C3-V4.12: CRC for jointless restoration of damaged concrete road pavements
Table of contents
Project data
Titel | Title Rissbreitenuntersuchung als Teilvorhaben im Vorhaben C3-V4.12: Carbonbeton zur fugenlosen Instandsetzung geschädigter Betonfahrbahndecken | TP C3-V4.12-II: Research of crack growth as part of the joint project C3-V4.12: Carbon concrete for a jointless restoration of damaged concrete road pavement Förderer | Funding Bundesministerium für Bildung und Forschung (BMBF); Projektträger: FZ Jülich GmbH / C3 – Carbon Concrete Composite Zeitraum | Period 3.2017 - 08.2019 Leiter Teilvorhaben | Subroject manager Prof. Dr.-Ing. Dr.-Ing. E.h. Manfred Curbach Bearbeiter | Contributor Dipl.-Ing. Kristina Farwig Projektpartner | Project partner Lehrstuhl für Baustofftechnik, Ruhr-Universität Bochum (Vorhabenleiter) |
Report in the annual report 2019
CRACK DEVELOPMENT IN CARBON REINFORCED CONCRETE ROAD PAVEMENTS
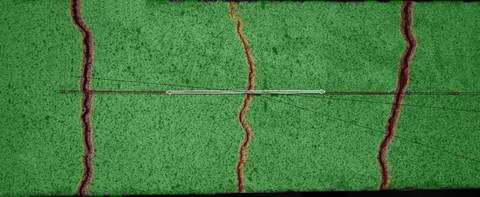
Photogrammetric measurement of cracks in carbon concrete in ARAMIS®
Unreinforced concrete pavements require a high level of maintenance due to the existing joints and are often damaged. An economical and ecological method for the maintenance is to refurbish the damaged road with a thin layer of carbon concrete. The high mechanical as well as thermal and hygric stresses acting on the pavement cause constraining stresses in the jointless carbon concrete layer, which acts in conjunction with the old concrete. In the area of the joint, the bond is therefore separated for a certain area so that a uniform crack distribution can be generated. In order to be able to record the expected crack spacings and widths in the carbon concrete layer experimentally and to verify them mathematically, tensile tests and pull-out tests were carried out at 20 °C, -18 °C and +80 °C in the Otto Mohr Laboratory of the TU Dresden. The 3 cm thick tension specimens were each provided with a centrally arranged layer of textile reinforcement, and compared to specimens with two layers, with each layer having a thickness of 10 mm. With the aid of a photogrammetric measuring system, the crack distances and widths at the tension specimens could be recorded with a high degree of measuring accuracy.
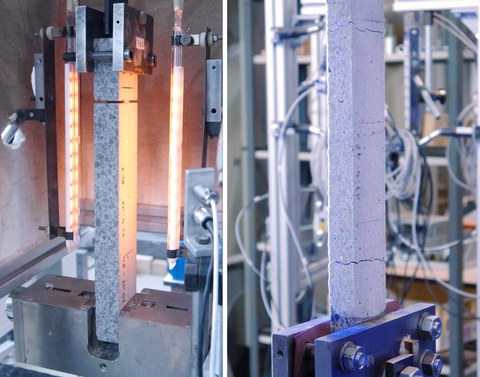
Crack formation at a tensile specimen (right), heating of a single-sided pull-out specimen (left)
The pull-out tests, on the other hand, served to determine the composite properties between the textile roving and the concrete matrix. The force-crack-opening relationship determined can be converted into a composite stress-slip relationship using a numerical calculation tool and is used to calculate the crack distances and widths. The comparison of calculation and test shows that the calculated minimum and maximum crack distances of the single layer reinforced test specimens correspond well with the values measured at
20 °C, -18 °C and +80 °C. The largest variation of the measured values was recorded at 80 °C. The use of two textile layers reduced both the distance between the cracks and the crack widths by almost half. Particularly, a large scattering of the results was measured at 80 °C.
At 20 °C, crack widths of 0.10 to 0.15 mm are recorded from specimens with two layers of reinforcement under service load. In contrast to the minimum and maximum crack spacings, the mean crack widths can be recorded less precisely with the aid of the calculation.
Report in the annual report 2018
CRACK DEVELOPMENT IN CARBON REINFORCED CONCRETE ROAD PAVEMENTS
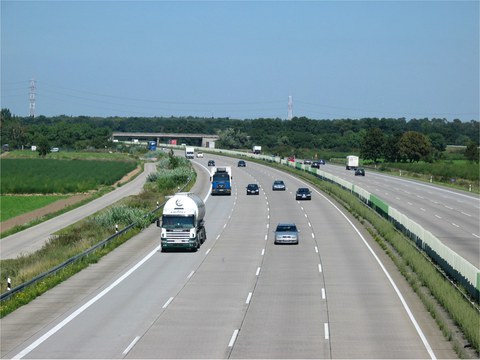
Betonfahrbahndecke
In concrete pavements, transverse joints are specifically cut to prevent cracking as a result of hygric and thermal stress. Due to the high loads resulting from the traffic volume and the weather conditions, the joints also represent a weak point in the concrete. Therefore, continuous maintenance is necessary.
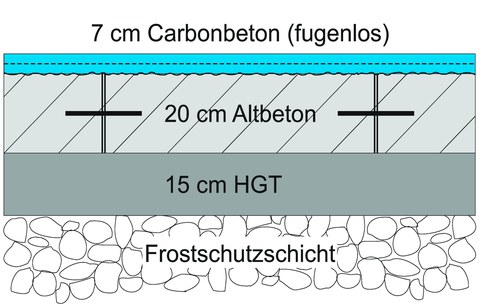
Carbon reinforced concrete as a strengthening layer
In order not to have to renew the entire concrete superstructure, this research project pursues the approach of providing a 3 to 7 cm thick, jointless carbon reinforced concrete layer as a rehabilitation measure. Since smaller crack widths are to be expected in carbon reinforced concrete, this would protect the old concrete from the penetration of water and de-icing agents. The occurring crack widths in the roadway concrete developed by the Ruhr-Universität Bochum in combination with the selected carbon grid is tested by standardised expansion specimen tests in the Otto Mohr Laboratory of the TU Dresden. The crack widths and distances are measured by photogrammetry. For predicting them a calculation model is to be developed. This model will be created on the basis of the force-crack-opening curves determined in single pull-out tests. From this the required anchorage length as well as the minimum crack distance and the average crack width can be determined iteratively. The calculation results are compared with the results of the expansion specimen tests. Further load cases from e. g. temperature effects (20 °C, 80 °C and -18 °C) with different number of layers of carbon reinforcement are tested. In the case of the two layers, a lower concrete tensile force or crack force is generated compared to one layer due to the smaller available concrete cross-sectional area.
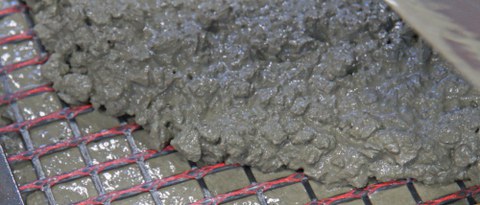
In frischem Straßenbeton eingebettetes Carbongelege
While the crack distances and widths of the test specimens with a single layer can be determined very well with the calculation model, only the maximum crack width is registered with the calculation for the double layer test specimens. However, the results of the calculated crack width determination can be used for further research on the calculation of crack distances and widths in carbon reinforced concrete road pavements.
Report in the annual report 2017
A NEW SKIN FOR DAMAGED CONCRETE ROADWAYS
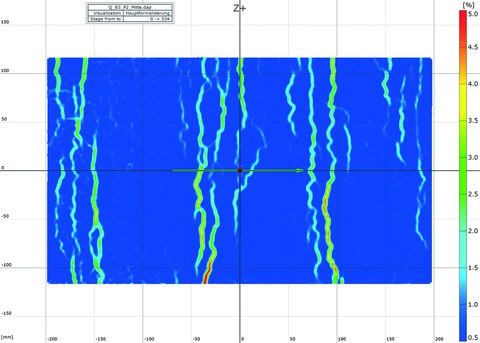
Visualisation of crack growth in a carbon fibre reinforced concrete specimen with photogrammetry
Did you ever wonder what this flappy noise is while you´re driving a car? Is it a damaged tire or is it the rhythmic sound of driving over the transversal dummy joints of concrete road pavement? There are several good reasons for using concrete pavements in road constructions: good load carrying capacity and distribution, high durability, non-slippery surface structure, and much more. But there are shadows where the sun shines. Transversal and longitudinal joints serve as predetermined breaking points to avoid uncontrolled cracking and to allow length changes (e.g., due to changes in temperature).
To ensure the durability of the joints, they are sealed with joint fillers resistant to chemical and fuel.
In reality, those joints have to be maintained and need to be regularly repaired. In case of damages, usually, the whole concrete deck needs to be replaced. That cost a lot of money, consumes material and has a high environmental impact. The main goal of this research project is to develop and proof the suitability of thin layers of carbon reinforced concrete as (additional) pavement. The carbon concrete pavement shall be 3 cm to 7 cm thin and will be used to bypass the joints of the old concrete. Cracks will spread over a wider area by the carbon reinforcement, and thus the crack width will remain small. Corrosive water cannot enter the concrete structure, and road damage will be prevented. For this purpose, the Ruhr-University in Bochum, as leader of the joint research group, and the TU Dresden are working together.
At the beginning of the project, typical concrete used in road construction will be optimized, in terms of the grain size (max. 8 mm), consistency, and workability with the aim to accurately place the fine-mesh grid-like carbon reinforcement. In an extensive series of experiments in the Otto Mohr Laboratory, the material characteristics, the bond behaviour of the carbon grid in combination with the optimized concrete, as well as the crack width development will be researched. The effect of temperature and moisture are considered in the testing. The experimental results will be used to calibrate models to predict and accurately calculate the development and width of cracks. The joint research project will be completed with the construction of a small test area.