C3-V2.1-I-a: Fatigue of carbon reinforced concrete
Table of contents
Project data
Titel | Title TP C3-V2.1-I-a: Ermüdungsverhalten von Carbonbeton sowie carbonbetonverstärkte Bauteile unter statischer und zyklischer Dauerlast im Verbundvorhaben C3-V2.1: Dauerstandverhalten von Carbonbeton | TP C3-V2.1-I-a: Fatigue behaviour of carbon reinforced concrete and structural elements strengthened with carbon reinforced concrete under static and cyclic long-term load as part of the joint research project C3-V2.1: Long-term behaviour of carbon reinforced concrete Förderer | Funding Bundesministerium für Bildung und Forschung (BMBF); Projektträger: FZ Jülich GmbH / C3 – Carbon Concrete Composite Zeitraum | Period 09.2017 – 06.2020 Verbundvorhabenleiter | Leader of the joint research project Prof. Dr.-Ing. Dr.-Ing. E.h. Manfred Curbach Leiter Teilvorhaben | Subproject manager Prof. Dr.-Ing. Dr.-Ing. E.h. Manfred Curbach Bearbeiterinnen | Contributors Dipl.-Ing. Elisabeth Schütze, Dipl.-Ing. Juliane Wagner Projektpartner | Project Partners 7 Partner, davon 4 aus der Forschung und 3 Firmen |
Report in the annual report 2020
INDEFATIGABLE CARBON REBARS
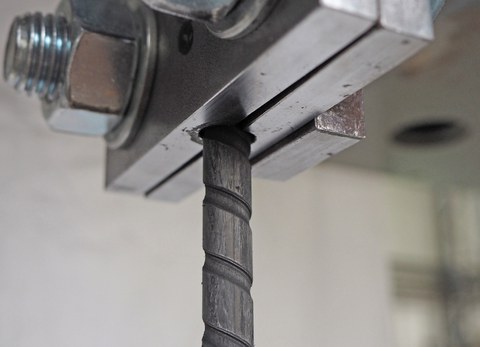
Close-up of a carbon rebar under cyclic tensile load
Carbon reinforced concrete aims to achieve a significantly longer service life compared to that of steel reinforced concrete. The foundations for this research were laid in the joint research project C3-V2.1 “Longterm behaviour of carbon reinforced concrete” as part of the research project C³ – Carbon Concrete Composite. Here, comprehensive knowledge was gained on the behaviour of carbon reinforced concrete under static and cyclic fatigue loading. Initially, suitable small-scale tests were carried out to investigate the material behaviour of carbon reinforced concrete for different loading periods and numbers of cycles to failure under various defined load levels and governing exposures.
In addition to various carbon textiles in a suitable concrete matrix, commercially available carbon rods without an encasing concrete matrix were also investigated in fatigue tests. The aim was to be able to make a statement about their load-bearing behaviour under tensile fatigue. For this purpose, the corresponding maximum loads were varied for each test series at different minimum loads to be able to create S-N lines as material parameters for the fatigue behaviour. The maximum number of load cycles to be achieved was limited to 2 million. The results obtained in the tests are quite positive. As is known from FRP, there was also a clear dependence of the achievable number of load cycles on both the minimum load and the maximum load in the case of the carbon rods. The number of cycles to failure varied very slightly so that the test results could be used to generate S-N lines for predicting the material behaviour. Finally, the residual load-bearing capacity after fatigue loading was tested on specimens that did not fail during fatigue loading. Here, too, no negative influence of the fatigue loading could be detected. The residual load-bearing capacity of all specimens was close to the static reference load and in some cases even significantly higher.
The transferability of the material behaviour demonstrated in the small-scale tests to large components was then checked and verified at our project partner – the Institute of Concrete and Masonry Structures at the Technische Universität Darmstadt. The project thus took a major step towards predicting the service life of carbon reinforced concrete components and paved the way for the future of carbon reinforced concrete.
Report in the annual report 2019
TOUGH GUYS!
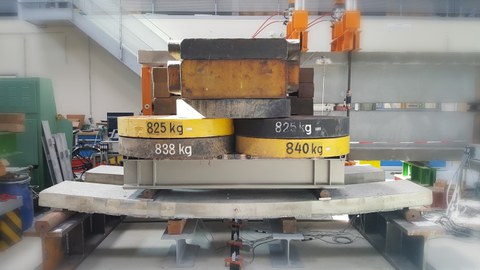
Structures under bending loads can withstand quite high loads over a long period of time
In the joint research project, C3-V2.1 specimens can’t take it easy. For the reliable guarantee of long service life of carbon reinforced concrete at different applications, its material behaviour under permanent loading has to be well known. Therefore, numerous static and cyclic fatigue tests have to be done.
Initially, a lot of small specimens were tested over different loading periods at different loads and load scenarios. In doing so, approaches for the prediction of the material behaviour were developed and validated. Afterwards, the transferability of the results from the small-scaled tests to large-scaled structures was tested in bending and shear force tests on structural elements. Therefore, existing engineering models for the load-bearing behaviour of carbon reinforced concrete are used. These models are usually created with the results from short term tests; their applicability on the material behaviour under static and dynamic fatigue has to be tested during the project.
For that reason, various structural elements have been studied in our laboratory since the summer of 2019. These elements were either T-beams for testing the shear strength or beams for testing the bending strength under static fatigue load. Both types were steel reinforced concrete elements which had been strengthened with one layer of carbon reinforced concrete.
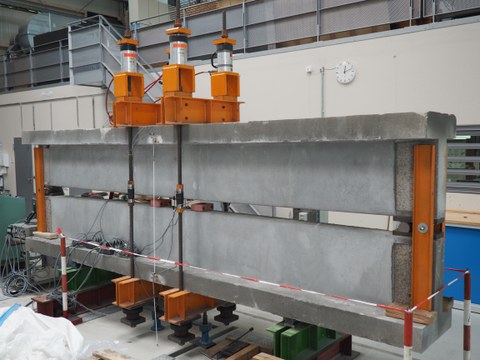
To test the shear capacity under permanent loads two structures were braced against each other
For generating the extremely high loads for the shear tests, the T-beams were braced against each other. Therefore, both elements received nearly the same load of approx. 60% of the reference strength. The two beams for testing the bending capacity were loaded with steel weights. The loads reached a level of 70 or 85% of the reference strength in the textile layer and each of the elements carried a weight of more than 7 tons. Due to the high loads, all of the elements shown a clearly visible deformation. However, if the material behaviour of the small-scaled tests could be transferred to the structural elements, they should survive a time period of 5000 h. So there is nothing left to say but: Tough guys!
Report in the annual report 2018
GOOD VIBRATIONS
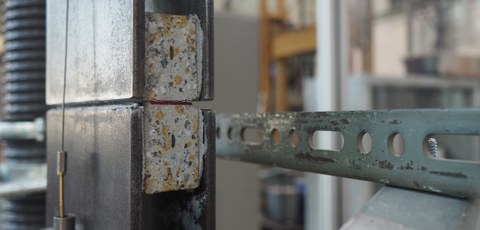
Auch sehr kurze Verbundlängen wurden im Einstufenschwingversuch getestet
How long is the actual life span of a carbon reinforced concrete element in usual load scenarios? To answer this question and predict the service life of carbon reinforced concrete reliably, the joint research project C3-V2.1 was initiated. Apart from conducting suitable small-scale tests under static and cyclic long-term loads, building components will be tested to validate the applicability of the material behaviour. However, the end of this road is still a long way off.
In the most recent test series, the fatigue behaviour of carbon reinforced concrete was tested on small-scale specimens. Single-stage fatigue tests were conducted to determinate both tensile and bond behaviour of a material combination that is supposed to be used mainly for new building components: a carbon textile with epoxy resin impregnation, embedded in high-strength concrete.
In these investigations, for a number of minimum stress levels, the upper-stress levels were varied with the aim of creating S-N curves as material characteristics for the fatigue behaviour. The maximum number of load cycles, after which tests were aborted, was set to 2 millions. To verify, whether fatigue loading had an influence on the required anchorage length, the focus of the bond tests was on investigating varying anchorage lengths in the first instance.
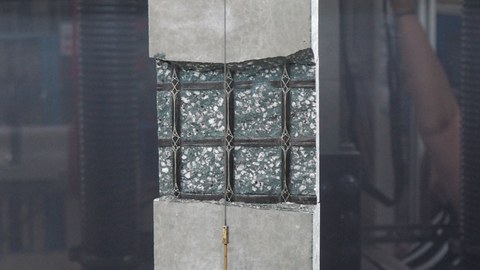
Ein Blick ins Innere: auch ohne Beton kann das Textil der Ermüdungsbelastung standhalten
So far, the small-scale tests have shown favourable results. In the tensile tests, specimens failed only at maximum stress levels exceeding 80 % of the static reference strength – independent of the respective minimum stress level. The bond tests also showed good results. The necessary anchorage length for a complete load transfer between textile and concrete was found to be the triple of the transverse fibre strand spacing in the quasi-static tests. Cyclic loading showed no adverse effects on the anchorage length in the fatigue tests. Only specimens with very short anchorage lengths failed quickly.
The residual strength of non-failed specimens was determined in quasi-static tensile tests. Adverse effects of fatigue could not be found either. The residual strength was close to the quasi-static reference strength for all specimens, some exceeding it significantly.
Report in the year book 2017
LONG LIVE CARBON CONCRETE!
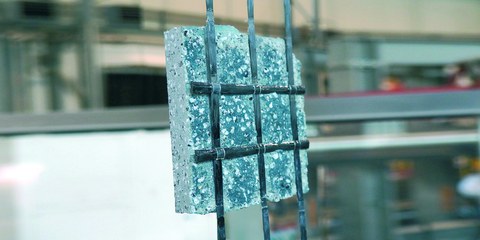
Textile outlives concrete by far
By using carbon reinforced concrete, the aim is to achieve a significantly longer service life compared to that of reinforced concrete. The basis to guarantee the service life of carbon reinforced concrete for a wide variety of applications is the extensive knowledge of the behaviour of carbon reinforced concrete under long-term and fatigue loading. In order to gain this knowledge, at first, methods for predicting the load-bearing behaviour of carbon concrete under continuous load must be developed and tested.
There are various approaches regarding test concepts and engineering models for the prediction of long-term and fatigue behaviour of similar materials such as reinforced concrete and (partially) textile reinforced concrete but also for fibre reinforced plastics. The feasibility of transferring such knowledge to carbon reinforced concrete has still to be tested. Within the joint research project C3-V2.1, in the frame of the project C3 – Carbon Concrete Composite, long-term tests are planned for both static and not predominantly static, cyclic long-term loads. It is expected that with these test series, the material behaviour of carbon reinforced concrete can be examined in suitable small-scale tests for different loading periods and numbers of load cycles respectively, as well as under various, defined load levels and critical exposures. The aim is to establish methods for the prediction of material behaviour and to validate them using these test results.
With tests on building components, under selected conditions, the applicability of the known material behaviour, proven in the smallscale tests, to structural components is then to be validated. Where available, this is based on existing engineering models for the structural behaviour of carbon reinforced concrete components, which currently are mostly based on short-term tests. The transferability of these models to the structural behaviour under cyclic or static long-term loads is to be tested. This approach should finally allow the prediction of the service life for indoor and outdoor applications in the area of strengthening, and new components for different material combinations, as examples carbon rods and two different textiles, and establish the material’s application limits. Thus, the path to the future is opened for carbon reinforced concrete.