Material-efficient design of anchorage and overlapping areas for textile reinforcements made of CFHT
Table of contents
Project data
Titel | Title Materialeffiziente und praxisgerechte Gestaltung von Verankerungen und Übergreifungen von Textilbetonbewehrungen aus Rovings hoher Feinheiten | Material-efficient and practice-orientated design of anchorage and overlapping areas for carbon fibre heavy tows (CFHT) textile reinforcements Förderer | Funding Arbeitsgemeinschaft industrieller Forschungsvereinigungen „Otto von Guericke“ e.V. (AiF) Zeitraum | Period 01.2015 – 11.2018 Leiter | Project manager Prof. Dr.-Ing. Dr.-Ing. E.h. Manfred Curbach Bearbeiter*in | Contributors Dr.-Ing. Kerstin Speck Dipl.-Ing. (FH) Franz Bracklow Projektpartner | Project Partners Institut für Textilmaschinen und Textile Hochleistungswerkstofftechnik (ITM), TU Dresden |
Report in the annual report 2018
LOOP-SHAPED ANCHORAGE
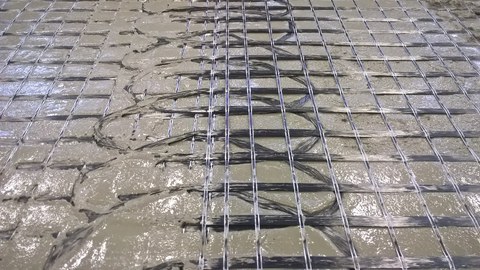
Übergreifungsstoß in der Verstärkungsschicht
Carbon fibre is enjoying increasing popularity both as a strengthening material for existing structures and as reinforcement in new construction. The use of yarns with more than 50.000 filaments per roving and a linear density of up to 3.300 tex, so-called “heavy tows”, allows high permissible stresses and improved performance of the textile reinforcement. The high yarn tensile forces with almost equal reinforcement surface leads to larger anchorage lengths and overlapping areas. A modified loop-shaped yarn arrangement at the textile edge ensures the force transmission within a short length and enables an economic design of the overall system.
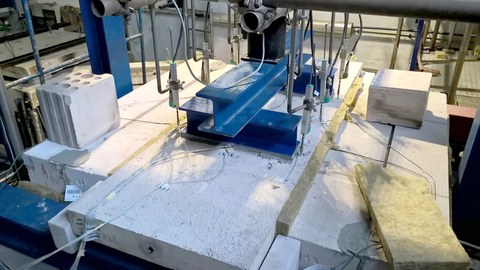
Versuchsaufbau der Plattenprüfung unter Einheitstemperaturkurve
Based on different investigations at the Institute of Concrete Structures - on arrangement, shape and bending radius of the anchoring loops - the Institute of Textile Machinery and High-Performance Material Technology was able to produce such a textile with loop-shaped anchorage ends in the weft direction. Further investigations, including a high number of strain tests, were carried out by the Institute of Concrete Structures. A qualitative comparison among the newly developed loops, straight overlaps and continuous reinforcement was conducted, and their behaviour under fatigue and temperature stresses was also investigated. Finally, large components was tested under fire to validate its behaviour. For this purpose, three reinforced concrete slabs (1.80 x 0.60 x 0.10 m) with a one cm thick strengthening layer and a loop overlapping at the mid-span were produced.
In preparation for the experiments under exposure to fire, the determination of the maximal load capacity with a four-point bending test took place at the Otto Mohr Laboratory. A bending failure occurred outside the textile overlap. The ultimate load correlated well to the calculated load capacity of a slab with continuous textile reinforcement. Based on this reference test, a fictitious service load level for the bending tests under uniform temperature curve at the Leipzig Institute for Materials Research and Testing was chosen. Both slabs could resist fire load for more than 60 or rather 90 minutes without losing load capacity. The loop-shaped anchoring shows a good functionality.
Report in the annual report 2017
MACHINE MANUFACTURED LOOP TEXTILES
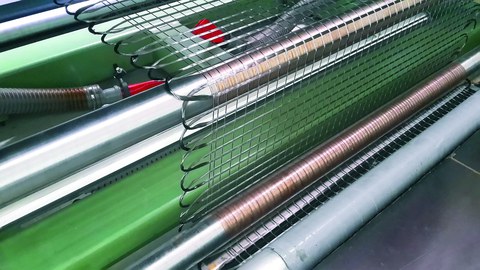
Mechanical production of the loops in the weft direction
The performance of carbon textile reinforced concrete can be significantly increased by using yarns with a higher cross-sectional area, the so-called carbon fibre heavy tows (CFHT) with a fineness of several thousand tex. By replacing several layers of textile grids with lower fineness with one CFHT layer with the same load carrying capacity, the manufacturing costs and the installation effort at the building site can be reduced. However, properties of the bond between textile grids and concrete matrix limit the application of CFHT reinforcements. The high amount of filaments in one yarn results in a smaller surface in comparison to its cross section. Considering also that a high tensile force needs to be transmitted, significant larger anchorage and overlapping lengths are necessary. Mechanical anchorages allow the reinforcement to transfer tensile forces through the round closure area of the loops in a very efficient way.
In the modified textile production process, form-locked anchorage elements will be mechanically integrated into the edges of textile carbon fabrics. An approach was to bend the whole edge of the textile. This method is conceivable in warp and weft direction, and it can be freely adapted at the building site. Because of its stiffness, the textile must be formed before manually soaking it. In comparison with straight yarn ends, the anchorage strength can be doubled with this process.
Due to the manual soaking, however, the total longitudinal force capacity of the carbon fibres cannot be activated. By a specific alignment of the heavy tows, it is possible to get an optimized form-locked connection element. A promising solution are anchorage loops in the weft direction of a textile grid, which are integrated into the manufacturing process. In pre-tests with manually manufactured textiles, the ideal loop diameter turned out to be triple the distance between the yarns. The challenge in transferring the manual manufacturing process into machine manufacturing lies in the forming and soaking of the loops to achieve an accurate shape. Conventional machine manufacturing and soaking processes turned out to be unsuitable. After the optimization process, machine manufactured textiles are now available for subsequent long-term and high-temperature tests.
Report in the annual report 2016
Short and tight CFHT anchorage
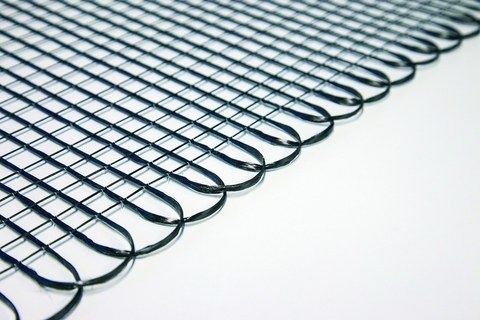
Loops with a diameter of three times the yarn distance
Textile grids are modern and established reinforcing materials, which can be used to strengthen existing structural elements as well as to build new ones. The performance of textile reinforcement can be improved by using yarns with a high fineness. Because of its significantly higher cross-section, carbon fibre heavy tows (CFHT) with a fineness of 3,300 tex can carry higher tensile forces per reinforcement layer than carbon fibres with a lower fineness.
By replacing several layers of textile grids with lower fineness with one CFHT layer with the same load carrying capacity, the manufacturing costs and the effort for the processing on the building site can be reduced. However, bond properties limit the application of CFHT reinforcements. The high amount of filaments in one yarn leads to a smaller surface in comparison to its cross section. Together with a co-occurred higher tensile force which has to be transmitted, significant larger anchorage and overlapping lengths are necessary. For economic reasons and geometrical constraints it is striven for that the overlapping areas should be carried out as short as possible. In the modified textile production process, new anchorage and overlapping elements should be directly mechanically integrated into the edges of a new generation of textile carbon fabrics. By a specific alignment of the heavy tows, it is possible to form anchorage loops in the weft direction of a textile grid to get an optimized form-locked connection element.
This promising solution allows the reinforcement to transfer tensile forces along the round closure area of the loops in a very efficient way. It should be considered that carbon fibres are highly sensitive to transverse pressure. Therefore, a minimum deflection radius must be observed. On the other hand, the amount of necessary crossover points of yarns increases with the size of the loops. Then again, these crossovers lead to weak points in the concrete matrix. Therefore the ideal diameter should be two or three times of the distance between the yarns. With loops of that size, anchorage and overlapping lengths between 5 and 10 cm can be used to anchor the full yarn tensile force or rather to realise a complete lap splice of the reinforcement layers.
Report in the annual report 2015
Loop-anchorage for textile reinforcements
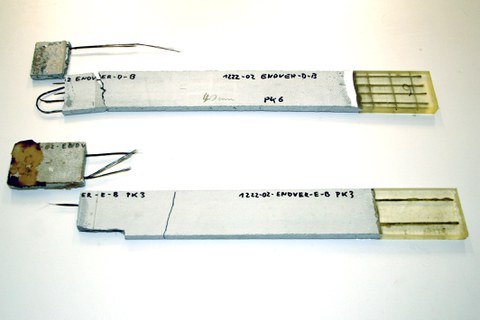
pecimen after an anchorage length test
Multi-axial textile grids are high-performance and very efficient reinforcements for concrete structures. Nowadays, textile reinforcements made of carbon fibers are characterized by extremely high tensile strength – around four times higher than the strength of common steel reinforcement – and by their low weight which amounts to only a quarter of the weight of steel. A very high effectiveness of textile reinforcements can be achieved by using carbon fiber heavy tows (CFHT). CFHT consist of 50,000 filaments and have a fineness of 3,300 tex (1 tex means 1 g per 1,000 m). However, there are some constraints, which limit the application of CFHT reinforcements. CFHT can carry high tensile forces, but only relatively small forces can be carried within the bonding zone. Due to this, the required anchorage and overlapping lengths are relatively large. Therefore, the main goal of this project is to minimize these anchorage lengths to less than 20 cm by implementing new technologies.
In the modified textile production process, new anchorage elements should be mechanically integrated into the edges of a new generation of textile fabrics. By a specific alignment of the yarns, it is possible to form anchorage loops in the weft direction of a textile grid. This solution allows the reinforcement to transfer tensile forces along the round closure area of the loops in a very efficient way.
As a first step, carbon yarns with 30 mm diameter loops were cast in concrete specimens and checked in anchorage length tests. The trials showed that the required anchorage length could be reduced to 50 mm. In the next project phase, overlapping length tests will follow as an attempt to confirm the results of the previous experiments. Later, it is planned to test big-scale specimens under short-term and long-term loading. Another important part of the project is the investigation of the thermal loading behavior of the new anchorage elements.