Repair and recycling technologies

Simulation of CFR samples in various states of repair and under
One decisive factor in establishing the use of fiber-reinforced composites (FRCs) is the availability of technologies and methods allowing a complete repair of components and a recycling of the materials while retaining their properties as far as possible.
R&D work at the ITM aims to shed light on repairability of damages to FRCs with high reproducibility and restoration of the original composite properties. To this end, innovative chemical-physical repair methods are being researched for carbon-fiber-reinforced components (CFR components). The approach focuses on innovative ideas based on semiconductor technology, allowing a complete removal of the matrix in a locally defined damage area. The textile reinforcement structure is exposed and damaged fibers are removed. Afterwards, a force-flow-adapted layer restructuring using patches developed with the aid of simulations is performed to re-establish as much of the loading capacity of the CFR component. The necessary patented processes for a gentle matrix removal are currently being developed at the ITM.

CFR sample with damage trait and removed matrix (left), CFR sample with integrated, simulation-based repair patch (center), CFR sample with re-filled matrix (right)
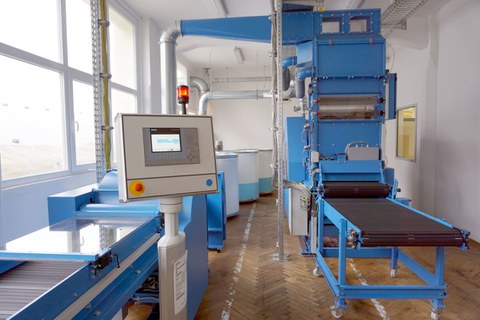
ITM carding unit for the further processing of recycled carbon fibers
Another focus at the ITM is the development of a new process chain for the production and further processing of recycled carbon fibers (rCF) into innovative yarn constructions for further use in load-bearing CFR components. For this, the following fundamental tests are made for the spinning of rCF:
- technology development for a gentle production of rCF for textile-technically processable yarn constructions,
- development of hybrid yarn constructions from rCF for thermoplastic CFR components,
- development of yarn constructions from 100 % rCF for use in thermoset CFR components or as a fine staple fiber yarn, and
- transfer of the developed technologies to other high-performance recycling fibers.
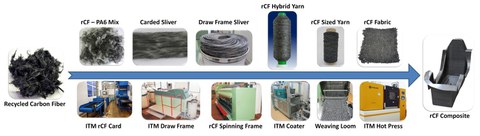
Process chain for the production of load-bearing CFR components from rCF
The aim is to develop yarn structures with a maximum performance level in the CFR component in comparison to the original CF primary filament yarns (strength up to 90 %). The basic examined process considers the entire thread production chain. These research efforts were honored with the German Resource Efficiency Award 2016 and the AVK Innovation Award 2016.
Contact person:
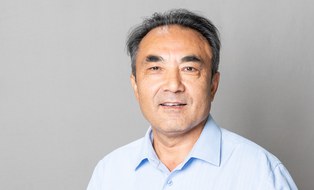
Mr Dr.-Ing. Anwar Abdkader
Head of multi-material yarn structures for high-tech applications
Send encrypted email via the SecureMail portal (for TUD external users only).
Visitor Address:
Breitscheidstraße 78, House D, Roum 1.1.11
01237 Dresden
Deutschland
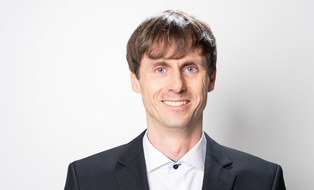
Mr Dr. Thomas Gereke
Research Group Leader Structure & Process Simulation
Send encrypted email via the SecureMail portal (for TUD external users only).
Visitor Address:
George-Bähr-Straße 3c, Zeuner-Bau, Room 132
01069 Dresden
Deutschland