Simulation des Betonbruchverhaltens mit diskreten Elementen
Inhaltsverzeichnis
Projektdaten
Titel | Title Simulation des Betonbruchverhaltens mit diskreten Elementen | Simulation of concrete failure with discrete elements Förderer | Funding Deutsche Forschungsgemeinschaft (DFG – Zukunftskonzept der TU Dresden) | Institut für Massivbau (IMB), TU Dresden Zeitraum | Period 10.2013 – 2019 Leiter | Project manager Prof. Dr.-Ing. Dr.-Ing. E.h. Manfred Curbach Bearbeiterin | Contributor Dr.-Ing. Birgit Beckmann |
Bericht aus dem Jahrbuch 2019
DISKRETE-ELEMENTE-SIMULATION DES BETONBRUCHVERHALTENS IN 2D
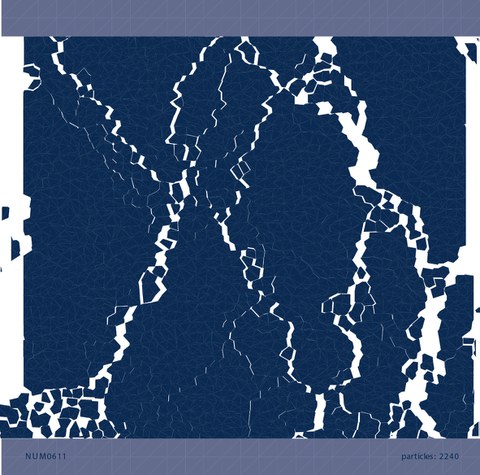
Rissbild in der Simulation eines virtuellen Betonprobekörpers mit 2.240 Partikeln
Mit der numerischen Simulation auf Basis der Diskrete-Elemente-Methode (DEM) werden in diesem Projekt Betonbruchphänomene untersucht. Dabei werden polygonal berandete Partikel verwendet. In partikelbasierten Simulationen wie der DEM sind die diskreten Elemente nicht nur Rechengröße, sondern repräsentieren tatsächliche, einzelne Betonelemente oder Betonpartikel, die sich kinematisch unabhängig voneinander bewegen können. Dieser grundsätzliche Ansatz erlaubt es, Risse simulieren zu können. Ein während der Simulation entstehender Riss ist dabei tatsächlich diskret und bedeutet Abwesenheit von Betonmaterial, also eine Lücke bzw. eine kleine Fehlstelle im Beton. Diese Eigenschaft der DEM, dass Risse per se diskret sind und ganz direkt simuliert werden können, ist ein ganz wesentlicher Grund für die Wahl dieser Simulationsmethode. Ein weiterer Grund ist die inhärent enthaltene Komplexität. Wenn eine große Anzahl von Partikeln, die sich nur in ihrer Geometrie zufallsbedingt geringfügig unterscheiden, die aber von der Art und optional auch von ihren Materialeigenschaften alle gleich sind, ergibt sich allein durch das Zusammenspiel einer großen Anzahl Partikeln eine Komplexität und ein statistischer Charakter. Das bedeutet, zwei Simulationen mit exakt gleichen Simulationsparametern nur mit zwei leicht verschiedenen Partikelensembles ergeben ähnliche, doch leicht andere Ergebnisse in der Simulation.

Rissbild in der Simulation eines virtuellen Betonprobekörpers mit 2.240 Partikeln und geringfügig abweichenden Partikelpositionen
Dies spiegelt genau dieselben Beobachtungen von realen Laborexperimenten wider. Auch hier können zwei Probekörper nie exakt dieselben Positionen der Zuschlag- bzw. Gesteinskörner aufweisen, und auch hier zeigen die Bruchkörper am Ende des Versuchs statistische Abweichungen. Um aus dem Zusammenspiel einer großen Anzahl einzelner Partikel einen statistischen Charakter der Betonprobekörpercharge zu erhalten, muss die Partikelanzahl nicht übermäßig groß sein. Schon eine Partikelanzahl von ca. 2.200 Partikeln reicht aus, ein statistisch variierendes Ergebnis zweier verschiedener Ensembles, also zweier Probekörperrepräsentationen derselben Charge, zu erhalten.
Von zwei Ensembles mit 2.240 Partikeln, die sich durch den bei der Partikelgenerierung enthaltenen Zufallsgenerator nur in der Position der jeweiligen Partikel unterscheiden und ansonsten vollständig gleich Simulationsparameter aufweisen, ähneln sich die erhaltenen Rissbilder, jedoch unterscheiden sie sich geringfügig in der konkreten Rissposition – wie im realen Laborexperiment auch.
Bericht aus dem Jahrbuch 2018
DISKRETE-ELEMENTE-SIMULATION DES BETONBRUCHVERHALTENS
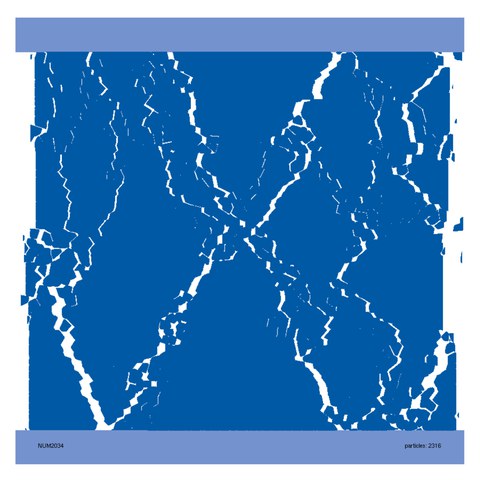
Rissmuster eines Betonprobenkörpers
In diesem Projekt werden Betonbruchphänomene untersucht. Spezielles Augenmerk wird dabei auch auf den statistischen Charakter gelegt. Um Versagensmechanismen, Rissausbreitung und Schadensentwicklung zu erforschen, wird unter Verwendung einer auf der Diskrete-Elemente-Methode (DEM) aufbauenden, numerischen Simulation das Betonverhalten unter Druckbeanspruchung untersucht. Dabei werden speziell Rissmuster, Rissinitiation und Schadensentwicklung betrachtet. Die entstehenden Risse sind diskret – so wie im realen Laborexperiment auch. Die Risse entstehen während der Simulation (allein) aufgrund der Partikelinteraktion und ohne eine Hinzunahme vordefinierter Risszonen oder Risselemente.
In der Simulation werden ein Kontaktansatz mit Überlappungsfläche, die Detektion neuer Partikelkontakte während der Simulation anstatt vordefinierter Nachbarschaftslisten und Partikel mit beliebig polygonaler Geometrie in Kombination verwendet und darüber hinaus statistisch variierende Eigenschaften einbezogen. Während vorangehende Arbeiten den Vergleich von Simulationsergebnissen mit experimentellen Laborergebnissen zum Schwerpunkt hatten, liegt der Fokus der diesjährigen Arbeit in der Präsentation und Beschreibung der theoretischen Grundlagen, vor allem der statistischen Aspekte. In der Simulation werden zwei grundlegende statistische Ansätze verwendet: erstens wird während der Partikelgenerierung ein Zufallsfaktor einbezogen, sodass statistisch variierende Partikelgeometrien und -positionen entstehen; zweitens wird die maximale Längenausdehnung der (optionalen) Kohäsionselemente unter Einbeziehung einer Weibull-Verteilung beschrieben. Dieser statistische Ansatz ist elementar und vergleichsweise einfach. Außerdem werden keine makroskopischen Effekte dem Modell hinzugefügt. Auf dieser Grundlage wird deutlich, dass die Komplexität des Partikelensembles und die Interaktion zahlreicher, jedoch einfacher Partikel die makroskopischen Effekte wie Risse und Rissmusster entstehen lassen.
Als ein Ergebnis der Simulation wird gezeigt, dass es ausreichend, ja sogar förderlich ist, wenn die statistischen Ansätze einfach und elementar sind. Schon allein die Einbeziehung von einfachen, elementaren statistisch abweichenden Material- und Geometrieeigenschaften führt zu variierenden Rissmustern. Dies zeigt, dass die DEM ein passender Ansatz zur Erforschung von Versagens- und Bruchvorgängen ist.
Bericht aus dem Jahrbuch 2017
DISKRETE-ELEMENTE-SIMULATION VON BETONVERSAGEN
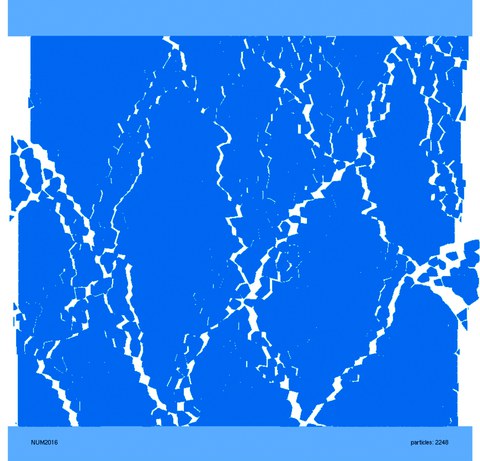
Rissmuster von Betonprobekörpern unter höherer Belastungsgeschwindigkeit
Das Versagensverhalten von Beton wird in diesem Forschungsprojekt in einer numerischen Simulation auf Grundlage der Diskrete-Elemente-Methode (DEM) unter-sucht. Dabei geht es vor allem darum, den Versagensprozess und das Bruch-verhalten einschließlich der dazugehörigen Rissent-wicklung zu untersuchen. Eine diskrete Simulation ist hierfür besonders geeignet, da Risse inhärent in der Methode enthalten sind. In der Simulation wird dabei der Betonprobekörper durch ein Ensemble von einzelnen Partikeln repräsentiert. Ein diskreter Modellierungsansatz unter-scheidet sich von einem kontinuums-basierten Ansatz dahingehend grundlegend, dass die Bewegungsgleichungen der einzelnen Partikel kinematisch unabhängig sind und dass Diskontinuitäten eine inhärente Eigenschaft der Simulationsmethode sind.
In der numerischen Simulation werden die Betonprobekörper durch Einbeziehung einer Zufallsfunktion so generiert, dass sie hinsichtlich ihrer konkreten Positionen der einzelnen Partikel statistische Abweichungen zeigen. Dies entspricht im realen Laborexperiment verschiedenen Probekörpern derselben Betoncharge; denn auch hier unterliegen die konkreten Positionen der einzelnen Zuschlagbestandteile und der Matrix statistischen Variationen.
In der Simulation werden verschiedene Partikelgenerierungen mit denselben sonstigen Parametern berechnet. Dies entspricht wieder verschiedenen Probekörpern derselben Betoniercharge im Laborexperiment. Darüber hinaus werden in der Simulation auch exakt dieselben Probekörper mehrfach virtuell beansprucht – einmal unter langsamerer und einmal unter schnellerer Belastungsgeschwindigkeit. Die Möglichkeit, ein und denselben Probekörper mehrfach und unter verschiedenen Bedingungen bis zum Bruch belasten zu können, ist ein Vorteil der numerischen Simulation gegenüber dem Laborexperiment. In den Bildern werden zwei wesentliche Ergebnisse deutlich. Zum einen ist ersichtlich, dass sich die Bruchbilder von verschiedenen Repräsentationen derselben Charge prinzipiell ähneln, sich aber in den Details der konkreten Risspositionen unterscheiden. Dies ist genauso wie im Laborexperiment, wo die Risse an zwei Proben auch nie exakt an denselben Positionen entstehen. Zum anderen wird in den Bildern sichtbar, dass die Probekörper unter höherer Belastungsgeschwindigkeit Rissbilder zeigen, die einander ähnlicher sind als bei geringeren Belastungsgeschwin-digkeiten und beispielsweise auch eine stärkere Verzweigung aufweisen.
Bericht aus dem Jahrbuch 2016
DEM-Simulation von Betonkomponenten
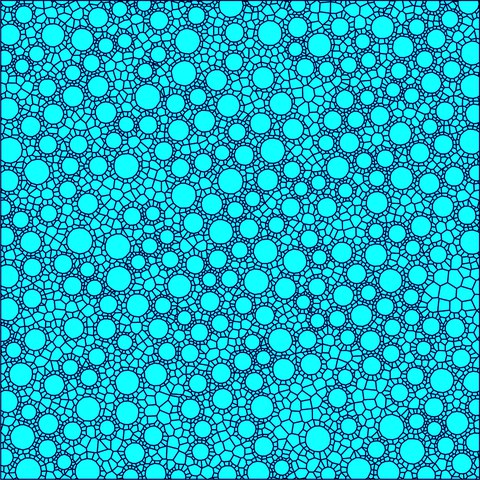
Substruktur für Zuschlag und Zementsteinmatrix – Ensemble von polygonalen Partikeln unterschiedlicher Größe
Bei einer Simulation mit der Diskrete-Elemente-Methode (DEM) wird der Betonprobekörper durch ein Ensemble von einzelnen Partikeln repräsentiert. Bei einem diskreten Modellierungsansatz sind die Bewegungsgleichungen der einzelnen Partikel kinematisch unabhängig und Diskontinuitäten eine inhärente Eigenschaft der Simulationsmethode. Gerade durch die letztgenannte Eigenschaft eignen sich diskrete Formulierungen sehr gut zur Simulation von Rissen und zur Untersuchung von Bruchvorgängen.
Für die Berechnung der Übertragungskräfte zwischen einander kontaktierenden Partikeln ist es erforderlich, dass die Partikel von konvexer Gestalt sind. Um sowohl konvexe als auch konkave Probekörpergeometrien betrachten zu können, werden bei der Generierung des Partikelensembles solche Partikel, die an einer konkaven Ecke liegen, in Subpartikel unterteilt, um somit auch bei konkaven Probekörpergeometrien die Konvexität der Partikel selbst erhalten zu können. Im Projekt werden polygonal berandete Partikel verwendet. Daher ist diese prinzipiell dreidimensional konzipierte Simulation zunächst auf zwei Dimensionen beschränkt. An unserem Institut wurde außerdem noch eine weitere DEM-Simulation mit kugelförmigen Teilchen entwickelt, die für alle drei Raumdimensionen verwendet werden kann.
2016 wurde weiter an der Partikelgenerierung und an der Modellierung einer Substruktur gearbeitet, um die unterschiedlichen Betonkomponenten Zuschlagkorn und Zementmatrix zu repräsentieren. Dies gelingt durch ein Zusammenwirken der beiden genannten Simu-lationstypen. Zunächst wird mit der Simulation für kugelförmige (bzw. im zweidimensionalen Fall kreisförmige) Teilchen eine Durchmischung bzw. Schüttung aus Körnern unterschiedlicher Durchmesser berechnet. Danach wird mit den Mittelpunkten der die Zuschlagkörner repräsentierenden Partikel eine modifizierte Voronoi-Zerlegung durchgeführt. Bei der Modifizierung werden Hilfspunkte in zufällig variierenden Abständen um die Zuschlagkörner herum platziert, um hierdurch deutlich kleinere, jedoch wiederum zufällige bzw. statistisch abweichende Partikel der Zementmatrix zu erhalten. Hierbei entstehen unterschiedlich große Partikel, die von runden Partikeln abstammen, jedoch polygonal berandet und konvex sind, was ein dichtschließendes Ensemble ergibt. Die Konvexität ist zudem für den Kontaktkraftberechnungsalgorithmus erforderlich.
Bericht im Jahrbuch 2014
DEM 2D – Bruchphänomene im Beton
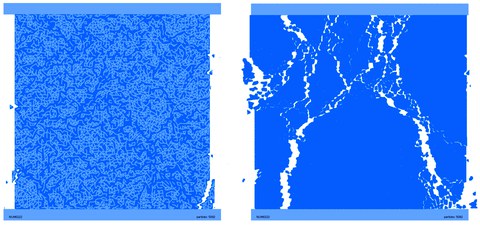
Intakte Kohäsionsstäbe (hellblau) und gerissene Kohäsionsstäbe (dunkelblau) zeigen bereits vorab (links) spätere Makrorissentwicklung im Nachbruchverhalten (rechts) an.
Um die Tragsicherheit von Bauteilen in der Baupraxis zu gewährleisten, muss stets ein ausreichend großer Sicherheitsabstand zum Versagenspunkt eingehalten sein. Demgegenüber ist es in der Grundlagenforschung von Interesse, in Experimenten oder numerischen Simulationen gezielt den Versagenspunkt zu untersuchen. Wann entstehen Mikrorisse? Wie entwickeln sich diese weiter zu Makrorissen? Wie gleichmäßig oder ungleichmäßig verläuft die Schädigungsentwicklung? Wie stark kann die Last nach begonnener Schädigung bis zum vollständigen Versagen noch gesteigert werden? Welches Riss- bzw. Bruchbild weist der Betonprobekörper bei vollständigem Versagen auf? Welche Schädigungsmechanismen laufen ab und können bereits zu Beginn der Schädigungsentwicklung Aussagen über deren weiteren Verlauf getroffen werden? – Um solche und ähnliche Fragestellungen beantworten zu können, wird das Betonbruchverhalten in einer zweidimensionalen numerischen Simulation auf Grundlage der Diskrete-Elemente-Methode (DEM) untersucht. Ein weiteres Ziel ist, die Anwendbarkeit solcher Simulationen zu verallgemeinern.
Konkret wird ein Betonkörper durch ein Ensemble einzelner (diskreter) Partikel beschrieben. Diese Partikel können sich kinematisch unabhängig voneinander bewegen. Wenn zwei Partikel zusammenstoßen und sich in einer gedachten Überlappungsfläche durchdringen, wird daraus eine Rückstoßkraft berechnet. Durch die Interaktion aller Partikel des Ensembles werden auf diese Weise Druckkräfte von der Belastungsplatte bis zur Auflagerplatte übertragen. Solch eine Modellierung ist für die Beschreibung von spröden und vorrangig druckbeanspruchten Materialien wie Beton sinnvoll. Um ergänzend zu den Kontakt-Druckkräften auch Kohäsions-Zugkräfte modellieren zu können, wird ein zusätzliches Netz von Federn bzw. Stäben modelliert. Diese Stäbe können wahlweise Normalkräfte oder Normalkräfte und Biegung übertragen.
In der Simulation kann der grundsätzliche Kraftfluss im Probekörper anhand unterschiedlich dick dargestellter Stäbe sichtbar gemacht werden. Die Dicke der Stäbe steht für die Kraftgröße in ihnen. Gerade zu Beginn einer Belastung kann z. B. gezeigt werden, dass zu einem sehr frühen Belastungszeitpunkt der Kraftfluss, ausgehend von der Lastplatte, noch nicht vollständig die Auflagerplatte erreicht hat. Auch machen während der simulierten Belastungssteigerung gerissene Kohäsionsstäbe das spätere Riss- und Versagensmuster bereits zu einem früheren Belastungszeitpunkt sichtbar.