Acoustic emission for damage detection
Table of contents
Project data
Titel | Title TP Experimentelle Untersuchungen und Datenbasis (ExData) im Verbundvorhaben KI-unterstütztes Schallemissionsmonitoring zur automatischen Schadenserkennung in Tragstrukturen von Windenergieanlagen | Subproject Experimental studies and data basis (ExData) within the joint research project AI-supported acoustic emission monitoring for automatic damage detection in supporting structures of wind turbines Förderer | Funding Bundesministerium für Wirtschaft und Klimaschutz (BMWK) Zeitraum | Period 07/2020 – 06/2024 Teilprojektleiter | Subproject manager Prof. Dr.-Ing. Steffen Marx Team | Team Dipl.-Ing. Ronghua Xu, René Wallschläger Projektpartner | Project partners Institut für Informationsverarbeitung, Leibniz Universität Hannover | Institut für Informatik – FG Mathematik und Informatik, Freie Universität Berlin |MKP GmbH, Hannover Assoziierte Partner | Associated partners Max Bögl Wind AG, Neumarkt in der Oberpfalz | | TÜV Süd Industrie, Service GmbH, München |
Report from year book 2023
Energy spectral analysis of wire breaks in tendons

Energy distribution of the 30 post-tensioned wire breaks from one tendon
The use of hybrid towers for onshore wind turbines has become increasingly popular in recent years. Such towers consist of a prestressed concrete tower on which a steel tower is placed. This modular construction method is cost-efficient and offers advantages during transport and installation.
The concrete tower consists of precast segments and is prestressed externally. Maintaining the proper condition of the tendons is crucial for the safety and performance of the tower. To investigate the characteristics of possible wire breaks, tests were carried out on prestressed tendons with similar boundary conditions to real wind turbines. Four SUSPA EX30 tendons, each with 30 parallel wires, were individually prestressed to 700 kN in a 12 m × 4 m test rig. In each of these four tendons, 30 wires were severed, resulting in a total of 120 wire breaks.
To record the acoustic signals generated by each wire break, 24 piezoelectric acoustic emission sensors were installed along the length of the tendon. Three measuring systems from Vallen Systeme, each with eight measuring channels, were used to pre-process and store the acoustic signals generated. In a case study on one of these four tendons, an energy spectral analysis of the wire breaks was presented. Using the 30 wire breaks and the energy distribution calculated from them, it was possible to analyze the behavior of the tendons above the usual frequency range in the construction sector between 0 to
50 kHz.
The results show that the energy of the wire breaks is concentrated in a low frequency range, particularly at frequencies between 5 and 20 kHz, which account for over 90 % of the total energy. Since ambient noise often has a normal spectral distribution over a wide frequency range, the distinct frequency pattern observed in wire breaks can be effectively used to detect them even in the presence of high ambient noise.
Report from year book 2022
Acoustic emission measurement for detection of tension wire breaks
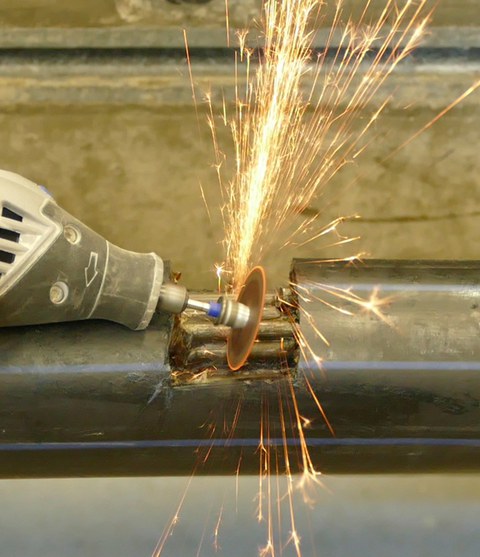
Artificial wire break using a dremel
In hybrid towers of wind turbines, tendons and their anchorages are stressed with high dynamic loads. Due to the difficult access to the tendons inside the tower, possible damage cannot be detected immediately. The overall goal of the project is therefore to develop methods for efficient detection of damage events of the tendons using acoustic emission analysis.
In order to achieve this goal, a prestressed concrete frame was constructed and built at the Otto Mohr Laboratory, which corresponds to the boundary conditions of a real wind turbine. The 12 m × 4.1 m large frame consists of four concrete beams and four external tendons inside the frame. The unbonded tendons are each located in a pipe filled with special anti-corrosion material. Each tendon consists of 30 individual parallel wires. With a total prestressing force of 700 kN, approximately 23 kN is applied to each individual wire.
Acoustic emission measurements are carried out in the tension frame with distributed piezoelectric sensors. A total of 16 sensors are used in combination with different preamplifiers and dampers. Two AMSY-6 with eight channels each from Vallen Systeme GmbH are used as the measurement system. The tendons are first exposed at targeted locations. After the sensors are coupled to tendons and surrounding components, wire breaks are generated using a dremel. After the experiment is performed, acoustic emission parameters such as amplitude, arrival time, energy etc. are extracted and stored. Transient waveforms of the fracture signals are also stored at a predefined sampling rate. The stored signals can be subsequently processed in programs such as Python, or Matlab. In the end, more than 2,000 individual signals can be expected at all sensors, which form a good basis for the development of an algorithm for automated damage detection.
Report from year book 2021
Acoustic emission measurement
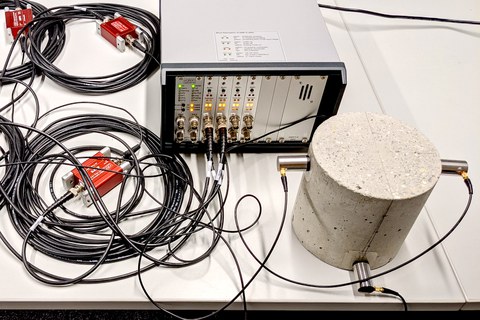
Trial test with measuring instrument AMSY6 from Vallen Systeme
A wind turbine converts the kinetic energy of the wind into electrical energy and feeds it into an electricity grid. In recent years, hybrid towers for wind turbines have become increasingly important. The hybrid towers consist of concrete rings and steel segments that are assembled in a modular way. In order to ensure the stability of the towers, tendons are prestressed in the longitudinal direction inside the towers. In the interest of cost-effective repair, any damage such as tension wire breaks should be detected as early as possible.
There are various methods for evaluating the tendon condition, such as visual inspection and magnetic stray field measurement. However, sometimes the methods cannot be used due to limited accessibility. A permanent observation of the tendon states and an early damage detection are possible by using the acoustic emission measurement despite the difficult accessibility. The measuring method is based on the principle that the acoustic signal of the breaking wire can be picked up by the piezoelectric sensors and further processed by the recording unit. With the piezoelectric effect, electrical voltage is caused by the deformation of the tendons and will be converted to the diagonal signal. Afterwards, preamplifiers ensure that the signal is transmitted over long cables without high impedance. Using an analogue-to-digital converter, analogue signals are digitized and then fed to a signal processor. From the digitized signals, both acoustic emission parameters (AE parameters) such as arrival time, signal duration, maximum amplitude etc. are extracted and transient waveforms are stored.
One focus of the research project is to determine the characteristics of each link in a measurement chain. By decoupling the influences of source mechanism and propagation path on the signal shape, AE events can be characterized precisely. The second research focus is the development of an algorithm using machine learning methods. Based on the obtained AE parameters and waveforms, the algorithm should be able to predict a failure with sufficient accuracy.
Report from year book 2020
Automatic SHM System of wind turbines
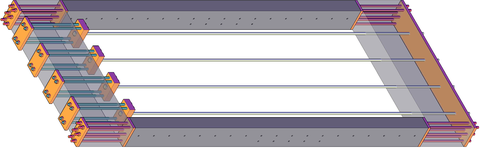
Experimental setup for acoustic emission measurements
In 2018, the Federal Ministry for Economic Affairs and Energy (BMWi) demanded in the sixth monitoring report of the energy transition that by 2050 at least 80% of greenhouse gas emissions should be reduced and at the same time a share of 60% of renewable energies in the gross final consumption of energy should be achieved compared to 1990. With around 16% participation in total energy generation in Germany, wind energy is one of the focal points of the energy transition. To be able to meet the goal, on the one hand, the performance of the wind turbines must be increased and, on the other hand, their construction and maintenance costs must be reduced. For lower maintenance costs, damage to components must be detected on time before they cause a critical failure and require costly repairs. The basis for this type of maintenance is data that contain information about changes in condition and damage.
For the wind turbines in operation, most of the data is obtained using conventional measurement methods, e.g. strain gauges or acceleration sensors. With this method, however, it is assumed that sufficiently large damage causes global structural deformation in the structure or in components, which can be recorded by the above-mentioned measurement technology. Small damage that has occurred cannot be identified and localized in time with this method.
In this project, acoustic emission measurements are used to generate data that enables the damage events to be detected directly. A large number of large-scale experiments are planned in the Otto Mohr laboratory of the TU Dresden in which the generated wire break signals of tendons are recorded by acoustic emission sensors. Various influencing parameters are investigated during the tests, such as different sensor arrangements, distances between breakpoints and sensors. The determined data is processed with the help of the new evaluation methods from the field of artificial intelligence (AI). Based on the findings, a concept for an effective structural health monitoring system (SHM system) for wind turbines should be developed, which can provide information about the condition of the load-bearing structures.