UHPC pressure housings made for the deep sea
Table of contents
Project data
Titel | Title TP Untersuchung von UHPC und UHPC-Druckgehäusen unter stoßartiger Belastung, Langzeitbelastung und mehraxialer Beanspruchung im Verbundvorhaben Druckgehäuse aus ultrahochfestem Beton für die Meerestechnik (DeepCsolution) | SP Investigation of UHPC and UHPC pressure vessels under impact loads, long-term loads and multi-axial stresses within the joint research project Ultra-high strength concrete pressure vessels for marine engineering (DeepCsolution) Förderer | Funding BMWK / Maritimes Forschungsprogramm |
Report from year book 2022
One year at the bottom of the polar sea
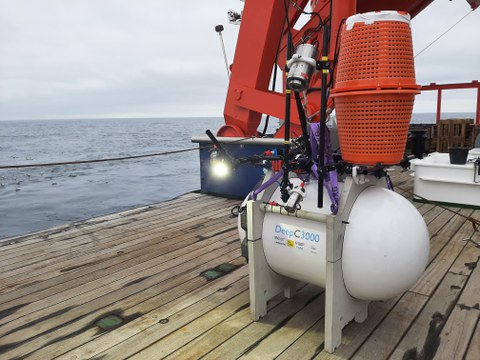
DeepC3000 on board the research ship Maria S. Merian shortly before deployment
To advance the exploration of the seafloor at great depths is the primary goal of the project DeepCsolution. In concrete terms, the aim was to build a robust battery storage system on the seafloor that is capable of storing the required amount of electricity for one year of research operations. The special feature here is that the battery shell was made of ultra-high performance concrete (UHPC). But why UHPC? Normally, concrete is not connected with deep-sea research; titanium or ceramics are usually used here. The reason for choosing concrete resp. UHPC is the size of the pressure casings that can be manufactured. In the case of titanium and ceramics, the outer dimensions are limited because the corresponding semi-finished products can only be manufactured in limited dimensions. As a result, the usable volume is ultimately very limited. However, if UHPC is used, these limits can be significantly exceeded. In the end, the size of the existing formwork now determines the dimensions of the housing, allowing very large usable and storable volumes and thus very large amounts of energy to be available on the seafloor.
In cooperation with the project partners, the realization of such a housing has been worked on during the recent years. This included materials investigations that served to enable the design of the DeepC3000 pressure housing for a deployment depth of up to 3,000 m at the necessary safety level. Before such pressure housings can be used in a real mission in the deep sea, they have to be put through their paces. For this purpose, the concrete housings were tested in a pressure tank at the University of Rostock under an external pressure of up to 420 bar and tested for load-bearing capacity as well as leak tightness. This pressure corresponds to a sea depth of about 4,200 m. After passing all tests, a DeepC3000 was equipped with batteries and measurement technology and released into the polar sea at a depth of about 2,500 m, where it will remain until the middle of 2023. After recovery, the measurement data can be evaluated.
Report from year book 2021
3,000 metres below sea level
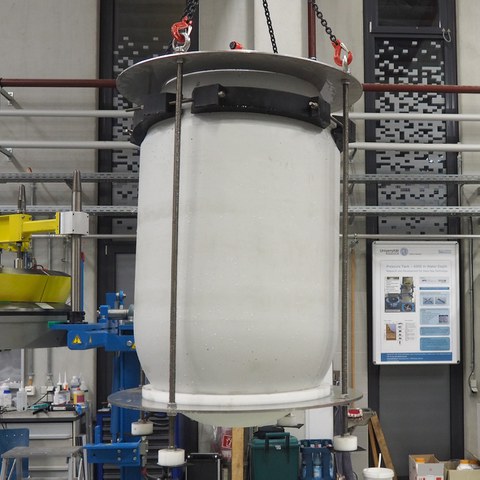
Concrete pressure vessel on hook, ready for testing
It is generally known that water, especially salt or seawater, causes corrosion of steel components. Corrosion-resistant stainless steels were developed to prevent this. However, these steels cannot withstand corrosion in seawater for very long. This is a major problem, especially in deep-sea research. To supply the measuring points with energy over long periods of time, highly robust and corrosion-resistant pressure vessels are necessary.
For this reason, a lot of work has been done with titanium vessels so far, as titanium has a very high mechanical strength and a very good corrosion resistance. However, the main disadvantages of this material are a very high production price and difficult workability. Ultra-high performance concrete (UHPC) with a compressive strength of 130 MPa and more is a viable alternative. Concrete can be cast in a variety of shapes when fresh and is extremely strong when cured. UHPC thus has very good workability and strength properties. In addition, there is the corrosion resistance of concrete. This makes concrete an ideal material for such pressure housings. The main disadvantage of concrete is that its tensile strength is only a small fraction of the compressive strength. However, this can be compensated for by careful planning. The test specimens examined in the DeepCsolution project were designed in such a way that tensile stresses were minimized and therefore no longer represent a problem.
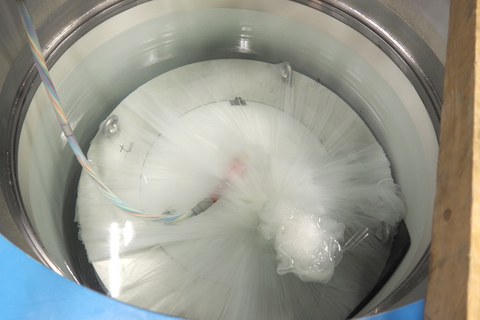
Concrete pressure vessel in the pressure tank of the University of Rostock
However, carrying out all these considerations only theoretically is not sufficient to prove the functionality of such a pressure vessel. For this reason, component tests were carried out in 2021 at the Chair of Ocean Engineering of the University of Rostock. During these tests, the concrete pressure vessels were subjected to a test pressure of 330 bar, which corresponds to a water depth of 3,300 m. The concrete pressure vessel made of UHPC has passed this component test and can now be used. For this purpose, a long-term mission is being planned in cooperation with the Alfred-Wegener- Institute (AWI), in which such a concrete pressure vessel is to be used as a protective battery shell.
Report from year book 2020
Concrete for deep ocean
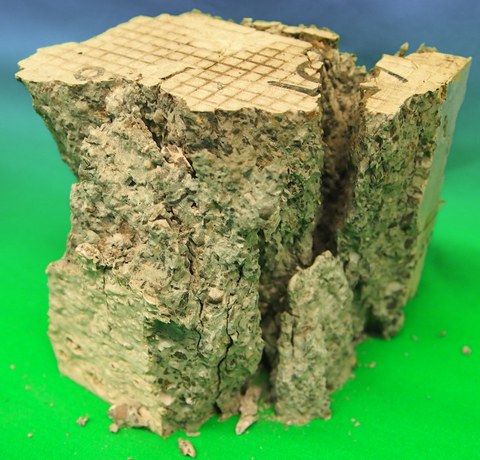
Remains of a concrete cube after the compression strength test with load brushes
Wherever we look, concrete has become an integral part of our everyday lives. The main area of application for concrete is in building structures, as it is an inexpensive material that can be shaped into almost any form. Depending on the mix, it has a very high compressive strength. Concrete with a compressive strength higher than 100 MPa (measured in a cylinder test), is referred to as UHPC (ultra-high performance concrete). However, concrete has an essential disadvantage: no matter how high the compressive strength of the concrete is, the tensile strength only reaches a percentage of this value.
This heterogeneity between compressive and tensile strength poses a challenge for the use of concrete outside the building industry. However, if care is taken from the outset in the development of concrete structures to ensure that almost only compressive stresses arise in the material due to an external load, it is possible to use concrete effectively outside the building industry. The first steps in this direction were taken with the already completed ROBEX project. Here, a small-scale pressure vessel made of UHPC was developed for the deep sea, which can withstand extreme pressure at great depths. By optimising the shape of the housing, tensile stresses were nearly eliminated, allowing the potential of concrete to be fully utilised. In the current project, the aim is to work together with the project partners to revisit the concept of the concrete pressure vessel, develop it further and implement it on a much larger scale. The project aims to develop a pressure vessel made of UHPC that can be used up to a diving depth of 3,000 m. The primary function of this pressure vessel will be to provide a pressure chamber that can be used as a pressure vessel. The primary function of this pressure vessel in the intended test mission will be to provide an energy source in the form of a battery on the seabed to operate measurement technology for deep-sea research.
To achieve this goal, the material properties of the planned UHPC must be investigated in a variety of possible loading scenarios. On the one hand, the uniaxial and multiaxial material properties of the UHPC must be determined for the basic design of the housing. Furthermore, the multi-axial creep behaviour of the concrete is of interest, as this has to be taken into account for the design of the sealing system.