C3-V1.1-X-d: Post-treatment methods as well as built-in parts
Project data
Titel | Title TP C3-V1.1-X-d: Untersuchung von Nachbehandlungsmethoden zur Sicherstellung einer dauerhaften Oberfläche und Beitrag zur Konstruktion von An- und Einbauteilen für Carbonbeton im Verbundvorhaben C3-V1.1: Entwicklung von Herstell- und Verarbeitungsprozessen von Carbonbeton | TP C3-V1.1-X-d: Investigation of post-treatment methods to ensure a durable surface and contribution to the construction of built-in parts for carbon reinforced concrete as part of the joint research project C3-V1.1: Development of manufacturing and workmanship processes of carbon concrete composite Förderer | Funding Bundesministerium für Bildung und Forschung (BMBF); Projektträger: PT Jülich / C3 – Carbon Concrete Composite Zeitraum | Period 12.2015 - 03.2018 Leiter Teilvorhaben | Subproject manager Prof. Dr.-Ing. Dr.-Ing. E.h. Manfred Curbach Bearbeiter | Contributor Dipl.-Ing. Juliane Wagner Projektpartner | Project partners Institut für Betonbau, HTWK Leipzig (Verbundkoordinator) | Baustoffprüflabor Müller und Lobisch GmbH, Dreiheide | Betonwerk Oschatz GmbH | Clement Germany GmbH, Rostock | EnergieAutark GmbH, Delitzsch | FISSEK GmbH, Mylau | Hentschke Bau GmbH, Bautzen | Implenia Construction GmbH, Leipzig | Institut für Baubetriebswesen, TU Dresden | Institut für Baustoffe, TU Dresden | Institut für Leichtbau und Kunststofftechnik, TU Dresden | Institut für Textilmaschinen und Textile Hochleistungswerkstofftechnik, TU Dresden | Institut für Werkzeugmaschinen und Steuerungstechnik, TU Dresden | Sächsisches Textilforschungsinstitut e.V., Chemnitz | Unger Bau-Systeme GmbH, Chemnitz |
Report from the annual report 2018
THERMAL ANCHOR - SMART AND STABLE!
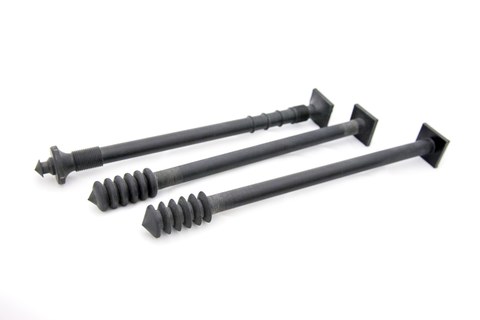
It was a long way until the final shape of the thermal anchor (front in the picture) was found
The aim of the joint research project C3-V1.1 „Development of manufacturing and workmanship processes of carbon reinforced concrete” was to minimize or rather completely eliminate market entry barriers for carbon reinforced concrete (CRC). An example of this is the automation of the manufacturing process of precast and semi-finished elements. However, the adaptation of the well-known manufacturing processes from steel reinforced concrete to thinner concrete structures and close-meshed, non-metallic reinforcement was not the only challenge.
A double wall was used as a reference structure within the project. Built out of steel reinforced concrete, this wall consists of two concrete shells with a thickness of six to seven centimetres. In between these shells, there is thermal insulation and a cavity to be filled by in-situ concrete. The connection of the two shells is done by a thermal anchor. However, the goal is to replace the common shells by CRC shells with a thickness of just three centimetres. As the bonding depth is reduced, the conventional thermal anchors cannot be used anymore and a new thermal anchor has to be developed. When designing the new anchor, a few conditions had to be taken into account. On the one hand, the anchor had to be adapted to the manufacturing process and the geometry of the textile mesh. On the other hand, it had to withstand structural, thermal and environmental loads.
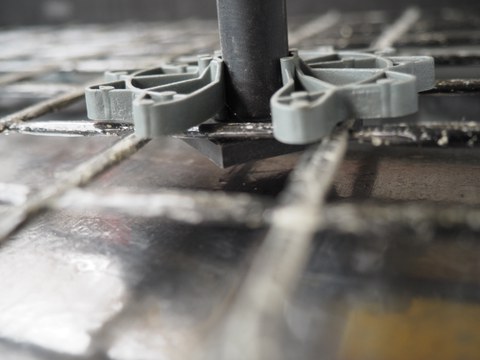
Ein Ende des Thermoankers dient gleichzeitig als Abstandhalter für die textile Bewehrung, eine handelsübliche Klemme kann zur Befestigung genutzt werden
After a lot of manufacturing tests in a precast factory, the ideal geometry for the anchor was found. Then, laboratory tests could be started. In small-sized specimens, the bond of both ends of the anchor was tested under longitudinal tension, compression and transversal tension. As the loading of a structure in a precast factory can occur right on the first day after the manufacturing, selected tests were done at the age of one day, in addition to the common tests after 28 days. To evaluate the results further, tests were done with the common thermal anchor for steel reinforced structures, in a thin CRC shell. Based on the test’s results, it was found out that the new anchor transmits nearly twice of the loads of when compared to that of the common anchor.
Report from the annual report 2017
BUILT-IN PARTS FOR CARBON REINFORCED CONCRETE
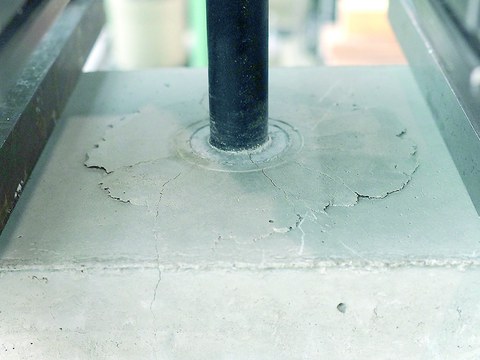
Tensile test on a built-in part for the parallel connection of carbon reinforced concrete elements
The joint research project C3-V1.1 „Development of manufacturing and workmanship processes of carbon reinforced concrete” aims to streamline the manufacturing processes of carbon reinforced concrete. To achieve this, an economical manufacturing process, a finished product with high quality standards, as well as the automation of the manufacturing process of carbon reinforced concrete structures in precast factories needs to be accomplished. Therefore, built-in pre-cast carbon reinforced concrete structural elements have to be developed.
Building with carbon reinforced concrete means thinner structures than structures made out of steel reinforced concrete. The new components have a thickness of 3 cm; the minimum thickness of an element to be produced with the current technology is
5 cm. Thus, known solutions for built-in parts cannot be used anymore. Within the project, built-in parts for the parallel connection of carbon reinforced concrete elements were developed as well as for the longitudinal connection, with connections at right angles. When developing the built-in parts, mechanical, physical and manufacturing aspects have to be taken into consideration. Thermal bridges should be avoided and a flawless manufacturing process at the precast factory has to be guaranteed. After optimization of the built-in parts to make them suitable for construction process at a precast factory, their load-bearing capacity in different loading directions has to be investigated. Longitudinal tension and pressure tests as well as transverse tension tests will be executed on built-in parts which could be placed either on the side or throughout the surface of concrete specimens. These specimens are made out of a carbon textile with epoxy resin embedded in a high-strength concrete. Since in precast factories built-in parts could be loaded at an age of one day, some mechanical tests will be executed one day after being set in concrete instead of after the usual 28 days.
Based on the results of the load bearing tests, it would be possible to determine the applicability of the built-in parts in thin carbon reinforced concrete elements. If necessary, further optimization could be done. It is the projects goal to erect a demonstrator under real manufacturing conditions.
Report from the annual report 2016
LEARNING FROM THE PAST
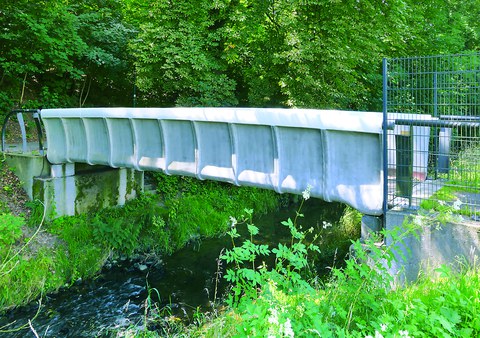
The surface of the TRC bridge in Oschatz was investigated too; on the right: entrance area with revolving door.
Today, carbon concrete composite – in short: C3 – is no longer a foreign concept. Its predecessor, textile reinforced concrete (TRC), has been under investigation in Germany for the nearly two decades. During this period, a number of basic practical applications have been completed. To guarantee the economic manufacturing of structures made of carbon concrete composites, and especially to ensure high quality in the finished product, many aspects of the construction process must be considered. This is where the joint research project C3-V1.1 “Development of manufacturing and workmanship processes of carbon concrete composite” steps in. During the project, manufacturing processes will be streamlined, with the aim of producing surfaces of premium quality.
At the beginning of the project, existing structures made of textile reinforced concrete were reviewed, and the influence of the manufacturing process on their surface quality was examined. All over Germany, four maintenance and strengthening projects, eight load-bearing structures and eight facade structures were reviewed. This investigation found, that the composition of the concrete, the curing and the post-processing have an influence on the surface quality. Cracks due to shrinkage e.g. occur more often if the diameter of the largest grain of the concrete is smaller than 4 mm. As further influencing factors, these cracks occur less often the longer the curing lasts or the longer the structures are left in their formwork. Nevertheless, a long curing or resting time in the formwork will lead to discolorations on the concrete’s surface. But these discolorations can be removed by acid-washing the surface. An outline of the textile reinforcement can often be seen on the concrete’s surface, but if the concrete cover is higher than 5 mm this phenomenon can be prevented.
The outcomes of the review of existing structures made of textile reinforced concrete will be the basis for further test programmes within the joint research project C3-V1.1. Next year, the influence of different curing and post-processing methods on the surface qualities of newly constructed or strengthened structures will be examined under consistent conditions.