FEM versus experimental evidence
Table of contents
Project data
Titel | Title Belastungsversuche an geschweißten Stahlgitterbauteilen | Load tests on welded steel lattice elements Auftraggeber | Client LTB Leitungsbau GmbH, Radebeul Zeitraum | Period 11.2016 Leiter | Project leader Prof. Dr.-Ing. Dr.-Ing. E.h. Manfred Curbach Bearbeiter | Contributors Dipl.-Ing. Robert Schneider, Heiko Wachtel, Maik Patricny, Doreen Sonntag |
Report in the yearbook 2016
FEM versus experimental evidence
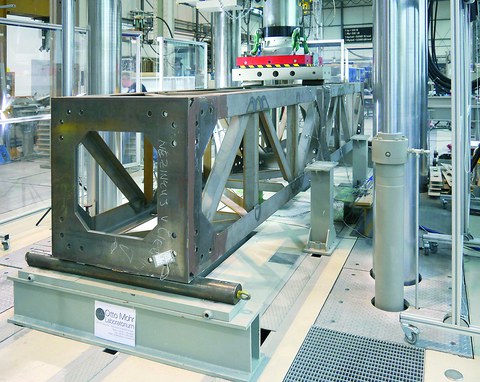
A steel lattice component in the 10 MN testing machine in our laboratory
In 2016, the LTB Leitungsbau GmbH came to us with the request to determine the load bearing capacity of a special, welded steel lattice component by means of a three-point bending test. Prior to this, the company had consulted the full repertoire of calculation models in order to determine the theoretical load bearing capacity of the component. The calculations ranged from simple truss models, calculated using the program RSTAB, over extensive calculations according to Petersen, to detailed modelling in finite element programs by specially trained engineers.
As is well known, theory and reality sometimes differ widely. Scattering material properties, not 100 % ideal connections, manufacturing-induced imperfections and much more are subjected to certain uncertainties and – sometimes – difficult to grasp mathematically. By means of simplified models and partial safety factors for the design process, one wishes to ensure that the result remains on the safe side. But what is to be done, however, if the complex calculation using FE models results in 300 kN as linear-elastic load-bearing capacity of a steel lattice component, and other calculation models yield more than double? What is the more reliable result?
To answer this question, an experimentally load test was necessary. In the case of this steel girder, 28 strain gauges and 2 inductive displacement transducers were applied to record the strains of the single rods and the deformation of the whole structure. With the help of these data, it is possible to calculate the forces in the single rods during loading. It also can be seen, at what load level the material reaches the end of its elastic strain capacity and passes to the plastic range, from where it comes to irreversible plastic deformations when the load is further increased. From a certain point, the component is then no longer able to absorb further forces, the deformations increase disproportionately and the failure level is reached.
In the concrete case, the elastic range was reached at approximately 650 kN and the total load bearing capacity at approximately 1000 kN, thus 100 tons load. If one had only relied on the theoretical FE models in this case, a highly uneconomical structure would have been the result.