Wirkmedienbasierte Blechumformung mit formgebenden Werkzeugen aus HPC
Inhaltsverzeichnis
Projektdaten
Titel | Title |
Kurzbeschreibung
Im Rahmen dieses Forschungsvorhabens werden gemeinsam mit unserem Kooperationspartner, dem Institut für Umformtechnik und Leichtbau der Universität Dortmund, formgebende Umformwerkzeuge aus Betonwerkstoffen für wirkmedienbasierte Umformverfahren entwickelt und erforscht. Aus einem stahlfaserbewehrten Feinkornbeton der sich durch hohe Festigkeit, einen hohen Elastizitätsmodul sowie hohe Dichtheit und hohe Abriebfestigkeit der Oberfläche auszeichnet, wurden ein formgebendes Werkzeug ohne und eines mit Umschnürung hergestellt. Die Umschnürung dient dazu, einen Querdruck auf das Werkzeug auszuüben, um im Beton einen mehraxialen Druckspannungszustand hervorzurufen. Durch diesen mehraxialen Druckspannungszustand wird die Druckfestigkeit gegenüber der Druckfestigkeit bei einaxialer Beanspruchung gesteigert und ermöglicht somit eine höhere Beanspruchbarkeit der Betonwerkzeuge. Die durchgeführten Versuche haben gezeigt, dass das Umformwerkzeug ohne Umschnürung bereits bei einem Umformdruck von rund 95 MPa versagte, während das Werkzeug mit Umschnürung bis zu einem Umformdruck von 100 MPa noch keine sichtbare Schädigung aufwies. Der Umschnürungsdruck betrug hierbei 20 MPa. Für eine effektive Gestaltung der Umformwerkzeuge ist es notwendig Simulationen von Umformprozessen mit Werkzeugmatrizen aus Betonwerkstoffen mittels FE-Analyse durchzuführen. Hierfür muss das Werkstoffverhalten des Betons bis zu seiner Beanspruchungsgrenze beschrieben und bei einer Simulation berücksichtigt werden. Die Versuche am Umformwerkzeug ohne Umschnürung haben gezeigt, dass eine Druck-Druck-Zug-Beanspruchung in einem Teilbereich des Werkzeugs zum Versagen führte. Bei der Bestimmung des Werkstoffverhaltens wird daher diese spezielle Beanspruchung untersucht. Um die erwarteten kleinen Probekörperverformungen messen zu können, wurde eine Messmethode entwickelt, bei der mittels Faser-Bragg-Gitter-Sensoren die Dehnungen im Probekörper gemessen werden. Die Ausführung der Fasern aus dem Probekörper erfolgt auf einer Fläche von maximal 5mm x 5mm. Diese Fläche wird durch die verwendeten Lasteinleitungsmittel vorgegeben und beträgt weniger als 1% von einer der belasteten Seitenflächen des 10cm x 10cm x 10cm großen Probekörperwürfels. Die insgesamt sechs Sensoren sind auf den Kanten eines tetraederförmigen Trägergerüstes appliziert. Durch Transformation der gemessenen Dehnungen können die Dehnungen in Normalrichtung sowie die Schubverzerrungen bestimmt werden. Mit der entwickelten Messmethode wird eine Versuchsserie mit dreiaxialen Druck-Druck-Zug-Beanspruchungen durchgeführt und anhand der Messergebnisse das Materialverhalten beschrieben.
Bericht aus dem Jahrbuch 2013
Blechumformung mit Betonwerkzeugen
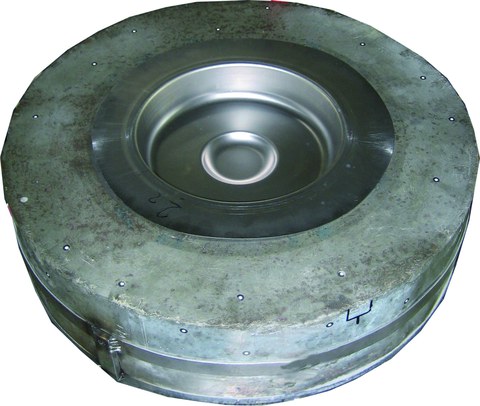
Betonwerkzeug mit einer Napfgeometrie mit Nebenformelement und umgeformtes Blech.
Die steigende Zahl von unterschiedlich geformten Blechen, speziell in kleinen und mittleren Fertigungsserien, bedingt die Entwicklung von effizienten Umformprozessen und wirtschaftlichen Herstellungsverfahren für Umformwerkzeuge. Im Bereich der wirkmedienbasierten Blechumformung ist Ultrahochleistungsbeton mit einaxialen Druckfestigkeiten von über 150 N/mm² für die Herstellung von Werkzeugmatrizen eine Alternative zu konventionell eingesetzten metallischen Werkstoffen.
Mit einem feinkörnigen stahlfaserbewehrten Ultrahochleitungsbeton konnte die Eignung von Beton als Werkstoff für formgebende Matrizen bei der wirkmedienbasierten Hochdruck- und Innenhochdruckblechumformung gezeigt werden. Bei der Hochdruckblechumformung wurden ab Umformdrücken von 50 N/mm² gute Umformergebnisse erzielt. Das weitere Steigern des Druckes führte nur noch zu geringfügigen Verbesserungen der Konturgenauigkeit der geformten Bleche. Beim Traglasttest versagte das Werkzeug schließlich bei einem Wirkmediendruck von 96,5 N/mm².
Während der Blechumformung treten in einem solchen Werkzeug mehraxiale Spannungszustände auf. Diese haben in Abhängigkeit von der Spannungskombination eine festigkeitssteigernde oder -mindernde Wirkung auf den Beton, woraus sich die Beanspruchbarkeitsgrenze des Umformwerkzeugs ergibt. Aufgrund der eher geringen Zugfestigkeit von Beton führen mehraxiale Zug-Druck-Druck-Spannungszustände in der Werkzeugmatrize zur Überschreitung dieser Grenze. Dabei ist nicht die maximale Festigkeit, sondern die der Elastizitätsgrenze maßgebend, da für die Herstellung konturgleicher Bleche keine plastischen Verformungen im Werkzeug auftreten dürfen. Will man die Einsatzmöglichkeiten von Betonmatrizen bei Umformprozessen abschätzen bzw. die Matrizengeometrie mit Hilfe von Simulationen effizient gestalten und optimieren, muss das Materialverhalten unter mehraxialen Spannungszuständen bekannt sein. Zur Bestimmung dieses Materialverhaltens wurden mehraxiale Belastungsversuche mit vorrangiger Betrachtung von Zug-Druck-Druck-Beanspruchungen durchgeführt.
Aus den gemessenen Spannungs-Dehnungs-Linien wurden jeweils ein Modell zur Beschreibung der Festigkeitsgrenzfläche an der Elastizitätsgrenze und der maximalen Festigkeit sowie des Spannungs-Dehnungs-Verhaltens abgeleitet. Diese Ergebnisse sollen nun in ein FE-Programm überführt und für Simulationen von Umformprozessen genutzt werden.
Bericht aus dem Jahrbuch 2012
Blechumformung mit Betonmatrizen
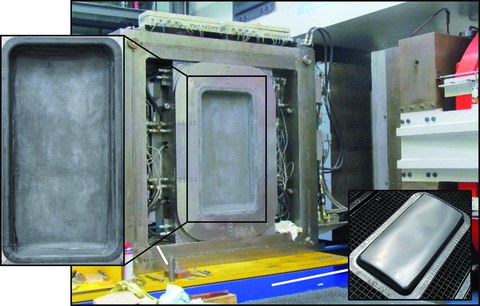
Großformatiges Betonwerkzeug in einer Hochdruckblechumformungspresse
Die Umformung von Blechen erfolgt mit Werkzeugmatrizen, die die spätere Kontur des Bleches vorgeben. Beim konventionellen Tiefziehen werden dafür eine Matrize und ein Stempel benötigt, wobei der Stempel das Blech in die Matrize drückt. Bei wirkmedienbasierten Umformverfahren wird die Aufgabe des Stempels von einem flüssigen Wirkmedium übernommen, was vorteilhaft für den Umformprozess ist. Außerdem lässt sich Material einsparen, da kein Stempel benötigt wird. Ziel des Forschungsvorhabens ist es, die im Allgemeinen aus Stahl oder Legierungen hergestellten Matrizen durch Umformwerkzeuge aus hydraulisch gebundenem Beton zu ersetzen, um somit die Effizienz der wirkmedienbasierten Blechumformung speziell bei Klein- und Kleinstserien noch weiter zu steigern.
Die prinzipielle Eignung eines feinkörnigen ultrahochfesten Betons mit Stahlfaserbewehrung konnte an kleinen Umformwerkzeugen mit einfachen Geometrien bereits im Vorjahr nachgewiesen werden, weshalb der Schwerpunkt der aktuellen Forschung auf der Erweiterung des Anwendungsfeldes für derartige Betonwerkzeuge liegt. Zum einen wird der Einsatz des Betons bei großformatigen Umformwerkzeugen mit komplexeren Geometrien und zum anderen bei einem zweiten Umformverfahren, der Innenhochdruckumformung, untersucht.
Die Versuche mit einem großformatigen Betonwerkzeug mit einer Wannengeometrie ergaben gute Umformergebnisse und zeigen, dass mit einer Betonmatrize gleichwertig geformte Bleche hergestellt werden können. Mit einem seitlichen Stützdruck an den Werkzeugrändern lässt sich die Beanspruchbarkeit der Matrize signifikant erhöhen. Hierbei ist es ausreichend, wenn der Stützdruck passiv wirkt und durch ein formschlüssiges Anliegen des Werkzeugs in einer umlaufenden Werkzeugaufnahmevorrichtung der Presse hervorgerufen wird, wie es z. B. auch bei der Innenhochdruckumformung erfolgt.
Bei diesem Umformverfahren wird das aus zwei Hälften bestehende formgebende Werkzeug in den Aufnahmevorrichtungen der Presse formschlüssig fixiert und das zu formende Halbzeug, z. B. ein Rohr, zwischen diesen beiden Hälften platziert. Das Wirkmedium gelangt nach dem Schließen der Presse über eine Öffnung in den Innenraum des Halbzeugs, welches sich mit steigendem Umformdruck an die Kontur der Matrize anlegt. Wie schon bei der wirkmedienbasierten Blechumformung können auch bei der Innenhochdruckumformung mittels Betonmatrizen Blechteile mit gleichwertiger hoher Konturgenauigkeit hergestellt werden.
Bericht aus dem Jahrbuch 2011
Formgebende Werkzeuge aus hydraulisch gebundenen Werkstoffen
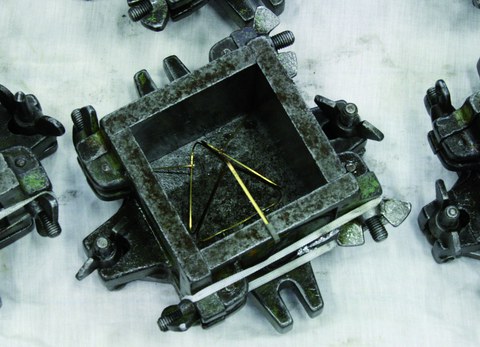
Tetraederträgergerüst in einer Würfelform vor der Betonage
Durch die Entwicklung von ultrahochfesten Betonen eröffnen sich hydraulisch gebundenen Materialien neue Anwendungsfelder. So können zum Beispiel formgebende Matrizen aus Beton bei der wirkmedienbasierten Blechumformung eingesetzt werden, die gegenüber Stahlmatrizen speziell bei Klein- und Kleinstserien Vorteile bieten. Durch die gießtechnische Herstellung der Matrizen in konturgebenden Formen bedürfen sie keiner weiteren Nachbearbeitung und sind durch eine spezielle Wärmenachbehandlung 24 Stunden nach der Betonage einsatzbereit. Versuche haben gezeigt, dass mit Betonmatrizen Umformerzeugnisse mit der gewünschten Maßgenauigkeit bis zu einem Umformdruck von 80 MPa erzielt werden können.
Für eine effiziente Gestaltung ist es notwendig, den Umformprozess durch wirklichkeitsnahe Berechnungen vorab zu simulieren, um positive Materialeigenschaften wie die Festigkeitssteigerung bei mehraxialen Druckspannungszuständen auszunutzen oder negative Eigenschaften wie die geringe Zugfestigkeit zu berücksichtigen. Für eine realitätsnahe Simulation ist das implementierte Materialgesetz des verwendeten Betons von großer Bedeutung. Da davon ausgegangen wird, dass ein Versagen der Matrize durch das Überschreiten der Zugfestigkeit unter einer mehraxialen Beanspruchung erfolgt, werden derzeit dreiaxiale Zug-Druck-Druck-Versuche an würfelförmigen Prüfkörpern durchgeführt, um die maximale Beanspruchbarkeit sowie das Verformungsverhalten des Betons zu bestimmen. Zur Ermittlung der Dehnungen erfolgt vor der Betonage eine tetraederförmige Anordnung von sechs Faser-Bragg-Gitter-Sensoren auf einem Trägergerüst in der Betonierform, von denen vorab nachgewiesen wurde, dass sie nahezu keine Auswirkungen auf das Materialverhalten haben.
Aus den Messwerten werden die Normaldehnungen berechnet. Die bisherigen Ergebnisse zeigen, dass der verwendete Beton beim Auftreten einer Zugspannungskomponente, die die größte Beanspruchung aller drei Richtungen darstellt, ein lineares Materialverhalten bis zum Versagen aufweist. Unter der Zunahme der Druck- und Abnahme der Zugbeanspruchung stellt sich bei Belastungen nahe der maximalen Festigkeit ein zunehmender Bereich nichtlinearen Materialverhaltens ein. Um eine möglichst hohe Beanspruchbarkeit im Bereich des linear-elastischen Materialverhaltens zu erreichen, sollten aufgrund der geringen Zugfestigkeit des Betons mehraxiale Spannungszustände mit großen Zugspannungskomponenten vermieden werden.
Bericht aus dem Jahrbuch 2010
Werkzeugmatrizen für wirkmedienbasierte Blechumformverfahren
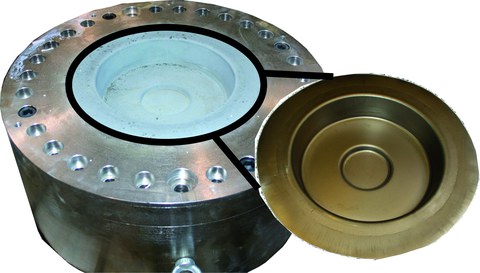
Umformwerkzeug mit Umschnürung zum aktiven Aufbringen eines seitlichen Druckes auf die Betonmatrize und umgeformtes Blech
In diesem Projekt werden formgebende Werkzeugmatrizen aus hydraulisch gebundenen Werkstoffen für wirkmedienbasierte Blechumformverfahren entwickelt und deren Materialverhalten wirklichkeitsnah simuliert. Gute Ergebnisse wurden mit einer Werkzeugmatrize aus einem feinkörnigen stahlfaserbewehrten Ultrahochleistungsbeton erzielt, mit der bei einem Wirkmediendruck (Umformdruck) von bis zu 80 MPa mehrere konturgleich geformte Bleche hergestellt werden konnten.
Die Beanspruchbarkeit eines Betonwerkzeugs kann bei Ausnutzung der festigkeitssteigernden Wirkung eines mehraxialen Druckspannungszustandes erhöht werden. Deshalb wurde eine zweite Matrize mit einer Umschnürung entwickelt, die es erlaubt, einen seitlichen Druck von bis zu 20 MPa aktiv auf das Werkzeug auszuüben. So konnten bisher Bleche bis zu einem Umformdruck von 100 MPa geformt werden, ohne dass an dem Werkzeug Anzeichen plastischer Verformungen auftraten. In weiteren Versuchen soll die Grenze des maximal realisierbaren Umformdrucks ermittelt werden.
Für eine effiziente Gestaltung der Matrizen ist es wichtig, den Umformprozess mit materialspezifischen Last-Verformungs-Beziehungen zu simulieren. Aus den Versuchsergebnissen der Matrize ohne Umschnürung wurde geschlussfolgert, dass ein dreiaxialer Druck-Druck-Zugspannungszustand zum Versagen des Werkzeugs führt. Für diese Beanspruchungsart sind daher Versuche an würfelförmigen Probekörpern geplant. Zur Erfassung der Probekörperverformungen wird derzeit eine Messmethode entwickelt, bei der die Verformungen des Materials nicht wie bisher indirekt über die Lasteinleitungsmittel, sondern im Innern des Probekörpers selbst bestimmt werden. Dazu werden Fasern mit eingeschriebenen Bragg-Gittern, appliziert auf ein tetraederförmiges Trägergerüst, in die Probe einbetoniert. Zur Verifizierung der Messmethode wurden bereits einaxiale Druck- und Zugversuche durchgeführt, bei denen die Verformungen gleichzeitig auch mit Dehnmessstreifen gemessen wurden. Die Versuche zeigten, dass Faser-Bragg-Gitter geeignet sind, kleine Probekörperverformungen zu messen. Die Untersuchungen ergaben außerdem, dass die Inhomogenität des Feinkornbetons keine Auswirkung auf die Dehnungsmessung der nur 5 mm langen Bragg-Gitter hat bzw. dass die Messergebnisse in der gleichen Größenordnung wie die herkömmlicher Dehnmessstreifen streuen. Zur abschließenden Verifizierung der Messmethode werden Faser-Bragg-Gitter in Probewürfel einbetoniert und mit den Messwerten der auf der Probekörperoberfläche applizierten Dehnmessstreifen verglichen.
Bericht aus dem Jahrbuch 2009
Formgebende Werkzeuge aus hydraulisch gebundenen Werkstoffen
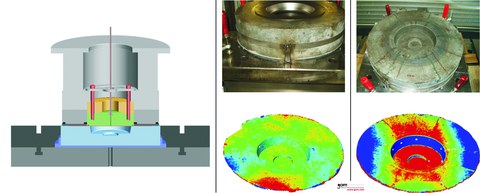
Konfiguration des Umformprozesses und plastische Verformungen des Werkzeugs nach Beaufschlagung mit unterschiedlichen Umformdrücken
Die steigende Zahl von unterschiedlich geformten Blechen, speziell in kleinen und mittleren Fertigungsserien, bedingt die Entwicklung von effizienten Umformprozessen und wirtschaftlichen Herstellungsverfahren für Umformwerkzeuge. Im Rahmen dieses Forschungsprogramms wird der Einsatz von formgebenden Werkzeugen aus hydraulisch gebundenen Werkstoffen für die wirkmedienbasierte Blechumformung untersucht.
Eine Druckfestigkeit von über 100 MPa und eine glatte und dichte Oberfläche sind die Grundvoraussetzungen für den Einsatz eines Betons zur Herstellung von Unformwerkzeugen. Für die Umsetzung eines Prototypenwerkzeugs wurde ein feinkörniger stahlfaserbewehrter Beton verwendet.
Mit dem Prototypenwerkzeug umgeformte Bleche zeigten gute Ergebnisse. Ab einem Umformdruck von 60 MPa konnte ein Radius von 2,5 mm ausgeformt werden. Erste Risse im Werkzeug traten bei einem Umformdruck von 80 MPa auf und bei einem Druck von 95 MPa versagte es vollständig.
Eine Möglichkeit, die Beanspruchungsgrenze zu steigern, ist, einen Umschnürungsdruck auf das Werkzeug auszuüben. Versuche an zylindrischen Proben zeigten, dass passive Umschnürungen, d. h. Umschnürungen, die den Umschnürungsdruck nur durch Querdehnungsbehinderung hervorrufen, keinen nennenswerten Effekt erzielten. Getestete passive Umschnürungen wurden durch eine Bewehrungswendel, eine Carbon-Sheet Umwicklung und durch ein Stahlrohr realisiert. Vergleichend zu den passiven Umschnürungen wurden mehraxiale Druckfestigkeitsprüfungen an kubischen Proben mit unterschiedlichen Probenaltern durchgeführt. Der Betrag des Umschnürungsdrucks betrug 10 % der Hauptbelastung. Die erzielte Steigerung der Beanspruchungsgrenze des Materials, verglichen mit Versuchswerten ohne Umschnürungsdruck, betrug 100 % nach drei Tagen und 20 % nach 28 Tagen.
Eine weitere positive Beeinflussung erfolgt durch eine Wärmenachbehandlung des Betons direkt nach dem Betonieren. Es konnten vorteilhafte Materialeigenschaften wie der hohe Elastizitätsmodul oder die Druckfestigkeit zu einem sehr frühen Zeitpunkt weiter gesteigert werden. Durch die Wärmenachbehandlung ist das Umformwerkzeug 48 h nach der Betonage einsatzbereit. Außerdem wird der Vorgang des Schwindens während der Nachbehandlung beschleunigt, sodass anschließende Schwindverformungen vernachlässigbar sind.
Es wurde ein weiteres Werkzeug entwickelt, welches von einer universellen Umschnürung eingefasst ist. Der maximal aufbringbare Querdruck beträgt 20 MPa. Vor dem Applizieren des Umschnürungssystems wurde das Werkzeug wärmenachbehandelt.