2D- & 3D-Wirken
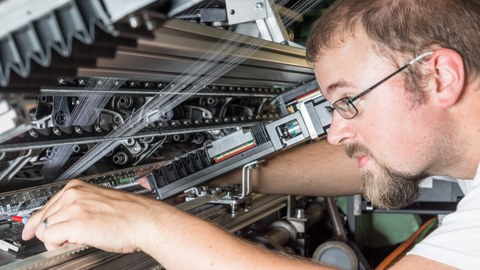
RR-Raschelmaschine mit einem am ITM entwickelten flexiblen und produktiven Schusseintragssystem
Das Kettenwirkverfahren weist durch seine hohe Strukturvariabilität und hervorragende Produktivität ein besonders hohes Leistungspotenzial auf, das jedoch aufgrund der hochdynamischen Fadenbeanspruchungen speziell bei technischen Anwendungen besondere konstruktive Maßnahmen erfordert. Dazu zählen die Leistungssteigerung der Kettenwirkmaschinen durch gezielte technologisch-konstruktive und kinematische Modifikationen, die Entwicklung von Zusatzsystemen für Kettenwirkmaschinen und die Bindungsentwicklung für Gewirke hoher Komplexität. Der Ausbau anforderungsgerechter Technologien und Produkte erfolgt stets in enger Zusammenarbeit mit den Industriepartnern.
Das ITM hat es sich zur Aufgabe gemacht, neben der CAD-gestützten Bindungs- und Strukturentwicklung von klassischen und vor allem komplexen technischen Kettengewirken gezielte Maschinenentwicklungen umzusetzen. Die umfassende Analyse von Kettenwirkmaschinen mit modernster Messtechnik (z. B. hochdynamische Fadenzugkraftaufnehmer, 3D-High-Speed-Viedokameras, Beschleunigungsaufnehmer und Lasertriangulatoren) und Modal- sowie FFT-Analysen ermöglicht hierzu technologische Entwicklungen zur effektiven Verarbeitung von dehnungsarmen Fäden und zur Integration von Funktionsfäden in Kettengewirke, die die Leistung der Maschinen signifikant steigern und das Sortiment der funktionsintegrierten Gewirke im Bereich der Technischen Textilien erweitern. So werden am ITM Lösungen zum Fadenzugkraftausgleich entwickelt, mit der sich an Kettenwirkautomaten hochfeste Filament-, Kompakt- und auch Baumwoll-Ringgarne bei hohen Drehzahlen schonend verarbeiten lassen.
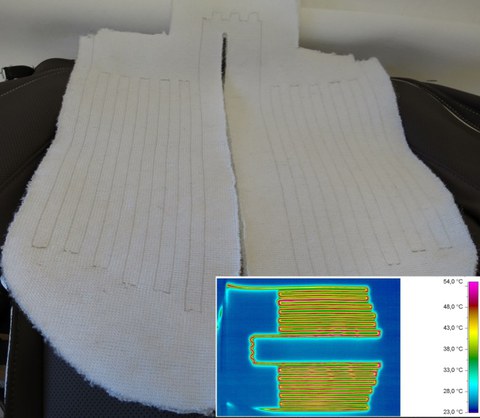
Abstandsgewirke mit integriertem Heizfaden und Wärmebild der Sitzheizung
Für die Steigerung der Produktvariabilität und der Maschinenleistung erfolgte die Entwicklung eines neuen flexiblen und produktiven Schusseintragssystems an Kettenwirkmaschinen, mit dem sich Funktionsfäden direkt und variabel in die Gewirke integrieren lassen. Durch die Integration von elektrisch leitfähigen Garnen in die Gewirke sind handelsübliche Heizsysteme, wie Sitzheizungen für den Automobilbereich, mit einer erheblichen Produktionssteigerung gegenüber bisherigen Verfahren und neuartige innovative Heizsysteme für den Bereich der Elektromobilität herstellbar.
Durch konstruktiv-technologische Modifikationen an RR-Raschelmaschinen wird die effektive Verarbeitung von groben Hochleistungsfäden (Carbon- und Glasfäden ab 800 tex) im Schuss-, Steh- und Polfadensystem möglich. Auf dieser Basis werden Abstandsgewirke für Leichtbaupaneele entwickelt, die bei geschlossenen Deckflächen in x-, y- und z-Richtung Verstärkungsfäden aufweisen.
Derzeitige Entwicklungen konzentrieren sich auf die Realisierung von variabel gekrümmten Spacer-Strukturen mit integrierten Verbindungselementen in unterschiedlichen geometrischen Ausprägungen als großflächige Leichtbaupaneele, die beispielsweise im Fahrzeug-, Behälter- und Bootsbau sowie in der Kanalsanierung zur Anwendung kommen.
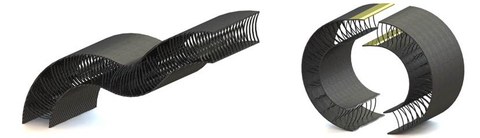
Entwicklung variabel gekrümmter Spacer-Strukturen
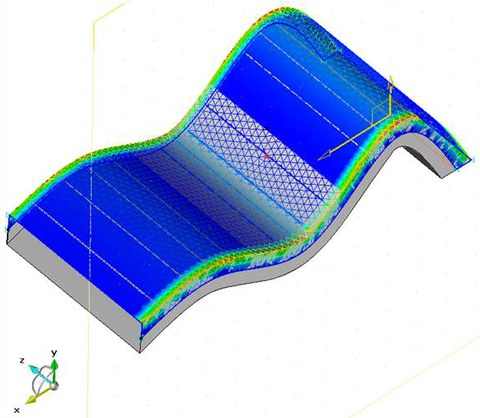
Modellierung des Strukturverhaltens von gewirkten 3D-Strukturen
Die konstruktiven Arbeiten am ITM werden von der Modellierung und Simulation der Faden- und Maschinendynamik sowie von der Modellierung des Strukturverhaltens von gewirkten Strukturen auf Basis der Finiten-Elemente-Methode begleitet.
Derzeit sind am ITM RL- und RR- Kettenwirkmaschinen installiert, die inzwischen mit einer Vielzahl von neu entwickelten Modulen ausgestattet sind, womit sich völlig neuartige textile Konstruktionen fertigen lassen.
Ansprechpartner:
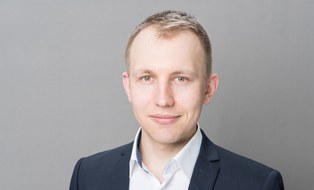
Herr Dr.-Ing. Paul Penzel
Wissenschaftlicher Leiter der Professur Textiltechnik
Eine verschlüsselte E-Mail über das SecureMail-Portal versenden (nur für TUD-externe Personen).
Besucheradresse:
George-Bähr-Str. 3c, Zeuner-Bau, Zimmer 113
01069 Dresden
Deutschland