Development and testing of a spacer system for textile reinforcements in concrete
Table of contents
Project data
Titel | Title |
Report in the yearbook 2014
Casting fabrication of TRC
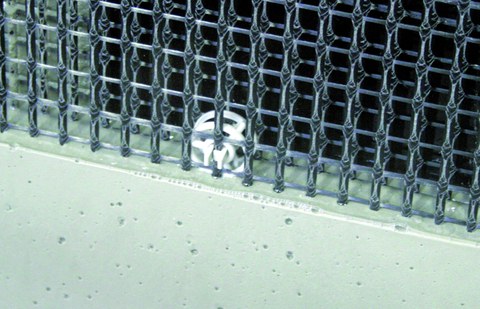
Casting with DistTEX
The production of textile reinforced concrete (TRC) structures takes place usually throughout a laminating process. In such a way that, a thin layer of concrete and a layer of textile reinforcement is inserted alternatively in a mould. Finally, a thin layer of fine concrete is applied. This method of production allows for a highly accurate production of TRC-components in almost any shape providing simultaneously a high positional accuracy of the textile reinforcement. But, this process requires a lot of working space, time and manpower. For serial production of simple plates, it is simply too expensive.
Production optimization was the purpose of the new spacer system DistTEX development for TRCcomponents at TUD along with project partners KDS GmbH and beweka concrete factory Kahla GmbH. The system consists of both: spacers to ensure the distance between the outer layers of reinforcement to formwork, and distance baskets to ensure the distance between the textile layers.
In the research project, the system was developed and investigated comprehensively, e. g. in terms of material handling and of the structural behaviour effects of components produced with DistTEX. Finally, we studied the behaviour of spacer elements under UV radiation in „standard continental“ climate and of concrete embedded spacers in case of fire. In these studies, it was observed that the shape of the spacers for a simulated time-lapse of one year changed: the material of the spacer deformed; the tips of the spacers got slimmer and longer. The changes were between -6 % and +4 %. To follow the high standards on the positional accuracy of the textile reinforcement associated to the spacers, the DistTEX components must be protected against external climatic influences until they are used.
Furthermore, it was possible to produce a curved slab in a casting process by using the spacers. The picture shows a 60 cm wide arc with an arch rise of 17 cm. The reinforcement armed with the spacers were properly placed into the formwork and concreting.
More information regarding the function and components of DistTEX can be found at www.disttex.com.
Report in the yearbook 2013
Textile Reinforced Concrete is Cast
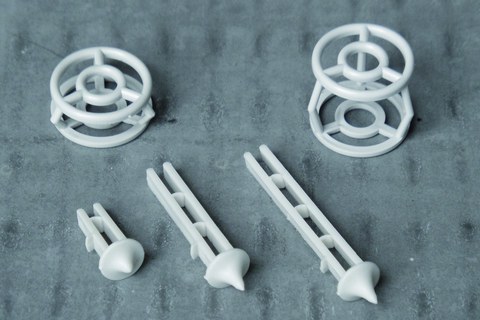
Spacersystem DistTEX consists of spacer-bolts and distance-cages, which are simply sticked together
So far, components from textile reinforced concrete (TRC) were either laminated or shot. The process of casting, known from reinforced concrete construction, was of insignificant importance due to a lack of suitable spacers with the function to keep the textile in place within the formwork during the concreting process. Spacers from reinforced concrete constructions could not be used for TRC because of the different dimensions regarding the reinforcement’s cross section or the component’s geometry.
Consequently, we already developed the spacer system DistTEX for textile reinforced concrete in 2012. With its help, it is possible to fix 2D or 3D fabrics safely in the formwork. Thus, the greatest obstacle to manufacture by casting has been eliminated. The general functionality of the system was initially successfully tested on prototypes. Now, the components of the spacer system have also been successfully manufactured using an injection molding process. However, we did not have any experience in terms of handling the spacer system DistTEX in the production of TRC elements and the influence of DistTEX on the produced components. In 2013, we carried out tests on a large scale to show that the casting process is possible in vertical and horizontal direction.
After the textiles had been prepared, the spacers were mounted in three simple steps: applying the bolts to the first textile layer − applying the distance cages – and applying the second textile layer. Subsequently, the concrete was added. After the slabs had been stripped, the applied spacers could not be perceived from the outside anymore. Sawing up the components proved that even a small number of spacers can guarantee the intended position of the textile reinforcement. The following tensile and bending tests did not indicate any reduction in the load-carrying capacity. Even when the slabs were exposed to temperature changes between 20 °C and 80 °C, there was no danger of the spacers standing out. Apart from this, the watertightness of the slabs was not affected by the spacer. A second concreting process furthermore showed that the production of the textile reinforced concrete slabs in space sav-ing battery formwork is now possible. Accordingly, thanks to DistTEX, there are no longer any obstacles against the effective production of textile reinforced concrete components by casting.
Report in the yearbook 2012
The Textile Wants to be Held
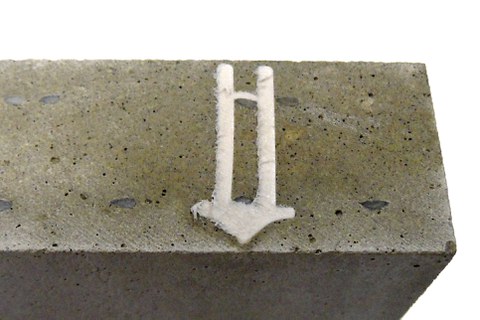
Prototype for a spacer for a 3D textile
Textile reinforced concrete can be produced mainly in two procedures: the spraying or rather laminating method and the casting method. For strengthening of older structures the first one has proven itself. Concrete and textile reinforcement are being applied alternately in layers until the desired reinforcement amount and component form is reached.
For new components or prefabricated parts the in common reinforced concrete already established casting method would be the much more economical alternative. At this procedure the reinforcement is being aligned in a mould subsequently filled with concrete. Therefor the textile has to be fixed or held in the mould so as to ensure a defined clearance to the mould – the later outer edge of the component – and between the reinforcements. Within the field of reinforced concrete construction this is achieved by spacers.
Due to constructive reasons these spacers cannot be used for textile reinforced concrete. Reinforced concrete covers are around 20-50 mm and the bar diameters
8 - 32 mm. TRC though requires concrete covers of only around 2-5 mm and has yarn diameters of around 1 mm. Therefor it is necessary to develop a new spacer system which should:
- realise the needed spacings both between 2D and 3D textiles,
- be manageable at construction sites as well as pre-cast factories,
- be resistant to outer impacts such as for example temperature or humidity,
- be compatible to the textile concrete, its coating and the concrete,
- not influence the load-bearing capacity of the textile concrete and
- be producible with common production methods.
First experiences with spacers for two dimensional textile reinforcements were made while constructing the textile concrete building on the premises of the company beweka Betonwerk Kahla GmbH. Parallel a spacer system for twoand three-dimensional textile reinforcements was developed and several system variations registered for a patent. Following this a number of prototypes were produced able to show that the system works in principle. At the moment the single components of the system are being produced, optimized and checked thoroughly within a research project in cooperation with the company Radeberger Präzisions-Formen- und Werkzeugbau GmbH. Thus the textile can be held also in the future.