CarboLight Bridge
Project data
Titel | Title CarboLight Bridge als Demonstrator für die SPP1542-Projekte des IMB, TU Dresden | CarboLight Bridge as demonstrator for the SPP1542 projects of the IMB, TU Dresden Förderer | Funding Deutsche Forschungsgemeinschaft (DFG) / SPP 1542 | Institut für Massivbau, TU Dresden | Deutsches Museum München Fertigstellung | Finished 12/2021 Leiter | Project manager Prof. Dr.-Ing. Dr.-Ing. E.h. Manfred Curbach Bearbeiter | Contributors Dipl.-Ing. Marc Koschemann, Iurii Vakaliuk M.Sc. Unterstützer | Supporters HICONFORM – Freitaler Modellwerkstätten eG, Freital | Heidelberger Beton GmbH | Institut für Baustoffe, TU Dresden |
Report in the annual report 2021
Kür was successful. IMB: 12 points!
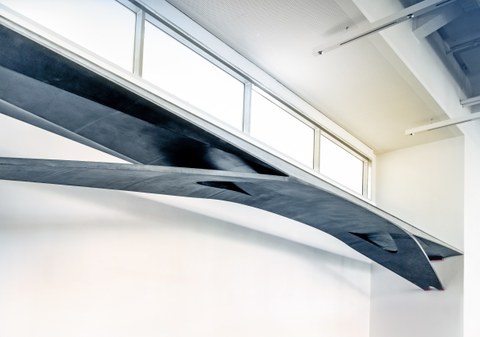
CarboLight Bidge in the Deutsches Museum Munich
Making construction with concrete more resource-efficient and climate-friendly is one of the most important goals in the construction industry. Within the DFG Priority Programme 1542 “Concrete Light”, bionic and mathematical design principles were applied for this purpose to use innovative concretes efficiently. As a demonstrator for this approach, a bridge made of carbon and infra-lightweight concrete was developed at the Institute of Concrete Structures and set up in the refurbished bridge division at the Deutsches Museum in Munich.
The CarboLight Bridge is designed as a filigree construction consisting of two gently inclined columns and a three-sectional superstructure with 9.50 m length and of 1.20 m width. The design and construction possibilities of lightweight construction with concrete and carbon concrete are demonstrated above all by the construction weight of only 2.1 t and the slim V-shaped columns. The force-flow-optimised shape and the sandwich superstructure play a major role in this. The three-layer structure varies in height between 60 mm and 160 mm. The biaxially curved underside and the flat top layer are made of carbon-reinforced concrete 20 mm thick. In between is infra-lightweight concrete with a density of around 800 kg/m³.
Based on the 3D modelling of the bridge, the geometry was optimised in terms of load transfer and design and the moulds were made from milled plywood. To test the assembly, appearance and load-bearing capacity of the carbon concrete bridge and individual segments, an identical test bridge was manufactured in the Otto Mohr Laboratory. After successful testing, five prefabricated segments were transported to the installation site at a height of approx. 3 m in the Deutsches Museum. Employing an adjustable support system, the segments were aligned and the infra-lightweight and the carbon-reinforced concrete top layer were cast on site.
In addition, a tactile exhibit of the superstructure cross-section demonstrates the optimised interaction of carbon and infra-lightweight concrete in this hybrid construction. This ultimately resulted in a significant resource-saving compared to a reinforced concrete structure of comparable load-bearing capacity. Both exhibits will be accessible at the Deutsches Museum from the summer of 2022.
Report in the year book 2020
Ready for the show
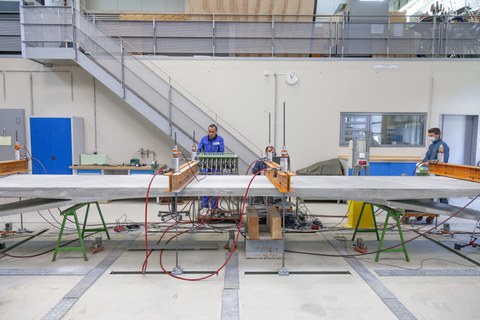
Load test of the test sample of the carbon concrete bridge
As part of the modernization of the Deutsches Museum in Munich, more space is being offered to future-oriented innovations. This will soon include an exhibition bridge made of carbon concrete in the civil engineering section. A first sample was manufactured and successfully tested this year in the Otto Mohr Laboratory at TU Dresden.
With a length of 9.50 m, the carbon concrete bridge is designed as a filigree structure consisting of two gently inclined columns and a three-section superstructure. The design and constructional possibilities of lightweight construction with concrete and carbon concrete are demonstrated above all by the slender V-shaped columns and the construction weight of only 2.1 t. The force-flow-optimized shape and the sandwich structure of the superstructure play a major role in this. The three-layer structure varies in height between 60 and 160 mm. The biaxially curved underside and the flat top layer are made of carbon concrete 20 mm thick. The layer in between is made of infralight concrete with a density of approx. 800 kg/m³.
Based on the 3D modelling of the bridge, the geometry was optimized in terms of load transfer and design. The columns and the bottom shells of the three-part superstructure are manufactured as precast elements, whereas the top concrete layers are poured on-site. Based on the final 3D model, the formwork was manufactured from milled plywood. To test the assembling, appearance and load-bearing capacity of the carbon concrete bridge and individual segments, a test sample of the bridge was manufactured in the Otto Mohr Laboratory during the year. For this purpose, the filigree elements were supported on wooden substructures, massive supports were constructed and a vertical and horizontal adjustable support system was designed. After alignment of the five bridge segments, the boundary formwork was installed, the layer of infralight concrete was poured and the bridge was then completed with the top layer. After removing the temporary supports, the deformation behaviour of the structure under service load was documented over several days and the bridge was finally tested to failure. The applied load of 4 x 1.5 t exceeded 20 times the planned live load and thus also all expectations. After the successful trial run, the real show is about to begin.
The exhibition bridge will be erected at the Deutsches Museum in Munich at the beginning of 2021.
Report in the annual report 2019
LIGHT, LIGHTER, CARBON CONCRETE!
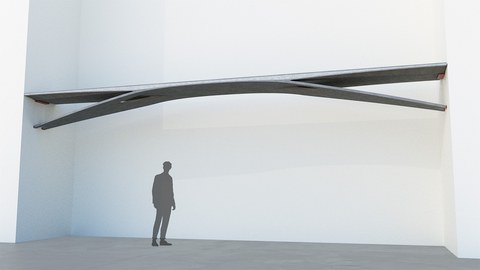
Visualization of the carbon concrete exhibition bridge
Museums are generally regarded as places of the past and offer visitors a historical retrospective. The Deutsches Museum Munich dares to look ahead and offers more space for future-oriented innovations. As part of the reorganisation of the bridge and hydraulic engineering section, a bridge made of carbon concrete will soon be on display.
This bridge is planned as a filigree construction of two slim and inclined columns with a three-section superstructure. Having a total length of 9.50 m, the structure demonstrates the design and fabrication possibilities of lightweight constructions using layered high-performance concrete and carbon reinforcement. The construction weight is only 2.0 t and has a width of 1.20 m. The two v-shaped columns have a length of approx. 3.0 m and are made of carbon concrete with a thickness of 50 mm. In order to increase the stability against possible buckling, a segment with a circular cross-section and a slight elevation in the longitudinal direction were chosen. The superstructure consists of a 3.60 m middle segment and two mirrored edge fields. The construction is made in three layers and varies in height between 60 mm and 180 mm. The biaxial curved underside is produced with a carbon concrete layer of 20 mm. The middle layer consists of infra-light concrete with a density of less than 1,000 kg/m³. A further layer of carbon concrete completes the sandwich structure and provides a flat top surface.
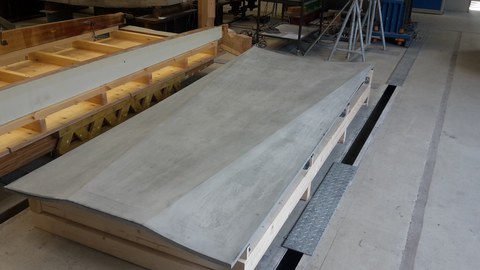
Biaxial curved carbon concrete shell for the underside of the edge fields
A parameterized 3D model of the bridge was created using the Rhino and Grasshopper software to determine the geometry and optimize the load-bearing behaviour. The parameterization enabled a comprehensive variant investigation, starting with the span ratio and ending with detail points such as the connection point between the stem, the midspan and the edge field. By programming an interface to RFEM, all required static calculations were carried out on the same Grasshopper model. By means of this approach, effects resulting from a geometry change on the load transfer could be determined quasi-simultaneously.
The geometry data of the final 3D model formed the basis for the subsequent design and production of the formwork. These were milled from solid plywood panels and then sealed. The first bridge segments have already been successfully manufactured. Technology tests, laboratory experiments and the assembly of the carbon concrete bridge in the Deutsches Museum in Munich are planned for 2020.