
Impact research − slowly, it is getting serious
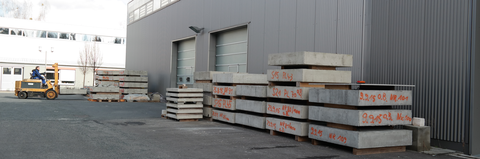
Handling der Plattenimpaktproben auf dem Hof des Otto-Mohr-Laboratoriums
For more than 8 years, concrete structures have been dynamically tested in a variety of ways at the IMB. Under the initiative of “impact research”, experiments have been undertaken on a structural and material level. Everything began with several free-fall drop tower experiments on concrete slabs from a few meters high with handy weights. Meanwhile, a system has been installed, which can drop weights of up to 2.5 tons from a maximum of 10 meters in height. At the same time, the expertise related to the dynamic material characterization was built up within the institute. For this purpose, several Split-Hopkinson-Bar facilities were implemented, and thousands of experiments have been carried out.
It quickly became clear that the more interesting structural effects occur at higher speeds. Since then, several hundred tests have been carried out and analysed in speed ranges of up to 100 m/s with the accelerator facility at the Otto Mohr Laboratory. It turned out that the capacity of the self-made facility is far from exhausted, and that speeds of up to 250 m/s are feasible.
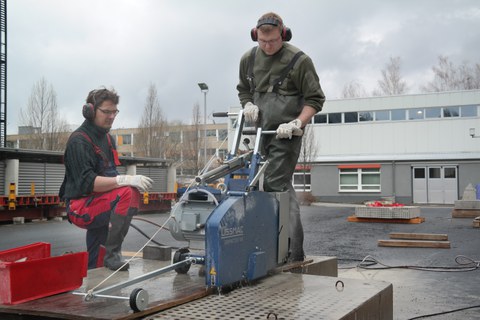
Durchführung von Sägeschnitten
Since the start of the project of “Tank Impact 1C”, more emphasis has been put on the numerical part, because the experiments are only understandable if they can be properly mapped and reproduced at this level. This is where the experience of the projects has been flowing since 2010. At that time, the VERD model laid the foundation for a material description at the macroscopic level. Since then, numerical analysis has continued to develop in parallel on the meso- and macroscopic level under the guideline of Prof. Häußler-Combe. The integration of experience gained in dynamic composite experiments makes it possible now to study the overall structure with all its parameters. For this purpose, preliminary studies on different projectile variants were started in 2017 with the aim of fully mapping the main impact scenarios to the real world conditions. With regard to stage 2, it will be possible, for the first time, to describe a complex overall structure and to predict the damage mechanisms. The structural calculations and strengthening efforts for such a large structure are getting serious.
Report in the annual report 2018, part II
Steel reinforced concrete under impact loading – all good things come in threes
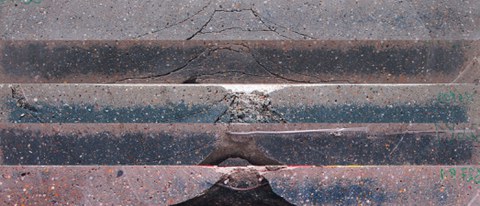
Stahlbetonplatten nach Impakt mit Geschwindigkeiten zwischen 25 und 61 m/s
The composite material steel reinforced concrete plays figuratively and literally a supporting role in civil engineering. Despite many years of research, there are still unanswered questions about the material behaviour, in particular under dynamic loading. To answer these questions, the experiments carried out in the previous two project phases “Tankaufprall 1A” and “Tankaufprall 1B, will be expanded, and the influence of various parameters will be systematically investigated.
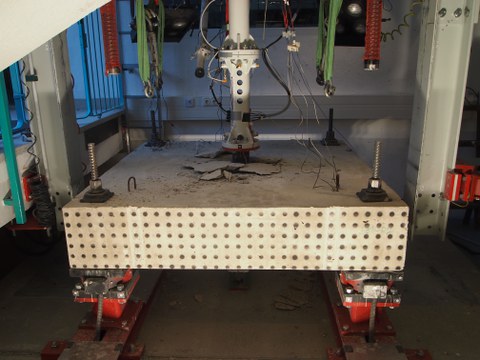
Stahlbetonplatte nach Impaktversuch
Within the third project, phase 1C, further slab specimens will be tested in the accelerated configuration of the drop tower in the Otto Mohr Laboratory. Here the variation in external and internal parameters is foreseen. Specimens with different thickness and bending reinforcement layouts will be tested. Further, it is assumed that the shear reinforcement has a significant effect on the damage behaviour of the slabs, so the arrangement of different stirrups is also a part of the experimental plan. All experiments will be carried out with different impactor velocities. The results will be used to investigate the scale effect and to validate the detailed numerical analysis of the experiments. In this way, the knowledge gained could be scale-up to larger building structures.
Besides the implementation of an ambitious measurement technology for rates up to some megahertz, experiments will be carried out to characterize and analyse the damage. Among them are the liquid penetration test under atmospheric and high pressure, as well as the assessment of the damage directly from the perforated and sawed reinforced concrete slabs. The tested slabs will be examined using planar computed tomography at the “Bundesanstalt für Materialforschung und –prüfung”, which will make visible aspects like micro cracking.
Report in the year book 2017, Part I
Impact tests in the third round

Numerical study on scale effects; here: slabs with an edge length of 1.5 m (above) and 2.0 m (below) under full scale load
Reinforced concrete is the preferred material for the design of power plants, both for new buildings as well as for any planned subsequent protections. Despite decades of intensive research, there are still unanswered questions about the complex material behaviour under highly dynamic loading, especially in the civil sector. In the two previous project rounds on this topic, a fundamental experimental understanding of stresses in impact events has been developed. In the third round, the local effects will now be numerically evaluated, and based on those, the planned experiments will be optimized in advance. After that, all findings will flow together in a large-scale experiment.
The current focus is on investigations of a sufficiently accurate numerical mapping of the bond behaviour between reinforcing steel and concrete matrix, the scalability of the experiments on real component‘s geometries as well as the optimization of the arrangement of a load-bearing reinforcement. The modelling of the coupling between reinforcement and concrete matrix poses a particular challenge at this macroscopic scaling level. Only by discrete modelling of the reinforcement, sufficient information about the occurring damage mechanisms can be obtained. Currently, this modelling is done by rigid coupling of the respective nodes, which can lead to slight distortions of the results, especially in the integration of stirrup reinforcements. It can be shown by parameter studies with different imaging variants that although this method maps the global component behaviour well, local effects are insufficiently taken into account. For example, a stress running transversely to the axis of the reinforcement cannot really be taken into account.
Furthermore, the influence of liquid-filled or hollow body impactors with their variable stiffnesses can be clarified. These provoke a significantly different component behaviour than the solid rigid bodies investigated so far. It has been shown that plausible effects and parameters can be generated purely numerically by appropriate coupling of finite element and smoothed-particle hydrodynamics (SPH) methods.
Report in the year book 2017, Part II (numerical part)
Bond modeling for impact load
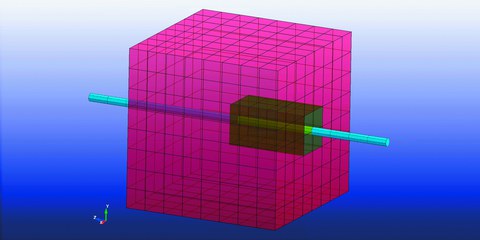
Model of a pull-out specimen with two differently defined concrete elements (red without and green with bond condition to the steel)
As already mentioned in the report ‘Impact tests in the third round’, numerical investigations have been carried to investigate the modeling options for the bond behaviour between reinforcing steel and the concrete matrix. For this purpose, virtual pull-out tests were carried out within the project using a finite element simulation. In such an FE model, the virtual test specimen was modeled according to DIN EN 10080 guidelines for the standardized experimental testing of the bond behaviour of ribbed and profiled reinforcement steel. Accordingly, a bar embedded in a concrete cube was subjected to a tensile force. The test result is a tensile force-slip relationship, where the slip is the relative displacement between steel and concrete. The results of the simulations were compared with those from experimental tests and literature.
Various models have been implemented to take account of the bond mechanisms. In the first computer model, the connection between the transverse and bending reinforcement (model as beam elements) to the concrete (model as volume elements) was implemented using fixed node connections, as it is usual in the reinforced concrete simulation. However, this type of modeling neglects the slippage that occurs in reality. To increase the accuracy of the simulation and to replicate the slippage of the reinforcement when using beam elements, alternative composite models were taken into account. These have been examined in more detail about their suitability, accuracy, and feasibility in parameter studies. The usual procedure for composite modeling was compared with the use of spring elements and the application of so-called constraints (additional conditions). Good results were achieved with the latter. In addition to the realistic depiction of slip, this option offers an additional advantage: The finite element mesh of the beam elements can be defined independently of the mesh of the solid elements.
Report in the year book 2016
Impact testing with piercing effects
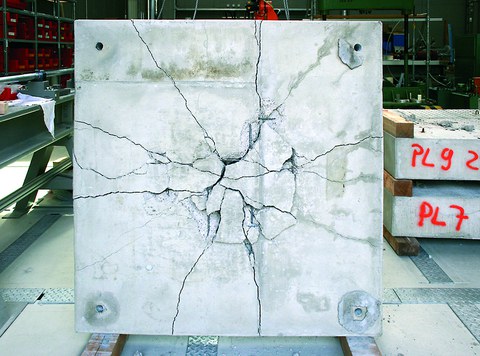
Bottom side of a reinforced concrete slab
Generally, it is well known how a steel reinforced slab behaves, or which components the applied loads counteract. These structures are all around us in the form of room-enclosing walls or deck slabs among others. Yet, little is known regarding how such a plate resists an impact load scenario. Which impact resistance is available? Which level of damage is to be expected, and how much load bearing capacity is available after the impact loading? These questions are to be answered within the project.
While the project is currently in progress (at the stage 1B), several impact tests on steel reinforced concrete slabs have already been completed. One of the main questions we have to answer is: how should ‘impact’ or ‘impact loading’ be defined? In contrast to static loads, there needs to be a differentiation between ‘soft’ and ‘hard’ impacts. The difference between these impact processes lies in the interaction between the structure that was hit (reinforced concrete slab) and the impactor. Within this project, the effect of a ‘hard’ impact is the main object of research. A hard impact is defined as an impact where the impactor is rigid. This means that there are no significant deformations of the impactor. In contrast to the impactor, the reinforced concrete slab shows large damage.
The main objective of this project is to investigate the relationship between impact load and the resulting level of damage. This investigation is necessary to finally understand the structural and the material behaviour. The investigation of the damage of the reinforced concrete elements is done by our project partner BAM in Berlin. The investigation is conducted using planar tomography. This is a so-called non-destructive testing method. By using planar tomography, it is possible to observe cracks inside the plate. In addition, the direction and the width of the cracks can be determined, providing important parameters to describe the damage of the plate.
Report in the year book 2015
Reinforced concrete slabs under impact
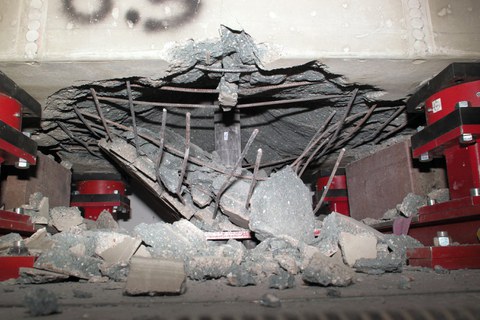
Reinforced concrete plate immediate after testing with an impact load
Since the incidents of September 11th, 2001, the scenario of an aircraft striking a structure has become more relevant and tangible than ever before for both engineers and the design of buildings. In order to guarantee the structural safety of the building, it is necessary that the design can handle an impact load case, regardless of what caused such an occurrence. The current research and testing at our institute intends to propose procedures and structural models to calculate the various load scenarios that shall be considered when dealing with the situation of an impact event.
To validate the procedures and models with measured data, impact experiments with reinforced concrete slabs were carried out at the Otto-Mohr-Laboratorium using an 11 m high drop tower. To investigate the behaviour of the reinforced slabs under impact different input parameters were varied: the geometry of the slabs, the reinforcements content as well as the speed and the mass of the impactor. This year, 10 experiments were carried out to complete the existing database. Altogether, more than 70 experiments with slabs made of reinforced concrete were carried out in this project. With the collected data, it was possible to investigate the load bearing and the failure behaviour of reinforced concrete slabs. The observed failure pattern varied from bending cracks to failure cones when punching shear failure occurred. The most significant parameter in terms of the damage observed was found to be the speed of the impactor.
Investigation of the outer damage is only one part of the project. At our project partner BAM, Berlin, the inner cracks are examined with tomographic methods to estimate and quantify the degree of damage.
Another main aspect is the investigation of size effects. These effects are investigated to develop a standardized small size impact test. A small size test is necessary because it is extremely difficult to test real structures like walls of a nuclear power plants. Furthermore, a calculation model for post-test calculation is under development.
Report in the year book 2014
Reinforced concrete slabs under impact loading
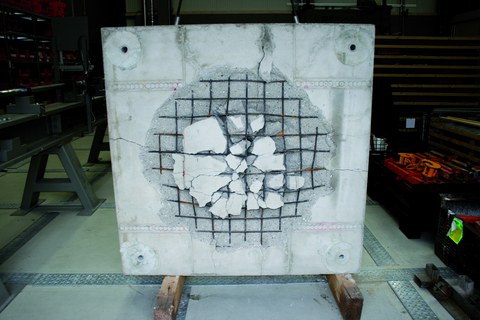
Slab after the experiment, big punching cone at the bottom side
Reinforced concrete slabs are usually used for ceilings, flat roofs or in bridges, for example as bridge decks. They are normally stressed statically, which means that the loads are applied in a moderate pace. Examples are furniture on floors, or even vehicles on bridges (a controlling load on bridges is that caused by a “traffic jam”). In addition to these usual stresses, in exceptional cases, extreme loads can occur, which differ not only by significantly higher absolute values, but also often by a higher loading rate than “normal” loads. Examples include earthquakes, vehicle impact or falling rocks in the mountains. In particular, the impact of objects at high speed leads to extreme impulse stresses of components or structures in a very short period of time.
In order to design slabs that are sufficiently resistant against such kind of stresses, it is necessary to know the behaviour of these components under the conditions described. Therefore, more than 50 plates are currently tested in a drop tower at our institute. In these tests, an impactor with a mass varying from 600 kg to 1500 kg falls from heights ranging between one to four meters on plates with different geometry and load capacity. Here, the acting forces as well as the deformation and damage occurring present interesting features to this evaluation.
First results are available. As expected, for example, the damage of the plates increases with increasing drop height and falling mass. However, at a certain combination of height and weight, the maximum deflection at the part of the test plate that is not destroyed decreases. This is caused by a change in the failure mechanism. At lower stresses, the plate is primarily subjected to bending, whereas with increasing force (caused by increasing drop height or mass), the punching of the plate is the main failure mechanism.
At the end of the project, it should be possible to predict the behaviour of reinforced concrete slabs under similar loading conditions, on the basis of these findings. Conversely, this will allow to design slabs with sufficient load bearing capacity.