Cross sectional adaption for rod-shaped elements in compression
Table of contents
Project data
Titel | Title Querschnittsadaption für stabförmige Druckbauteile | Cross sectional adaption for rod-shaped elements in compression Förderer | Funding Deutsche Forschungsgemeinschaft (DFG) / SPP 1542 Zeitraum | Period 10/2011 – 10/2014 (1. Phase) 11/2014 – 06/2020 (2. Phase) Leiter | Project manager Prof. Dr.-Ing. Dr.-Ing. E.h. Manfred Curbach Bearbeiterinnen | Contributors Dipl.-Ing. Angela Schmidt, Dipl.-Ing. Katrin Schiteilo |
Report in the annual report 2018
EFFICIENTLY SHAPED COLUMNS
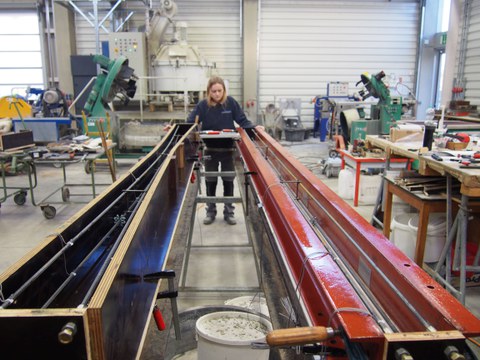
Schalungen für untersuchte Stützenformen bei einer kombinierten Beanspruchung aus Längskraft und Biegung
Within the DFG Priority Programme 1542 “Concrete light”, this subproject investigated the extent to which the load-bearing capacity of compression members can be increased by shaping them according to the flow of forces. With the exception of the construction of the final demonstrator, work on the project has been completed after seven successful years.
In a typical reinforced concrete skeleton structure, the characteristic load cases of compression members usually involve design for a centric load on the inner columns and an eccentric load on the edge columns resulting from the frame moments. In the first funding period of the project, the focus was, therefore, on the investigation of axially loaded columns, while in the second funding period, the focus was on a combined load of longitudinal compression and bending.
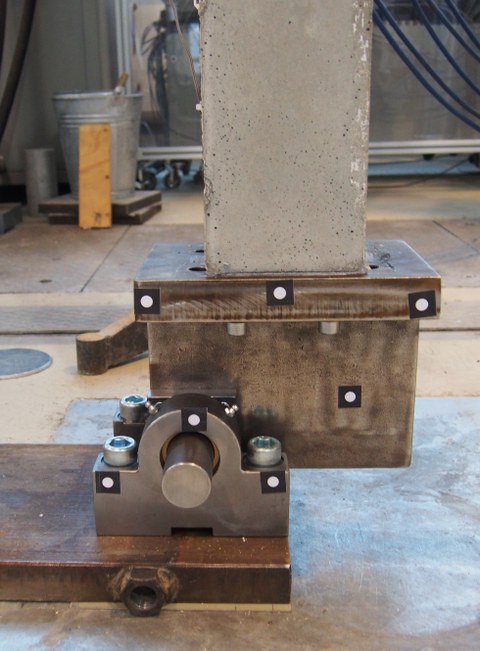
Lasteinleitungskonstruktion bei exzentrischer Belastung
With a planned centric load, and taking into consideration a stability failure, a more favourable column shape for slender columns could be defined than that of a column with a constant cross-section. For compact columns, which do not deflect due to axial compression, the constant shape is already the best, since it approximately produces constant stress over the entire height of the columns. On the other hand, the stability of a column can be increased both by its cross-sectional form and by its shape in the longitudinal direction of the rod. Both effects were investigated by calculation and subsequently verified experimentally. By optimizing the shape in the longitudinal direction, an increase in load capacity of approximately 25 % compared to that of a reference column of the same volume was achieved.
In the case of a combined load, the ratio of the applied normal force to the respective moment is decisive for the form-finding of the columns. In addition to the design of the building, the boundary conditions at the respective storey are the determining factor. Because, in a braced structure, the bending stress is almost constant on all floors, but the compressive forces constantly increase from the top to the bottom floor. The form-finding was carried out as a case study for two different load conditions. Subsequently, it was experimentally investigated. In the case of columns predominantly stressed by bending, a load bearing capacity increase of approximately 70 % was achieved.
The research project showed that compression members can be designed more efficiently by adapting their shape to the flow of forces.
Report in the year book 2017
COLUMNS LIGHT
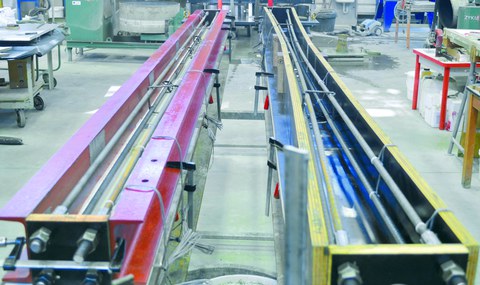
Formwork of the reference column (left) in comparison to the optimized shape (right)
The main aim of the project was the design and construction of compression members according to the expected loads. This method leads to the design of a load-bearing element which is sustainable and reduces the material used.
Theoretical and experimental investigations on centrically loaded columns were successfully carried out in recent years. Building on these experiences, eccentrically loaded columns were considered in a second step. For typical building constructions, such loading on columns occur at the edges of framework structures. The highest stress arises at the connecting point between ceiling and column because the largest bending moments occur in this area. Based on these considerations, it can be concluded that to achieve an optimized shape, a larger cross-section is necessary at the column’s bottom and top, while tapering is possible in the middle area. The exact column’s shape was attained by an iterative calculation method, where a cross-section analysis was undertaken at different height levels. To achieve uniform stress of the column along its length, the cross-sectional dimensions at each level considered were adapted in a way that the allowable concrete strains were fully utilized. However, given a constant amount of reinforcement, it was not possible to reach the steel yield strength along the whole column, because, in areas with low or no bending, the tensile stresses are also very low. Instead, reaching the yield strength in at least 50 % of the structural element was the criterion used to choose the reinforcement.
To demonstrate the methodology, the experimental load-bearing behaviour of a column, designed according to the proposed method, was investigated. Accordingly, an experimental setup was developed, which introduced the assumed loading in the column. For comparison purposes, a reference column with a constant cross section was also tested. On the basis of three tests, a load bearing capacity increase of approximately 70 % was achieved for the optimized geometry, and in this manner, the calculation method was also proved. Furthermore, strain measurements confirmed an almost uniform concrete strain distribution along the column height.
If the comparison is not undertaken by an equal volume but the loading, an optimized geometry can be made only with one-half of the concrete amount, but with the same stability.
Report in the year book 2016
Columns shaped as a function of loading
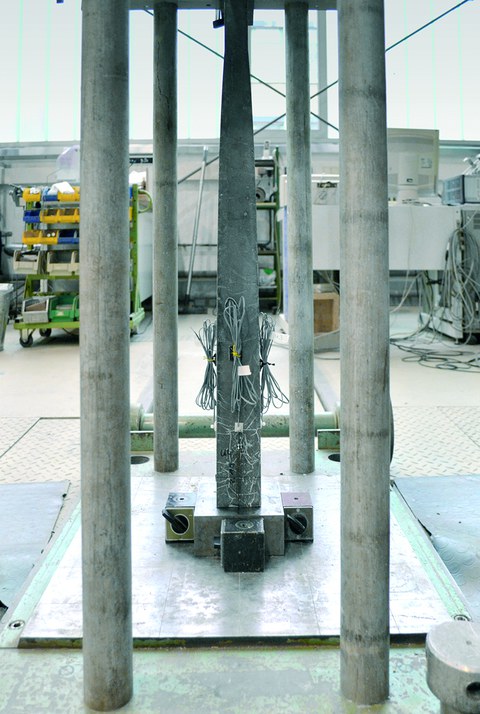
Bottom area of a form optimised column in the testing machine
The aim of this SPP 1542 subproject is to design and construct columns according to the flow of forces within a structure so that optimized shapes can be obtained. In most cases, the load bearing capacity, relative to that of columns with the same volume and a constant cross-section, can be increased with this method. Accordingly, this construction approach allows for an efficient use of building materials, and therefore, slender and more lightweight columns. In addition to this functional improvement, the method carries a high aesthetic potential.
The last few years were spent studying axially loaded columns. For this loading type, an optimized shape for slender columns, differing from the usual constant geometry, offers an advantage. In slender columns, the deflection depending on the function of the deformation figure leads to bending moments. The size of the bending moments varies over the column length, resulting in changing stresses along the column’s cross-sections. To achieve a uniform stress distribution, and thereby the best utilization of material over the entire length of a column, the shape can be optimized. Interestingly, the deformation of short and compact columns under axial compression is negligible. As a result, bending moments and related stresses in compact columns do not play a significant role. The generated stress is only a function of the compressive force, and a constant shape in the longitudinal direction results in a uniform stress distribution. The optimization of slender axially loaded columns was studied extensively in this project. The theoretically determined results were verified with experiments in both longitudinal and transverse direction.
Based on the results obtained, columns with an eccentric loading will be studied in a second step. Therefore, the first step was to identify the most typical load cases of columns and then define eligibility criteria. Afterward, an optimization method was developed to obtain the best material utilization. The experimental testing is subject to further research.
Report in the year book 2015
Load increase by varying the form
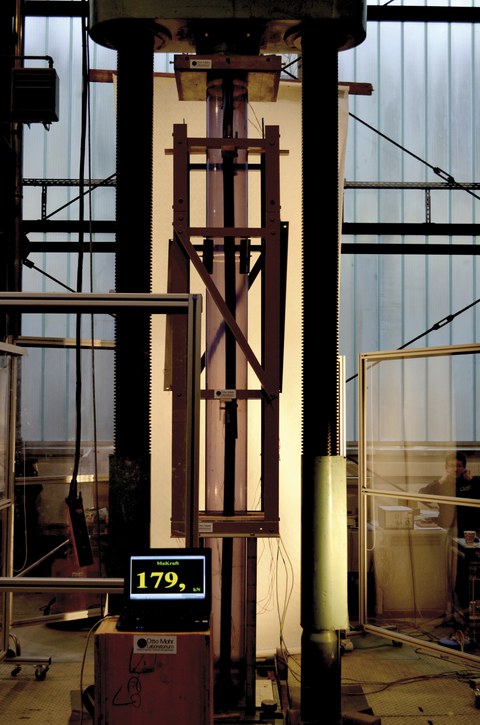
Pressure test with a slender column, clamped on both sides
Columns are important structural elements for most buildings and they can have an architectural function too. With the intention of carrying more and more loads and building slender and filigree structures at the same time, high-performance materials, like ultra-high performance concrete (UHPC), become crucial. However, slender UHPC columns have an increased risk of buckling. The failure loads of columns susceptible to buckling are influenced by their shape; thus, an adequate shape selection may result on a column with a higher buckling resistance than that of columns with a constant cross section. This opens new possibilities for a lightweight, architectural building, in which elements are optimized according to the direction and size of forces.
The relationship between the form of the column and the ultimate buckling load is easy to understand by changing the cross-section geometry. It is known that a greater stability can be achieved by using hollow cross sections instead of solid ones, with the same material requirement. The reason is that the stability of a column is essentially influenced by the moment of inertia, which is increased when material is removed from the main axis. Consequently, one can observe a load increase when using an unusual triangular layout, because the tips of a triangle result in an increase of the moment of inertia. For verification, two series of tests were made which achieved more than 10 % higher load capacities compared to those of square columns.
The form of a column is not only determined by the section type, but also by the shape in the longitudinal direction. Higher or lower stressed areas of a slender column are characterized by the deformation of buckling. Understanding this, a more favourable shape in the longitudinal direction can be derived. However, this form depends always on the column’s end support conditions. The optimal shape can be achieved mathematically through the solution of the corresponding differential equation. For a column with fixed ends, the optimized geometry has been verified by three test series. Comparing columns with the proposed shape to reference columns, which have the same volume, the carrying capacity could be increased, on an average, by almost 25 %. Our experimental testing verified the theory for shape optimized columns for the first time.
Report in the year book 2014
Do you know what buckling is?
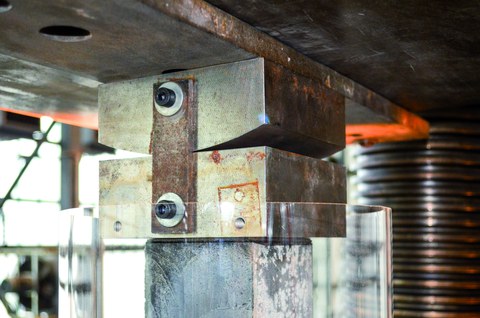
Implementation of line supports, in the picture: at the top of a column
Yes of course! – Most of you will say – thinking about that question – that’s what we’ve learned in the first semester of mechanics! – A slender structure loses its stability and fails suddenly. Surely, most of you will recall typical examples like a pressed thin rod or a slim bended steel profile. But in contrast, few will think of a buckled concrete column and if they do, it will probably be only as an occurrence resulting from a horizontal load, such as a vehicle impact.
But is that still buckling? If a horizontal load acts in the middle of a column, the failure pattern can be similar to buckling; but in fact, it is more like a bending failure, where, if necessary, a load in the direction of the member axis is taken into account. But, where exactly is the difference between bending and buckling at all?
In the well-known Euler buckling modes, derived from the differential equation of the bending line, the failure loads are only given for axially loaded columns, where there is an unlimited deflection. According to this, buckling would be a special case of bending, where the deformation, which results from an axial load instead of from a transverse load, leads to collapse. In addition, the assumptions made within the Euler buckling theory are: an ideal elastic material and exactly straight columns. But, what happens if we have realistic small deviations from these assumed conditions? Then, in a strict sense, we do not have buckling any more, but instead a second order stress failure, where the deflection of the deformed system and the resulting bending stress becomes, with an increasing slenderness, greater and greater and finally leads to failure.
At our institute, we carried out concentric pressure tests with eight 3.50 m long, simply supported, unreinforced UHPC-columns (slenderness ratio l ≈ 130). The failure loads can be calculated quite well, using Euler’s buckling equations (maximal deviation: 12 %). After all, buckling is approximately possible, because, with only little eccentricities, the second order stress failure is a limit case, which returns back to the Euler modes. In reality, from a mathematical point of view, the failure is not exactly due to buckling, because the real cause of the failure will always be the exceedance of stress; nevertheless, the equations of Euler can still be used for concentric loaded concrete columns. Experiments with columns, clamped on both sides, confirm these conclusions.
Report in the year book 2013
Optimization of Slim Columns
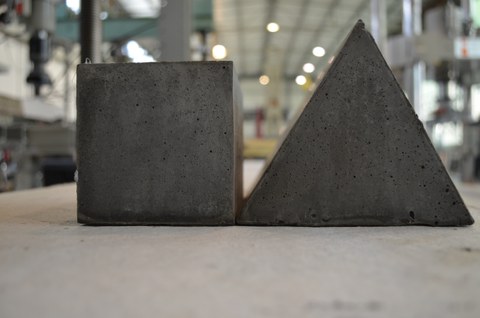
Slim UHPC columns with different cross-sections.
Columns have always been important components of buildings because they lead all vertical loads of a building concentrated into the ground. Today’s conventional column sizes and loads usually lead to failure because of an exceeding of the design stresses. However, it is conceivable that in the future, for example when using ultra high-strength concrete, slenderer columns will be built. Consequently, the stability hazard would be gaining importance.
The columns we build today usually have a constant circular or rectangular cross section over their whole length. If stability failure was crucial, there would be more and less loaded areas in these components. According to the principle of „form follows force“, one can find a load path aligned form for such columns. The result is a uniform stress state, whereby the material requirement can be minimized for an equal failure load. In the first part of the project, theoretical considerations to the buckling problem of a perfect centric pressed column were at the centre. For the group of the convex full profiles, the equilateral triangle has − in this special case – the most favourable form with respect to the buckling resistance because the moment of inertia is largely compared to the cross-sectional area.
The variation of the columns shape in the longitudinal direction, however, depends on the bending line and therefore on the restraint conditions of a column. If the columns were only optimized with respect to their buckling, one would obtain shapes whose cross-sections in the regions of the inflection points of the bending lines are zero. In reality, however, the minimum cross-sections depend on the size of the load to be transmitted to ensure the stress transmission even in these critical areas. The possible increase of the failure load compared to an equal-volume column with constant cross-section depends on the size of this required minimum cross section. If in addition the influence of a triangular shape instead of a conventional circular shape is taken into account, buckling load increases of up to 60 percent can be achieved. Even greater load increases can be achieved with structured cross sections, e.g. in hollow profiles or profiles in the form of a cross. To verify the theoretical results, first experiments were performed. We are currently planning further experiments.
Report in the year book 2012
Columns with Optimized Shapes
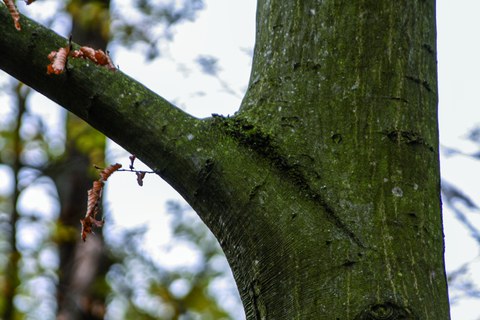
Material addition to reduce stress peaks at a tree fork.
Slim columns are a design feature which is quite popular in contemporary architecture. At the same time, columns are an essential element in their function as load-carrying parts of the supporting structure of buildings. Nonetheless, the columns, which are normally applied, usually have a circular or rectangular cross section which remains unchanged for the entire length of the column. This circumstance offers potential for optimization and is examined in this research project which is part of the DFG priority program 1542 „Leicht Bauen mit Beton“. Structures similar to columns in a building can be found in nature. Thus, tree trunks, which can reach huge heights, represent effective structures in plant life that are clearly related to the structure of columns in engineering. It is the aim of the tree’s trunk and branches to resist the mechanical stress of wind, snow and their own weight as effectively as possible while making use of very little material at the same time.
The trees‘ shape is optimized. Their growth works in such a way as not to create any stress concentrations. They add material in those places which are most heavily loaded. Accordingly, the forks of trees are always rounded and no edges or constant cross sections can be found. In earlier times, attempts were already made to copy this effect in concrete pillars by constructing so-called mushroom columns. In the beginning, work in the research project focussed on stress distribution in the place where concrete pillar and ceiling meet. In an FEM study, a pillar of the kind which is commonly used in buildings was loaded in such a way as is typical. Then, the area where ceiling and pillar meet was examined with regard to changes in load distribution based on different curvatures. The typical angular shape of the connecting element results in significant stress concentrations in the corners. However, even simple triangular material additions lead to a clear reduction of local stresses in these areas. If the triangular shape is replaced by a circular shape, the stress can be reduced still further. An optimized stress curve can be achieved by applying the method of tensile triangles or using an exponential function which is the shape that is closest to nature.