Team
Inhaltsverzeichnis
Principal Investigators*
*in alphabetischer Reihenfolge
Prof. Dr.-Ing.
Gianaurelio (Giovanni) Cuniberti
TU Dresden, Bereich Ingenieurwissenschaften
Professur für Materialwissenschaft und Nanotechnik
Prof. Dr.-Ing.
Sibylle Gemming
TU Chemnitz
Theoretische Physik quantenmechanischer Prozesse und Systeme
und TU Dresden, cfaed
Prof. Dr.-Ing. habil.
Maik Gude
TU Dresden, Bereich Ingenieurwissenschaften
Professur für Systemleichtbau und Mischbauweisen
Prof. Dr.-Ing.
Julia Kristin Hufenbach
Technische Universität Bergakademie Freiberg
Professur Entwicklung und Funktionalisierung metallischer Werkstoffe
und Leibniz-Institut für Festkörper- und Werkstoffforschung Dresden e. V.
Univ.-Prof. Dr.-Ing. habil.
Michael Kaliske
TU Dresden, Bereich Bau und Umwelt
Institut für Statik und Dynamik der Tragwerke
Prof. Dr.-Ing. habil.
Markus Kästner
TU Dresden, Bereich Ingenieurwissenschaften
Professur für Numerische und Experimentelle Festkörpermechanik
Prof. Dr.-Ing. habil.
Christoph Leyens
TU Dresden, Bereich Ingenieurwissenschaften
Professur für Werkstofftechnik
Dr.
Marco Salvalaglio
TU Dresden, Bereich Mathematik und Naturwissenschaften
Institut für Wissenschaftliches Rechnen
Prof. Dr. sc. techn.
Ivo F. Sbalzarini
TU Dresden, Bereich Ingenieurwissenschaften
Professur für Wissenschaftliches Rechnen für Systembiologie
Prof. Dr.-Ing.
Martina Zimmermann
TU Dresden, Bereich Ingenieurwissenschaften
Professur für Werkstoffmechanik und Schadensfallanalyse
Internationale Mentoren
Alloy design |
Data-driven inference |
Computational physics |
Fellows
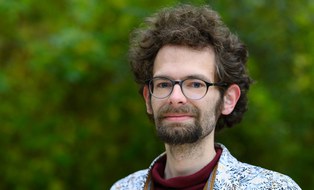
Abel Milor
Eine verschlüsselte E-Mail über das SecureMail-Portal versenden (nur für TUD-externe Personen).
About Me
Having studied Mathematics at the Georg-August University of Göttingen, my main interests are lying between geometry, topology, graph and category theory. After focusing on the use of higher categorical structures to differential geometry during my master’s thesis, my aim in joining the D³ is to apply this theoretical knowledge to new and more application-oriented considerations, including the creation and development of new mathematical tools that can be reused inside or outside the GRK project. Today, my main scientific considerations are about the topology of the metamaterial, with a strong focus on hyperuniform arrangements. This research is a real opportunity for me to explore with more detail other scientific domains, such as mechanical physics and machine learning informatics. Furthermore, I do personally hold in high esteem group work, as well as strong interdisciplinary interactions, and I am always happy to discuss any field of research, even far from mine.
My D³ Project
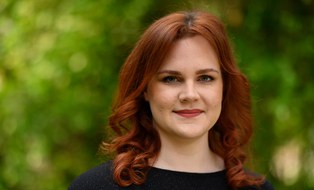
Dipl.-Ing. Alexandra Otto
Eine verschlüsselte E-Mail über das SecureMail-Portal versenden (nur für TUD-externe Personen).
Professur für Numerische und Experimentelle Festkörpermechanik
Professur für Numerische und Experimentelle Festkörpermechanik
Besuchsadresse:
Zeunerbau, Zimmer 342 George-Bähr-Straße 3c
01069 Dresden
About Me
I am a mechanical engineering graduate of TU Dresden, where I specialized in simulation methods of mechanical engineering. During my studies I mainly worked on topics focusing on the application of Machine Learning methods in the context of applied mechanics. Starting with my diploma thesis, I delved deeper into the topic of fatigue strength and durability estimations of carbon-fibre reinforced plastic (CFRP) parts for the first time, in collaboration with a Dresden-based engineering company.
After graduation, I joined the company as a simulation engineer. In this role, I built on the topic of my diploma thesis and deepened my expertise in the simulation of rail vehicle components made from CFRP as well as the simulative modeling of the pultrusion manufacturing process of CFRP parts with constant cross-section.
At the start of 2024, I returned to the TU Dresden a research fellow in the "DCube" Research Training Group where I am responsible for the project S1. This project aims to discover new design principles enabling the generation of resilient spinodoid metamaterials. For me, the DCube Research Training group is a great opportunity to work on innovative and application-orientated research topics with a strong scientific background. Working closely in a team of young researchers from various scientific fields is not only a lot of fun, but above all provides many helpful and interesting insights into a wide range of research fields that I would otherwise probably would not have come across.
My D³ Project

Frau Deekshitha Kancharla
Eine verschlüsselte E-Mail über das SecureMail-Portal versenden (nur für TUD-externe Personen).
About me
Through the course of pursuing my Master's degree in Computational Sciences Engineering from TU Braunschweig, I had the opportunity to do an internship in the field of Additive manufacturing (AM) at Fraunhofer IWS, Dresden. During this time, I worked with metal binder jetting and also got an insight into the capabilities of AM as a manufacturing method and this further piqued my interest in this field. Later, I went on to write my master thesis at IWS. Titled, “Grain Growth Analysis of Binder Jetted 316L Stainless Steel using Dilatometry Data”, it gave me an opportunity to work with both experimentation and simulation of Binder Jetting. To be a part of the Research Training Group 2868 D³ as a doctoral student felt like the natural next step for me. This interdisciplinary project provides me with a possibility to not only delve deep into AM, but also gives me a chance to interact and learn from researchers of different scientific backgrounds. My research topic mainly deals with fabrication of the complex metamaterial structures using metal AM.
My D3 Project
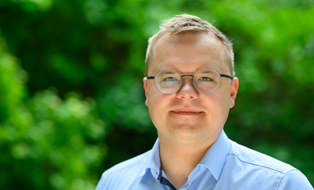
Felix Harazin
Eine verschlüsselte E-Mail über das SecureMail-Portal versenden (nur für TUD-externe Personen).
Institut für Statik und Dynamik der Tragwerke
About Me
After completing my high school diploma (Abitur) in 2018, I studied Civil Engineering at the TU Dresden. There, I specialized in "Computational Engineering". I got in touch with this respective field as a student assistant at the Institute for Structural Analysis at the Faculty of Civil Engineering. In my project work and diploma thesis, I mainly worked on the topics of random fields in uncertainty quantification and machine learning in the context of polymorphic uncertainty quantification. After my graduation I started working as a research assistant at the Institute for Structural Analysis in the field of polymorphic uncertainty in multiscale analysis. There, i deepened my understanding of continuum mechanics, multiscale uncertainty quantification and the interaction between all those fields of research.
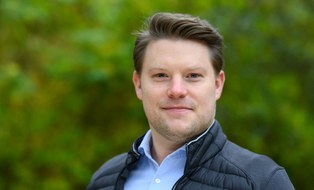
Herr Florian Lehmann
Eine verschlüsselte E-Mail über das SecureMail-Portal versenden (nur für TUD-externe Personen).
About Me
After completing my apprenticeship as an electronics technician for automation technology, I began studying mechanical engineering at the Dresden University of Technology (TUD) and specialized in lightweight engineering. As a student assistant at the Institute for Institute of Lightweight Engineering and Polymer Technology, I was able to apply my knowledge of automation technology in process technology and functional integration, as well as develop and optimize innovative manufacturing processes. After my diploma thesis at Dr. Ing. h.c. Porsche AG and a short stopover as a production engineer at Diehl Aviation GmbH, I started to research the optimization of process and system technology and the problems of multi-material production in the LPBF(M) process at the Fraunhofer IWU. My vision at the time was to combine the design freedom of metal 3D printing with the adaptable properties of polymers. In the Research Training Group 2868, I can implement this version and share my interdisciplinary expertise in an international team of highly motivated scientists. In subproject F2, I am responsible for the hybrid functionalization of 3D-printed spinodoid structures. My goal is to further expand the functional scope of these structures with the help of high-performance polymer and to optimize them for a specific application.
When I'm not combining our metal structures with plastics, I'm a passionate photographer and videographer and am involved in the JuniorIng Sachsen e.V. and the Akademischer Club Leichtbau e.V.
My D³ Project
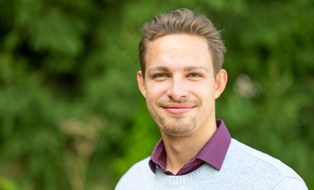
Dipl.-Ing. Lennart Linden
Eine verschlüsselte E-Mail über das SecureMail-Portal versenden (nur für TUD-externe Personen).
Professur für Numerische und Experimentelle Festkörpermechanik
Professur für Numerische und Experimentelle Festkörpermechanik
Besuchsadresse:
Zeunerbau, Zimmer 350 George-Bähr-Straße 3c
01069 Dresden
About me
After completing my high school diploma (Abitur) in 2015, I started studying Mechanical Engineering at TU Dresden, specializing in Applied Mechanics and Simulation Methods. Driven by my interest in the mathematical foundations of modeling and simulation, I decided to pursue a parallel Bachelor's degree in Mathematics, focusing on numerical methods and optimization. Throughout both degree programs, I developed a strong interest in continuum mechanics and constitutive modeling. In my diploma thesis in Mechanical Engineering, I worked on data-driven modeling of anisotropic elasticity at finite strains using artificial neural networks. My Bachelor's thesis in Mathematics dealt with the implementation of a data-driven algorithm for simulating nonlinear elastic truss structures based on a discrete material database, leading to a combined discrete-continuous optimization problem. Alongside my studies, I worked as a student and later as a research assistant at the Chair of Computational and Experimental Solid Mechanics, where I gained early research experience in solid mechanics. After completing my studies, I continued this line of research and became part of the D³ Research Training Group.
My D³ Project
With Markus Kästner as first supervisor, I am responsible for project D4 – Data-driven material modeling. Within this project, I address the central question: How can we develop accurate and flexible constitutive models for complex materials using only experimentally measurable data?
In particular, I focus on nonlinear material behavior, such as anisotropic hyperelasticity, where classical model calibration is often limited by restrictive assumptions and the need for extensive a priori knowledge. To overcome these limitations, my work follows a consistent two-step data-driven approach: First, I use data-driven identification (DDI) to determine tuples consisting of stress and strain states from full-field displacement measurements, such as those obtained by digital image correlation (DIC). This method allows identifying material response from measurable boundary conditions and deformation fields without assuming a predefined constitutive law.
In the second step, the identified data are used to train a physics-augmented neural network (PANN). By integrating physically motivated constraints – such as material frame indifference and thermodynamic consistency – into a flexible neural network architecture, the model not only captures known material behavior accurately but also allows for reliable extrapolation to previously unseen, but physically plausible, material states.
To evaluate the performance and generalization ability of this framework, I conduct benchmark studies based on synthetic data that replicate realistic experimental conditions. The overarching goal is to develop a robust and fully data-driven alternative to classical model calibration –suitable for capturing the complex behavior of heterogeneous materials and supporting more accurate, application-oriented simulations of modern metamaterials.
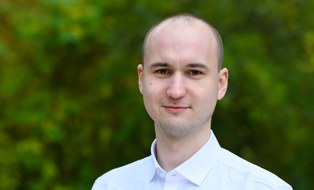
Leonhard Stampa
Eine verschlüsselte E-Mail über das SecureMail-Portal versenden (nur für TUD-externe Personen).
Professur für Werkstoffmechanik und Schadensfallanalyse
Fraunhofer Institut für Werkstoff- und Strahltechnik IWS:
Winterbergstraße 28
01277 Dresden
Deutschland
About Me
Leonhard Stampa studied Material Science (Dipl.-Ing.) at Technische Universität Dresden. Since 2023, he has been working in the Research Training Group 2868 “Data-driven design of resilient metamaterials”. His research focuses on the mechanical behavior of metallic materials, with particular emphasis on the investigation of the fatigue and fracture phenomena. Previous research has concentrated on characterizing the defect-affected fatigue behavior of additive manufactured Ti-6Al-4V and investigating the rolling texture dependent fatigue crack growth in magnesium alloy AZ31. In the current Research Training Group 2868, he is characterizing the mechanical behavior of additive manufactured metamaterials with a particular emphasis on their damage tolerance and fracture behavior.
My D³ Project
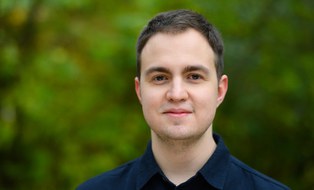
Lukas Volkmer
Eine verschlüsselte E-Mail über das SecureMail-Portal versenden (nur für TUD-externe Personen).
About Me
Hi! My name is Lukas and I studied physics at MLU Halle-Wittenberg and TU Dresden. During my bachelor's program I realized, that staying in the lab is not a thing for me, but running simulations and pen&paper work is far more fun. I am interested in solid state physics, nano science and machine learning. In October 2023 I joined the Research Training Group GRK 2868 as a PhD student. There I use active learning methods to accelerate first principle calculations for the screening of mechanical properties in alloys. In my free time I grow carnivorous plants and like going to the gym.
My D³ Project
I
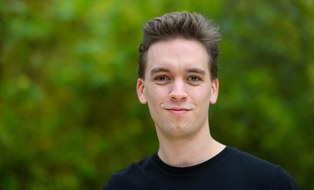
Max Rosenkranz
Eine verschlüsselte E-Mail über das SecureMail-Portal versenden (nur für TUD-externe Personen).
About me
After my high school diploma (Abitur) in 2017, I decided to study mechanical engineering at the University of Technology here in Dresden. During that time I chose the specialization Simulation Methods of Mechanical Engineering, focusing in particular on continuum solid mechanics and constitutive modeling. In my research project and diploma thesis I developed data-driven constitutive models based on artificial neural networks, with particular emphasis to the incorporation of fundamental physical principles. After my studies I continued approaching this problem as a research assistent, before becoming part of D3.
My D³ Project
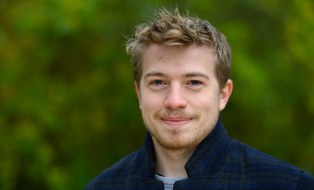
Philip Grimm
Eine verschlüsselte E-Mail über das SecureMail-Portal versenden (nur für TUD-externe Personen).
About Me
During the study internship at the Brose Group, I came in contact with additively manufactured metal components and the fascinating capabilities of laser powder bed fusion for the first time. While my focus in my Master’s thesis was more into 2D materials and fundamental research, I decided to work on a more application-orientated research topic after completing my Master’s Degree in Materials Science. Therefore, this research training group was the best opportunity to pursue the interest in additive manufacturing that I had awakened years ago and furthermore, to work in an international and motivated young research community. In close collaboration with other PhD students and e.g., their support in data-driven materials scouting my task is to develop a tailored aluminum alloy for laser powder bed fusion. My goal is to design an alloy that is processable and masters the challenges of additive manufacturing on the one hand and has the desired mechanical properties on the other.
My D³ Project
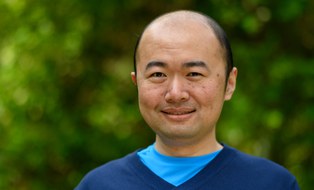
Zhengqing Wei
Eine verschlüsselte E-Mail über das SecureMail-Portal versenden (nur für TUD-externe Personen).
Institut für Physik, Theoretische Physik quantenmechanischer Prozesse und Systeme (TQPS)
Institut für Physik, Theoretische Physik quantenmechanischer Prozesse und Systeme (TQPS)
Professur für Quantenmechanische Prozesse und Systeme:
Reichenhainer Str. 70
09126 Chemnitz
Deutschland
About me
During my lab working in the industry on polymer materials research, I witnessed the rapid development of Industry 4.0. This development highlighted the significant role of digitalization in industrial manufacturing, as well as in the new materials researches. I found that computational materials scientists could study materials through modeling and the first-principle calculations, which sparked my interest in material researches via simulations. To deepen my knowledge, I pursued a Master’s degree in Advanced Functional Materials at Chemnitz University of Technology. There, I learned about cutting-edge topics of functional materials, also including the specialized knowledges in, for instance, surface and interface sciences, crystallography, and solid-state physics. I conducted simulation studies on the design of InGaN materials for the solar cells in my research project and master’s thesis. The RTG 2868 D³ subproject F1 presents an excellent opportunity for my doctoral research. I am highly interested in theoretical surface science and computational material sciences. My doctoral research will focus on an in-depth investigation of the interfaces between aluminum alloys and polymers using numerical simulations methods.
My D³ Project
Postdoc
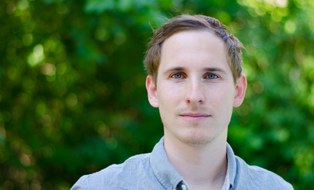
Dr.-Ing. Karl Kalina
Eine verschlüsselte E-Mail über das SecureMail-Portal versenden (nur für TUD-externe Personen).
Professur für Numerische und Experimentelle Festkörpermechanik
Professur für Numerische und Experimentelle Festkörpermechanik
Besuchsadresse:
Zeunerbau, Zimmer 356 George-Bähr-Straße 3c
01069 Dresden
Assoziierte
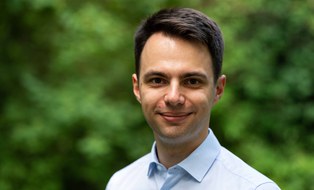
Dipl.-Ing. Alexander Raßloff
Eine verschlüsselte E-Mail über das SecureMail-Portal versenden (nur für TUD-externe Personen).
Professur für Numerische und Experimentelle Festkörpermechanik
Professur für Numerische und Experimentelle Festkörpermechanik
Besuchsadresse:
Zeunerbau, Zimmer 350 George-Bähr-Straße 3c
01069 Dresden
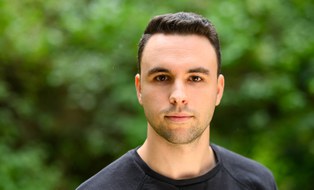
Dipl.-Ing. Heinrich Tristan Roth
Eine verschlüsselte E-Mail über das SecureMail-Portal versenden (nur für TUD-externe Personen).
Professur für Numerische und Experimentelle Festkörpermechanik
Professur für Numerische und Experimentelle Festkörpermechanik
Besuchsadresse:
Zeunerbau, Zimmer 355 George-Bähr-Straße 3c
01069 Dresden
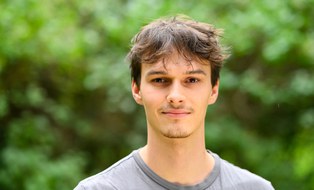
Dipl.-Ing. Konrad Friedrichs
Eine verschlüsselte E-Mail über das SecureMail-Portal versenden (nur für TUD-externe Personen).
Professur für Numerische und Experimentelle Festkörpermechanik
Professur für Numerische und Experimentelle Festkörpermechanik
Besuchsadresse:
Zeunerbau, Zimmer 356 George-Bähr-Straße 3c
01069 Dresden
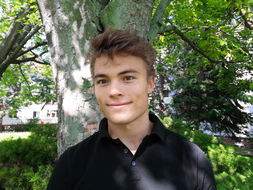
Wissenschaftlicher Mitarbeiter
NameDipl.-Ing. Maik Punke
Eine verschlüsselte E-Mail über das SecureMail-Portal versenden (nur für TUD-externe Personen).
Adressen des Institutes
Adressen des Institutes
Besuchsadresse:
Bürogebäude Z 21, 244 Zellescher Weg 21-25 a
01069 Dresden
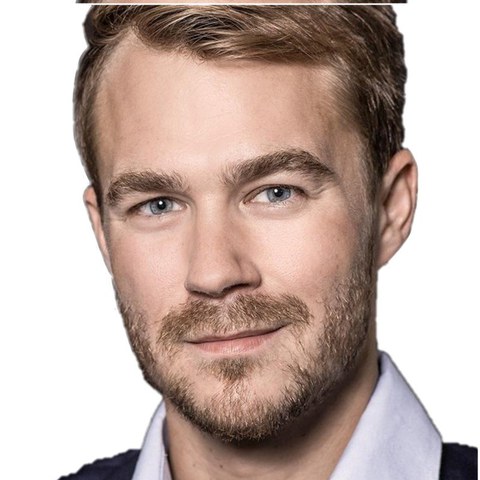
Richard Grothe
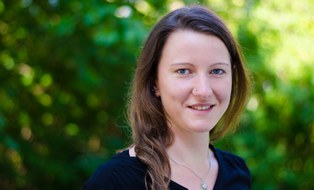
Dipl.-Ing. Ulrike Gebhardt
Eine verschlüsselte E-Mail über das SecureMail-Portal versenden (nur für TUD-externe Personen).
Professur für Numerische und Experimentelle Festkörpermechanik
Professur für Numerische und Experimentelle Festkörpermechanik
Besuchsadresse:
Zeunerbau, Zimmer 355 George-Bähr-Straße 3c
01069 Dresden
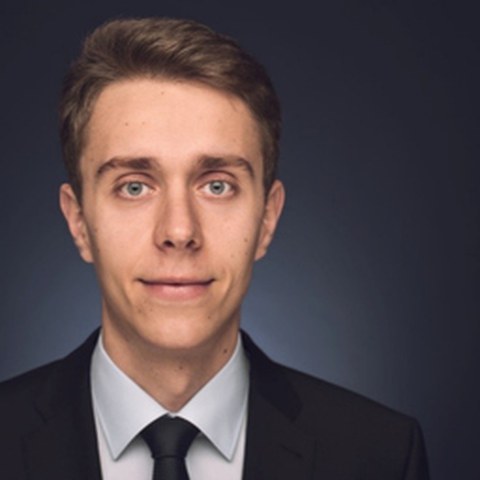
Wikentij Koshukov
Koordination
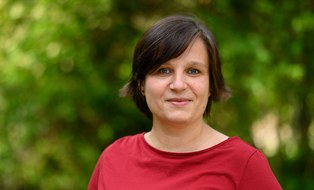
Nadja Kühne
Eine verschlüsselte E-Mail über das SecureMail-Portal versenden (nur für TUD-externe Personen).
Professur für Numerische und Experimentelle Festkörpermechanik
Professur für Numerische und Experimentelle Festkörpermechanik
Besuchsadresse:
Zeunerbau, 352A
01069 Dresden
Data Steward
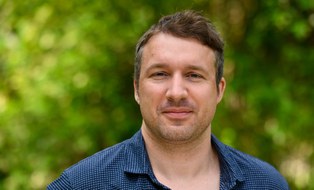
B.A. Philip Träger
Professur für Werkstoffmechanik und Schadensfallanalyse
Besuchsadresse:
Fraunhofer-Institut für Werkstoff- und Strahltechnik IWS Winterbergstraße 28
01277 Dresden
Dipl.-Inf. (FH) Swen Blobel
Eine verschlüsselte E-Mail über das SecureMail-Portal versenden (nur für TUD-externe Personen).
Professur für Numerische und Experimentelle Festkörpermechanik
Professur für Numerische und Experimentelle Festkörpermechanik
Besuchsadresse:
Zeunerbau, Zimmer 342 George-Bähr-Straße 3c
01069 Dresden