C3-V1.1-X-d: Nachbehandlungsmethoden sowie An- und Einbauteile
Projektdaten
Titel | Title |
Bericht aus dem Jahrbuch 2018
THERMOANKER - INNOVATIV UND TRAGFÄHIG!
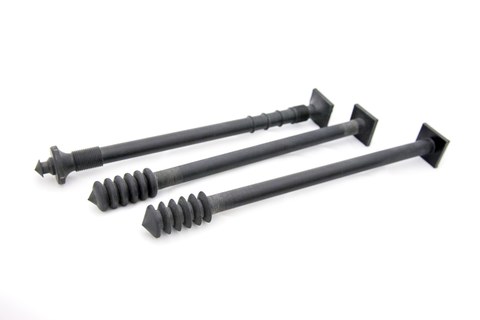
Es war ein langer Weg, bis die finale Form des Thermoankers (vorn im Bild) gefunden war
Das Verbundvorhaben C3-V1.1 „Entwicklung von Herstell- und Verarbeitungsprozessen von Carbonbeton“ hatte zum Ziel, Markteintrittsbarrieren für Carbonbeton zu minimieren bzw. gänzlich zu eliminieren. Dies betrifft auch die automatisierte Herstellung von (Halb-)Fertigteilen im Betonfertigteilwerk. Die Anpassung der für Stahlbetonstrukturen bewährten Fertigungsprozesse an dünnere Betonelemente und engmaschigere, nichtmetallische Bewehrung war allerdings nicht die einzige Herausforderung.
Eine Thermodoppelwand diente als Referenzbauteil im Projekt. In der Stahlbetonvariante besteht diese Wand aus zwei Betonschalen von sechs bis sieben Zentimetern Dicke. Zwischen diesen Schalen befinden sich eine werksseitig aufgebrachte Wärmedämmung und ein Hohlraum zur Verfüllung mit Ortbeton. Die Verbindung beider Schalen erfolgt über einen sogenannten Thermoanker. Das Ziel war es, die Stahlbetonschalen durch nur drei Zentimeter dünne Carbonbetonschalen zu ersetzen. Da diese Einbindetiefe für herkömmliche Thermoanker jedoch zu gering ist, wurde im Projekt ein neuartiger Thermoanker entwickelt. Mit dem Entwurf des Thermoankers galt es, mehrere Hürden gleichzeitig zu überwinden. Zum einen sollte dieser so ausgeführt werden, dass er herstelltechnologisch optimal in den vollautomatischen Fertigungsprozess integriert werden kann und geometrisch an die engmaschige textile Bewehrung angepasst ist. Zum anderen musste er bauphysikalischen und mechanischen Anforderungen genügen.
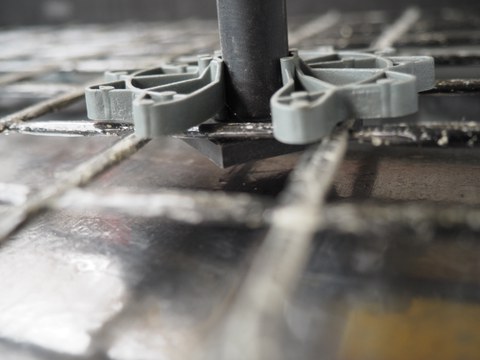
Ein Ende des Thermoankers dient gleichzeitig als Abstandhalter für die textile Bewehrung, eine handelsübliche Klemme kann zur Befestigung genutzt werden
In mehreren Herstellversuchen im Fertigteilwerk wurde die Geometrie des Thermoankers optimal an den Herstellprozess angepasst, sodass letztendlich dessen Tragfähigkeit in Laborversuchen untersucht werden konnte. Hierfür wurde an kleinteiligen Probekörpern der Verbund beider Enden des Einbauteils zum Beton in Längszug-, Längsdruck- und Querzugversuchen untersucht. Da die Belastung des Bauteils im Fertigteilwerk bereits am ersten Tag nach der Herstellung erfolgen kann, wurden, zusätzlich zu den üblichen 28 Tagen, ausgewählte Versuche bereits einen Tag nach der Herstellung durchgeführt. Um die Ergebnisse einordnen zu können, erfolgten zusätzlich Versuche am Thermoanker für Stahlbetondoppelwände in einer dünnen Carbonbetonschicht. Diese Versuche ergaben, dass mit dem neuen Thermoanker fast doppelt so hohe Kräfte übertragen werden können wie im Vergleich zu der herkömmlichen Stahlbetonlösung.
Bericht aus dem Jahrbuch 2017
EINBAUTEILE FÜR CARBONBETON
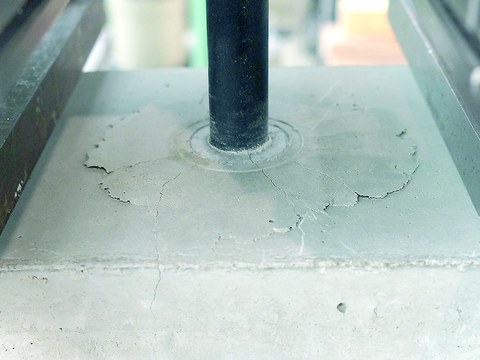
Zugversuch an einem Einbauteil zur parallelen Verbindung von Carbonbetonbauteilen
Das Verbundvorhaben C3-V1.1 „Entwicklung von Herstell- und Verarbeitungsprozessen von Carbonbeton“
im Verbundforschungsvorhaben C³ – Carbon Concrete Composite hat sich die Optimierung von Herstellprozessen von Carbonbeton zum Ziel gesetzt. Neben einer wirtschaftlichen Herstellung und definierten, hochwertigen Oberflächen-qualitäten steht auch die Automatisierung der Herstellung von Carbonbetonbauteilen im Betonfertigteilwerk im Vordergrund. Zugehörig hierzu ist auch die Entwicklung von Ein- und Anbauteilen für Carbonbetonfertigteile.
Da in der Carbonbetonbauweise dünnere und filigranere Bauteile angestrebt werden, als man es aus dem Stahlbetonbau gewohnt ist – minimale Bauteildicken von 3 cm sind das Ziel –, sind bekannte und bewährte Ein- und Anbauteillösungen nicht mehr ohne Weiteres verwendbar. Im Vorhaben wurden sowohl Einbauteile zur parallelen Verbindung von Bauteilen als auch für Längs- und Übereckverbindungen entwickelt. Die bisher bekannten Lösungen hierfür erforderten Wandstärken von mindestens 5 cm. Neben den mechanischen Aspekten mussten bei der Entwicklung der Einbauteile auch bauphysi-kalische und herstellungsbedingte Aspekte berücksichtigt werden.
Wärmebrücken sollten vermieden und eine reibungslose Herstellung im Fertigteilwerk musste garantiert werden. Nach der Optimierung der Einbauteile bezüglich deren Anwendbarkeit im Fertigteilwerk wird nun deren Tragfähigkeit im Hinblick auf verschiedene Beanspruchungsrichtungen untersucht. Neben Längszug- und -druckversuchen sollen auch Querzugversuche an den sowohl flächig als auch stirnseitig eingebauten Einbauteilen durchgeführt werden. Hierfür werden diese in Probekörper, bestehend aus einem mit Epoxidharz beschichteten Carbongelege und einer hochfesten Betonmischung, einbetoniert. Da die Belastung von Einbauteilen im Fertigteilwerk schon bereits am ersten Tag nach der Herstellung erfolgen kann, werden ausgewählte Tragfähigkeitsuntersuchungen bereits nach einem Tag statt nach den üblichen 28 Tagen nach der Herstellung durchgeführt.
Anhand der Ergebnisse der Tragfähigkeitsuntersuchungen kann letztendlich eine Aussage über die Anwendbarkeit der Einbauteile in dünnen Carbonbetonbauteilen getroffen werden. Bei Bedarf können weitere Optimierungen vorgenommen werden. Ziel des Projektes ist die Errichtung eines Demonstratorbauteils unter realen Fertigungs-bedingungen.
Bericht aus dem Jahrbuch 2016
Aus Vergangenem lernen
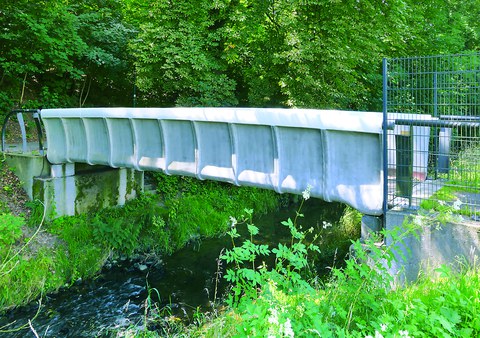
Auch die Oberfläche der Textilbetonbrücke in Oschatz wurde genau unter die Lupe genommen, im Bild zu sehen der Eingangsbereich mit Drehtür.
Carbonbeton dürfte inzwischen für niemanden mehr ein Fremdwort sein. Seit zwei Jahrzehnten wird an seinem Vorgänger – dem Verbundwerkstoff Textilbeton – geforscht. Im Zuge dieser Forschung sind etliche Praxisanwendungen entstanden. Um allerdings eine wirtschaftliche Herstellung und definierte, hochwertige Oberflächenqualitäten von Carbonbetonbauteilen zu erzielen, müssen dessen Herstellprozesse, vor allem im Fertigteilwerk, bis zur Anwendungsreife weiterentwickelt werden. Hier knüpft das Verbundvorhaben C3-V1.1 „Entwicklung von Herstell- und Verarbeitungsprozessen von Carbonbeton“ im Verbundforschungsvorhaben C³ an.
Zu Projektbeginn wurden hierfür bereits ausgeführte Projekte in Textilbetonbauweise begutachtet und die Auswirkungen bestimmter Herstellungs- und Materialparameter auf deren Oberflächenqualitäten untersucht. Unter den untersuchten Projekten befanden sich vier Instandsetzungs- bzw. Verstärkungsmaßnahmen, acht Tragwerke und acht Fassadenverkleidungen, welche in ganz Deutschland realisiert worden waren.
Die Auswertung der Ergebnisse der Begutachtung ergab, dass unter anderem die Parameter Betonzusammensetzung, Nachbehandlung und Nachbearbeitung eine Auswirkung auf die Qualität der Oberflächen haben. So traten beispielsweise Schwindrisse häufiger auf, wenn das Größtkorn des verwendeten Betons kleiner als 4 mm im Durchmesser maß. Ein Abzeichnen des in den Beton eingelegten Textils trat seltener bei Betonüberdeckungen von 5 mm oder größer auf. Aber auch die Dauer der Nachbehandlung und die Art der Nachbearbeitung der Oberflächen haben einen Einfluss auf deren Qualität. So traten die besagten Schwindrisse umso seltener auf, je länger die Oberflächen nachbehandelt bzw. die Bauteile in der Schalung belassen worden waren. Eine lange Nachbehandlung oder Verweildauer in der Schalung können allerdings auch zu fleckigen Oberflächen führen. Flecken ließen sich jedoch nie an abgesäuerten Oberflächen entdecken.
Die Ergebnisse aus der Begutachtung der bereits ausgeführten Praxisprojekte dienen als Grundlage für das nun geplante Versuchsprogramm. Innerhalb des Projekts sollen z. B. im kommenden Jahr 2017 die Auswirkungen verschiedener Nachbehandlungs- und Nachbearbeitungsmethoden auf die Oberflächenqualität von Neubauteilen und verstärkten Flächen aus Carbonbeton unter einheitlichen Randbedingungen untersucht werden.