C3-V1.5: Abbruch, Rückbau und Recycling von C³-Bauteilen
Inhaltsverzeichnis
Projektdaten
Titel | Title TP C3-V1.5-I-d: Konzeption Großbauteile und Lastenheft „Herstellung“ im Verbundvorhaben C3-V1.5: Abbruch, Rückbau und Recycling von C³-Bauteilen | TP C3-V1.5-I-d: Conception large scale structures and specification „production“ as a part of the joint research project C3-V1.5: demolition, dismantling and recycling of C³ structures Förderer | Funding Bundesministerium für Bildung und Forschung (BMBF); Projektträger: PT Jülich / C3 – Carbon Concrete Composite Zeitraum | Period 01.03.2016 – 30.06.2018 Leiter Teilvorhaben | Subproject manager Prof. Dr.-Ing. Dr.-Ing. E.h. Manfred Curbach Bearbeiter | Contributor Dipl.-Ing. Sebastian May Projektpartner | Project partners Institut für Baubetriebswesen, TU Dresden (Verbundkoordinator) | Institut für Baustoffe, TU Dresden | Lehrstuhl für Betriebliche Umweltökonomie, TU Dresden | AIB GmbH, Bautzen | CARUSO Umweltservice GmbH, Großpösna | MÜLLER-BBM GmbH, Dresden | steinbeisser GmbH, Landsberg | KLEBL GmbH, Gröbzig |
Bericht aus dem Jahrbuch 2018
WOHIN MIT DEM REST?

Händisches Freilegen von Textilien
Eine nachhaltige und ressourcensparende Wertstoffkette muss auch über den Bauteillebenszyklus hinaus funktionieren und sinnvoll sein. Das Forschungsprojekt C3-V1.5 beschäftigt sich mit genau dieser Herausforderung. Ein sogenanntes Downcycling der Ausgangsstoffe Carbon und Beton sollte möglichst vermieden werden, da hierbei die ursprüngliche Qualität und die exzellenten Eigenschaften des hochwertigen Baustoffes verloren gehen. Nur bei einer Wiederverwendung oder einer effizienten stofflichen Weiterverwertung der Primärmaterialien kann von einem ressourcenschonenden Recycling und damit von einer nachhaltigen Verwendung der Materialien gesprochen werden.
Neben der Konzeptionierung und Herstellung von schlanken, materialeffizienten Neubauteilen wurde auch die Nachnutzung beziehungsweise Wiederverwendung des Baumaterials Carbonbeton in den vergangenen drei Jahren tiefgründig untersucht. Des Weiteren wurden Ansätze zum Fügen der dünnen Carbonbetonbauteile theoretisch betrachtet und anschließend praktisch unter Laborbedingungen geprüft. Die Idee dahinter ist, langlebige Carbonbetonbauteile nach einer primären Nutzung zu trennen und an anderer Stelle zur erneuten Nutzung als Einheit wieder zusammenzufügen. Dazu wurden dünne Platten mit einem Carbontextil und einem Verbindungselement im Labor betoniert, kraftschlüssig verspannt und anschließend auf die maximale Tragfähigkeit in Längs- und Querrichtung zur Koppelstelle geprüft. Ein frühzeitiges Versagen konnte dabei nicht festgestellt werden. Einer praxistauglichen Anwendung steht also nichts im Weg.
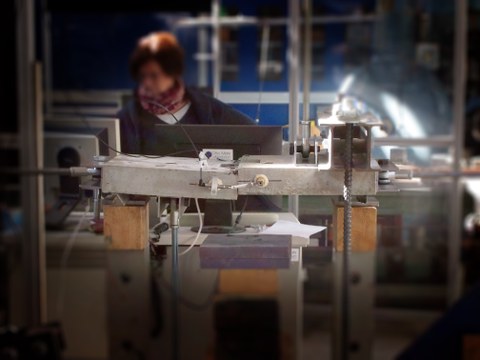
Zug- und Querkraftüberprüfung von zwei gestoßen Carbonbetonplatten
Darüber hinaus wurden die im Jahresbericht 2017 beschriebenen abgebrochenen Großbauteile in ihre Komponenten Beton und Carbonbewehrung separiert und zur weiteren Verwendung in kleinteiligen Versuchen von den Partnern genutzt. Dabei wurden die recycelten Carbontextile sowie geschredderte Carbongarne erneut einbetoniert und in Standardversuchen getestet. Die Versuchsergebnisse und Erkenntnisse waren dabei teilweise erfolgversprechend, zeigten aber auch noch weiteren Forschungsbedarf. Darauf aufbauend werden im Rahmen des Forschungsprojekts C3-V-I.13 „Recycling“ wiederaufbereitete Carbonfasern erneut zu Carbongarnen versponnen und anschließend Textilien hergestellt und getestet.
Bericht aus dem Jahrbuch 2017
ABBRECHEN KOMMT VOR DEM BAUEN

4-Punkt-Biegetest einer Pi-Platte aus Carbonbeton
In dem Projekt betrachten wir die komplette Wertstoffkette im Lebenszyklus eines Bauteiles aus Carbonbeton. Dabei werden die Phasen Herstellung, Nutzung, Umbau und Modernisierung sowie Abbruch, Rückbau und Recycling von Großbauteilen aus Carbonbeton untersucht. Einzelne kleinere Versuche wurden dazu bereits 2016 erfolgreich durchgeführt. Nun galt es 2017, die gewonnenen Erkenntnisse und Ergebnisse an großformatigen Versuchskörpern zu überprüfen. Hierfür wurden zwei raumabschließende Gebäude aus Carbonbeton vorgefertigt und errichtet. Es wurden nur 8 cm dicke Fertigteile als schlanke tragende und nicht tragende Wände und zwei Doppel-Pi-Platten als Decke mit einer lediglich 6 cm starken Druckplatte verwendet. Die „kleinen“ Carbonbeton-Häuschen hatten die Abmaße 5,0 m × 2,5 m × 2,7 m (Länge × Breite × Höhe). Als Bewehrungen dienten flächige Matten und erstmals auch Stäbe aus Carbon. Beide Bewehrungshersteller sind erfolgreich auf dem deutschen und internationalen Markt tätig und wichtige Partner im gesamten C³-Projekt.
An beiden Versuchshäusern wurden Betonbohr- und -trenntechniken sowie Demontagearbeiten durchgeführt, welche im Zuge des Umbaus von Gebäuden oder zum Ende der Nutzungsdauer entstehen können. Diese Arbeiten können aber auch bereits in der Herstellungsphase als auch in der Nutzungsphase, z. B. bei Änderungswünschen des Planers oder Nutzers, notwendig werden. Bei den Versuchen zum Abbruchverhalten konnten wir feststellen, dass der Baustoff Carbonbeton – trotz seiner hervorragenden Verbundeigenschaften – sehr gut in die Ausgangsmaterialien Carbon und Beton trennbar ist. Weitere Versuche zur Kennwertermittlung und Weiterverwendung von zurückge-wonnenen Carbonfasern werden aktuell durchgeführt.
Zur Überprüfung der bekannten Bemessungsansätze von Großbauteilen mit Carbonbeton wurde ein Deckenelement im Otto-Mohr-Laboratorium auf seine Tragfähigkeit geprüft. Diese Ergebnisse sind für parallel laufende C³-Projekte wichtig. Die rechnerische Versagenslast wich dabei gerade einmal 3 % von der experimentell bestimmten Bruchlast ab. Aktuell wird ein modulares Deckenbauteil für den Hochbau aus Carbonbeton geplant und bemessen, wobei die Möglichkeit einzuplanen ist, dass bei einer späteren Erhöhung der Nutzlast eine nachträgliche externe Carbonvorspannung aufgebracht werden kann, damit weiterhin alle erforderlichen Nachweise eingehalten werden. Die entwickelte Vorspanntechnik aus dem C³-Projekt V4.2 Vorgespannter Carbonbeton wird hierbei angewendet.
Bericht aus dem Jahrbuch 2016
Nachhaltigkeit von Carbonbeton
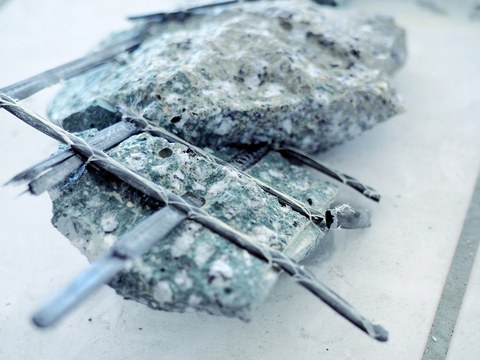
Carbonbewehrtes Abbruchmaterial
Im September 2015 hat die Weltgemeinschaft beim UN-Nachhaltigkeitsgipfel in New York die „Agenda 2030“ vereinbart. Die Ziele der Agenda umfassen dabei in den nächsten Jahren unter anderem eine nachhaltige Verwendung von Ressourcen sowie eine Reduzierung des Energiebedarfs und der Treibhausgase. Diese Ziele hat sich auch das C3-Vorhaben auf die Fahne geschrieben und bereits mit dem Basisvorhaben C3-B2 – Basiskonzepte für nachhaltige Bindemittel und Betone der Zukunft – erfolgreich umgesetzt.
Im Vorhaben C3-V1.5 beschäftigen wir uns mit der nachhaltigen Betrachtung des kompletten Lebenszyklus eines Bauwerkes oder Bauteils aus dem innovativen Verbundwerkstoff Carbonbeton. Hierbei werden die Phasen Herstellung, Nutzung, Umbau und Modernisierung sowie der Abbruch und Rückbau der Bauteile aus dem zukunftsträchtigen Werkstoff Carbonbeton herangezogen. Die Demontagearbeiten beinhalten neben dem Entfernen von Bauteilen im Zuge des Umbaus von Gebäuden oder zum Ende der Nutzungsdauer auch den Einsatz von Betonbohr- und -trenntechniken in der Herstellungsphase. Das Ziel einer ressourcensparenden Wertstoffkette ist, dass alle im Lebenszyklus anfallenden Stoffe im Wirtschaftskreislauf verbleiben. Ein sogenanntes Downcycling der Ausgangsstoffe Carbon und Beton muss hierbei verhindert werden, da sonst bei einer Wertstoffvernichtung die ursprüngliche Qualität und die exzellenten Eigenschaften des hochwertigen Baustoffes verloren gehen. Bei einer Wiederverwendung oder einer effizienten stofflichen Verwertung der Primärmaterialien kann von einem ressourcenschonenden Recycling und damit von einer nachhaltigen Verwendung der Materialien gesprochen werden. Am Ende des Vorhabens wird ein Lastenheft für die Herstellung von Bauwerken und Bauwerksteilen aus Carbonbeton sowie ein Lastenheft für den Verbleib der Baustoffe im Kreislauf bei Abbruch und Rückbau entwickelt sein.
In den ersten Monaten der Projektlaufzeit wurden Probekörper hergestellt, an denen zunächst Tastversuche mit unterschiedlichen Bearbeitungsverfahren – Bohren, Stemmen, Sägen – mit gleichzeitiger Emissionsmessung durchgeführt wurden. Die Carbonbetonplatten ließen sich mit geringerem Aufwand bearbeiten, die Carbonbewehrung konnte man leichter vom Beton trennen als den Stabstahl. Aussagekräftige Ergebnisse zur Emissionsmessung sind in Arbeit. Aktuell werden die Großbauteile für 2017 konzeptioniert und geplant, an welchen unter realitätsnahen Bedingungen Abbruch- und Recyclingprozesse untersucht werden sollen.